Nonwovens Industry Staff04.05.12
Converting companies are an integral of the nonwovens supply chain. For all of the advantages the industry’s products provide, a lot has to happen prior to their end use. Nonwovens need to be cut into a variety of shapes and sizes, scaled down to become a single-use product, as well as printed, packaged and more. Sometimes the process is simple, and sometimes more complex, with converting companies using the latest technology to add value to products, and making them easier to use. The following is a compilation of capabilities and services of some the nonwovens industry’s leading converters.
Aurizon Ultrasonics
Aurizon Ultrasonics, Kimberly, WI, USA, has patented technology and years of experience in implementing rotary ultrasonic processing systems that offer an alternative to pressure, thermal, and adhesive bonding systems, as well as other types of ultrasonic technologies used in nonwovens converting.
“In addition to its capabilities in rotary bonding and diecutting, Aurizon Ultrasonics also has expertise in continuous liquid processing, a potentially superior alternative to traditional batch processing that has been demonstrated to improve blending of difficult ingredients dramatically, emulsify multicomponent formulations and effectively dispersing pigments and other particles,” says Bob Cool, executive vice president. Potential benefits include increased productivity, improved quality and product consistency, on-demand manufacturing, lower processing costs, reduced waste and cleanup and removal of dissolved gases in liquids.
Ultrasonic nozzle technology is another Aurizon Ultrasonic specialty. It is described as an efficient and effective means of improving the atomization of liquids or increasing the throughput of viscous liquids through orifices. Aurizon’s ultrasonic nozzles are “self-cleaning,” helping to minimize or eliminate clogging that can often occur with small orifices or viscous liquids.
For rotary processing systems, Aurizon Ultrasonics delivers a high-speed, non-contact means to achieve bonding of materials that contain thermoplastic components, precision cutting of a wide variety of materials, or simultaneous combinations of the two.
“Our state-of-the-art rotary technology maintains unmatched precision processing without contact, delivering high-speed bonding and/or diecutting while virtually eliminating wear and tear on the equipment,” Cool adds.
“By utilizing patented dual-mounted horn and anvil designs, as well as a comprehensive systems approach, our technology delivers high amplitude radial expansion to create rapid compression of materials passing through an in-running nip,” Cool explains. “The cross-direction uniformity of this radial expansion assures a consistent effect on the materials across the width of the process.”
Cantilevered versions of this technology are also available, allowing a smaller manufacturing footprint and easier implementation for processing applications that involve large or bulky products.
www.aurizonultrasonics.com
Berk Wiper Converting & Packaging
Berk Wiper Converting has been in the business of converting disposable wiping cloths for more than 35 years. Located in Lansdale, PA, USA, in a 248,000-square-foot building, the company runs 16 production lines 24 hours a day.“Starting from humble beginnings in the garage of our childhood home, we built a business that today, is one of the fastest growing wiper converters in the country,” says Larry Berk, president.
Berk says the focus of the company is on “one stop shopping.” He says, “Distributors today are looking to simplify the purchasing process, while at the same time provide a large selection of products to their customers. With one of the broadest lines of wipers in the industry, Berk Wiper makes this process easy. We have a wiping cloth for every market in the industry including jan-san, food service, healthcare, automotive and industrial. Everything you need in one vendor,” he says.
Berk Wiper and Converting’s facility is capable of flat sheeting, interfolding, 1/2, 1/4, 1/6 and 1/8 folding, perforating, laminating and slitting up to 139 inches wide by 100 inch diameter. The company offers delivered pricing, private labeling, third party and drop shipping, as well as contract converting services. There are no order minimums.
www.berkwiper.com
Bacon Felt Company
Founded in 1825, the Bacon Felt Company (BFC), East Rochester, NH, USA, was America’s first felt mill. Growth was advanced as the Boston Felt Company was added to the team. Today, with its sister company, Supreme Felt & Abrasives, in Chicago, converted product and service offerings have been further enhanced.
BFC specializes in felt manufacturing and fabricating. Having a diverse set of technologies and engineering expertise, BFC offers performance, functional materials, prototype and small volume production, precision-driven quality and service. Process capabilities include felt and needled nonwoven manufacturing, laminating, diecutting, sheeting, slitting/stripping, coating, impregnating, skiving, machining/grinding/shaping, perforating, assembly and packaging.
Product design begins with fiber selection. BFC offers materials of all fiber types: natural or synthetic, as blends or composites. As a felt manufacturer, BFC specializes in wool, what the company says is naturally the most versatile known fiber. Along with offering a wide range of densities, products provide functional attributes such as fire retardant, heat resistant, acoustical/thermal insulation, abrasion resistant, absorbent and chemical resistant.
With such high performance characteristics for wicking, fluid retention and transfer, resilience, shock and vibration protection, BFC offers a versatile range of finished products that include pen nibs, piano felt, polishing wheels, drum beaters, adhesive-backed felt, metal processing wipers, erasers, wicks, seals, ring buffs, insoles and damping pads.
www.baconfelt.com
Boyd Technologies
Boyd Technologies, South Lee, MA, USA, has been in the converting industry for more than 32 years and is growing its core converting and contract manufacturing capabilities in technical markets. The company began in 1979 as a converter of technical papers and nonwovens, and today produces both component and finished products from technical papers, nonwovens, membranes, films, foils, extruded netting and nanofiber materials.
Boyd built its converting and contract manufacturing capabilities in the consumer marketplace, producing finished products that include bandage and wound care products, oral care products and home cleaning products. Services include multilayer laminating, rotary diecutting, printing and a variety of finished packaging. All of these products also require advanced quality and regulatory controls.
Another set of capabilities for Boyd Technologies, also developed out of the consumer space, is its project management skills, which it calls “Technology Consulting.” Here, Boyd manages product launches through material specification, product specification, equipment design and installation and validation procedures. All of this is done during fast-to-market, high volume consumer product launches.
Today, the company is growing in medical device and power storage and delivery markets, which is largely due to the advanced capabilities it has developed over the last 30 years, which are increasingly in demand. “Through our experience in the consumer space, we’ve been able to continually develop our validation procedures and GMP levels, which allow us to deploy solutions that meet the needs of customers in the medical and electronics markets,” says Chip Schnackenberg, the company’s director of quality and IT.
Boyd Technologies has exciting plans for new growth in 2012, which include the installation of a cleanroom manufacturing space, a new high speed rotary diecutting and lamination line and several new product launches in its business development pipeline.
www.boydtech.com
Carpet Systems
Carpet Systems currently has opportunities across several market segments including filtration, landscape, hygiene and industrial end uses. Most of its work involves multi-layer laminations utilizing thermal or sonic technology and the company has recently partnered with a local company to offer hot-melt adhesive capabilities. This line is capable of producing specialized spray patterns out to 80" wide. Add rates can be as low as seven gsm and as high as 80 gsm. This capability has been placed inline with one of its thermal bonders and can accommodate single-side adhesive lay down for downstream processing or the company can utilize its bonding line to fuse two layers together.
Additionally, Carpet Systems has a newly upgraded website, www.carpetsystems.com where potential clients can find out more about its company or the creation of a composite structure to meet their specific needs.
www.carpetsystems.com
Felix
Films and laminates manufactured by Felix are produced as roll goods, however, a range of converting technologies are also available, including slitting—the company rewinds and slits a collection of materials, mostly films and laminates, to the width, length, core size and other specific requirements of the customer. Felix also does hot-melt laminating. Here, a porous hot melt lamination technique is available to create custom composite fabrics, using hot melt and pressure to combine and bond two or more substrates together.
Other capabilities include film extrusion, as the company can deliver micro-embossed extruded film products. Two-color flexographic printing is available, and Felix has hot-melt surface coating and extrusion coating capabilities to develop its coated products. Felix, with headquarters in Eskisehir, Turkey, also provides custom contract manufacturing and converting capabilities such as hot-melt coating and lamination, printing and roll slitting.
www.felixplastic.com
FIberweb (India) Limited
Fiberweb (India) Limited set up its first facility in India in 1996 for the manufacture of PP spunbond nonwoven fabrics. The facility is located in Daman, about 100 miles north of Mumbai. The plant has a 3.2 meter Reifenhauser two-beam line for manufacturing fabrics from 15 gsm to 150 gsm. The company exports more than 70% of its production to various customers across the globe. Fiberweb (India) Limited has a presence in three major segments—hygiene, crop protection and textile applications. But Fiberweb has a converting division located in this same facility. The converted products handled by the company include mini-rolls (retail packs), mattress covers, pillow and cushion ticks, folded fabrics (flat packs), carry bags and more.
The converting division has about 50 sewing machines covering lock-stitch, chain-stitch and inter-lock, and is capable of turning out more than 300,000 mini-rolls. This section incorporates several winder-unwinder units as well as an automatic side-sealer and shrink-wrapping system. “The tailors in the stitching section are specialists in the field, having worked for many years in export-focused garment industries,” says Pravin Sheth, managing director.
“The retail packs generally require an insert label,” Sheth explains. “The converting division is in a position to get such labels printed in four to six or even eight colors, depending on the customers’ requirements. A barcode label can also be printed either as part of the main insert label or as a label to be affixed separately.”
All self-adhesive labels incorporating product and packing information are generated in-house at Fiberweb (India) Limited. The retail packs can be manufactured in bundles/packs or in display boxes with outer cartons. The cartons can be palletized and stretch-wrapped, if required.
“Fiberweb (India) Limited is uniquely positioned to ensure quality across the entire chain of the converting process since the company is also a manufacturer of nonwoven fabrics,” Sheth says.
www.fiberwebindia.com
Ginni Consumer Products
Ginni Consumer Products is an ISO 9001-2000 certified business unit of Ginni Filaments Ltd., one of India’s leading textile conglomerates producing nonwoven spunlace fabric, cotton yarn, knit fabric and garments. The company is FDA-approved and manufactures a wide variety of versatile products including dry and wet wipes for baby care, beauty care and cleansing and makeup remover wet wipes.
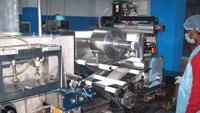
Ginni specializes in wipes converting.
The converting unit situated in Haridwar, India, is equipped with the latest converting machinery. Among its converted products are ready-to-use wet wipes face masks and exfoliating facial dry cloths. Personal hygiene items include cleansing and calming wet wipes, refreshing wipes and anti-bacterial wipes. The company also converts home care wipes, hand sanitizer wipes, anti-bacterial wipes, sunscreen Wipes, fairness wipes, after-shave wipes and menthol wipes. Ginni also offers a wide range of surgical wound care dressing products.
The company’s nonwoven spunlace plant has a production capacity of 12,000 tons per annum, with technology equipped and supplied by Perfojet France.
www.ginnifilaments.com
Independent Machine
Independent Machine Company has developed a new 1600 mm wide slitter with Pope-type Minimum Gap Surface assist Rewind and auto cut and transfer for light gauge nonwoven materials. The slitter features separate two-position driven unwinds with closed loop tension control to accommodate two meter [78 inch] diameter supply rolls and are positioned before the main process, which is the speed reference of the entire system. A 36-inch diameter drum roll follows the main texturing process speed reference to 250 meters per minute and pulls the material through a dancer/accumulator that provides closed loop tension feedback and material storage to maintain speed during the auto cut and transfer.
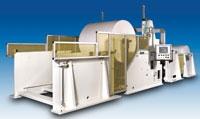
Independent Machine’s new slitter is ideal for
ligh gauge nonwovens.
The material is slit just before contact with the drum roll at the adjustable driven pneumatic shear assembly. The slit strands are wound to a 2.5 meter [98 inch] diameter on individual cores all secured on a common air shaft. The rewind provides minimum gap winding and is driven by an AC follower drive to provide programmable taper winding throughout the entire rewind cycle. Roll density and rewind tension is controlled by continuous drive speed ratio changes during winding.
An automatic core shaft feeder loading system is located over the top of the drum roll. The shaft feeder has pneumatic clamps which grasp the shaft from the magazine by the journals and pneumatically lowers the shaft into the transfer arm assembly.
The cut-off knife on the lift roll assembly fires and severs the webs from the winding rolls and attaches to the preglued empty cores. The rolls wind to the predetermined length or maximum diameter programmed diameter. The multi drive AC vector system is controlled through an Allen–Bradley PLC with PanelView Touchscreen including recipe storage.
www.independentmachine.com
Kleen-Test
Kleen Test Products, Port Washington, WI, is one of the world’s largest contract manufacturers and packagers of wet wipes, dryer sheets, nonwoven and liquid products. The company’s FDA
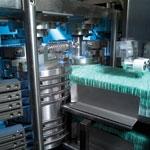
A close-up shot of a Kleen Test
converting job
and EPA registered manufacturing plants—five in Wisconsin and two in Ohio—have the ability to handle many diverse manufacturing and packaging needs efficiently, and are able to segregate confidential products and flexibly staff peaks in demand.
Kleen Test can pack wet wipes into canisters, tubs, cartons, single packs, rigid and flexible packs, and has the ability to cut and cross-fold, flat fold and interleave substrates. The company recently joined forces with Taiki USA to expand usage of Taiki’s patented “D Cap” flow wrap fitment products. The “D Cap” flow wrap and fitment is strategically designed to maximize product life by keeping products fresh and moist.
www.kleen-test.com
National Wiper Alliance
A leader in the field of nonwoven converting, Asheville, NC-based National Wiper Alliance continues to meet the growing needs of its current customers and acquires new customers by adding production lines and flexible packaging equipment. Working from 240,000 square feet of production and warehouse space, its newest production equipment will go on-line in the first quarter of 2012, allowing National Wiper Alliance to offer higher speeds and more efficient production outputs for both the wet wipe and dry wipe industries.
National Wiper Alliance offers converting capabilities for every put-up required in dry wipes for all segments of industry needs including industrial, medical, retail and others. The flexibility of the new equipment allows for efficiencies required on the larger runs to meet the demand for lower cost products and the production capabilities to offer custom converting options specific to individual’s requirements and the ability to offer private labeling on inner and outer product packaging.
The company’s converting services are geared to the individual client’s requirements, working with consumers to design and build brand recognition with their own private labeled brands and also strengthening national brands while offering a competitively priced and value product offering.
With an outside warehouse, National Wiper Alliance has the ability to keep on-hand both raw material and converted items, and increase the outsourcing services the company offers to customers. National Wiper Alliance handles the turnkey converting of products from the ordering of raw materials and ancillary items to logistics and distribution of converted products directly to its customers.
www.nationalwiper.com
Oxco
Founded in 1994, Oxco is a supplier and converter of nonwoven fabrics including but not limited to spunbond, spunlace, needlepunch, stitch bond, chemical bond, thermal bond and more. Oxco’s converting and processing capabilities include narrow and wide web slitting, rewinding, perforating, center folding, adhesive powder coating, laminating, printing, finishing and custom packaging.
With diverse nonwoven production and converting capabilities, Oxco is capable of responding to many customer demands. The company continually evaluates its production services to ensure it offers consistent, high quality and efficient output. As markets and applications evolve, Oxco adapts by implementing the necessary technology, the company says.
www.oxco.com
Prolamina
Prolamina is a $300+ million manufacturer with three plants in North America and is ranked as one of the Top 10 largest converters in North America, according to PCI Consulting’s recent market research report. The company has 11 laminators, 13 printing presses, laser scoring equipment, slitting and rewinding equipment. Prolamina has three of the largest & fastest tandem laminators in the world. The company is an expert at coating & laminating non-wovens and has been in business for more than 40 years.
The company has a full line of standard products as well as breathable products and special purpose products. The company has large multi-national customers and exports its products around the world. The company’s plants have all of the contemporary plant certifications. It operates a large R&D team in Montreal, Canada and has multiple PHDs working on next generation products. The company is a patent holding product developer and is committed to innovation and cost competitiveness.
Prolamina has experience with most specifications and line requirements and maintains a full technical team of field technical support to assist its customers with on-site technical support when it arises. The company provides tech support to more than 100 plants on a routine basis. The company is proud of its customer service and runs Vendor Managed Inventory (VMI) programs for its customers off of its state-of the-art Oracle information technology system.
Prolamina has global procurement scale and is familiar with price/performance tradeoffs among product structure options. The company’s goal is to provide the right answer for the right situation, automate the supply chain and maintain transparency of business operations with its customers. The company is committed to growth and has an open invitation for companies to visit its plants and meet its people.
www.prolamina.com
Rockline Industries
Rockline Industries continues to invest in long-term growth by strengthening its commitment to providing a comprehensive array of wipe manufacturing solutions. Recent highlights include adding multiple wipe manufacturing technology platforms to drive customers’ growth and achieving zero-landfill status at two additional sites, meeting its pledge to reduce its environmental impact. Rockline Industries anticipates sustainable growth throughout 2012 and beyond by continuing to leverage its global expertise in materials, manufacturing and innovation to provide customer-specific solutions.
www.rockline-ind.com
Superior Felt & Filtration
Superior Felt & Filtration, LLC continues to expand its operations in Ingleside, IL. Several new facilities have been opened recently which have expanded Superior’s nonwoven manufacturing and converting capabilities. Already stocking the largest inventory of micron, CFM, synthetic and SAE wool felts in North America, SFF also warehouses and converts Technostat, a sub-micron, high-efficiency filter media. Weights of 50 gsm to 900 gsm are in inventory to meet the most demanding tribo-electric filtration needs. SFF has also added a new white room which includes converting capabilities to further support its position in slitting, heat sealing, die-cutting and other value added services. Additionally, Superior is proud to announce that its manufacturing division, NonWoven Solutions, has commissioned its second state-of-the-art needle punch line to double production and strengthen its position in the medical and filtration textile industry; evidence that Superior Felt continues to position itself as a leader in the felt and filtration market.
www.superiorfelt.com
Tufco Technologies, LLC
Tufco Technologies, based in Green Bay, WI, is a provider of turnkey contract manufacturing services. The facility is ISO 9001-2008 certified, and FDA and EPA approved. Capabilities include wide-web flexographic printing, adhesive laminations, wet and dry wipe manufacturing along with integrated packaging solutions.
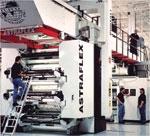
Tufco’s Astraflex wide web flexo press
Tufco’s modern, high speed assets have the capability to produce wipes in flat packs, tubs, canisters and sachets. Tufco can also offer in-house formulation and blending. Addressing the drive for eco-friendly products, Tufco has been focusing on developing products that fill this void. John Michaud, vice president of sales and marketing, says, “There have been natural formulations and compostable substrates around for a while but the missing piece has been the packaging. We’re working on some recyclable films that are showing great promise.”
Tufco has two wide-web flexographic printing presses that can print paper, films and nonwovens up to 62 inches wide with either water or solvent-based inks. Tufco has won many awards for flexographic printing and has a reputation for being able to work with difficult substrates. According to Cindy Fisher, Tufco’s flexographic sales manager, “Customers bring us the print jobs that no one else can do.” In addition to printing, Tufco can produce adhesive laminations up to 120 inches in web width.
Tufco Technologies is a business to business outsource manufacturer. Customers include nationally recognized consumer products market leaders. “From concept through commercialization, Tufco works side by side with your team to support your initiatives. Our mission is to be the leading one-stop manufacturer for printing, laminating and converting services,” Michaud says.
www.tufco.com.
Aurizon Ultrasonics
Aurizon Ultrasonics, Kimberly, WI, USA, has patented technology and years of experience in implementing rotary ultrasonic processing systems that offer an alternative to pressure, thermal, and adhesive bonding systems, as well as other types of ultrasonic technologies used in nonwovens converting.
“In addition to its capabilities in rotary bonding and diecutting, Aurizon Ultrasonics also has expertise in continuous liquid processing, a potentially superior alternative to traditional batch processing that has been demonstrated to improve blending of difficult ingredients dramatically, emulsify multicomponent formulations and effectively dispersing pigments and other particles,” says Bob Cool, executive vice president. Potential benefits include increased productivity, improved quality and product consistency, on-demand manufacturing, lower processing costs, reduced waste and cleanup and removal of dissolved gases in liquids.
Ultrasonic nozzle technology is another Aurizon Ultrasonic specialty. It is described as an efficient and effective means of improving the atomization of liquids or increasing the throughput of viscous liquids through orifices. Aurizon’s ultrasonic nozzles are “self-cleaning,” helping to minimize or eliminate clogging that can often occur with small orifices or viscous liquids.
For rotary processing systems, Aurizon Ultrasonics delivers a high-speed, non-contact means to achieve bonding of materials that contain thermoplastic components, precision cutting of a wide variety of materials, or simultaneous combinations of the two.
“Our state-of-the-art rotary technology maintains unmatched precision processing without contact, delivering high-speed bonding and/or diecutting while virtually eliminating wear and tear on the equipment,” Cool adds.
“By utilizing patented dual-mounted horn and anvil designs, as well as a comprehensive systems approach, our technology delivers high amplitude radial expansion to create rapid compression of materials passing through an in-running nip,” Cool explains. “The cross-direction uniformity of this radial expansion assures a consistent effect on the materials across the width of the process.”
Cantilevered versions of this technology are also available, allowing a smaller manufacturing footprint and easier implementation for processing applications that involve large or bulky products.
www.aurizonultrasonics.com
Berk Wiper Converting & Packaging
Berk Wiper Converting has been in the business of converting disposable wiping cloths for more than 35 years. Located in Lansdale, PA, USA, in a 248,000-square-foot building, the company runs 16 production lines 24 hours a day.“Starting from humble beginnings in the garage of our childhood home, we built a business that today, is one of the fastest growing wiper converters in the country,” says Larry Berk, president.
Berk says the focus of the company is on “one stop shopping.” He says, “Distributors today are looking to simplify the purchasing process, while at the same time provide a large selection of products to their customers. With one of the broadest lines of wipers in the industry, Berk Wiper makes this process easy. We have a wiping cloth for every market in the industry including jan-san, food service, healthcare, automotive and industrial. Everything you need in one vendor,” he says.
Berk Wiper and Converting’s facility is capable of flat sheeting, interfolding, 1/2, 1/4, 1/6 and 1/8 folding, perforating, laminating and slitting up to 139 inches wide by 100 inch diameter. The company offers delivered pricing, private labeling, third party and drop shipping, as well as contract converting services. There are no order minimums.
www.berkwiper.com
Bacon Felt Company
Founded in 1825, the Bacon Felt Company (BFC), East Rochester, NH, USA, was America’s first felt mill. Growth was advanced as the Boston Felt Company was added to the team. Today, with its sister company, Supreme Felt & Abrasives, in Chicago, converted product and service offerings have been further enhanced.
BFC specializes in felt manufacturing and fabricating. Having a diverse set of technologies and engineering expertise, BFC offers performance, functional materials, prototype and small volume production, precision-driven quality and service. Process capabilities include felt and needled nonwoven manufacturing, laminating, diecutting, sheeting, slitting/stripping, coating, impregnating, skiving, machining/grinding/shaping, perforating, assembly and packaging.
Product design begins with fiber selection. BFC offers materials of all fiber types: natural or synthetic, as blends or composites. As a felt manufacturer, BFC specializes in wool, what the company says is naturally the most versatile known fiber. Along with offering a wide range of densities, products provide functional attributes such as fire retardant, heat resistant, acoustical/thermal insulation, abrasion resistant, absorbent and chemical resistant.
With such high performance characteristics for wicking, fluid retention and transfer, resilience, shock and vibration protection, BFC offers a versatile range of finished products that include pen nibs, piano felt, polishing wheels, drum beaters, adhesive-backed felt, metal processing wipers, erasers, wicks, seals, ring buffs, insoles and damping pads.
www.baconfelt.com
Boyd Technologies
Boyd Technologies, South Lee, MA, USA, has been in the converting industry for more than 32 years and is growing its core converting and contract manufacturing capabilities in technical markets. The company began in 1979 as a converter of technical papers and nonwovens, and today produces both component and finished products from technical papers, nonwovens, membranes, films, foils, extruded netting and nanofiber materials.
Boyd built its converting and contract manufacturing capabilities in the consumer marketplace, producing finished products that include bandage and wound care products, oral care products and home cleaning products. Services include multilayer laminating, rotary diecutting, printing and a variety of finished packaging. All of these products also require advanced quality and regulatory controls.
Another set of capabilities for Boyd Technologies, also developed out of the consumer space, is its project management skills, which it calls “Technology Consulting.” Here, Boyd manages product launches through material specification, product specification, equipment design and installation and validation procedures. All of this is done during fast-to-market, high volume consumer product launches.
Today, the company is growing in medical device and power storage and delivery markets, which is largely due to the advanced capabilities it has developed over the last 30 years, which are increasingly in demand. “Through our experience in the consumer space, we’ve been able to continually develop our validation procedures and GMP levels, which allow us to deploy solutions that meet the needs of customers in the medical and electronics markets,” says Chip Schnackenberg, the company’s director of quality and IT.
Boyd Technologies has exciting plans for new growth in 2012, which include the installation of a cleanroom manufacturing space, a new high speed rotary diecutting and lamination line and several new product launches in its business development pipeline.
www.boydtech.com
Carpet Systems
Carpet Systems currently has opportunities across several market segments including filtration, landscape, hygiene and industrial end uses. Most of its work involves multi-layer laminations utilizing thermal or sonic technology and the company has recently partnered with a local company to offer hot-melt adhesive capabilities. This line is capable of producing specialized spray patterns out to 80" wide. Add rates can be as low as seven gsm and as high as 80 gsm. This capability has been placed inline with one of its thermal bonders and can accommodate single-side adhesive lay down for downstream processing or the company can utilize its bonding line to fuse two layers together.
Additionally, Carpet Systems has a newly upgraded website, www.carpetsystems.com where potential clients can find out more about its company or the creation of a composite structure to meet their specific needs.
www.carpetsystems.com
Felix
Films and laminates manufactured by Felix are produced as roll goods, however, a range of converting technologies are also available, including slitting—the company rewinds and slits a collection of materials, mostly films and laminates, to the width, length, core size and other specific requirements of the customer. Felix also does hot-melt laminating. Here, a porous hot melt lamination technique is available to create custom composite fabrics, using hot melt and pressure to combine and bond two or more substrates together.
Other capabilities include film extrusion, as the company can deliver micro-embossed extruded film products. Two-color flexographic printing is available, and Felix has hot-melt surface coating and extrusion coating capabilities to develop its coated products. Felix, with headquarters in Eskisehir, Turkey, also provides custom contract manufacturing and converting capabilities such as hot-melt coating and lamination, printing and roll slitting.
www.felixplastic.com
FIberweb (India) Limited
Fiberweb (India) Limited set up its first facility in India in 1996 for the manufacture of PP spunbond nonwoven fabrics. The facility is located in Daman, about 100 miles north of Mumbai. The plant has a 3.2 meter Reifenhauser two-beam line for manufacturing fabrics from 15 gsm to 150 gsm. The company exports more than 70% of its production to various customers across the globe. Fiberweb (India) Limited has a presence in three major segments—hygiene, crop protection and textile applications. But Fiberweb has a converting division located in this same facility. The converted products handled by the company include mini-rolls (retail packs), mattress covers, pillow and cushion ticks, folded fabrics (flat packs), carry bags and more.
The converting division has about 50 sewing machines covering lock-stitch, chain-stitch and inter-lock, and is capable of turning out more than 300,000 mini-rolls. This section incorporates several winder-unwinder units as well as an automatic side-sealer and shrink-wrapping system. “The tailors in the stitching section are specialists in the field, having worked for many years in export-focused garment industries,” says Pravin Sheth, managing director.
“The retail packs generally require an insert label,” Sheth explains. “The converting division is in a position to get such labels printed in four to six or even eight colors, depending on the customers’ requirements. A barcode label can also be printed either as part of the main insert label or as a label to be affixed separately.”
All self-adhesive labels incorporating product and packing information are generated in-house at Fiberweb (India) Limited. The retail packs can be manufactured in bundles/packs or in display boxes with outer cartons. The cartons can be palletized and stretch-wrapped, if required.
“Fiberweb (India) Limited is uniquely positioned to ensure quality across the entire chain of the converting process since the company is also a manufacturer of nonwoven fabrics,” Sheth says.
www.fiberwebindia.com
Ginni Consumer Products
Ginni Consumer Products is an ISO 9001-2000 certified business unit of Ginni Filaments Ltd., one of India’s leading textile conglomerates producing nonwoven spunlace fabric, cotton yarn, knit fabric and garments. The company is FDA-approved and manufactures a wide variety of versatile products including dry and wet wipes for baby care, beauty care and cleansing and makeup remover wet wipes.
Ginni specializes in wipes converting.
The company’s nonwoven spunlace plant has a production capacity of 12,000 tons per annum, with technology equipped and supplied by Perfojet France.
www.ginnifilaments.com
Independent Machine
Independent Machine Company has developed a new 1600 mm wide slitter with Pope-type Minimum Gap Surface assist Rewind and auto cut and transfer for light gauge nonwoven materials. The slitter features separate two-position driven unwinds with closed loop tension control to accommodate two meter [78 inch] diameter supply rolls and are positioned before the main process, which is the speed reference of the entire system. A 36-inch diameter drum roll follows the main texturing process speed reference to 250 meters per minute and pulls the material through a dancer/accumulator that provides closed loop tension feedback and material storage to maintain speed during the auto cut and transfer.
Independent Machine’s new slitter is ideal for
ligh gauge nonwovens.
An automatic core shaft feeder loading system is located over the top of the drum roll. The shaft feeder has pneumatic clamps which grasp the shaft from the magazine by the journals and pneumatically lowers the shaft into the transfer arm assembly.
The cut-off knife on the lift roll assembly fires and severs the webs from the winding rolls and attaches to the preglued empty cores. The rolls wind to the predetermined length or maximum diameter programmed diameter. The multi drive AC vector system is controlled through an Allen–Bradley PLC with PanelView Touchscreen including recipe storage.
www.independentmachine.com
Kleen-Test
Kleen Test Products, Port Washington, WI, is one of the world’s largest contract manufacturers and packagers of wet wipes, dryer sheets, nonwoven and liquid products. The company’s FDA
A close-up shot of a Kleen Test
converting job
www.kleen-test.com
National Wiper Alliance
A leader in the field of nonwoven converting, Asheville, NC-based National Wiper Alliance continues to meet the growing needs of its current customers and acquires new customers by adding production lines and flexible packaging equipment. Working from 240,000 square feet of production and warehouse space, its newest production equipment will go on-line in the first quarter of 2012, allowing National Wiper Alliance to offer higher speeds and more efficient production outputs for both the wet wipe and dry wipe industries.
National Wiper Alliance offers converting capabilities for every put-up required in dry wipes for all segments of industry needs including industrial, medical, retail and others. The flexibility of the new equipment allows for efficiencies required on the larger runs to meet the demand for lower cost products and the production capabilities to offer custom converting options specific to individual’s requirements and the ability to offer private labeling on inner and outer product packaging.
The company’s converting services are geared to the individual client’s requirements, working with consumers to design and build brand recognition with their own private labeled brands and also strengthening national brands while offering a competitively priced and value product offering.
With an outside warehouse, National Wiper Alliance has the ability to keep on-hand both raw material and converted items, and increase the outsourcing services the company offers to customers. National Wiper Alliance handles the turnkey converting of products from the ordering of raw materials and ancillary items to logistics and distribution of converted products directly to its customers.
www.nationalwiper.com
Oxco
Founded in 1994, Oxco is a supplier and converter of nonwoven fabrics including but not limited to spunbond, spunlace, needlepunch, stitch bond, chemical bond, thermal bond and more. Oxco’s converting and processing capabilities include narrow and wide web slitting, rewinding, perforating, center folding, adhesive powder coating, laminating, printing, finishing and custom packaging.
With diverse nonwoven production and converting capabilities, Oxco is capable of responding to many customer demands. The company continually evaluates its production services to ensure it offers consistent, high quality and efficient output. As markets and applications evolve, Oxco adapts by implementing the necessary technology, the company says.
www.oxco.com
Prolamina
Prolamina is a $300+ million manufacturer with three plants in North America and is ranked as one of the Top 10 largest converters in North America, according to PCI Consulting’s recent market research report. The company has 11 laminators, 13 printing presses, laser scoring equipment, slitting and rewinding equipment. Prolamina has three of the largest & fastest tandem laminators in the world. The company is an expert at coating & laminating non-wovens and has been in business for more than 40 years.
The company has a full line of standard products as well as breathable products and special purpose products. The company has large multi-national customers and exports its products around the world. The company’s plants have all of the contemporary plant certifications. It operates a large R&D team in Montreal, Canada and has multiple PHDs working on next generation products. The company is a patent holding product developer and is committed to innovation and cost competitiveness.
Prolamina has experience with most specifications and line requirements and maintains a full technical team of field technical support to assist its customers with on-site technical support when it arises. The company provides tech support to more than 100 plants on a routine basis. The company is proud of its customer service and runs Vendor Managed Inventory (VMI) programs for its customers off of its state-of the-art Oracle information technology system.
Prolamina has global procurement scale and is familiar with price/performance tradeoffs among product structure options. The company’s goal is to provide the right answer for the right situation, automate the supply chain and maintain transparency of business operations with its customers. The company is committed to growth and has an open invitation for companies to visit its plants and meet its people.
www.prolamina.com
Rockline Industries
Rockline Industries continues to invest in long-term growth by strengthening its commitment to providing a comprehensive array of wipe manufacturing solutions. Recent highlights include adding multiple wipe manufacturing technology platforms to drive customers’ growth and achieving zero-landfill status at two additional sites, meeting its pledge to reduce its environmental impact. Rockline Industries anticipates sustainable growth throughout 2012 and beyond by continuing to leverage its global expertise in materials, manufacturing and innovation to provide customer-specific solutions.
www.rockline-ind.com
Superior Felt & Filtration
Superior Felt & Filtration, LLC continues to expand its operations in Ingleside, IL. Several new facilities have been opened recently which have expanded Superior’s nonwoven manufacturing and converting capabilities. Already stocking the largest inventory of micron, CFM, synthetic and SAE wool felts in North America, SFF also warehouses and converts Technostat, a sub-micron, high-efficiency filter media. Weights of 50 gsm to 900 gsm are in inventory to meet the most demanding tribo-electric filtration needs. SFF has also added a new white room which includes converting capabilities to further support its position in slitting, heat sealing, die-cutting and other value added services. Additionally, Superior is proud to announce that its manufacturing division, NonWoven Solutions, has commissioned its second state-of-the-art needle punch line to double production and strengthen its position in the medical and filtration textile industry; evidence that Superior Felt continues to position itself as a leader in the felt and filtration market.
www.superiorfelt.com
Tufco Technologies, LLC
Tufco Technologies, based in Green Bay, WI, is a provider of turnkey contract manufacturing services. The facility is ISO 9001-2008 certified, and FDA and EPA approved. Capabilities include wide-web flexographic printing, adhesive laminations, wet and dry wipe manufacturing along with integrated packaging solutions.
Tufco’s Astraflex wide web flexo press
Tufco has two wide-web flexographic printing presses that can print paper, films and nonwovens up to 62 inches wide with either water or solvent-based inks. Tufco has won many awards for flexographic printing and has a reputation for being able to work with difficult substrates. According to Cindy Fisher, Tufco’s flexographic sales manager, “Customers bring us the print jobs that no one else can do.” In addition to printing, Tufco can produce adhesive laminations up to 120 inches in web width.
Tufco Technologies is a business to business outsource manufacturer. Customers include nationally recognized consumer products market leaders. “From concept through commercialization, Tufco works side by side with your team to support your initiatives. Our mission is to be the leading one-stop manufacturer for printing, laminating and converting services,” Michaud says.
www.tufco.com.