Tara Olivo, Associate Editor08.05.19
A.Celli Nonwovens
A.Celli Nonwovens, a current leader in its market, has been manufacturing nonwoven machinery for over 75 years.
A.Celli Nonwovens offers a comprehensive range of Master Roll Winders & Slitter-Rewinders featuring state-of-the-art solutions customized to spunbond, spunmelt, spunlace and airlaid nonwovens roll goods production with a special focus on lightweight fabrics and high speed production. The machinery range is completed by non-stop flying splice unwinders and multi-functional lines. The machinery range also includes non-stop flying splice unwinders and finishing & reprocessing lines.
A.Celli F-Line solutions represent the finishing & reprocessing lines offered by A.Celli Nonwovens. This includes finishing systems for Medical Treatment Lines, Lamination Lines (maximum operating speed of 800 mpm) and Spooling Systems (production speeds up to 800 m/min).
A.Celli Iridium is printing technology developed to offer to the highest quality of printing on different kinds of substrates including nonwovens, PP/PE film and tissue, in order to make products more aesthetic.
A.Celli R-Way - integrated solutions offers the industrial sector logistic solutions such as automatic packaging systems (Slittopack), Automated Guided Vehicles (R-WAY AGV) or Automated Warehouses System.
Extreme Automation is a business unit fully dedicated to the development of innovative digital solutions for analyzing and managing machine data with a view towards Industry 4.0.
A.Celli Nonwovens emphasizes customer satisfaction with 2-CARE, a knowledgeable, efficient and consistently available customer service structure, strongly focused on providing its customers with the best assistance and assiduous service. The goal is simple: to establish long-term relationships with its sales partners based on growth and development in a spirit of mutual satisfaction.
www.acelli.it
A.C.M. Engineering
A.C.M. Engineering is the benchmark in the market for cotton pad production machines since 1998.
Cutting-edge technology, high-speed, reliability and 40 years’ experience in the cotton field make A.C.M. Engineering the standard for excellence in cotton pads converting and packaging, offering complete, trouble-free, flexible, efficient, fast and reliable production lines in a wide range and with the lowest TCO.
During the exhibition ITMA19 in Barcelona, A.C.M. Engineering presented the latest innovations for the complete range of fully automatic machines, like the troubleshoot system and maintenance assistance step-by-step, but not only this. ACM machine boost is the most advanced system for cotton pad cutting and feeding, which allows it to work without any contamination for the cotton and to have smooth forwarding, in order to reduce at the minimum the risk of stretches and breakages of the cotton lap. In addition, the system for the bags closing and sealing assure the best quality of the bags’ welding (because bags are kept continuously under tension), this means safer product and more quality for the customers and the end users.
All the innovations from ACM are focused to the production needs, in order to be “user friendly.” The machine’s design is developed for simple and versatile use. One operator can easily control two mirrored machines thanks to the high ergonomics: ACM cotton pad machines are provided with panel, bags warehouse, rolls loading and conveyor for bags exit (at table height) on the same side. Easy and quick access for the operator to each part of the machine during standard and extraordinary maintenance, combined with the remote assistance, assure the easiest diagnostic on the machine in order to keep the machine at the best condition throughout the entire lifecycle of a machine.
www.acm-engineering.it
AccuWeb
The new AccuNET from AccuWeb combines superior speed with advanced technology in a web guide controller available with a five-inch touchscreen, a switch pad HMI, or sealed enclosure for DIN rail mounting. Closed loop 32 bit processing delivers faster response times when controlling brushed or brushless actuator motors. The 24V DC AccuNET controller readily integrates with existing PLC control systems and most popular fieldbus networks, including Ethernet IP, ProfiNET, EtherCAT and Modbus TCP. Equipped with AccuWeb’s DualEdge technology for centerline guiding with a single WideArray, the AccuNet controller is also capable of web oscillation, electronic guide point adjustment, web width measurement, and web position monitoring. Made in the U.S. by AccuWeb.
www.accuweb.com
Alliance Machine and Engraving
Because failure of a calender or thermo bonder bearing in a highly automated processing line can have drastic consequences, Alliance Machine and Engraving recently introduced the Automatic Bearing Lubrication System. In addition to saving significant down time, this system also decreases the cost associated with the riggers and mechanics needed to replace bearings and repair damaged rolls. Currently, the process of monitoring and lubricating critical components requires meticulous records and diligent maintenance personnel. As firms continue to do more and more with fewer employees, Alliance responded with a system through which bearings are continuously monitored and automatically lubricated. A central control cabinet with PLC and touchscreen controls a series of solenoids that deliver oil at prescribed intervals. Another screen displays individual alarms of each circuit in the event a bearing does not receive lubrication. A single visual alarm is also activated should any alarm on the system initiate. Options include a self-contained pump, lubricant reservoir and low-level alarm. And, the system can be retrofitted to any machine.
www.alliancemachineandengraving.com
Andritz Nonwoven
One of the most important achievements is the successive renewal of Andritz’s production and assembly equipment in order to strengthen its market position.
In terms of new products, it is essential to mention the new Andritz Raconip TT textile calender for technical textiles. This calender sets new standards in terms of versatility and user-friendliness. Other important developments can be found in the needlepunch segment, with special needlelooms such as the SDV needleloom for the production of velour products that are widely used in the automotive sector.
Andritz Nonwoven has also further refined its air-through bonding technology, which is particularly suitable for the production of hygiene products such as baby diapers. In the air-through bonding segment, Andritz operates a pilot plant together with CETI (European Center for Innovative Textiles) that is available to all customers as a test facility.
Another achievement is the production of glass fiber composite products using wetlaid technology. Not only does the customer receive a solution that is specially tailored to their markets, but everything also comes from a single source.
One more achievement within the Andritz Nonwoven organization: The spunlace process has strengthened its leading position thanks to the important new contracts relating to ultra-light products used in hygiene applications. Furthermore, the innovative Spunjet process makes a real difference compared to standard spunbond fabrics, providing more softness and bulk.
Finally, the meta-subject across all technologies is Metris, the Andritz technology brand that encompasses a whole range of digital products and IIoT technologies under one roof. All of them essentially serve the purpose of smarter production.
www.andritz.com
Autefa Solutions
For many years Autefa Solutions has been one of the leading suppliers of opening/blending, web forming, web bonding and drying equipment. With the development of the new hydroentanglement machine V-Jet Futura, Autefa Solutions close the missing link in the production process of spunlace fabrics. With this important step, the company offers complete lines in all leading nonwoven technologies.
For the highly competitive spunlace market, customers request a reduction of conversion costs, for the production of direct and crosslapped spunlace products. The web forming process, consisting of the unique Injection Card and Crosslapper Topliner series, is the key for high and consistent nonwoven fabric quality. With Autefa Solutions’ new hydroentanglement machine V-Jet FUTURA and the Square Drum Dryer SQ-V, the company has developed an advanced and unique technology with special focus on energy saving. This new technology offers a significant reduction of energy consumption compared to any state-of- the-art line.
Autefa Solutions operates worldwide with own subsidiaries and with long-standing representatives and partners. A new service package, Autefa Solutions Service 4.0, covers all aspects of improving the performance of a production line during lifetime. Committed to highest quality, Autefa Solutions machines and lines function and last for many years in production with stable performances.
www.autefa.com
Beta Machinery
Established in 1959 in Busto Arsizio, Italy, Beta distinguished itself in the design and production of finishing machinery for nonwovens, technical textiles and fabrics. In 60 years of activity, over 2000 machines and 10,000 rolls have been built and sold all around the world.
Its production range includes: squeezing padders; dyeing padders; impregnation plants; high pressure calenders; and thermosetting machines.
Beta Padders and Calenders are equipped with the exclusive Beta-Roll, a patented system that assures a uniform distribution of both working pressure and temperature along the whole table-width of the rolls. The Beta-Roll makes the difference and solves the endless issue of obtaining an even squeeze (and impregnation), which translates into a perfect production.
Beta machines are designed using 3D and FEA software solutions and are built with high quality raw materials and primary brands components. Its machines are recognized worldwide for their undisputed performance, sturdy construction, long life and high flexibility. Special emphasis is devoted to the design of the safety systems, in accordance with the strictest regulations.
Beta also provides all the related accessories (unwinders/winders, accumulators, dryers, trolleys, heaters), allowing the customer to deal with only one technological and trusted partner for the supply of turnkey plants.
Since 2010 Beta is part of the Comerio Ercole Group and shares the same innovative spirit, dedication, technology and safety procedures.
www.betanonwovens.com
Catbridge Machinery
Catbridge Machinery has designed machines for nonwoven converters that offer slitting and rewinding, spray laminating, and hot melt coating in one web path.
The spray laminating and hot melt coating capabilities are available on machines ranging from large surface winders to narrow lab lines. Lab lines for testing can handle web widths as narrow as 12 inches. Surface winders such as the model 210 and 215 can handle web widths to 144 inches.
These machines integrate a variety of performance features. The tension systems precisely control a wide range of tensions, allowing converters to run diverse products. Shafted, shaftless, or driven unwinds are available. The slitting sections can include one or more slitting methods, as well as automated knife positioning systems. The coating and laminating sections feature bracketry for the adhesive applicators that enables precise position adjustments. The machines can also provide features for specific needs such as unloading tables or roll wrapping stations.
The versatile three-in-ones do the range of work typically requiring three machines. With a single piece of equipment, converters can slit and rewind, coat, or laminate a wide variety of nonwoven products.
www.catbridge.com
Chase Machine and Engineering
Since 1954, Chase Machine and Engineering has been designing and building Custom Converting Equipment to process films, foils and woven/nonwoven/knit fabrics, while controlling speed, tension and guidance. It specializes in integrating technologies such as ultrasonics, impulse welding, hot air welding, adhesive dispensing, RF welding, band sealing, extruders and CO2 lasers.
Chase Machine manufactures unwinds, rewinds, slitters, laminators, traverse winders, cut-to-length machines, festooners, accumulators, ultrasonic sewing machines as well as custom machines. Its equipment is utilized in the manufacturing of consumer products such as face masks, wipes, safety vests, air/liquid filters, medical devices and hygiene products. Chase Machine uses its 65-plus years of web handling experience to benefit customers in the filtration, medical, packaging, automotive, textile and geotextile market segments.
www.chasemachine.com
Dan-Web Machinery
Dan-Web Machinery is the leading supplier of airlaid technology, such as complete turnkey airlaid production plants for production of all types of airlaid products, as well as standalone airlaid web forming systems, for combination with other nonwoven technologies, for instance carding and spunlace.
It offers a range of defibrators/hammermills for fluff pulp for airlaid applications, as well as other applications where optimal pulp defibration and energy consumption is needed, such as diaper lines, feminine hygiene lines etc.
A new generation of through-air drying and bonding ovens, engineered by Dan-Web to meet the specific demands for dryers and ovens for producing latex, thermal and multi bonded airlaid products feature highly efficient heat management, innovative cleaning technology for both wire and dryer modules as well as all round accessibility, minimizing downtime and risk of fires.
Upgrade and capacity increase projects, where existing airlaid lines are upgraded with new web forming technology, defibrators and dryer technology.
A wide range of airlaid pilot lines, from basic solutions to complete lines, as well as laboratory sized defibration systems.
Customized solution for web handling, web formation, defibration and general solutions to customer requirements.
www.dan-web.com
Diaper Recycling Technology
Further to continued R&D investment into their low-energy technology platform, Diaper Recycling Technology are scaling-up production of their multi-award winning technology throughout 2019.
Expanding their existing facility in Singapore to four assembly bays, Diaper Recycling Technology are using their HQ facility in Singapore for final equipment assembly, customer equipment acceptance tests and customer product testing trials.
With the Generation 7 recycling process operating at energy rates lower than 10KWs, the R&D team believed they could go no further with energy reduction enhancements. Therefore with Generation 8 the R&D focus was targeted on increasing output material stream purities. Pulp purity in terms of plastic contamination on Generation 7 ranged between 99.5-99.8% and new state-of-the-art purification systems now added to the Generation 8 platform increase purity levels to over 99.9998%. This essentially means customers can operate a risk-free recycling operation where the system performance is now at a level where external contaminants such as ear plugs can be automatically removed from the material streams.
Plastic purity also remained a key focus on Generation 8. Further process enhancements are now able to achieve plastic stream purities in terms of pulp and SAP contamination of over 99.5% and some diaper products are able to achieve up to 99.998% purity. Achieving such a purity level has a double-payback for customers as essentially all pulp and SAP are recovered and the plastic stream exits the recycling process so clean plastic can be re-pelletized and sold back into the plastics industry at high value.
Open house product testing of their new Generation 8 technology will commence later in 2019 and customers are already invited to send samples to Singapore for testing.
Diaper Recycling Technology will also be holding open house events in 2019 in multiple global locations for customers wishing to trial new technologies capable to increase mixed PE/PP plastic waste streams up to $1000 per ton.
www.diaperrecycling.technology
Dilo Group
Dilo exhibited new technology and machinery for the nonwoven industry at ITMA 2019 and received an overwhelming positive response. Dilo offers complete lines, from fiber preparation, to carding, crosslapping or aerodynamic webforming, needlepunching or other consolidation technologies for any fiber material or application.
Dilo’s innovations at ITMA open new markets for nonwovens worldwide:
The H Alpha loom is a new Hyperpunch version. By reducing detrimental draft, increasing throughput speed and lowering costs, it now becomes also interesting for universal applications. The surface quality of nonwovens is an important parameter and highly influenced by the needle pattern. The new needle pattern “8000X” can be considered a breakthrough for realizing very uniform stitch distributions over a wide range of line speed. The related “6000X” is also suitable for Hyperpunch needle looms.
Dilo shows completely new potentials for the nonwoven industry with its 3D-Lofter for additive textile manufacturing. This new web forming technology can be described as 3D printing with fibers and opens a vast range of new applications within the nonwoven process such as stress tailored automotive parts, extended color patterning of floor coverings or highly uniform pre-carded web for high-precision nonwovens.
Many further developments in fiber preparation, card feeding and crosslapping were made and with the implementation of I4.0 modules Dilo is looking forward to future projects which fulfill the highest demands for quality and productivity.
www.dilo.de
Enka Tecnica
As pioneers of precision spinnerets, dies and melt blown die tips dating back to 1910, Enka Tecnica has used this collective expertise and state of the art manufacturing technology to produce complete melt blown spin beam assemblies for hygiene, filtration and absorbent melt blown nonwoven production. Enka Tecnica delivers a completely vendor-neutral individual component based on their extensive knowledge and configured to the end customer’s system.
The Enka Tecnica Melt Blown Smart Dies are designed specifically for the requirements of the user. They have developed simpler, user-friendly functions such as cassette assembly, enabling for faster and easier settings. Fewer steps means more time for other processes resulting in greater efficiency. The MB Smart dies have longer cycle times meaning longer times between die tip exchanges, a more stable die tip geometry resulting in a lower risk of mechanical damage, and shorter change over times due to the fixed settings for air gap and set back. In addition to these key features, MB Smart dies have highly uniform air gaps for better process air distribution resulting in cross directional uniformity, and they are more energy efficient than older designs due to efficient heating elements and optimum insulation.
For Enka Tecnica, productivity means delivering exactly what the customer needs. Technical parameters such as the working width, hole density (hpi), capillary diameter and capillary length, Air Gap and Setback are all highly flexible.
www.enkatecnica.com
Filcon Fabrics
Filcon Fabrics announces SPUNPRO-7, its latest patented product for nonwovens makers. Filcon’s SPUNPRO series of belts for nonwoven lines are developed to ensure optimal web formation quality, accommodate the lightest web weights, and run at maximum production speeds.
SPUNPRO-7 belt offers a distinct and significant cleanability advantage over the already successful SPUNPRO-6. Filcon Fabrics knows that time spent cleaning a production line translates into less time rolling out product. Focused on “cleanability,” its engineering design team has developed a new patented belt structure that better resists resin from getting inside the belt. When cleaning SPUNPRO-7, resin drop removal is easier than before, thus minimizing damage to belt due to forceful cleaning. In sum, these benefits of SPUNPRO-7, lead to a longer and more productive belt life.
Filcon Fabrics, a division of Nippon Filcon Company Limited, is a global, R&D-driven manufacturer of high-performance forming belts that meet the demanding requirements of today’s nonwovens industry. A trusted partner to over 75% of Japanese nonwovens producers, Filcon has specialized in the design and manufacture of forming wires and belts for various industries for over 100 years.
Globally, its number of satisfied customers is steadily growing throughout North America, Europe and Asia. Filcon is confident that its innovative technology can help nonwovens manufacturers improve their levels of quality and productivity.
www.filcon-fabrics.com
Hyperion Materials & Technologies
Hyperion Materials & Technologies is a global leader in hard and super-hard materials with more than 60 years of experience in cemented carbide, diamond and cubic boron nitride technologies. Formerly part of Sandvik, Hyperion in July marked its first year as an independent company following an investment from KKR. Hyperion offers an extensive portfolio of products and custom solutions for many industries, including an extensive range of rotary cutters and cutting units for the hygiene market.
Embracing the trend of Industry 4.0, Hyperion developed IQUT, an intelligent rotary cutting solution for converting lines that monitors and records real-time data. By collecting and analyzing data, IQUT allows on-time reactivity and predictive maintenance, which optimizes overall equipment effectiveness and generates continuous savings.
Another one of Hyperion’s new offerings for the rotary cutter market is its Bridge product line. Bridge complements the company’s Expert rotary cutter product line by offering a middle-range solution between steel equipment and premium tungsten carbide solutions.
Hyperion also recently upgraded its rotary cutter regrinding capacity in China. The investment benefits customers by increasing the maximum outer diameter and total weight of the tools the company can regrind.
www.hyperionmt.com
Investkonsult Sweden
Investkonsult Sweden, a specialized consultant and broker, serving nonwoven and absorbent hygiene producers globally, is fully committed to meeting the needs from clients and serving its customers worldwide. The company currently has two major ongoing projects. The first one is a full turnkey project of relocating and starting up one Reicofil spunbond line. Investkonsult acts as both buyer and seller (in order to make it easy for the original owner as well as the new end-user) and also handles project management and oversees the entire project, an extensive task that includes many functions such as dismantling, loading, shipping and document handling related to all stages of the process. The company’s managing director, Johan Berlin, says: “This is one of our major strengths, our ability and know-how regarding all parameters of bringing such a large project safe and sound from A to Z. I believe that we are the only company in the world that have actually completed sales of surplus Reicofil spunmelt lines. Our customers can depend on us to handle projects like this.”
The second ongoing project is to oversee and reconfigure an upgrade of a (used) meltblown line that was delivered in 2017 to a customer in India. Mr. Berlin continues: “In a case like this we support the customer with ideas, project management, as well as more equipment in order to be able to achieve the task that the customer have given to us, so that the customer can focus on their core business. For this customer we are also just in the initiating phase of delivering a complete (used) geotex-line, and we are looking at delivery around Q3 2019.”
For more info about Investkonsult Sweden, check its new website that launched in conjunction with the IDEA2019 exhibition.
www.ik.se
Kansan Machinery
Kansan Machinery is known for continuously upgrading its machines to provide easier maintenance and higher machine uptime in order to increase its customers’ OEE statistics. Recently it focused on its cross-fold lines which are already highly appreciated by manufacturers all over the world. Even though it is already very compact, the machine footprint is now smaller along with a more ergonomic design. Everywhere is easily reachable by the operator. It is possible to get up to 3000 wipes per minute thanks to the mechanical improvements. These improvements removed the sensitive equipment from the wet area allowing for a more spacious adjustment area and more areas are accessible for cleaning. There is also a new wetting system employed to use on flushable and dispersible materials.
It is to Kansan’s advantage that it has such strong communication with its customers that with their feedback it is allowed to do constant improvements. And with its improvements customers are able to increase their productivity.
www.kansanmak.com
Martin Automatic
For more than 25 years, nonwoven material converters have turned to Martin Automatic’s MAS line of zero-speed, automatic splicers to help them reduce waste and improve productivity. The MAS series accommodates webs up to 160 in/4m wide and splicing speeds up to 3000 fpm/914 mpm. With more than 55 of these high performance splicers sold, Martin’s web transport, tension control and reliable splicing expertise have been trusted to feed the most demanding, high-capacity, high speed production lines around the world. The MAS nonwoven series can make either tapeless heatseal splices or taped lap splices. Most recently, Martin supplied two 126 in/3.2m wide MAS splicers to a U.S. based company that will unwind 8.5 to 20 gsm spunbond material for wipes products.
www.martinautomatic.com
Mobi-Air
Scaling up production, Mobi-Air will be shipping in 2019 their new air filtration technology, the zero M&R tornado system which eliminates the need to operate conventional passive and active air-filtration technologies typically enclosed within drum-filters and bag-houses.
The newly developed multi-vortex technology which was displayed at last year’s ANEX Tokyo exhibition operates at only one third of the energy of a conventional cyclone. The 244 independent tornados operate at over 1000G ensuring air contaminates are fully removed from the incoming air-stream. Capable of supporting any hygiene production machine of 0-75 KCMH per Mobi-Air Module, the process has been described by leading air experts as the most significant technological breakthrough since air filtration began.
Mobi-Air engineering and R&D teams took inspiration from naturally forming multi-vortex tornados which operate at over 10 times the G-Force of cyclones whilst requiring only one third of the energy to operate. The engineering and R&D teams have been able to reduce the energy consumption by over 70% whilst also significantly increasing air quality. “Our teams are very proud of their breakthrough achievements which will benefit many industries and perhaps more importantly planet earth,” says Martin Scaife, CTO.
The breakthrough patented technology not only significantly reduces running costs through reduced energy requirements and reduced spare parts, the technology fully eliminates dust explosion risks thereby negating the need for explosion venting.
Further enhancements to the Zero Energy HVAC have also taken place. This new patented plug-in zero energy HVAC technology, when operating in closed-loop configuration, can reduce customer HVAC costs between 45-85% depending on factory location.
www.mobiair.technology
Nippon Tungsten USA
On October 14, 2009, Nippon Tungsten USA was founded as an extension of sales and resharpening services for Nippon Tungsten Co. Ltd of Japan with a dream of providing premium cutting solutions at a processing rate ahead of the rest. This location allows for many of the world’s leading companies receive the full equipment maintenance they deserve without having to ship overseas. Nippon Tungsten is the industry leader in custom, complete rotary carbide die cutting modules and provides exceptional resharpening services that raise the standard bar of excellence in its class.
NTUSA has a small group of employees whose passion for their work is displayed in the quality of each repair. Speed of the repair is enhanced by the availability of its machines and machinists. The quality of resharpening is amplified by its unprecedented manual filing technique, achieving land-width of 5 microns. The sales team provides detailed records for each order and excellent customer service. After equipment is returned, NTUSA’s assistance does not end. With a global network, on site technical support can be offered where and whenever it is required. To ensure lines are running with precision and all company needs are met choose Nippon Tungsten USA.
www.nippontungstenusa.com
Optima Nonwovens
Changing market requirements that need to be implemented quickly and increasingly complex packaging processes are only two out of the many challenges that paper hygiene product manufacturers have to face today. Labor costs and the physical strain on machine operators also need to be considered. A new solution to this problem are cobots, collaborative robots that can take care of the strenuous, repetitive tasks and are easy to program. Optima Nonwovens uses them to supply machinery with packaging materials in an automated process.
Optima Nonwovens solves the matter of maintaining an overview of flexible, automated processes with the line management software OPAL. OPAL analyzes the performance of systems and evaluates common errors systematically and across different manufacturers – for entire production plants if required. This highlights any opportunities for improvement.
Customers are also inspired by Optima’s TCAM tool. Using a HoloLens and augmented reality features, comprehensive information such as servicing videos are presented very clearly right next to the machine. The data is directly linked to the Optima Service via the Optima Cloud and is therefore always up-to-date. These and other digital Smart Services increase machine availability and thus operational efficiency.
Other news from Optima is the new Optima logistics center. It went into full operation in March. Employees completed the move and the go-live in record time. The company is now able to finalize project processes and deliver spare parts even more quickly. 60,000 items are stored in the 6,000 square meter logistics center. The warehouse processes are managed and controlled using the most state-of-the-art warehouse management software on the market – SAP Extended Warehouse Management. The modern solution is complemented by comprehensive management and control activities as well as a logistics app for internal users. The IT system is rounded off by the Optima supplier portal, which was already up and running before the move. With this overall concept, it will therefore be possible for materials management to become a completely paper-free operation in future. The neighboring Schwaebisch Hall-Hessental airport will allow the company to fly urgently needed spare parts directly to its customers in future. The other Optima business units are also located nearby and can be quickly supplied. The ergonomically furnished packing room allows spare part deliveries to be prepared efficiently and securely. The latest hardware and software solutions complement the entire system and include pick-by-motion technology – a camera system that supports employees with their picking work.
www.optima-packaging.com
Osprey Corporation
Osprey Corporation, the global leader in process air filtration for the soft disposables industry, continues to focus on improving the customer ownership experience.
OspreyCONNECT is an IoT application which provides customers access to technical information, real-time machine data, remote service capabilities, and alarm notifications. Osprey continues to add machine sensor and monitoring technology to provide better insight into machine operation, performance data, and predictive maintenance recommendations.
A review of how customers have been using OspreyCONNECT over the past few years shows that customers are receiving the most benefit from the documentation portion of the application: viewing instructional videos, receiving project updates, accessing technical documentation, sharing design details, and accessing parts information. This increased collaboration between Osprey and customers during the project lifecycle provides quicker answers to customers and allows Osprey to better understand customer needs.
Customers have been slower to embrace the data-based portion of OspreyCONNECT. Therefore, customers have yet to fully realize the potential of the application to boost productivity, improve reliability, and achieve process optimization. The slow adoption of the data analytics capabilities can be traced to one primary issue: security concerns from information technology (IT) departments. The IT departments of many companies resist the idea of allowing their data and machinery performance to be connected to the cloud, and therefore limit access to production machines from the outside.
Osprey is continuing to work with customers and industry groups to address security concerns. As global security standards are created and IT department acceptance rates increase, more customers will be able to achieve operational efficiency gains related to Industry 4.0.
www.ospreyfilters.com
Polymag Tek
Robust, innovative and configurable, Polymag Tek’s NN-WC-DS Wide Web Cleaning System, provides two-sided cleaning for webs wider than 60”(1524mm) and up to 118” (3000 mm), at speeds up to 800 fpm. This system utilizes two sets of overlapping adhesive tape rolls to remove contaminants from the Polymag Tek Blue-S Contact Cleaning Rolls (CCRs) surface. Drawer slides that exit at the end of the machine provide safe, easy, “on-the-fly” tape changes outside of the web path.
Polymag Tek’s Automated Process Roll Cleaner offers on-line cleaning capability designed to remove contamination from a process roll with minimal operator interaction. An 18” wide, fabric covered touch roll engages against the surface of the process roll to wipe/collect contamination and buildup. The cleaning head then retracts and moves to the next section and repeats the process across the entire face of the roll. Before engaging at each section, the fabric is advanced to expose a fresh wiping surface.
www.polymagtek.com
Sonobond Ultrasonics
Sonobond Ultrasonics offers a wide variety of assembly equipment for the nonwovens industry that keeps pace with the ever-expanding list of applications requiring strong, secure, sealed seams. Its SeamMaster Ultrasonic Rotary Sewing Machine, PlungeBonder, Rotary Cutters and Hand Cutters continue to replace traditional sewing and gluing methods that cannot achieve manufacturers’ stringent requirements for durable, leak-proof bonds.
The SeamMaster was introduced in 1991 to meet OSHA’s regulatory requirements for secure barrier seams in medical garments and disposable medical items. In fact, these bonded seams even meet strict NIJ standards requiring body armor’s inner cover, that surrounds the ballistic-resistant material, to be waterproof, even after submersion for 30 minutes.
Its ultrasonic machines are used to assemble some of the latest products that require strong, sealed seams, including storage pouches used to hold medical and/or dental instruments as they undergo sterilization, and then protect them while they are subsequently stored and/or transported for future use.
Since Sonobond’s ultrasonic machines eliminate stitch holes, glue gaps, fraying and unraveling, they are being used to cut and seal the edges of certified 99% lint-free cleaning wipes, ensuring there are no lint or particles which could cause problems with motors, sensitive devices or vehicles being prepped prior to priming and painting.
Secure, leak-proof, bonded seams are produced on Sonobond equipment for oil containment and spill cleanup booms, airplane acoustic and insulation panels, bedwetting protection panties, pillow and mattress covers, protective covers for outdoor furniture, and all types of filters used for commercial, industrial, food, chemical, aviation and automotive applications.
www.sonobondultrasonics.com
Teknoweb Converting
Teknoweb has recently introduced several important innovations proving its commitment to the continuous improvement of machines and to the study of new solutions that enable wet wipes converters to achieve higher performance and reliability.
The first is the completely redesigned, high-speed roto-orbital cutting unit (log saw) that can reach 600 cuts/min; specifically designed for thick ribbons (up to 100 mm), and able to effectively process a wider range of cut off lengths (from 100 to 300 mm).
The cutting blades follow the constant movement of the ribbon, by means of a lateral component of the rotational velocity, obtaining an extremely precise and vertically straight cut.
This unit has the advantage of being designed as a stand-alone model, so it can be installed on TKW converting machines as well as on folders of other manufacturers.
This roto-orbital cutting unit is extremely safe and reliable due to extensive use of materials normally found in the aerospace industry and also due to the particular use of stainless-steel safety protections.
Other new Teknoweb Converting products are the CM150 lid applicator, which pushes speeds up to 150 packs/min thanks to its double delta-type robots, and the introduction of ultrasonic film welding technology on the already extremely reliable flowpack machines, making the welding process even more stable and yielding a neater appearance of the final package.
www.teknowebconverting.com
Tokuden
Tokuden’s most recent technical development - the “Air-Cooled Hybrid Roll,” a system that enables the roll to be cooled to room temperature simply by vacuuming air through the interior of the roll. The demand for this product has increased due to the ease and simplicity of using a vacuum system. Compared to other cooling methods, this system’s ability to decrease temperature is excellent.
Utilization of the roll can be one of two types: rapid cooling or balanced cooling operation.
The purpose of rapid cooling is to improve the productivity of multi-product small volume production. In the daily production schedule, the cooling time of the roll can be decreased rapidly allowing for quicker start-up times between grade or material changes.
The purpose of balanced operation is to maintain a constant roll surface temperature. In many applications, the temperature of the substrate entering the roll will be higher than the roll’s set point temperature, thereby increasing the roll surface temperature above the set point. When this occurs, the control system will automatically switch on the air cooling, maintaining the set point temperature.
There is a high level of need for air-cooled type rolls without utilization of water. Tokuden is in the process of accumulating some basic data needed from our customers to unify a design for their Air-Cooled Hybrid Roll to meet additional applications requested.
www.tokuden.com
VAC-U-MAX
VAC-U-MAX’s Signature Series vacuum conveyors offer processors a “Plug-and-Play” solution for conveying powders, super absorbent polymers, pellets and other granular bulk materials from sources like totes, drums, bulk bags, bins and gaylords to destinations like processing or packaging lines. Each 5-part system includes pick-up wand, convey hose, vacuum receiver with automatic pulse filter cleaning, vacuum producer, and UL-listed controls. Units are available in 1500 Series for vacuum conveying applications from handfuls to 1500 lbs/hr (680 kg/hr) or the 3500 Series for conveying rates up to 3500 lbs/hr (1600 kg/hr). Systems are available in general purpose or sanitary designs.
www.vac-u-max.com
Valmet
With its acquisition of a winding equipment company, Valmet now offers the highest performing “end of line” machines to nonwoven producers seeking the highest level of control in creating and maintaining product quality. Valmet’s novel “no stress” F(O)CUS winding/slitter rewinder technology gives web producers the best way of preserving product attributes. Combined with Valmet’s THRU-AIR dryer/bonder, nonwoven web producers now have a state-of-the-art equipment option to carefully and confidently protect their spunbond and other webs all the way from drying/bonding, winding, and through packaging.
Valmet’s “end of line” machine equipment can do the best job of creating and protecting the highest quality product attributes because:
www.valmet.com
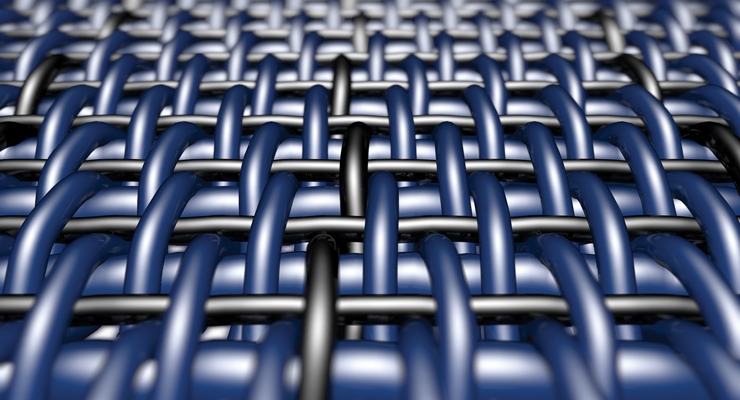
A.Celli Nonwovens, a current leader in its market, has been manufacturing nonwoven machinery for over 75 years.
A.Celli Nonwovens offers a comprehensive range of Master Roll Winders & Slitter-Rewinders featuring state-of-the-art solutions customized to spunbond, spunmelt, spunlace and airlaid nonwovens roll goods production with a special focus on lightweight fabrics and high speed production. The machinery range is completed by non-stop flying splice unwinders and multi-functional lines. The machinery range also includes non-stop flying splice unwinders and finishing & reprocessing lines.
A.Celli F-Line solutions represent the finishing & reprocessing lines offered by A.Celli Nonwovens. This includes finishing systems for Medical Treatment Lines, Lamination Lines (maximum operating speed of 800 mpm) and Spooling Systems (production speeds up to 800 m/min).
A.Celli Iridium is printing technology developed to offer to the highest quality of printing on different kinds of substrates including nonwovens, PP/PE film and tissue, in order to make products more aesthetic.
A.Celli R-Way - integrated solutions offers the industrial sector logistic solutions such as automatic packaging systems (Slittopack), Automated Guided Vehicles (R-WAY AGV) or Automated Warehouses System.
Extreme Automation is a business unit fully dedicated to the development of innovative digital solutions for analyzing and managing machine data with a view towards Industry 4.0.
A.Celli Nonwovens emphasizes customer satisfaction with 2-CARE, a knowledgeable, efficient and consistently available customer service structure, strongly focused on providing its customers with the best assistance and assiduous service. The goal is simple: to establish long-term relationships with its sales partners based on growth and development in a spirit of mutual satisfaction.
www.acelli.it
A.C.M. Engineering
A.C.M. Engineering is the benchmark in the market for cotton pad production machines since 1998.
Cutting-edge technology, high-speed, reliability and 40 years’ experience in the cotton field make A.C.M. Engineering the standard for excellence in cotton pads converting and packaging, offering complete, trouble-free, flexible, efficient, fast and reliable production lines in a wide range and with the lowest TCO.
During the exhibition ITMA19 in Barcelona, A.C.M. Engineering presented the latest innovations for the complete range of fully automatic machines, like the troubleshoot system and maintenance assistance step-by-step, but not only this. ACM machine boost is the most advanced system for cotton pad cutting and feeding, which allows it to work without any contamination for the cotton and to have smooth forwarding, in order to reduce at the minimum the risk of stretches and breakages of the cotton lap. In addition, the system for the bags closing and sealing assure the best quality of the bags’ welding (because bags are kept continuously under tension), this means safer product and more quality for the customers and the end users.
All the innovations from ACM are focused to the production needs, in order to be “user friendly.” The machine’s design is developed for simple and versatile use. One operator can easily control two mirrored machines thanks to the high ergonomics: ACM cotton pad machines are provided with panel, bags warehouse, rolls loading and conveyor for bags exit (at table height) on the same side. Easy and quick access for the operator to each part of the machine during standard and extraordinary maintenance, combined with the remote assistance, assure the easiest diagnostic on the machine in order to keep the machine at the best condition throughout the entire lifecycle of a machine.
www.acm-engineering.it
AccuWeb
The new AccuNET from AccuWeb combines superior speed with advanced technology in a web guide controller available with a five-inch touchscreen, a switch pad HMI, or sealed enclosure for DIN rail mounting. Closed loop 32 bit processing delivers faster response times when controlling brushed or brushless actuator motors. The 24V DC AccuNET controller readily integrates with existing PLC control systems and most popular fieldbus networks, including Ethernet IP, ProfiNET, EtherCAT and Modbus TCP. Equipped with AccuWeb’s DualEdge technology for centerline guiding with a single WideArray, the AccuNet controller is also capable of web oscillation, electronic guide point adjustment, web width measurement, and web position monitoring. Made in the U.S. by AccuWeb.
www.accuweb.com
Alliance Machine and Engraving
Because failure of a calender or thermo bonder bearing in a highly automated processing line can have drastic consequences, Alliance Machine and Engraving recently introduced the Automatic Bearing Lubrication System. In addition to saving significant down time, this system also decreases the cost associated with the riggers and mechanics needed to replace bearings and repair damaged rolls. Currently, the process of monitoring and lubricating critical components requires meticulous records and diligent maintenance personnel. As firms continue to do more and more with fewer employees, Alliance responded with a system through which bearings are continuously monitored and automatically lubricated. A central control cabinet with PLC and touchscreen controls a series of solenoids that deliver oil at prescribed intervals. Another screen displays individual alarms of each circuit in the event a bearing does not receive lubrication. A single visual alarm is also activated should any alarm on the system initiate. Options include a self-contained pump, lubricant reservoir and low-level alarm. And, the system can be retrofitted to any machine.
www.alliancemachineandengraving.com
Andritz Nonwoven
One of the most important achievements is the successive renewal of Andritz’s production and assembly equipment in order to strengthen its market position.
In terms of new products, it is essential to mention the new Andritz Raconip TT textile calender for technical textiles. This calender sets new standards in terms of versatility and user-friendliness. Other important developments can be found in the needlepunch segment, with special needlelooms such as the SDV needleloom for the production of velour products that are widely used in the automotive sector.
Andritz Nonwoven has also further refined its air-through bonding technology, which is particularly suitable for the production of hygiene products such as baby diapers. In the air-through bonding segment, Andritz operates a pilot plant together with CETI (European Center for Innovative Textiles) that is available to all customers as a test facility.
Another achievement is the production of glass fiber composite products using wetlaid technology. Not only does the customer receive a solution that is specially tailored to their markets, but everything also comes from a single source.
One more achievement within the Andritz Nonwoven organization: The spunlace process has strengthened its leading position thanks to the important new contracts relating to ultra-light products used in hygiene applications. Furthermore, the innovative Spunjet process makes a real difference compared to standard spunbond fabrics, providing more softness and bulk.
Finally, the meta-subject across all technologies is Metris, the Andritz technology brand that encompasses a whole range of digital products and IIoT technologies under one roof. All of them essentially serve the purpose of smarter production.
www.andritz.com
Autefa Solutions
For many years Autefa Solutions has been one of the leading suppliers of opening/blending, web forming, web bonding and drying equipment. With the development of the new hydroentanglement machine V-Jet Futura, Autefa Solutions close the missing link in the production process of spunlace fabrics. With this important step, the company offers complete lines in all leading nonwoven technologies.
For the highly competitive spunlace market, customers request a reduction of conversion costs, for the production of direct and crosslapped spunlace products. The web forming process, consisting of the unique Injection Card and Crosslapper Topliner series, is the key for high and consistent nonwoven fabric quality. With Autefa Solutions’ new hydroentanglement machine V-Jet FUTURA and the Square Drum Dryer SQ-V, the company has developed an advanced and unique technology with special focus on energy saving. This new technology offers a significant reduction of energy consumption compared to any state-of- the-art line.
Autefa Solutions operates worldwide with own subsidiaries and with long-standing representatives and partners. A new service package, Autefa Solutions Service 4.0, covers all aspects of improving the performance of a production line during lifetime. Committed to highest quality, Autefa Solutions machines and lines function and last for many years in production with stable performances.
www.autefa.com
Beta Machinery
Established in 1959 in Busto Arsizio, Italy, Beta distinguished itself in the design and production of finishing machinery for nonwovens, technical textiles and fabrics. In 60 years of activity, over 2000 machines and 10,000 rolls have been built and sold all around the world.
Its production range includes: squeezing padders; dyeing padders; impregnation plants; high pressure calenders; and thermosetting machines.
Beta Padders and Calenders are equipped with the exclusive Beta-Roll, a patented system that assures a uniform distribution of both working pressure and temperature along the whole table-width of the rolls. The Beta-Roll makes the difference and solves the endless issue of obtaining an even squeeze (and impregnation), which translates into a perfect production.
Beta machines are designed using 3D and FEA software solutions and are built with high quality raw materials and primary brands components. Its machines are recognized worldwide for their undisputed performance, sturdy construction, long life and high flexibility. Special emphasis is devoted to the design of the safety systems, in accordance with the strictest regulations.
Beta also provides all the related accessories (unwinders/winders, accumulators, dryers, trolleys, heaters), allowing the customer to deal with only one technological and trusted partner for the supply of turnkey plants.
Since 2010 Beta is part of the Comerio Ercole Group and shares the same innovative spirit, dedication, technology and safety procedures.
www.betanonwovens.com
Catbridge Machinery
Catbridge Machinery has designed machines for nonwoven converters that offer slitting and rewinding, spray laminating, and hot melt coating in one web path.
The spray laminating and hot melt coating capabilities are available on machines ranging from large surface winders to narrow lab lines. Lab lines for testing can handle web widths as narrow as 12 inches. Surface winders such as the model 210 and 215 can handle web widths to 144 inches.
These machines integrate a variety of performance features. The tension systems precisely control a wide range of tensions, allowing converters to run diverse products. Shafted, shaftless, or driven unwinds are available. The slitting sections can include one or more slitting methods, as well as automated knife positioning systems. The coating and laminating sections feature bracketry for the adhesive applicators that enables precise position adjustments. The machines can also provide features for specific needs such as unloading tables or roll wrapping stations.
The versatile three-in-ones do the range of work typically requiring three machines. With a single piece of equipment, converters can slit and rewind, coat, or laminate a wide variety of nonwoven products.
www.catbridge.com
Chase Machine and Engineering
Since 1954, Chase Machine and Engineering has been designing and building Custom Converting Equipment to process films, foils and woven/nonwoven/knit fabrics, while controlling speed, tension and guidance. It specializes in integrating technologies such as ultrasonics, impulse welding, hot air welding, adhesive dispensing, RF welding, band sealing, extruders and CO2 lasers.
Chase Machine manufactures unwinds, rewinds, slitters, laminators, traverse winders, cut-to-length machines, festooners, accumulators, ultrasonic sewing machines as well as custom machines. Its equipment is utilized in the manufacturing of consumer products such as face masks, wipes, safety vests, air/liquid filters, medical devices and hygiene products. Chase Machine uses its 65-plus years of web handling experience to benefit customers in the filtration, medical, packaging, automotive, textile and geotextile market segments.
www.chasemachine.com
Dan-Web Machinery
Dan-Web Machinery is the leading supplier of airlaid technology, such as complete turnkey airlaid production plants for production of all types of airlaid products, as well as standalone airlaid web forming systems, for combination with other nonwoven technologies, for instance carding and spunlace.
It offers a range of defibrators/hammermills for fluff pulp for airlaid applications, as well as other applications where optimal pulp defibration and energy consumption is needed, such as diaper lines, feminine hygiene lines etc.
A new generation of through-air drying and bonding ovens, engineered by Dan-Web to meet the specific demands for dryers and ovens for producing latex, thermal and multi bonded airlaid products feature highly efficient heat management, innovative cleaning technology for both wire and dryer modules as well as all round accessibility, minimizing downtime and risk of fires.
Upgrade and capacity increase projects, where existing airlaid lines are upgraded with new web forming technology, defibrators and dryer technology.
A wide range of airlaid pilot lines, from basic solutions to complete lines, as well as laboratory sized defibration systems.
Customized solution for web handling, web formation, defibration and general solutions to customer requirements.
www.dan-web.com
Diaper Recycling Technology
Further to continued R&D investment into their low-energy technology platform, Diaper Recycling Technology are scaling-up production of their multi-award winning technology throughout 2019.
Expanding their existing facility in Singapore to four assembly bays, Diaper Recycling Technology are using their HQ facility in Singapore for final equipment assembly, customer equipment acceptance tests and customer product testing trials.
With the Generation 7 recycling process operating at energy rates lower than 10KWs, the R&D team believed they could go no further with energy reduction enhancements. Therefore with Generation 8 the R&D focus was targeted on increasing output material stream purities. Pulp purity in terms of plastic contamination on Generation 7 ranged between 99.5-99.8% and new state-of-the-art purification systems now added to the Generation 8 platform increase purity levels to over 99.9998%. This essentially means customers can operate a risk-free recycling operation where the system performance is now at a level where external contaminants such as ear plugs can be automatically removed from the material streams.
Plastic purity also remained a key focus on Generation 8. Further process enhancements are now able to achieve plastic stream purities in terms of pulp and SAP contamination of over 99.5% and some diaper products are able to achieve up to 99.998% purity. Achieving such a purity level has a double-payback for customers as essentially all pulp and SAP are recovered and the plastic stream exits the recycling process so clean plastic can be re-pelletized and sold back into the plastics industry at high value.
Open house product testing of their new Generation 8 technology will commence later in 2019 and customers are already invited to send samples to Singapore for testing.
Diaper Recycling Technology will also be holding open house events in 2019 in multiple global locations for customers wishing to trial new technologies capable to increase mixed PE/PP plastic waste streams up to $1000 per ton.
www.diaperrecycling.technology
Dilo Group
Dilo exhibited new technology and machinery for the nonwoven industry at ITMA 2019 and received an overwhelming positive response. Dilo offers complete lines, from fiber preparation, to carding, crosslapping or aerodynamic webforming, needlepunching or other consolidation technologies for any fiber material or application.
Dilo’s innovations at ITMA open new markets for nonwovens worldwide:
The H Alpha loom is a new Hyperpunch version. By reducing detrimental draft, increasing throughput speed and lowering costs, it now becomes also interesting for universal applications. The surface quality of nonwovens is an important parameter and highly influenced by the needle pattern. The new needle pattern “8000X” can be considered a breakthrough for realizing very uniform stitch distributions over a wide range of line speed. The related “6000X” is also suitable for Hyperpunch needle looms.
Dilo shows completely new potentials for the nonwoven industry with its 3D-Lofter for additive textile manufacturing. This new web forming technology can be described as 3D printing with fibers and opens a vast range of new applications within the nonwoven process such as stress tailored automotive parts, extended color patterning of floor coverings or highly uniform pre-carded web for high-precision nonwovens.
Many further developments in fiber preparation, card feeding and crosslapping were made and with the implementation of I4.0 modules Dilo is looking forward to future projects which fulfill the highest demands for quality and productivity.
www.dilo.de
Enka Tecnica
As pioneers of precision spinnerets, dies and melt blown die tips dating back to 1910, Enka Tecnica has used this collective expertise and state of the art manufacturing technology to produce complete melt blown spin beam assemblies for hygiene, filtration and absorbent melt blown nonwoven production. Enka Tecnica delivers a completely vendor-neutral individual component based on their extensive knowledge and configured to the end customer’s system.
The Enka Tecnica Melt Blown Smart Dies are designed specifically for the requirements of the user. They have developed simpler, user-friendly functions such as cassette assembly, enabling for faster and easier settings. Fewer steps means more time for other processes resulting in greater efficiency. The MB Smart dies have longer cycle times meaning longer times between die tip exchanges, a more stable die tip geometry resulting in a lower risk of mechanical damage, and shorter change over times due to the fixed settings for air gap and set back. In addition to these key features, MB Smart dies have highly uniform air gaps for better process air distribution resulting in cross directional uniformity, and they are more energy efficient than older designs due to efficient heating elements and optimum insulation.
For Enka Tecnica, productivity means delivering exactly what the customer needs. Technical parameters such as the working width, hole density (hpi), capillary diameter and capillary length, Air Gap and Setback are all highly flexible.
www.enkatecnica.com
Filcon Fabrics
Filcon Fabrics announces SPUNPRO-7, its latest patented product for nonwovens makers. Filcon’s SPUNPRO series of belts for nonwoven lines are developed to ensure optimal web formation quality, accommodate the lightest web weights, and run at maximum production speeds.
SPUNPRO-7 belt offers a distinct and significant cleanability advantage over the already successful SPUNPRO-6. Filcon Fabrics knows that time spent cleaning a production line translates into less time rolling out product. Focused on “cleanability,” its engineering design team has developed a new patented belt structure that better resists resin from getting inside the belt. When cleaning SPUNPRO-7, resin drop removal is easier than before, thus minimizing damage to belt due to forceful cleaning. In sum, these benefits of SPUNPRO-7, lead to a longer and more productive belt life.
Filcon Fabrics, a division of Nippon Filcon Company Limited, is a global, R&D-driven manufacturer of high-performance forming belts that meet the demanding requirements of today’s nonwovens industry. A trusted partner to over 75% of Japanese nonwovens producers, Filcon has specialized in the design and manufacture of forming wires and belts for various industries for over 100 years.
Globally, its number of satisfied customers is steadily growing throughout North America, Europe and Asia. Filcon is confident that its innovative technology can help nonwovens manufacturers improve their levels of quality and productivity.
www.filcon-fabrics.com
Hyperion Materials & Technologies
Hyperion Materials & Technologies is a global leader in hard and super-hard materials with more than 60 years of experience in cemented carbide, diamond and cubic boron nitride technologies. Formerly part of Sandvik, Hyperion in July marked its first year as an independent company following an investment from KKR. Hyperion offers an extensive portfolio of products and custom solutions for many industries, including an extensive range of rotary cutters and cutting units for the hygiene market.
Embracing the trend of Industry 4.0, Hyperion developed IQUT, an intelligent rotary cutting solution for converting lines that monitors and records real-time data. By collecting and analyzing data, IQUT allows on-time reactivity and predictive maintenance, which optimizes overall equipment effectiveness and generates continuous savings.
Another one of Hyperion’s new offerings for the rotary cutter market is its Bridge product line. Bridge complements the company’s Expert rotary cutter product line by offering a middle-range solution between steel equipment and premium tungsten carbide solutions.
Hyperion also recently upgraded its rotary cutter regrinding capacity in China. The investment benefits customers by increasing the maximum outer diameter and total weight of the tools the company can regrind.
www.hyperionmt.com
Investkonsult Sweden
Investkonsult Sweden, a specialized consultant and broker, serving nonwoven and absorbent hygiene producers globally, is fully committed to meeting the needs from clients and serving its customers worldwide. The company currently has two major ongoing projects. The first one is a full turnkey project of relocating and starting up one Reicofil spunbond line. Investkonsult acts as both buyer and seller (in order to make it easy for the original owner as well as the new end-user) and also handles project management and oversees the entire project, an extensive task that includes many functions such as dismantling, loading, shipping and document handling related to all stages of the process. The company’s managing director, Johan Berlin, says: “This is one of our major strengths, our ability and know-how regarding all parameters of bringing such a large project safe and sound from A to Z. I believe that we are the only company in the world that have actually completed sales of surplus Reicofil spunmelt lines. Our customers can depend on us to handle projects like this.”
The second ongoing project is to oversee and reconfigure an upgrade of a (used) meltblown line that was delivered in 2017 to a customer in India. Mr. Berlin continues: “In a case like this we support the customer with ideas, project management, as well as more equipment in order to be able to achieve the task that the customer have given to us, so that the customer can focus on their core business. For this customer we are also just in the initiating phase of delivering a complete (used) geotex-line, and we are looking at delivery around Q3 2019.”
For more info about Investkonsult Sweden, check its new website that launched in conjunction with the IDEA2019 exhibition.
www.ik.se
Kansan Machinery
Kansan Machinery is known for continuously upgrading its machines to provide easier maintenance and higher machine uptime in order to increase its customers’ OEE statistics. Recently it focused on its cross-fold lines which are already highly appreciated by manufacturers all over the world. Even though it is already very compact, the machine footprint is now smaller along with a more ergonomic design. Everywhere is easily reachable by the operator. It is possible to get up to 3000 wipes per minute thanks to the mechanical improvements. These improvements removed the sensitive equipment from the wet area allowing for a more spacious adjustment area and more areas are accessible for cleaning. There is also a new wetting system employed to use on flushable and dispersible materials.
It is to Kansan’s advantage that it has such strong communication with its customers that with their feedback it is allowed to do constant improvements. And with its improvements customers are able to increase their productivity.
www.kansanmak.com
Martin Automatic
For more than 25 years, nonwoven material converters have turned to Martin Automatic’s MAS line of zero-speed, automatic splicers to help them reduce waste and improve productivity. The MAS series accommodates webs up to 160 in/4m wide and splicing speeds up to 3000 fpm/914 mpm. With more than 55 of these high performance splicers sold, Martin’s web transport, tension control and reliable splicing expertise have been trusted to feed the most demanding, high-capacity, high speed production lines around the world. The MAS nonwoven series can make either tapeless heatseal splices or taped lap splices. Most recently, Martin supplied two 126 in/3.2m wide MAS splicers to a U.S. based company that will unwind 8.5 to 20 gsm spunbond material for wipes products.
www.martinautomatic.com
Mobi-Air
Scaling up production, Mobi-Air will be shipping in 2019 their new air filtration technology, the zero M&R tornado system which eliminates the need to operate conventional passive and active air-filtration technologies typically enclosed within drum-filters and bag-houses.
The newly developed multi-vortex technology which was displayed at last year’s ANEX Tokyo exhibition operates at only one third of the energy of a conventional cyclone. The 244 independent tornados operate at over 1000G ensuring air contaminates are fully removed from the incoming air-stream. Capable of supporting any hygiene production machine of 0-75 KCMH per Mobi-Air Module, the process has been described by leading air experts as the most significant technological breakthrough since air filtration began.
Mobi-Air engineering and R&D teams took inspiration from naturally forming multi-vortex tornados which operate at over 10 times the G-Force of cyclones whilst requiring only one third of the energy to operate. The engineering and R&D teams have been able to reduce the energy consumption by over 70% whilst also significantly increasing air quality. “Our teams are very proud of their breakthrough achievements which will benefit many industries and perhaps more importantly planet earth,” says Martin Scaife, CTO.
The breakthrough patented technology not only significantly reduces running costs through reduced energy requirements and reduced spare parts, the technology fully eliminates dust explosion risks thereby negating the need for explosion venting.
Further enhancements to the Zero Energy HVAC have also taken place. This new patented plug-in zero energy HVAC technology, when operating in closed-loop configuration, can reduce customer HVAC costs between 45-85% depending on factory location.
www.mobiair.technology
Nippon Tungsten USA
On October 14, 2009, Nippon Tungsten USA was founded as an extension of sales and resharpening services for Nippon Tungsten Co. Ltd of Japan with a dream of providing premium cutting solutions at a processing rate ahead of the rest. This location allows for many of the world’s leading companies receive the full equipment maintenance they deserve without having to ship overseas. Nippon Tungsten is the industry leader in custom, complete rotary carbide die cutting modules and provides exceptional resharpening services that raise the standard bar of excellence in its class.
NTUSA has a small group of employees whose passion for their work is displayed in the quality of each repair. Speed of the repair is enhanced by the availability of its machines and machinists. The quality of resharpening is amplified by its unprecedented manual filing technique, achieving land-width of 5 microns. The sales team provides detailed records for each order and excellent customer service. After equipment is returned, NTUSA’s assistance does not end. With a global network, on site technical support can be offered where and whenever it is required. To ensure lines are running with precision and all company needs are met choose Nippon Tungsten USA.
www.nippontungstenusa.com
Optima Nonwovens
Changing market requirements that need to be implemented quickly and increasingly complex packaging processes are only two out of the many challenges that paper hygiene product manufacturers have to face today. Labor costs and the physical strain on machine operators also need to be considered. A new solution to this problem are cobots, collaborative robots that can take care of the strenuous, repetitive tasks and are easy to program. Optima Nonwovens uses them to supply machinery with packaging materials in an automated process.
Optima Nonwovens solves the matter of maintaining an overview of flexible, automated processes with the line management software OPAL. OPAL analyzes the performance of systems and evaluates common errors systematically and across different manufacturers – for entire production plants if required. This highlights any opportunities for improvement.
Customers are also inspired by Optima’s TCAM tool. Using a HoloLens and augmented reality features, comprehensive information such as servicing videos are presented very clearly right next to the machine. The data is directly linked to the Optima Service via the Optima Cloud and is therefore always up-to-date. These and other digital Smart Services increase machine availability and thus operational efficiency.
Other news from Optima is the new Optima logistics center. It went into full operation in March. Employees completed the move and the go-live in record time. The company is now able to finalize project processes and deliver spare parts even more quickly. 60,000 items are stored in the 6,000 square meter logistics center. The warehouse processes are managed and controlled using the most state-of-the-art warehouse management software on the market – SAP Extended Warehouse Management. The modern solution is complemented by comprehensive management and control activities as well as a logistics app for internal users. The IT system is rounded off by the Optima supplier portal, which was already up and running before the move. With this overall concept, it will therefore be possible for materials management to become a completely paper-free operation in future. The neighboring Schwaebisch Hall-Hessental airport will allow the company to fly urgently needed spare parts directly to its customers in future. The other Optima business units are also located nearby and can be quickly supplied. The ergonomically furnished packing room allows spare part deliveries to be prepared efficiently and securely. The latest hardware and software solutions complement the entire system and include pick-by-motion technology – a camera system that supports employees with their picking work.
www.optima-packaging.com
Osprey Corporation
Osprey Corporation, the global leader in process air filtration for the soft disposables industry, continues to focus on improving the customer ownership experience.
OspreyCONNECT is an IoT application which provides customers access to technical information, real-time machine data, remote service capabilities, and alarm notifications. Osprey continues to add machine sensor and monitoring technology to provide better insight into machine operation, performance data, and predictive maintenance recommendations.
A review of how customers have been using OspreyCONNECT over the past few years shows that customers are receiving the most benefit from the documentation portion of the application: viewing instructional videos, receiving project updates, accessing technical documentation, sharing design details, and accessing parts information. This increased collaboration between Osprey and customers during the project lifecycle provides quicker answers to customers and allows Osprey to better understand customer needs.
Customers have been slower to embrace the data-based portion of OspreyCONNECT. Therefore, customers have yet to fully realize the potential of the application to boost productivity, improve reliability, and achieve process optimization. The slow adoption of the data analytics capabilities can be traced to one primary issue: security concerns from information technology (IT) departments. The IT departments of many companies resist the idea of allowing their data and machinery performance to be connected to the cloud, and therefore limit access to production machines from the outside.
Osprey is continuing to work with customers and industry groups to address security concerns. As global security standards are created and IT department acceptance rates increase, more customers will be able to achieve operational efficiency gains related to Industry 4.0.
www.ospreyfilters.com
Polymag Tek
Robust, innovative and configurable, Polymag Tek’s NN-WC-DS Wide Web Cleaning System, provides two-sided cleaning for webs wider than 60”(1524mm) and up to 118” (3000 mm), at speeds up to 800 fpm. This system utilizes two sets of overlapping adhesive tape rolls to remove contaminants from the Polymag Tek Blue-S Contact Cleaning Rolls (CCRs) surface. Drawer slides that exit at the end of the machine provide safe, easy, “on-the-fly” tape changes outside of the web path.
Polymag Tek’s Automated Process Roll Cleaner offers on-line cleaning capability designed to remove contamination from a process roll with minimal operator interaction. An 18” wide, fabric covered touch roll engages against the surface of the process roll to wipe/collect contamination and buildup. The cleaning head then retracts and moves to the next section and repeats the process across the entire face of the roll. Before engaging at each section, the fabric is advanced to expose a fresh wiping surface.
www.polymagtek.com
Sonobond Ultrasonics
Sonobond Ultrasonics offers a wide variety of assembly equipment for the nonwovens industry that keeps pace with the ever-expanding list of applications requiring strong, secure, sealed seams. Its SeamMaster Ultrasonic Rotary Sewing Machine, PlungeBonder, Rotary Cutters and Hand Cutters continue to replace traditional sewing and gluing methods that cannot achieve manufacturers’ stringent requirements for durable, leak-proof bonds.
The SeamMaster was introduced in 1991 to meet OSHA’s regulatory requirements for secure barrier seams in medical garments and disposable medical items. In fact, these bonded seams even meet strict NIJ standards requiring body armor’s inner cover, that surrounds the ballistic-resistant material, to be waterproof, even after submersion for 30 minutes.
Its ultrasonic machines are used to assemble some of the latest products that require strong, sealed seams, including storage pouches used to hold medical and/or dental instruments as they undergo sterilization, and then protect them while they are subsequently stored and/or transported for future use.
Since Sonobond’s ultrasonic machines eliminate stitch holes, glue gaps, fraying and unraveling, they are being used to cut and seal the edges of certified 99% lint-free cleaning wipes, ensuring there are no lint or particles which could cause problems with motors, sensitive devices or vehicles being prepped prior to priming and painting.
Secure, leak-proof, bonded seams are produced on Sonobond equipment for oil containment and spill cleanup booms, airplane acoustic and insulation panels, bedwetting protection panties, pillow and mattress covers, protective covers for outdoor furniture, and all types of filters used for commercial, industrial, food, chemical, aviation and automotive applications.
www.sonobondultrasonics.com
Teknoweb Converting
Teknoweb has recently introduced several important innovations proving its commitment to the continuous improvement of machines and to the study of new solutions that enable wet wipes converters to achieve higher performance and reliability.
The first is the completely redesigned, high-speed roto-orbital cutting unit (log saw) that can reach 600 cuts/min; specifically designed for thick ribbons (up to 100 mm), and able to effectively process a wider range of cut off lengths (from 100 to 300 mm).
The cutting blades follow the constant movement of the ribbon, by means of a lateral component of the rotational velocity, obtaining an extremely precise and vertically straight cut.
This unit has the advantage of being designed as a stand-alone model, so it can be installed on TKW converting machines as well as on folders of other manufacturers.
This roto-orbital cutting unit is extremely safe and reliable due to extensive use of materials normally found in the aerospace industry and also due to the particular use of stainless-steel safety protections.
Other new Teknoweb Converting products are the CM150 lid applicator, which pushes speeds up to 150 packs/min thanks to its double delta-type robots, and the introduction of ultrasonic film welding technology on the already extremely reliable flowpack machines, making the welding process even more stable and yielding a neater appearance of the final package.
www.teknowebconverting.com
Tokuden
Tokuden’s most recent technical development - the “Air-Cooled Hybrid Roll,” a system that enables the roll to be cooled to room temperature simply by vacuuming air through the interior of the roll. The demand for this product has increased due to the ease and simplicity of using a vacuum system. Compared to other cooling methods, this system’s ability to decrease temperature is excellent.
Utilization of the roll can be one of two types: rapid cooling or balanced cooling operation.
The purpose of rapid cooling is to improve the productivity of multi-product small volume production. In the daily production schedule, the cooling time of the roll can be decreased rapidly allowing for quicker start-up times between grade or material changes.
The purpose of balanced operation is to maintain a constant roll surface temperature. In many applications, the temperature of the substrate entering the roll will be higher than the roll’s set point temperature, thereby increasing the roll surface temperature above the set point. When this occurs, the control system will automatically switch on the air cooling, maintaining the set point temperature.
There is a high level of need for air-cooled type rolls without utilization of water. Tokuden is in the process of accumulating some basic data needed from our customers to unify a design for their Air-Cooled Hybrid Roll to meet additional applications requested.
www.tokuden.com
VAC-U-MAX
VAC-U-MAX’s Signature Series vacuum conveyors offer processors a “Plug-and-Play” solution for conveying powders, super absorbent polymers, pellets and other granular bulk materials from sources like totes, drums, bulk bags, bins and gaylords to destinations like processing or packaging lines. Each 5-part system includes pick-up wand, convey hose, vacuum receiver with automatic pulse filter cleaning, vacuum producer, and UL-listed controls. Units are available in 1500 Series for vacuum conveying applications from handfuls to 1500 lbs/hr (680 kg/hr) or the 3500 Series for conveying rates up to 3500 lbs/hr (1600 kg/hr). Systems are available in general purpose or sanitary designs.
www.vac-u-max.com
Valmet
With its acquisition of a winding equipment company, Valmet now offers the highest performing “end of line” machines to nonwoven producers seeking the highest level of control in creating and maintaining product quality. Valmet’s novel “no stress” F(O)CUS winding/slitter rewinder technology gives web producers the best way of preserving product attributes. Combined with Valmet’s THRU-AIR dryer/bonder, nonwoven web producers now have a state-of-the-art equipment option to carefully and confidently protect their spunbond and other webs all the way from drying/bonding, winding, and through packaging.
Valmet’s “end of line” machine equipment can do the best job of creating and protecting the highest quality product attributes because:
- Valmet’s THRU-AIR dryer/bonder delivers the best uniformity of air temperature and air flow through the web,
- Valmet’s F(O)CUS “no stress” electromechanical winding/rewinding technology, combined with a unique application of load cell monitoring, continuously and automatically controls reel building and rewinding with each and every wrap of the growing roll, and,
- Valmet’s automatic packaging system is fully integrated into this state-of-the-art “end of line” machine offering.
www.valmet.com
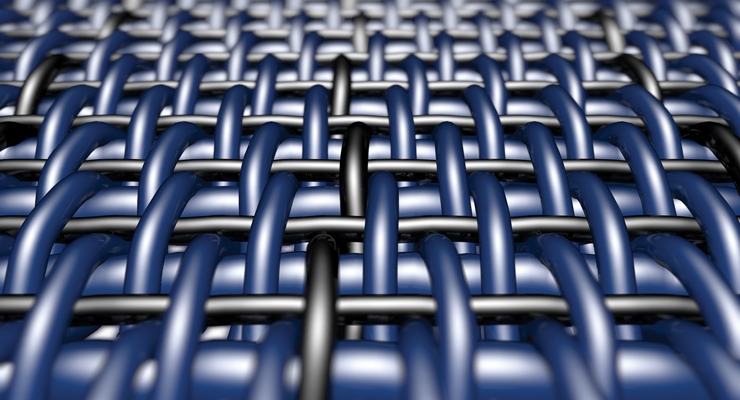