Karen McIntyre, Editor03.06.12
During the past five years, the nonwovens industry has reaped the benefits of national legislation requiring mattress tops to withstand a certain amount of heat before combusting into flames. This legislation, first passed in California and later nationally by the Consumer Products Safety Commission, requires mattress tops to meet certain flammabilitiy standards to reduce the severity of fires ignited by open flames such as candles, matches and lighters.
Passed nationally in 2006, this legislation created a temporary boom for nonwovens producers in this category. While the flammability effect could be achieved in traditional woven mattress tops, many bedding manufacturers opted for nonwovens because of their ability to achieve the results right in the manufacturing process without the use of an extra step post production. Additionally, the use of nonwovens requires less toxic aftertreatments, making the final product safer for consumers.
Five years after the ruling, most of the nonwovens manufacturers—including Milliken, Freudenberg and Precision Custom Coatings—doing business in this space have reported high penetration levels within the mattress top markets, but they continue to eye the passage extended regulations, covering upholstered furniture and top of the bed materials, as growth engines moving forward. While these regulations continue to be put on the back burner, the industry is optimistic that they will ultimately go into affect. After all the, top-of-bed legislation was more than a decade in the making and the boost that ruling gave was worth the wait for many.
The U.S. Consumer Product Safety Commission and the National Institute of Standards and Technology (NIST) continue to conduct research aimed at expanding the mattress flammability regulations. The commission also proposed an amendment to the existing mattress standard (16 CFR Part 1632) to incorporate the new Standard Reference Material cigarette developed in cooperation with NIST (SRM 1196) as the ignition source in the tests. NIST’s research on the SRM cigarette could also be incorporated into the proposed upholstered furniture rule. NIST’s research toward a possible SRM test foam is also progressing, as is other continuing testing at the CPSC laboratory.
Among these tests is the reported development—by the NIST —of a bench mock-up flammability test for furniture. Some current standards require you test an entire piece of furniture but with the bench scale, you can do a mock-up and if it passes you may not have to burn a full piece of assembled furniture. It allows companies to start doing a lot more testing of combinations. One of the approaches that NIST is working with is a ‘layer-upon-layer’ approach. If the upholstery fabric is flame resistant and the first layer below it is flame resistant, and so on, you may be able to pass a more severe test than if only one layer has some fire protection in it.”
In the meantime, the NIST is providing resources for companies that might want to target this market when the time comes. The institute’s website has a list of requirements a barrier product has to meet and nonwovens makers and suppliers are now working on making their offerings more robust because they are trying to protect a lot more polyurethane foam in the furniture than they had to protect in mattresses.
Beyond the furniture market, flammability efforts are being made in protective apparel, military and aerospace applications, to name a few. In response to this, nonwovens makers and their suppliers are constantly broadening their efforts in this technology.
Raw material supplier Leigh Fibers is focusing on the flame retardant market with its SafeLeigh product line. The line, which is inherently fire retardant and made from recycled materials can be used in heat and flame barriers and insulation products.
“Inherent fire retardancy means that our customers don't need to use chemical treatments, eliminating drying and processing time. Because SafeLeigh is made from recycled materials, it helps our customers meet their buyers’ green requirements and reduces landfill waste,” said Parris Hicks-Chernez, marketing and advertising manager.
Hicks-Chernez says Leigh Fibers has seen an increased interest in SafeLeigh as a result of new legislation as well as a push from the final customer for green and
Another company making headway in the FR materials market is Precision Custom Coatings, Totowa, NJ with its Satin FR line. Noting that Precision offers FR barriers that address the regulations as well as polyester quilting materials and laminated components.
Meanwhile, Lenzing produces a flame resistant cellulose fiber, Lenzing FR. It is made from wood pulp which is extracted from trees grown in managed forests. “We make it flame resistant by including an additive in the fiber during manufacture,” says Tom Burrow, marketing manager Lenzing FR. “This is permanent—it cannot be washed out and stays with the fiber for the whole of its life, so the fiber is inherently flame retardant.
Lenzing FR is used in a range of protective clothing. Tencate produce Defender M which is used by the U.S. military for their battledress uniforms. Meanwhile other fabrics are produced for use in firefighting, metal and glass splash protection, electric arc protection and welding protection. Lenzing FR fabrics work well in these applications because when exposed to flame or intense heat they char but do not shrink or split open. Fabrics are comfortable to wear because the cellulose from which the fiber is made is hydrophilic and has excellent moisture handling capabilities, Burrow adds. “The fiber is produced from highly sustainable raw material and can be easily disposed of at the end of its life,” he explains.
In January, Lenzing announced it had sealed a deal with the U.S. military to supply flame-resistant specialty fibers for a new generation of U.S. Army combat uniforms. The signature of U.S. President Obama on December 31, 2011 formally approving the National Defense Authorization Act enables the delivery of “TenCate Defender” uniform fabrics for an unlimited period of time (“permanent waiver”). The key component included in this fabric is the heat protection fiber Lenzing FR of the Austrian Lenzing Group. In principle, only clothing products with the “Made in USA” seal are allowed for the U.S. Army. Up until now, textiles made from Lenzing fibers were supplied on the basis of a limited exemption granted in the year 2008.
Clariant Takes Green Approach to FR
Clariant’s latest offering to the flame retardant market is the Pekoflam system, which the company is touting as a fundamental breakthrough in durable FR finishes heralding a new generation in the production of FR protective textiles. Clariant’s bicomponent system, Pekoflam ECO and Pekoflam SYN, meets the needs of the textile industry for a more sustainable and high performance FR application that can be used with existing equipment.
“The Pekoflam process is based on a synergistic application of phosphorus and nitrogen,” explains Thomas Winkler, head of Clariant’s Business Unit Textile Chemicals. “When we were examining the methods currently in use for creating fire retardant textiles as part of our innovation program, we knew we had to move away from traditional methods and get rid of any formaldehyde emissions. Balancing our innovation parameters of cost effectiveness, safety and sustainability, while at the same time providing a viable, commercial solution for our partners in the global textile industry, has taken some three years of research and development where the final solution was jointly developed utilizing an external research and development partnership. The result has been worth the wait.”
The new bicomponent Pekoflam system – ECO for ecological and economic, SYN for synergy – has a very low impact on the fabric strength to which it is applied.
By creating the new Pekoflam system, which is suited to cotton and cotton-rich blends, Clariant is again broadening the opportunities for manufacturers to develop their product range and markets. Until now, they have had to rely mainly on systems based on commodity chemistry that can be very restrictive, especially in the production of materials that may be used in children’s clothing. As health and safety issues have grown in recent years, the manufacturers have been targeted for alternative materials by many brands and retailers of home textiles.
Clariant’s Textile business has been focusing successfully on non-halogenated* products for a fairly long time. Finally – with Pekoflam – the problem of formaldehyde and amine emissions* has also been eliminated in FR systems. Moreover, the current FR systems also can affect the residual tensile strength of fabrics, which places severe limitations on the weights of fabric that could be produced.
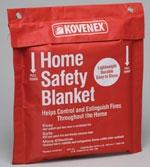
Flame retardant products are creeping into
the consumer goods market like this fire
extinguishing blanket to help put out home fires.
“The new Clariant chemistry is not simply another product on the market – it provides a fundamental and far-reaching change to the way the producers of FR fabric have been forced to work. The new system doesn’t contain any SVHC2 restricted chemicals, commonly used in FR and it’s cost efficient, too,” says Mr. Winkler. The Clariant theme of Sustainable Protection will also highlight another innovation in fire retardant finishing. Pekoflam HFC is a novel powder flame retardant coating technology, in which organic phosphinate compounds substitute for halogen-based systems. It focuses on applications to synthetic fibers, especially for the upholstery sector and carpeting. The non-halogenated coating reduces smoke emissions, a problematical aspect associated with halogen based coatings. Pekoflam HFC provides high performance on synthetic fibers and blends. It has better binder compatibility and a lower impact on rheological behavior commonly observed by increased viscosity when compared to other phosphorus based powder flame retardants.
Passed nationally in 2006, this legislation created a temporary boom for nonwovens producers in this category. While the flammability effect could be achieved in traditional woven mattress tops, many bedding manufacturers opted for nonwovens because of their ability to achieve the results right in the manufacturing process without the use of an extra step post production. Additionally, the use of nonwovens requires less toxic aftertreatments, making the final product safer for consumers.
Five years after the ruling, most of the nonwovens manufacturers—including Milliken, Freudenberg and Precision Custom Coatings—doing business in this space have reported high penetration levels within the mattress top markets, but they continue to eye the passage extended regulations, covering upholstered furniture and top of the bed materials, as growth engines moving forward. While these regulations continue to be put on the back burner, the industry is optimistic that they will ultimately go into affect. After all the, top-of-bed legislation was more than a decade in the making and the boost that ruling gave was worth the wait for many.
The U.S. Consumer Product Safety Commission and the National Institute of Standards and Technology (NIST) continue to conduct research aimed at expanding the mattress flammability regulations. The commission also proposed an amendment to the existing mattress standard (16 CFR Part 1632) to incorporate the new Standard Reference Material cigarette developed in cooperation with NIST (SRM 1196) as the ignition source in the tests. NIST’s research on the SRM cigarette could also be incorporated into the proposed upholstered furniture rule. NIST’s research toward a possible SRM test foam is also progressing, as is other continuing testing at the CPSC laboratory.
Among these tests is the reported development—by the NIST —of a bench mock-up flammability test for furniture. Some current standards require you test an entire piece of furniture but with the bench scale, you can do a mock-up and if it passes you may not have to burn a full piece of assembled furniture. It allows companies to start doing a lot more testing of combinations. One of the approaches that NIST is working with is a ‘layer-upon-layer’ approach. If the upholstery fabric is flame resistant and the first layer below it is flame resistant, and so on, you may be able to pass a more severe test than if only one layer has some fire protection in it.”
In the meantime, the NIST is providing resources for companies that might want to target this market when the time comes. The institute’s website has a list of requirements a barrier product has to meet and nonwovens makers and suppliers are now working on making their offerings more robust because they are trying to protect a lot more polyurethane foam in the furniture than they had to protect in mattresses.
Beyond the furniture market, flammability efforts are being made in protective apparel, military and aerospace applications, to name a few. In response to this, nonwovens makers and their suppliers are constantly broadening their efforts in this technology.
Raw material supplier Leigh Fibers is focusing on the flame retardant market with its SafeLeigh product line. The line, which is inherently fire retardant and made from recycled materials can be used in heat and flame barriers and insulation products.
“Inherent fire retardancy means that our customers don't need to use chemical treatments, eliminating drying and processing time. Because SafeLeigh is made from recycled materials, it helps our customers meet their buyers’ green requirements and reduces landfill waste,” said Parris Hicks-Chernez, marketing and advertising manager.
Hicks-Chernez says Leigh Fibers has seen an increased interest in SafeLeigh as a result of new legislation as well as a push from the final customer for green and
Another company making headway in the FR materials market is Precision Custom Coatings, Totowa, NJ with its Satin FR line. Noting that Precision offers FR barriers that address the regulations as well as polyester quilting materials and laminated components.
Meanwhile, Lenzing produces a flame resistant cellulose fiber, Lenzing FR. It is made from wood pulp which is extracted from trees grown in managed forests. “We make it flame resistant by including an additive in the fiber during manufacture,” says Tom Burrow, marketing manager Lenzing FR. “This is permanent—it cannot be washed out and stays with the fiber for the whole of its life, so the fiber is inherently flame retardant.
Lenzing FR is used in a range of protective clothing. Tencate produce Defender M which is used by the U.S. military for their battledress uniforms. Meanwhile other fabrics are produced for use in firefighting, metal and glass splash protection, electric arc protection and welding protection. Lenzing FR fabrics work well in these applications because when exposed to flame or intense heat they char but do not shrink or split open. Fabrics are comfortable to wear because the cellulose from which the fiber is made is hydrophilic and has excellent moisture handling capabilities, Burrow adds. “The fiber is produced from highly sustainable raw material and can be easily disposed of at the end of its life,” he explains.
In January, Lenzing announced it had sealed a deal with the U.S. military to supply flame-resistant specialty fibers for a new generation of U.S. Army combat uniforms. The signature of U.S. President Obama on December 31, 2011 formally approving the National Defense Authorization Act enables the delivery of “TenCate Defender” uniform fabrics for an unlimited period of time (“permanent waiver”). The key component included in this fabric is the heat protection fiber Lenzing FR of the Austrian Lenzing Group. In principle, only clothing products with the “Made in USA” seal are allowed for the U.S. Army. Up until now, textiles made from Lenzing fibers were supplied on the basis of a limited exemption granted in the year 2008.
Clariant Takes Green Approach to FR
Clariant’s latest offering to the flame retardant market is the Pekoflam system, which the company is touting as a fundamental breakthrough in durable FR finishes heralding a new generation in the production of FR protective textiles. Clariant’s bicomponent system, Pekoflam ECO and Pekoflam SYN, meets the needs of the textile industry for a more sustainable and high performance FR application that can be used with existing equipment.
The new bicomponent Pekoflam system – ECO for ecological and economic, SYN for synergy – has a very low impact on the fabric strength to which it is applied.
By creating the new Pekoflam system, which is suited to cotton and cotton-rich blends, Clariant is again broadening the opportunities for manufacturers to develop their product range and markets. Until now, they have had to rely mainly on systems based on commodity chemistry that can be very restrictive, especially in the production of materials that may be used in children’s clothing. As health and safety issues have grown in recent years, the manufacturers have been targeted for alternative materials by many brands and retailers of home textiles.
Clariant’s Textile business has been focusing successfully on non-halogenated* products for a fairly long time. Finally – with Pekoflam – the problem of formaldehyde and amine emissions* has also been eliminated in FR systems. Moreover, the current FR systems also can affect the residual tensile strength of fabrics, which places severe limitations on the weights of fabric that could be produced.
Flame retardant products are creeping into
the consumer goods market like this fire
extinguishing blanket to help put out home fires.
“The new Clariant chemistry is not simply another product on the market – it provides a fundamental and far-reaching change to the way the producers of FR fabric have been forced to work. The new system doesn’t contain any SVHC2 restricted chemicals, commonly used in FR and it’s cost efficient, too,” says Mr. Winkler. The Clariant theme of Sustainable Protection will also highlight another innovation in fire retardant finishing. Pekoflam HFC is a novel powder flame retardant coating technology, in which organic phosphinate compounds substitute for halogen-based systems. It focuses on applications to synthetic fibers, especially for the upholstery sector and carpeting. The non-halogenated coating reduces smoke emissions, a problematical aspect associated with halogen based coatings. Pekoflam HFC provides high performance on synthetic fibers and blends. It has better binder compatibility and a lower impact on rheological behavior commonly observed by increased viscosity when compared to other phosphorus based powder flame retardants.