Tara Olivo, Associate Editor08.05.19
Industry 4.0—also referred to as the fourth industrial revolution, smart manufacturing, or the IIoT (Industrial Internet of Things)—has taken hold in the nonwovens industry. Machinery and equipment manufacturers have developed platforms that offer a new level of interconnectivity in manufacturing, encompassing automation, digitization, M2M (machine-to-machine) technologies, machine learning, real-time data and more.
While still considered in its early stages—and not without some challenges—organizations across the globe have already started to see the benefits that Industry 4.0 concepts have brought to the manufacturing landscape.
One of the immediate benefits of Industry 4.0 technologies is improved productivity through reduced machine downtime, says Todd Dietz, general manager of Osprey Corporation, a developer of process air filtration and recycling systems for the soft disposables industry. “This reduced downtime is possible due to enhanced machine monitoring which automatically alerts customers to issues and allows for early maintenance intervention.”
A second benefit of the technology, he adds, is reduced costs through energy monitoring. “The first step is to show customers what the actual power usage of their system is at any given time, but the real benefit comes from being able to correlate the amount of power usage to different operating conditions or system settings. This information enables customers to make more informed choices to help reduce the overall energy usage for their system,” he explains.
Osprey equipment includes many types of IoT devices such as machine sensors and power monitoring equipment. The data produced by this sensor technology is connected to the cloud via secure VPN devices, where customers can access the information through the OspreyCONNECT application.
“Large amounts of IoT data by itself has limited usage, but its value can be unlocked by generating predictive maintenance recommendations and operational alerts through data analysis,” Dietz says. “Therefore, data analytics is becoming one area of focus for our ongoing improvement efforts. We are also developing a remote mentor solution which allows customers and technicians to visualize IoT data and collaborate with other experts while interfacing with the equipment.”
The objective of machinery supplier A.Celli Group involves the global integration of the machines, starting with those for winding and rewinding processes, extended to offer integrated solutions for managing and optimizing storage, preparation and freight forwarding processes. For this reason, the company’s vision is strongly focused on digitalization and integration issues. A.Celli group invested in the creation of a dedicated structure to smart technologies called Extreme Automation.
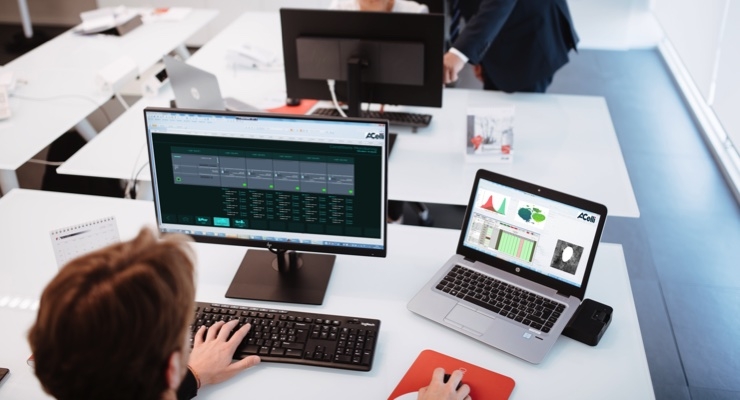
Photo courtesy of A.Celli
The Industry 4.0 Extreme Automation solution is divided in two main categories of service, field technologies and a cloud integrated platform. Field technologies are intended to provide immediate solutions to real time processes through innovations like “Automatic Defect Recognition,” to classify and to catalogue production defects using AI algorithms based on neural networks. The cloud integrated platform is intended to provide a distributed monitoring system called “dashboard machine monitoring,” an industrial business intelligence platform called “Efficiency 4.0,” and a product passport methodology called “iREEL” to improve the production performances and a fully integrated framework to enable the dialogue between data coming from machines and data available in the industrial and business software application like MES, PLM, ERP etc., according to Daniele Cardesi, digital solutions manager at A.Celli.
With the Extreme Automation solution, A.Celli has already seen a high potential and interest around the analysis of idle times to improve performances. “We have already mapped many idle conditions, and we are still improving the collection of data, offering digital reporting tools to qualify any idle condition in the process and to give insights about where to intervene promptly and where to plan a review of the processes,” Cardesi says.
Nonwoven systems supplier Andritz pools all of the digital solutions it develops under a brand called Metris. Metris technologies are aimed at digitalizing and networking machines and plants. With the help of the Metris UX platform, the customer has a single interface that offers access to all the different solutions and applications it provides for machinery and processes. All solutions and elements are compatible with one another, but can also be used individually so each customer receives a personalized IIoT solution.
The newly developed Metris UX digital platform is a human-machine interface that enables full support for industrial plants throughout their entire life cycle. It combines the functionalities of a distributed control system (DCS), simulation of production and real-time plant simulation, and condition monitoring with smart sensors in an integrated approach.
“The platform allows our customers to use functionalities for data analytics to set up a complete distributed control system (Metris X), and it serves as an integrated tool for optimization of process performance contracts (Metris OPP),” says Andreas Lukas, senior vice president and division manager of Andritz Nonwoven.
As part of Andritz Digital Solutions, Metris Smart Service focuses on the optimization and digitalization of internal and external business processes. With the Metris Spare Parts Catalog, customers can order spare and wear parts efficiently, and with Metris Customer Care – the new B2B portal – customers have a single point entry for all Andritz digital services, including assistance by means of augmented reality.
“In particular, the networking and communication of different machine elements is an initial prerequisite for smooth running of the entire line,” Lukas says. “Andritz Nonwoven offers complete solutions for needlepunch, spunlace, wetlaid and converting, from fiber preparation to the winder. As a supplier of these complete lines, we know best the areas for optimization in which IIoT can bring truly beneficial advantages. But, of course, Metris can also be implemented in any other machine element even if it does not originate from Andritz.”
Several tools are currently helping Andritz’s customers better manage production in the age of Industry 4.0. One already being used in Andritz Nonwoven’s calendering area is neXtrend remote monitoring of the installed base. “By collecting, analyzing and evaluating data, rapid forecasts can be made for maintenance activities or recommendations for the replacement or update of individual elements,” Lukas explains. “The customer receives clear information in advance and reduces the risk of unforeseen breakdowns and machine downtimes.”
Other examples of IIoT-solutions within Andritz Nonwoven are ProDyn, a system in needlepunch lines for saving raw materials, and through-air dryer humidity sensors called neXecodry and the associated control loops for energy saving.
“Both neXecodry and ProDyn are examples in which the data loop at the customer’s site remains at the production site and no further communication with Andritz server systems is required,” he continues.
According to Andritz, Metris products can help customers achieve their production and corporate goals in terms of increasing the efficiency and profitability of plants, optimizing the use of resources, avoiding breaks in production, and achieving highest product quality. “The networking of machines, processes and the people involved opens up a multitude of possibilities in control, monitoring, planning and process acceleration,” Lukas says.
For its part, Kansan Machinery integrates a range of Industry 4.0 technologies into its wet wipe machinery and equipment. These solutions include predictive maintenance components such as i/o link sensors and PLCs that help collect statistical data and monitor AI machines, as well as machines that communicate through OPC UA, a machine to machine communication protocol for industrial automation. Machines also calculate their own OEE (overall equipment effectiveness) data, which makes it possible to monitor equipment and operator efficiency.
“Industry 4.0 enables the technology to produce machines that can express themselves,” says Buse Dusunceli, area sales manager, Kansan. “What the wet wipe producer wants from the machine is to reduce the unplanned stops, machine recognizing alarming signals and forwarding the necessary information to the user which is called predictive maintenance. This opens ways to better calculate production cost and a more sensitive calculation for energy and raw material consumption.”
With Industry 4.0 solutions, machine down time has reduced significantly, while machine OEE and production process efficiency have significantly increased. “The important thing is to run the machine at the highest possible speed, therefore this technology helps with the increase of total machine production time and rates,” she adds.
Teknoweb Converting, a provider of complete manufacturing solutions for the wet wipes industry, launched its Industry 4.0 platform—The Connected Wipes—in 2017.
The Connected Wipes project features IoT (Internet of Things) framework, consisting of a specific protocol and gateway to allow machines to communicate to the manufacturer’s infrastructure; a segment dedicated to data storage; a segment focused on data processing; a tool for presentation of data based on business intelligence and analytical tools; and a business gateway to communicate to ERP and MES (Manufacture Execution Systems). Through Connected Wipes, Teknoweb also offers optional cloud technology, and all can optionally converge in a real and full MES, which becomes the backbone of shop-floor activity, according to Guido Conio, chief commercial officer, Teknoweb Converting.
“Customers expect to monitor machine performances in full and collect data to drive business decisions quickly, effectively,” he says. “Our Industry 4.0 allows customers to continuously improve results, OEE and to ultimately make more money.”
Teknoweb experienced many cases where Industry 4.0 was instrumental in achieving challenging objectives. In all projects, the company shares data collected from machines and, on a weekly basis, it defines, jointly with its customer, actions to remove basic causes of malfunctions, which can span from technological limits to training needs for operators. “We build together a path which shows progress week after week and makes the customer aware of the potential of this framework. We build confidence,” Conio adds.
When it comes to cost savings, customers using Connected Wipes can monitor performances and reasons for rejects. “Addressing these reasons makes the machine work smoother and without over-rejecting raw material and finished products,” he explains. “If you consider 85% of operating costs of a single wet wipes machine is raw materials, you would figure out immediately how much money you may save.”
Singapore-based Diaper Recycling Technology makes state-of-the-art recycling equipment that separates waste diapers back into their original raw material formats, SAP, pulp and plastic. Its proprietary technology operates at just 15KW requiring just 30 square meters of floor space while achieving break-through purity levels while not damaging the extracted SAP.
According Martin Scaife, chairman and CTO, the company’s Allen Bradley, Siemens and Mitsubishi configurations all come with Industry 4.0 interface as standard, which has hard-wire access to all system IOs, analogue and digital, as well as the full system HMI (human-machine interface) console.
“We find most companies now expect Industry 4.0 interface as standard,” Scaife says.
Diaper Recycling Technology recently added a camera surveillance package which also allows off-shore operation should its customers wish to choose this option. The optional video camera package consists of eight to 24 cameras (dependent of machine capacity) and includes an Industry 4.0 interface as standard.
“When customers see the camera footage coming from the cameras for the first time, they are typically very impressed as the images are crystal clear, having LED lighting and real time visuals from deep within the process,” he says.
Learning Curves
For companies implementing Industry 4.0 technologies, acquiring the high-tech solutions is only part of the equation. Finding the right recruits and investing in employee training are major factors to achieve success in the fourth industrial revolution.
“Many companies believe buying a technology is the only task that is required to benefit from all advantages of the Industry 4.0 framework,” says Teknoweb’s Conio. “Unfortunately you must be aware the company must adopt a new methodology to handle the machinery. First, operators must input, where required, meaningful data. Decisions must be data based. No longer just feelings and experiences, but actual data analysis.”
From Teknoweb’s point of view, it isn’t just a matter of recruiting, but training. “Being aware of change in the approach and methodology, companies must be ready to invest in training and let the operation grow following implementation of new technologies,” Conio adds.
Osprey’s Dietz agrees that training is key for companies in the age of smart manufacturing. “As more jobs become automated, industries need to re-train employees to work with the new technologies and to adapt to the digitized workplace. As a result, the demand for data scientists, programmers, and industrial designers will grow rapidly. In the past, companies could usually recruit employees which had the specific skills they needed to succeed. However, as the transition to Industry 4.0 progresses, companies will need to be prepared to provide more ongoing training to all employees in order to keep up with the rapidly evolving technology trends.”
One advantage for manufacturers, according to Dietz, is that Industry 4.0 technologies enable better employee training: virtual reality interfaces allow employees to immerse themselves in the training environment, IoT devices allow better tracking of what is happening, and real-time data analysis allows for instant feedback. “Companies will need to focus on both recruiting new employees and the retraining of existing employees if they want to succeed in the new Industry 4.0 landscape,” he says.
Because the introduction of new smart digital services requires the adoption of skills different from the ones typically available in an industry, A.Celli’s Extreme Automation offer three different helpful services. A User Experience and User Interface offers continuous improvement to simplify the access and the usability of the technologies delivered. End User training services, providing solution training and courses on digital innovation in the industrial market. And finally, a Chat-based platform guarantees the best results with the adoption of Extreme Automation solutions. “We integrated and connected to the Extreme Automation cloud platform a specific intelligent chat and chatbot platform to share data, processes and best practices between industry field operators/supervisors and machinery providers,” says Cardesi.
Other Challenges
It should be no surprise that security remains one of the main challenges being confronted in the age of Industry 4.0.
Andritz’s Lukas says the greatest challenge is to convince customers that Andritz encrypts the data they provide, keeps it absolutely secure and no third parties can gain access to it. Certain data sets are not visible to Andritz unless they are necessary, for example, for the previously-mentioned process optimization. “No customer wants his production processes to appear anywhere unexpectedly, and this wish is certainly not exclusive to our industry. Due to the sensitivity of this data, Metris’ programming must also be state-of-the-art in terms of data security,” Lukas says.
Similarly for Osprey, the biggest challenge it has experienced in implementing OspreyCONNECT is that the information technology (IT) departments of many customers are reluctant to allow their production machines to be connected to an outside network in the cloud. Because of this, these customers are not able to utilize the data-based portion of the application, and they cannot leverage data-analytics to improve operational efficiency, Dietz explains. “Osprey is working with these customers and industry groups to address security concerns.”
In the future, Osprey expects that global industry security standards will be established, which will make this IT acceptance process easier.
A related challenge is that Osprey is still in the early stages of developing robust data analytics capabilities to allow customers to make more informed decisions. But until they are able to access more field data, it is difficult to determine which types of data analysis will provide the most benefit and value to its customers, according to Dietz. “We have designed the application so that certain features will work even if the customer is not able to provide our equipment access to the cloud network. If the security concerns persist into the future, it might be necessary to move the data storage and data analytics capabilities to the local machine itself through edge computing.”
Teknoweb’s Conio agrees that customers are worried of revealing too much information with the machinery manufacturer, despite the greater benefits from implementation of Industry 4.0 framework coming from data sharing with the machine manufacturer. Customers are skeptical about the cloud, data sharing, collaborative projects and integrated synergies. “It is not easy to convince them benefits could be much greater than the risk the manufacturer knows if the machine is running and for how many hours and days,” he adds.
Scaife, of Diaper Recycling Technology, shares that company fire-walls in most instances need to be navigated to allow a correct Industry 4.0 interface to be set-up. “We find some companies desire to have a VPN connection for enhanced security; whilst this is all standard technology, it may require an additional three to four weeks to supply a system with VPN,” he says.
Predictions
Suppliers foresee that Industry 4.0 will continue to improve over the next several years, and ultimately machines will take further steps without human intervention.
Osprey believes that the manufacturing industry is still in the early stages of Industry 4.0. “Manufacturers and producers are taking advantage of sensor technology, connectivity, and data analytics to reduce costs and increase productivity on a machine by machine basis. Manufacturers are more flexible and can respond more quickly to consumer preferences due to the efficiency gains provided by the newer technologies. The next step in the evolution will be toward the creation of smart factories where the independent machines communicate together and automatically adjust their performance without user intervention. This step will probably not be widespread until global security and communication standards are established so that different manufacturers are following the same protocols.”
From A.Celli’s point of view, Industry 4.0 is already accelerating automation and production efficiency. “We are now moving from asset capability and warranty of product outcome through digital technologies, to business platform capability,” Cardesi says. “Business platform capability will be the highest goal reached by the integration of the entire digital assets. Business platform capability will allow industries, machinery suppliers, prime material and utility suppliers to cooperate in a co-innovation way, monitoring near real time process to improve the results with a very high frequency and predictive control.”
Comparing the IoT evolutions in other industries such as automotive, medical technology or the smart home sector, Andritz’s Lukas says there’s no doubt that automation and digitization will also continue to progress in the nonwoven sector. “The potential for time and cost savings as well as a learning AI for further process optimization are simply too tempting not to at least consider them,” he adds. “In the very long term, there will probably be no production technologies and machinery lines that are not fully networked with comprehensive data management as a constant companion. And as a result, all further steps for further automation will unfold. This ranges from error detection to the ordering process to delivery of the corresponding spare part to the customer and automated appointment coordination with the appropriate service staff to replace the part. In this respect, customer and supplier are growing even closer together through this automation by means of digitalization.”
Diaper Recycling Technology’s Scaife says the transformations in the past five years have been immense and they see the speed of innovation increasing. The company’s new off-shore machine operation was only launched three months ago and enables companies to operate the machine at a fraction of the cost versus on-site staff. “From an efficiency POV, we find the streamed video footages coming from directly inside the machine enables off-shore operators to have a far better understanding of the process versus operators standing next to the machine,” he explains. “We believe that with higher computing power and with AI just around the corner, video streams in five to 10 years from now will be processed centrally with essentially the computer system automatically viewing all parts of the process and automatically taking action managing the process without human intervention.”
While still considered in its early stages—and not without some challenges—organizations across the globe have already started to see the benefits that Industry 4.0 concepts have brought to the manufacturing landscape.
One of the immediate benefits of Industry 4.0 technologies is improved productivity through reduced machine downtime, says Todd Dietz, general manager of Osprey Corporation, a developer of process air filtration and recycling systems for the soft disposables industry. “This reduced downtime is possible due to enhanced machine monitoring which automatically alerts customers to issues and allows for early maintenance intervention.”
A second benefit of the technology, he adds, is reduced costs through energy monitoring. “The first step is to show customers what the actual power usage of their system is at any given time, but the real benefit comes from being able to correlate the amount of power usage to different operating conditions or system settings. This information enables customers to make more informed choices to help reduce the overall energy usage for their system,” he explains.
Osprey equipment includes many types of IoT devices such as machine sensors and power monitoring equipment. The data produced by this sensor technology is connected to the cloud via secure VPN devices, where customers can access the information through the OspreyCONNECT application.
“Large amounts of IoT data by itself has limited usage, but its value can be unlocked by generating predictive maintenance recommendations and operational alerts through data analysis,” Dietz says. “Therefore, data analytics is becoming one area of focus for our ongoing improvement efforts. We are also developing a remote mentor solution which allows customers and technicians to visualize IoT data and collaborate with other experts while interfacing with the equipment.”
The objective of machinery supplier A.Celli Group involves the global integration of the machines, starting with those for winding and rewinding processes, extended to offer integrated solutions for managing and optimizing storage, preparation and freight forwarding processes. For this reason, the company’s vision is strongly focused on digitalization and integration issues. A.Celli group invested in the creation of a dedicated structure to smart technologies called Extreme Automation.
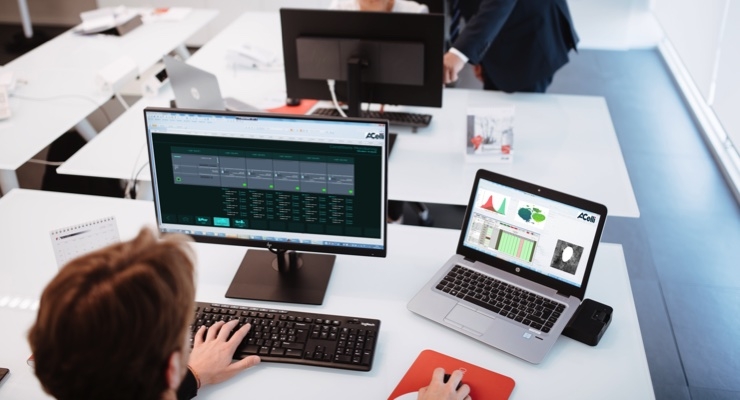
Photo courtesy of A.Celli
The Industry 4.0 Extreme Automation solution is divided in two main categories of service, field technologies and a cloud integrated platform. Field technologies are intended to provide immediate solutions to real time processes through innovations like “Automatic Defect Recognition,” to classify and to catalogue production defects using AI algorithms based on neural networks. The cloud integrated platform is intended to provide a distributed monitoring system called “dashboard machine monitoring,” an industrial business intelligence platform called “Efficiency 4.0,” and a product passport methodology called “iREEL” to improve the production performances and a fully integrated framework to enable the dialogue between data coming from machines and data available in the industrial and business software application like MES, PLM, ERP etc., according to Daniele Cardesi, digital solutions manager at A.Celli.
With the Extreme Automation solution, A.Celli has already seen a high potential and interest around the analysis of idle times to improve performances. “We have already mapped many idle conditions, and we are still improving the collection of data, offering digital reporting tools to qualify any idle condition in the process and to give insights about where to intervene promptly and where to plan a review of the processes,” Cardesi says.
Nonwoven systems supplier Andritz pools all of the digital solutions it develops under a brand called Metris. Metris technologies are aimed at digitalizing and networking machines and plants. With the help of the Metris UX platform, the customer has a single interface that offers access to all the different solutions and applications it provides for machinery and processes. All solutions and elements are compatible with one another, but can also be used individually so each customer receives a personalized IIoT solution.
The newly developed Metris UX digital platform is a human-machine interface that enables full support for industrial plants throughout their entire life cycle. It combines the functionalities of a distributed control system (DCS), simulation of production and real-time plant simulation, and condition monitoring with smart sensors in an integrated approach.
“The platform allows our customers to use functionalities for data analytics to set up a complete distributed control system (Metris X), and it serves as an integrated tool for optimization of process performance contracts (Metris OPP),” says Andreas Lukas, senior vice president and division manager of Andritz Nonwoven.
As part of Andritz Digital Solutions, Metris Smart Service focuses on the optimization and digitalization of internal and external business processes. With the Metris Spare Parts Catalog, customers can order spare and wear parts efficiently, and with Metris Customer Care – the new B2B portal – customers have a single point entry for all Andritz digital services, including assistance by means of augmented reality.
“In particular, the networking and communication of different machine elements is an initial prerequisite for smooth running of the entire line,” Lukas says. “Andritz Nonwoven offers complete solutions for needlepunch, spunlace, wetlaid and converting, from fiber preparation to the winder. As a supplier of these complete lines, we know best the areas for optimization in which IIoT can bring truly beneficial advantages. But, of course, Metris can also be implemented in any other machine element even if it does not originate from Andritz.”
Several tools are currently helping Andritz’s customers better manage production in the age of Industry 4.0. One already being used in Andritz Nonwoven’s calendering area is neXtrend remote monitoring of the installed base. “By collecting, analyzing and evaluating data, rapid forecasts can be made for maintenance activities or recommendations for the replacement or update of individual elements,” Lukas explains. “The customer receives clear information in advance and reduces the risk of unforeseen breakdowns and machine downtimes.”
Other examples of IIoT-solutions within Andritz Nonwoven are ProDyn, a system in needlepunch lines for saving raw materials, and through-air dryer humidity sensors called neXecodry and the associated control loops for energy saving.
“Both neXecodry and ProDyn are examples in which the data loop at the customer’s site remains at the production site and no further communication with Andritz server systems is required,” he continues.
According to Andritz, Metris products can help customers achieve their production and corporate goals in terms of increasing the efficiency and profitability of plants, optimizing the use of resources, avoiding breaks in production, and achieving highest product quality. “The networking of machines, processes and the people involved opens up a multitude of possibilities in control, monitoring, planning and process acceleration,” Lukas says.
For its part, Kansan Machinery integrates a range of Industry 4.0 technologies into its wet wipe machinery and equipment. These solutions include predictive maintenance components such as i/o link sensors and PLCs that help collect statistical data and monitor AI machines, as well as machines that communicate through OPC UA, a machine to machine communication protocol for industrial automation. Machines also calculate their own OEE (overall equipment effectiveness) data, which makes it possible to monitor equipment and operator efficiency.
“Industry 4.0 enables the technology to produce machines that can express themselves,” says Buse Dusunceli, area sales manager, Kansan. “What the wet wipe producer wants from the machine is to reduce the unplanned stops, machine recognizing alarming signals and forwarding the necessary information to the user which is called predictive maintenance. This opens ways to better calculate production cost and a more sensitive calculation for energy and raw material consumption.”
With Industry 4.0 solutions, machine down time has reduced significantly, while machine OEE and production process efficiency have significantly increased. “The important thing is to run the machine at the highest possible speed, therefore this technology helps with the increase of total machine production time and rates,” she adds.
Teknoweb Converting, a provider of complete manufacturing solutions for the wet wipes industry, launched its Industry 4.0 platform—The Connected Wipes—in 2017.
The Connected Wipes project features IoT (Internet of Things) framework, consisting of a specific protocol and gateway to allow machines to communicate to the manufacturer’s infrastructure; a segment dedicated to data storage; a segment focused on data processing; a tool for presentation of data based on business intelligence and analytical tools; and a business gateway to communicate to ERP and MES (Manufacture Execution Systems). Through Connected Wipes, Teknoweb also offers optional cloud technology, and all can optionally converge in a real and full MES, which becomes the backbone of shop-floor activity, according to Guido Conio, chief commercial officer, Teknoweb Converting.
“Customers expect to monitor machine performances in full and collect data to drive business decisions quickly, effectively,” he says. “Our Industry 4.0 allows customers to continuously improve results, OEE and to ultimately make more money.”
Teknoweb experienced many cases where Industry 4.0 was instrumental in achieving challenging objectives. In all projects, the company shares data collected from machines and, on a weekly basis, it defines, jointly with its customer, actions to remove basic causes of malfunctions, which can span from technological limits to training needs for operators. “We build together a path which shows progress week after week and makes the customer aware of the potential of this framework. We build confidence,” Conio adds.
When it comes to cost savings, customers using Connected Wipes can monitor performances and reasons for rejects. “Addressing these reasons makes the machine work smoother and without over-rejecting raw material and finished products,” he explains. “If you consider 85% of operating costs of a single wet wipes machine is raw materials, you would figure out immediately how much money you may save.”
Singapore-based Diaper Recycling Technology makes state-of-the-art recycling equipment that separates waste diapers back into their original raw material formats, SAP, pulp and plastic. Its proprietary technology operates at just 15KW requiring just 30 square meters of floor space while achieving break-through purity levels while not damaging the extracted SAP.
According Martin Scaife, chairman and CTO, the company’s Allen Bradley, Siemens and Mitsubishi configurations all come with Industry 4.0 interface as standard, which has hard-wire access to all system IOs, analogue and digital, as well as the full system HMI (human-machine interface) console.
“We find most companies now expect Industry 4.0 interface as standard,” Scaife says.
Diaper Recycling Technology recently added a camera surveillance package which also allows off-shore operation should its customers wish to choose this option. The optional video camera package consists of eight to 24 cameras (dependent of machine capacity) and includes an Industry 4.0 interface as standard.
“When customers see the camera footage coming from the cameras for the first time, they are typically very impressed as the images are crystal clear, having LED lighting and real time visuals from deep within the process,” he says.
Learning Curves
For companies implementing Industry 4.0 technologies, acquiring the high-tech solutions is only part of the equation. Finding the right recruits and investing in employee training are major factors to achieve success in the fourth industrial revolution.
“Many companies believe buying a technology is the only task that is required to benefit from all advantages of the Industry 4.0 framework,” says Teknoweb’s Conio. “Unfortunately you must be aware the company must adopt a new methodology to handle the machinery. First, operators must input, where required, meaningful data. Decisions must be data based. No longer just feelings and experiences, but actual data analysis.”
From Teknoweb’s point of view, it isn’t just a matter of recruiting, but training. “Being aware of change in the approach and methodology, companies must be ready to invest in training and let the operation grow following implementation of new technologies,” Conio adds.
Osprey’s Dietz agrees that training is key for companies in the age of smart manufacturing. “As more jobs become automated, industries need to re-train employees to work with the new technologies and to adapt to the digitized workplace. As a result, the demand for data scientists, programmers, and industrial designers will grow rapidly. In the past, companies could usually recruit employees which had the specific skills they needed to succeed. However, as the transition to Industry 4.0 progresses, companies will need to be prepared to provide more ongoing training to all employees in order to keep up with the rapidly evolving technology trends.”
One advantage for manufacturers, according to Dietz, is that Industry 4.0 technologies enable better employee training: virtual reality interfaces allow employees to immerse themselves in the training environment, IoT devices allow better tracking of what is happening, and real-time data analysis allows for instant feedback. “Companies will need to focus on both recruiting new employees and the retraining of existing employees if they want to succeed in the new Industry 4.0 landscape,” he says.
Because the introduction of new smart digital services requires the adoption of skills different from the ones typically available in an industry, A.Celli’s Extreme Automation offer three different helpful services. A User Experience and User Interface offers continuous improvement to simplify the access and the usability of the technologies delivered. End User training services, providing solution training and courses on digital innovation in the industrial market. And finally, a Chat-based platform guarantees the best results with the adoption of Extreme Automation solutions. “We integrated and connected to the Extreme Automation cloud platform a specific intelligent chat and chatbot platform to share data, processes and best practices between industry field operators/supervisors and machinery providers,” says Cardesi.
Other Challenges
It should be no surprise that security remains one of the main challenges being confronted in the age of Industry 4.0.
Andritz’s Lukas says the greatest challenge is to convince customers that Andritz encrypts the data they provide, keeps it absolutely secure and no third parties can gain access to it. Certain data sets are not visible to Andritz unless they are necessary, for example, for the previously-mentioned process optimization. “No customer wants his production processes to appear anywhere unexpectedly, and this wish is certainly not exclusive to our industry. Due to the sensitivity of this data, Metris’ programming must also be state-of-the-art in terms of data security,” Lukas says.
Similarly for Osprey, the biggest challenge it has experienced in implementing OspreyCONNECT is that the information technology (IT) departments of many customers are reluctant to allow their production machines to be connected to an outside network in the cloud. Because of this, these customers are not able to utilize the data-based portion of the application, and they cannot leverage data-analytics to improve operational efficiency, Dietz explains. “Osprey is working with these customers and industry groups to address security concerns.”
In the future, Osprey expects that global industry security standards will be established, which will make this IT acceptance process easier.
A related challenge is that Osprey is still in the early stages of developing robust data analytics capabilities to allow customers to make more informed decisions. But until they are able to access more field data, it is difficult to determine which types of data analysis will provide the most benefit and value to its customers, according to Dietz. “We have designed the application so that certain features will work even if the customer is not able to provide our equipment access to the cloud network. If the security concerns persist into the future, it might be necessary to move the data storage and data analytics capabilities to the local machine itself through edge computing.”
Teknoweb’s Conio agrees that customers are worried of revealing too much information with the machinery manufacturer, despite the greater benefits from implementation of Industry 4.0 framework coming from data sharing with the machine manufacturer. Customers are skeptical about the cloud, data sharing, collaborative projects and integrated synergies. “It is not easy to convince them benefits could be much greater than the risk the manufacturer knows if the machine is running and for how many hours and days,” he adds.
Scaife, of Diaper Recycling Technology, shares that company fire-walls in most instances need to be navigated to allow a correct Industry 4.0 interface to be set-up. “We find some companies desire to have a VPN connection for enhanced security; whilst this is all standard technology, it may require an additional three to four weeks to supply a system with VPN,” he says.
Predictions
Suppliers foresee that Industry 4.0 will continue to improve over the next several years, and ultimately machines will take further steps without human intervention.
Osprey believes that the manufacturing industry is still in the early stages of Industry 4.0. “Manufacturers and producers are taking advantage of sensor technology, connectivity, and data analytics to reduce costs and increase productivity on a machine by machine basis. Manufacturers are more flexible and can respond more quickly to consumer preferences due to the efficiency gains provided by the newer technologies. The next step in the evolution will be toward the creation of smart factories where the independent machines communicate together and automatically adjust their performance without user intervention. This step will probably not be widespread until global security and communication standards are established so that different manufacturers are following the same protocols.”
From A.Celli’s point of view, Industry 4.0 is already accelerating automation and production efficiency. “We are now moving from asset capability and warranty of product outcome through digital technologies, to business platform capability,” Cardesi says. “Business platform capability will be the highest goal reached by the integration of the entire digital assets. Business platform capability will allow industries, machinery suppliers, prime material and utility suppliers to cooperate in a co-innovation way, monitoring near real time process to improve the results with a very high frequency and predictive control.”
Comparing the IoT evolutions in other industries such as automotive, medical technology or the smart home sector, Andritz’s Lukas says there’s no doubt that automation and digitization will also continue to progress in the nonwoven sector. “The potential for time and cost savings as well as a learning AI for further process optimization are simply too tempting not to at least consider them,” he adds. “In the very long term, there will probably be no production technologies and machinery lines that are not fully networked with comprehensive data management as a constant companion. And as a result, all further steps for further automation will unfold. This ranges from error detection to the ordering process to delivery of the corresponding spare part to the customer and automated appointment coordination with the appropriate service staff to replace the part. In this respect, customer and supplier are growing even closer together through this automation by means of digitalization.”
Diaper Recycling Technology’s Scaife says the transformations in the past five years have been immense and they see the speed of innovation increasing. The company’s new off-shore machine operation was only launched three months ago and enables companies to operate the machine at a fraction of the cost versus on-site staff. “From an efficiency POV, we find the streamed video footages coming from directly inside the machine enables off-shore operators to have a far better understanding of the process versus operators standing next to the machine,” he explains. “We believe that with higher computing power and with AI just around the corner, video streams in five to 10 years from now will be processed centrally with essentially the computer system automatically viewing all parts of the process and automatically taking action managing the process without human intervention.”