Tara Olivo, Associate Editor08.12.16
Perishables found in the grocery store such as meat, chicken, fish and produce rely on the food pads underneath them to soak up excess liquids and keep the foods fresh, and suppliers in the nonwovens and associated industries have stepped up to the plate by developing solutions in this market.
Nonwovens first made their way into food pads after specialty chemicals company Evonik earned FDA clearance for its food grade superabsorbent polymers (SAP) in the late 1990s, according to industry consultant Phil Mango. “This opened the door for nonwovens in food pads, as nonwovens contain SAP better than the previously used tissue or fluff pulp food pads,” he says.
Mango identifies airlaid as the primary nonwoven used in food pads, but spunbond/SAP/spunbond laminates are also appearing in this market.
“Airlaid is ideal because a food pad has some of the same requirements as a hygiene absorbent core; quick acquisition rates, no/low rewet, absorbency capacity,” he says. “No other nonwoven can combine with SAP as well to provide all of these attributes.”
Fitesa, McAirlaid’s and Glatfelter are among the airlaid manufacturers that currently produce materials for this market.
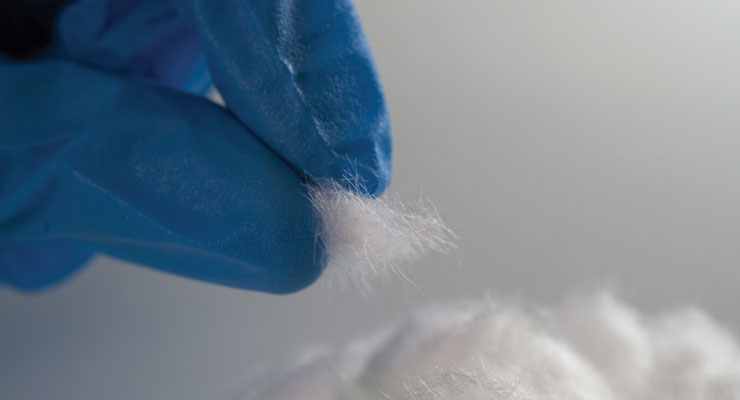
Airlaid continues to expand its role in food packaging applications.
Mango estimates that in Europe, airlaid consumption for food pads has reached 17,000 metric tons and is growing at a CAGR of 5.5%. “Food pads themselves are growing at a smaller rate, but nonwovens penetration is increasing. In Europe, there are many smaller producers—no one or two dominant producers. There is also less centralized meat packaging. This makes it more advantageous to use airlaid; or to switch over.”
Meanwhile in North America, 4500 metric tons of airlaid are consumed annually for food pads and the category is expected to grow at a CAGR of 6%, according to Mango. But in the U.S., two big food pad manufacturers that take up roughly 60-70% market share of the food pad market—Novipax and Paper Pak—aren’t using airlaid. Yet, these companies still look to nonwovens for their products.
Novipax, headquartered in Oak Brook, IL, manufactures an array of food pads that incorporate nonwovens. According to Frank Vaughn, technical marketing manager, Novipax uses spunbond nonwovens in some of its Dri-Loc, Pad-Loc and Multi-Loc varieties. Available in four options, the Dri-Loc pad is a polyethylene film on a polyethylene film. Dri-Loc Premier Pads feature a highly absorbent nonwoven bottom layer. Meanwhile, the company’s Pad-Loc Pads feature a polyethylene film on a nonwoven layer, while Pad-Loc Fresh pads feature a non-permeable/non-stick polyethylene film, highly absorbent fibrous wood pulp, CO2-generating materials and a hydrophilic nonwoven bottom layer film that attracts moisture to the pad. Novipax’s Multi-Loc pads include highly absorbent nonwoven top and bottom layers.
“In the pad, the nonwoven offers us a breathable pad,” Vaughn says. “It allows the evacuation of air out of the pad a lot quicker. Also the nonwoven allows us to have the ability to wick juices in a single tray.”
Elaborating on the company’s unique products, Scott Maurer, director of marketing & new product development for Novipax, says: “We offer a sealed pouch pad, and the benefits of a sealed pouch pad is that all of our absorbent materials are consistently maintained within the confines of the pad itself. So there’s no risk of adulterating the food products, our pads are used with, so all of our materials remain fully contained within the pad – that’s one of the huge advantages we have in the industry.”
Further, he adds, many companies that use Novipax pads use high-tech packing equipment, some of which forces huge demands via vacuum on the meat or produce. “They use our products because of the seal strength, and for those pads with nonwovens, they really hold up super well out in the marketplace.”
Meanwhile, La Verne, CA-based Paper Pak Industries’ (PPI) base food pad products use a “pre-consumer” recycled tissue, but the company also incorporates coated spunbond polypropylene facing materials into many aspects of its products, along with super absorbents either as needed or requested by its customers, according to Ron Jensen, president and CEO of PPI.
“Using nonwovens allows us to change the rate of sorbency and better tailor that rate to the application,” he says.
Differentiating itself from other food pad makers in the U.S., Jensen says PPI offers the widest product line in the industry, giving it a major competitive advantage. “Our use of proprietary pre-consumer recycled tissue also allows us to make our products with the lowest carbon footprint, as determined by using the ASTM formula,” he says. “Finally, we have a large, growing and patent protected line of ‘active’ absorbents used to either extend shelf life, reduce package odor or improve organoleptics. This line of products is largely unique within the food packaging industry, and it is receiving significant customer acceptance. Our R&D pipeline is quite full and we intend to continue to expand our product line to further develop this ‘active’ technology.”
Super Absorbent Suppliers
Evonik, one of the world’s largest producers of SAP, is currently the only maker of FDA-approved SAP for food grade nonwovens. Its only other competitor in this market, BASF, stopped global production for this type of SAP in 2012, according to industry insiders. Evonik’s superabsorbents can be used in food pads that are placed under poultry, meat, fish, fruits and vegetables.
Creasorb, Evonik’s non-hygiene product line, has been producing FAVOR-PAC superabsorbent polymers for food-grade nonwovens since the late 1990s. Its current grade, FAVOR-PAC 593, is its latest generation product, which has been on the market since 2007. FAVOR-PAC polymers are produced at two facilities in the U.S., in Greensboro, NC, and Garyville, LA.
Producing SAP for the food packaging industry is no easy task. Bobby Mitra, business director for Evonik Creasorb, Nutrition & Care, says to garner FDA approval for such a product, a company must prove that it can control the amount of migratables in the product. The first part of the stringent approval process consists of toxicological studies, which ensure that the formulation contains no “chemicals of concern,” which is essentially a list of undesirable chemicals for food safety. A good practice is to use GRAS (Generally Regarded As Safe) ingredients where possible.
Next, the product has to go through migration studies, which show that nothing harmful is migrating out of the product into the food. Migration studies are required for all FDA approved SAP.
“There are some limitations in terms of what [the FDA] considers to be a sensitive migratable. So we must control the molecular weight of migratables,” Mitra explains. “That’s an important part of the FDA approval and it is put on our Certificate of Analysis.”
Another important part of the FDA approval process is record keeping and formulation control. “Once you have registered a formulation with the FDA, that’s locked in,” he adds.
If the product becomes FDA approved, then the site where it’s produced is subject to auditing. “You have to be readily available for unscheduled audits. Then there are a lot of process controls that we have, to ensure both quality and formulation control,” he says. When Evonik’s FAVOR-PAC SAP became FDA approved, it received the food contact notification number 427.
According to Mitra, FAVOR-PAC provides added benefits when used in food pads compared to other absorbent products. “Whether it is used for hygiene products or food pads—in gram for gram absorbency—SAP is more cost effective than fiber, fluff pulp, tissue or anything else.”
Gelok International, a producer of superabsorbent laminates used in food pads, currently uses granular SAP from Evonik. The SAP is sandwiched in between two cellulose sheets to form the laminate. These roll goods are cut into pads by the food tray producers and used as the absorbent core inside of a top sheet and bottom sheet to lock in the SAP, according to Steve Lazenby, general manager of Gelok.
The Dunbridge, OH-based manufacturer, which also produces laminates for hygiene, wound care and industrial applications, considers food pads a very good market for the company. “We’ve seen some pretty good growth in the food pad market because with our laminate, which is ultrathin, the food manufacturers can pack three times as much pads into a container as they could with a traditional fluff/SAP pad,” Lazenby says. “So literally they’re putting their shipping costs down by two-thirds. That’s something very unique to us. Our niche in the market is that we do ultrathin high absorbency laminates.”
Meanwhile, an alternative to using Evonik’s FAVOR-PAC SAP is Technical Absorbents’ Super Absorbent Fiber (SAF). Technical Absorbents has been producing SAF since 1993, and Dr. Mark Paterson, product development director, says SAF for food packaging has been used since the company’s early days.
According to Paterson, compared to SAP, SAF has a more rapid uptake of water due to its high aspect ratio and the SAF can be fully integrated into the product to prevent gel shedding and loss.
“We make a number of different grades of SAF based on the customer’s and product needs, this includes different fiber lengths and thicknesses. The SAF chosen for a particular application is designed to give appropriate absorbent properties for the given application and to be processable on the different technologies involved to meet the final product needs,” he says.
While he couldn’t go into detail, Paterson says the food packaging market is significant for Technical Absorbents’ SAF, and right now, while the overall market is seeing modest year-on-year growth, he indicates growth opportunities do exist in Asia.
“All our SAF grades are made to the highest quality standards and we exceed the requirements for producing food packaging SAF grades,” he adds. “The on-going challenge is to continue to produce SAF grades at a lower cost and to continue to exceed the ever changing and evolving regulatory requirements across different regions of the world.”
Adhesive’s Role
Milan, Italy-based Savaré Specialty Adhesives, which supplies an assortment of hot-melt adhesives to many markets in the nonwovens industry, has been producing hot melts for the food pad industry for nearly a decade.
“The experience gained over the years across the whole production process of this specialty business has enabled us to achieve a leading position,” says Lorenzo Stella, sales manager, Savaré.
Savaré offers several specialty products both for the pad lamination and for the pad fixation into the trays. For pad lamination, Stella says the company’s adhesives are designed to meet various technical needs including high yield with excellent bonding strength at low add-on rates on different nonwoven types; direct food contact compliance; no bleed-through with aperture nonwovens; excellent aging behavior; clear color and low odor.
Stella notes that for the hot-melt to be successful, it should be designed so that the pad absorption capacity is not altered. Further, strong pad edge bonding is required, even under severe wet conditions.
While Savaré isn’t new to food pads, the company continues to see room for development in this market. Stella says: “The trend of customized pads to satisfy specific consumer needs for fruit, vegetables, meat and fish, as well as moving to recycled tray materials, are triggering new challenges and opportunities.”
Nonwovens first made their way into food pads after specialty chemicals company Evonik earned FDA clearance for its food grade superabsorbent polymers (SAP) in the late 1990s, according to industry consultant Phil Mango. “This opened the door for nonwovens in food pads, as nonwovens contain SAP better than the previously used tissue or fluff pulp food pads,” he says.
Mango identifies airlaid as the primary nonwoven used in food pads, but spunbond/SAP/spunbond laminates are also appearing in this market.
“Airlaid is ideal because a food pad has some of the same requirements as a hygiene absorbent core; quick acquisition rates, no/low rewet, absorbency capacity,” he says. “No other nonwoven can combine with SAP as well to provide all of these attributes.”
Fitesa, McAirlaid’s and Glatfelter are among the airlaid manufacturers that currently produce materials for this market.
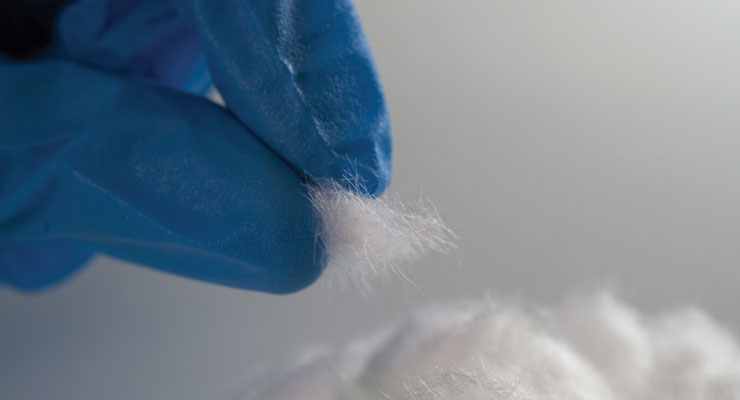
Airlaid continues to expand its role in food packaging applications.
Meanwhile in North America, 4500 metric tons of airlaid are consumed annually for food pads and the category is expected to grow at a CAGR of 6%, according to Mango. But in the U.S., two big food pad manufacturers that take up roughly 60-70% market share of the food pad market—Novipax and Paper Pak—aren’t using airlaid. Yet, these companies still look to nonwovens for their products.
Novipax, headquartered in Oak Brook, IL, manufactures an array of food pads that incorporate nonwovens. According to Frank Vaughn, technical marketing manager, Novipax uses spunbond nonwovens in some of its Dri-Loc, Pad-Loc and Multi-Loc varieties. Available in four options, the Dri-Loc pad is a polyethylene film on a polyethylene film. Dri-Loc Premier Pads feature a highly absorbent nonwoven bottom layer. Meanwhile, the company’s Pad-Loc Pads feature a polyethylene film on a nonwoven layer, while Pad-Loc Fresh pads feature a non-permeable/non-stick polyethylene film, highly absorbent fibrous wood pulp, CO2-generating materials and a hydrophilic nonwoven bottom layer film that attracts moisture to the pad. Novipax’s Multi-Loc pads include highly absorbent nonwoven top and bottom layers.
“In the pad, the nonwoven offers us a breathable pad,” Vaughn says. “It allows the evacuation of air out of the pad a lot quicker. Also the nonwoven allows us to have the ability to wick juices in a single tray.”
Elaborating on the company’s unique products, Scott Maurer, director of marketing & new product development for Novipax, says: “We offer a sealed pouch pad, and the benefits of a sealed pouch pad is that all of our absorbent materials are consistently maintained within the confines of the pad itself. So there’s no risk of adulterating the food products, our pads are used with, so all of our materials remain fully contained within the pad – that’s one of the huge advantages we have in the industry.”
Further, he adds, many companies that use Novipax pads use high-tech packing equipment, some of which forces huge demands via vacuum on the meat or produce. “They use our products because of the seal strength, and for those pads with nonwovens, they really hold up super well out in the marketplace.”
Meanwhile, La Verne, CA-based Paper Pak Industries’ (PPI) base food pad products use a “pre-consumer” recycled tissue, but the company also incorporates coated spunbond polypropylene facing materials into many aspects of its products, along with super absorbents either as needed or requested by its customers, according to Ron Jensen, president and CEO of PPI.
“Using nonwovens allows us to change the rate of sorbency and better tailor that rate to the application,” he says.
Differentiating itself from other food pad makers in the U.S., Jensen says PPI offers the widest product line in the industry, giving it a major competitive advantage. “Our use of proprietary pre-consumer recycled tissue also allows us to make our products with the lowest carbon footprint, as determined by using the ASTM formula,” he says. “Finally, we have a large, growing and patent protected line of ‘active’ absorbents used to either extend shelf life, reduce package odor or improve organoleptics. This line of products is largely unique within the food packaging industry, and it is receiving significant customer acceptance. Our R&D pipeline is quite full and we intend to continue to expand our product line to further develop this ‘active’ technology.”
Super Absorbent Suppliers
Evonik, one of the world’s largest producers of SAP, is currently the only maker of FDA-approved SAP for food grade nonwovens. Its only other competitor in this market, BASF, stopped global production for this type of SAP in 2012, according to industry insiders. Evonik’s superabsorbents can be used in food pads that are placed under poultry, meat, fish, fruits and vegetables.
Creasorb, Evonik’s non-hygiene product line, has been producing FAVOR-PAC superabsorbent polymers for food-grade nonwovens since the late 1990s. Its current grade, FAVOR-PAC 593, is its latest generation product, which has been on the market since 2007. FAVOR-PAC polymers are produced at two facilities in the U.S., in Greensboro, NC, and Garyville, LA.
Producing SAP for the food packaging industry is no easy task. Bobby Mitra, business director for Evonik Creasorb, Nutrition & Care, says to garner FDA approval for such a product, a company must prove that it can control the amount of migratables in the product. The first part of the stringent approval process consists of toxicological studies, which ensure that the formulation contains no “chemicals of concern,” which is essentially a list of undesirable chemicals for food safety. A good practice is to use GRAS (Generally Regarded As Safe) ingredients where possible.
Next, the product has to go through migration studies, which show that nothing harmful is migrating out of the product into the food. Migration studies are required for all FDA approved SAP.
“There are some limitations in terms of what [the FDA] considers to be a sensitive migratable. So we must control the molecular weight of migratables,” Mitra explains. “That’s an important part of the FDA approval and it is put on our Certificate of Analysis.”
Another important part of the FDA approval process is record keeping and formulation control. “Once you have registered a formulation with the FDA, that’s locked in,” he adds.
If the product becomes FDA approved, then the site where it’s produced is subject to auditing. “You have to be readily available for unscheduled audits. Then there are a lot of process controls that we have, to ensure both quality and formulation control,” he says. When Evonik’s FAVOR-PAC SAP became FDA approved, it received the food contact notification number 427.
According to Mitra, FAVOR-PAC provides added benefits when used in food pads compared to other absorbent products. “Whether it is used for hygiene products or food pads—in gram for gram absorbency—SAP is more cost effective than fiber, fluff pulp, tissue or anything else.”
Gelok International, a producer of superabsorbent laminates used in food pads, currently uses granular SAP from Evonik. The SAP is sandwiched in between two cellulose sheets to form the laminate. These roll goods are cut into pads by the food tray producers and used as the absorbent core inside of a top sheet and bottom sheet to lock in the SAP, according to Steve Lazenby, general manager of Gelok.
The Dunbridge, OH-based manufacturer, which also produces laminates for hygiene, wound care and industrial applications, considers food pads a very good market for the company. “We’ve seen some pretty good growth in the food pad market because with our laminate, which is ultrathin, the food manufacturers can pack three times as much pads into a container as they could with a traditional fluff/SAP pad,” Lazenby says. “So literally they’re putting their shipping costs down by two-thirds. That’s something very unique to us. Our niche in the market is that we do ultrathin high absorbency laminates.”
Meanwhile, an alternative to using Evonik’s FAVOR-PAC SAP is Technical Absorbents’ Super Absorbent Fiber (SAF). Technical Absorbents has been producing SAF since 1993, and Dr. Mark Paterson, product development director, says SAF for food packaging has been used since the company’s early days.
According to Paterson, compared to SAP, SAF has a more rapid uptake of water due to its high aspect ratio and the SAF can be fully integrated into the product to prevent gel shedding and loss.
“We make a number of different grades of SAF based on the customer’s and product needs, this includes different fiber lengths and thicknesses. The SAF chosen for a particular application is designed to give appropriate absorbent properties for the given application and to be processable on the different technologies involved to meet the final product needs,” he says.
While he couldn’t go into detail, Paterson says the food packaging market is significant for Technical Absorbents’ SAF, and right now, while the overall market is seeing modest year-on-year growth, he indicates growth opportunities do exist in Asia.
“All our SAF grades are made to the highest quality standards and we exceed the requirements for producing food packaging SAF grades,” he adds. “The on-going challenge is to continue to produce SAF grades at a lower cost and to continue to exceed the ever changing and evolving regulatory requirements across different regions of the world.”
Adhesive’s Role
Milan, Italy-based Savaré Specialty Adhesives, which supplies an assortment of hot-melt adhesives to many markets in the nonwovens industry, has been producing hot melts for the food pad industry for nearly a decade.
“The experience gained over the years across the whole production process of this specialty business has enabled us to achieve a leading position,” says Lorenzo Stella, sales manager, Savaré.
Savaré offers several specialty products both for the pad lamination and for the pad fixation into the trays. For pad lamination, Stella says the company’s adhesives are designed to meet various technical needs including high yield with excellent bonding strength at low add-on rates on different nonwoven types; direct food contact compliance; no bleed-through with aperture nonwovens; excellent aging behavior; clear color and low odor.
Stella notes that for the hot-melt to be successful, it should be designed so that the pad absorption capacity is not altered. Further, strong pad edge bonding is required, even under severe wet conditions.
While Savaré isn’t new to food pads, the company continues to see room for development in this market. Stella says: “The trend of customized pads to satisfy specific consumer needs for fruit, vegetables, meat and fish, as well as moving to recycled tray materials, are triggering new challenges and opportunities.”