Tara Olivo, Associate Editor08.12.16
The global medical nonwoven disposables market is expected to reach $10.05 billion by the year 2020, according to a recent study from Grand View Research.
On the one hand, the increasing prevalence of hospital acquired infections (HAIs) is driving growth in the market, where products such as disposable drapes and gowns are playing an important role in reducing the rate of HAIs. On the other hand, rapidly increasing aging populations throughout the world are giving a boost to the adult incontinence market.

Nonwovens are gaining ground in many medical segments.
While medical products made with nonwovens are more likely to be used in the developed regions of North America and Western Europe, major players in the industry are beginning to see increasing interest in these high-performance materials spreading to all corners of the globe.
“It is forecasted by independent research firms that the demand for medical nonwovens is growing even in developed regions,” says Lynda Kelly, SVP Care Business area, Suominen. “In North America, demand for nonwovens for medical products is projected to grow roughly 5%, while in Europe the estimated annual growth rate is around 3%. These growth forecasts are supported by the current global health and well-being megatrends: an increase in the number of pandemics and hospital-acquired infections, as well as the challenges and changing operating models faced by the healthcare sector.”
However, she adds, emerging markets are currently growing the fastest. In fact, the company recently made an investment at its Paulínia site in Brazil which will allow the company to serve its South American medical customers with new products.
Another emerging region playing an important role is Asia, where medical nonwovens are becoming more prevalent, and which is showing strong economic growth rates that are leading to increasing living standards, according to Dr. Frank Heislitz, CTO, Freudenberg Performance Materials. “This development creates demand for products, which were not consumed in the past.”
Berry Plastics is also seeing more interest for nonwovens in these geographies. “In developing markets, such as China and Brazil, where the adoption of single-use nonwovens products are just gaining momentum, the growth rates are much larger but off of a smaller base,” says David Parks, SVP - Marketing, Strategy & Business Development for the Health, Hygiene and Specialties division of Berry Plastics.
Berry Integrates Avintiv
Berry Plastics’ $2.45 billion purchase of Avintiv last year has brought new and complementary assets to Berry’s already established range of solutions in the healthcare market. Together, the companies supply a full range of medical barrier fabrics utilizing a combination of all core nonwoven technologies as well as film laminate components. End use applications include surgical drapes and gowns, facemasks, scrubs, headwear and footwear, isolation gowns, and CSR wrap, according to Parks.
“The heritage Avintiv nonwoven materials used in medical products are complementary to Berry film products serving the healthcare market,” Parks says. “The two portfolios are being combined in order to offer customers a more complete solution for their infection prevention needs. The combined portfolio not only provides fabrics used in medical products but also the packaging materials used to protect them and maintain sterility where applicable.”
As Berry continues to integrate Avintiv’s assets into its existing portfolio, it’s also
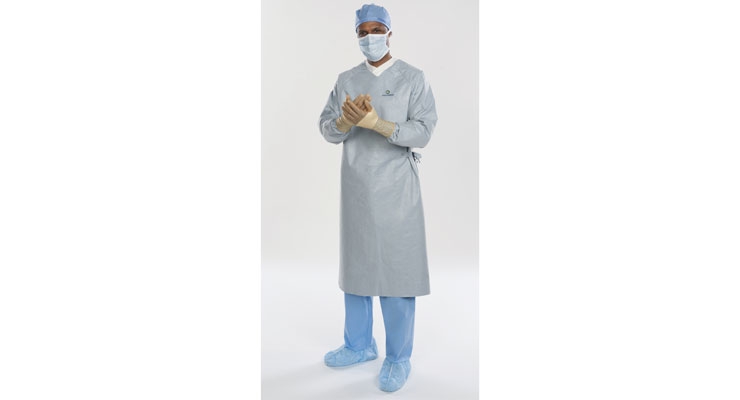
Advances in spunmelt technology a making them ideal for medical apparel.
planning to expand in North America to meet forecasted growth in the market. In May, Berry announced plans for an investment that will add an incremental 16,000 metric tons of capacity serving the region. Parks says the investment, in a yet-to-be-determined location, “will be focused on premium applications in desired hygiene and healthcare markets.”
The asset is expected to be up and running in 2018.
Meanwhile, a recent €25 million ($28 million) investment in Europe, at the company’s Tarragona, Spain, and Terno, Italy, facilities, primarily target hygiene, though some capabilities benefit applications in the healthcare market, according to Parks.
Attention on Advanced Wound Care
While surgical drapes and gowns made from spunmelt make up a majority of products in the medical nonwovens sector, Freudenberg Performance Materials has focused on producing drylaid nonwovens for its medical products which include advanced wound care, traditional wound care, stoma care and transdermal solutions.
Most recently, the company has put forth major efforts in the advanced wound care segment.—its 2015 acquisition of polyurethane foam manufacturer Polymer Health Technologies of the U.K. allowed it to expand its expertise in this piece of the medical market.
“Now we manufacture both components for nonwoven-foam laminates in-house,” says Dr. Heislitz. “By investing in cleanroom lamination capabilities in the U.K., we have strengthened the synergies of these two technologies, nonwovens and foam.”
These offerings provide excellent absorption and retention characteristics for modern wound dressings that are used to treat complex, hard-to-heal wounds such as pressure sores and diabetic foot or leg. “The systems absorb wound exudate and create an ideal environment for the healing of chronic wounds. They thus contribute to the quality of life of patients and support the healing process. Both treatment time and costs can be significantly reduced,” he adds.
One of Freudenberg’s most recent innovations for hydrophilic polyurethane foams include customized, antimicrobial polyurethane foam systems for medium to strong extruded wounds such as decubitus and second degree burns. “The antimicrobial effect contributes to reducing the bacterial load in infected wounds. It also acts as a barrier in wounds with high and renewed risk of infection,” Heislitz says.
The rising trend of antimicrobials has influenced Freudenberg’s decision to invest in a corresponding finishing process. In early 2017, the company will be producing advanced, flexible fabrics for Class III medical devices, and will have an ISO 13485 quality management system in place, which is tailored to the industry’s quality expectations and regulatory requirements.
Mogul Makes Investments
Turkish producer Mogul manufactures a vast range of nonwovens for the medical market including polypropylene (PP) spunbond for basic masks, caps and shoe covers; polyester (PET) spunbond for blood filtration, meltblown and SMS for face masks and patient gowns, spunlace for gauzes, and new cross lap technology that targets tapes and bandages.
In April, Mogul launched a new product line comprising polyester based thermoplastic polyurethane (TPU) fabrics under the Elastex brand of nonwovens, which will serve the medical market as well as applications for other nonwovens markets such as hygiene, food packaging, automotives and others.
A highly elastic product for use where good stretching capabilities are needed, Mogul ElastexTPU products are designed to provide maximum elongation and maximum elastic recovery. Besides its elastic characteristics, ElastexTPU has high air permeability and is resilient to abrasion, puncture, aging and ultraviolet light. Available in weights ranging from 40-400 gsm, ElastexTPU nonwovens are made without solvents and are thereby kind to the skin when used in clothing, as protective covering for mattresses and other healthcare applications, according to the company.
In addition to enhancing its product range, Mogul has also expanded its international footprint. A year ago the company announced plans to establish its first foreign operation in South Carolina. According to Serkan Gogus, Mogul’s CEO, a new spunlace line installed at the site will start in the last quarter of this year, producing 14,000 metric tons of capacity.
“After 18 years in nonwovens and being among the top 40 companies, we believed it is time to move overseas in order to grow as a global player,” Gogus says. “The decision to invest in the U.S. had various reasons. Since the beginning, the U.S. has always been among our major export markets and we have developed a good customer base and reputation in the marketplace. If you look at the global economy, you see uncertainty and problems in most parts of the world while the U.S. is the only economy that is sound and growing.
“Other advantages to investing in South Carolina were available that attracted our attention. We also see South Carolina as an export base to South America and APAC region,” he adds.
The Andritz Nonwoven-supplied neXline spunlace line in Gray Court, SC, with in-line carding configuration, will produce lightweight fabrics at very high speeds for applications in the medical and wipes sectors.
Mogul also recently announced the addition of a new facility in Luleburgaz, Turkey, located outside of Istanbul. The company already operates two plants in Gaziantep, Turkey, which is a considerable distance away from Luleburgaz.
An Andritz neXline spunlace line will be installed at the Luleburgaz plant, and it is designed with a crosslapped configuration in order to cater to a great variety of end uses such as applications for the automotive sector, artificial leather, dry wipes or roofing substrates. The crosslap line will also target medical applications such as tapes, bandages and gauzes, Gogus says. Mogul also invested in an Andritz spunjet line for Luleburgaz to produce technical nonwovens from splittable bi-component filaments, but will also target some niche applications for medical.
“Istanbul is the heart of industry and trade in Turkey, and we wanted to be close to customers. That’s why we chose Luleburgaz,” he says.
The crosslap line is expected to start-up in the third quarter of this year, and the hybrid line is expected to begin production in the fourth quarter.
Suominen Focused on Growth
Finnish nonwovens supplier Suominen has continued to outline details of its three-year investment program that kicked off in 2015, and which focuses on profitable growth and creating a more balanced product portfolio so that its share of products with a higher added value will increase.
Initial steps in the program were investments made to existing lines in Alicante, Spain, and Paulínia, Brazil, where Suominen has expanded offerings in medical products, as well as nonwovens with higher added value, according to Kelly.
Meanwhile, a move that is reported as the largest portion of Suominen’s overall growth strategy is the $60 million investment in a new Andritz-supplied wetlaid line in Bethune, SC, that is currently being installed and will target a number of nonwoven applications including medical. When installed, the production line will utilize the latest wetlaid web forming and hydroentanglement technologies, while the company will also expand on its selection of finishing treatments and chemical substances such as color.
“At Bethune, the investment in a new production line will take the wetlaid technology to a totally new level in our industry,” says Kelly. “The new production line will supply nonwovens for several applications, including household and workplace wiping, medical products, flushable wipes and personal care applications. It is not by chance that Suominen is investing in these carefully selected market segments: They are growing markets and we know what are the needs in these applications.”
Kelly says this new line will offer a range of basis weights and will be able to produce nonwovens made of “100% cellulosic fibers to reinforced composite products and 100% synthetic fiber products with a wide array of features.”
Along with this investment, a recent flurry of product introductions has been central in implementing the company’s growth strategy. Last November, Suominen launched three new products targeting medical and healthcare: Fibrella Zorb, Fibrella Zorb+ and Fibrella Perf.
Fibrella Zorb and Fibrella Zorb+ nonwovens are designed for use in the operating rooms (OR) in hospitals for critical surgical applications. Used as specially tailored additions to standard draping techniques to isolate the patient and OR staff, Fibrella Zorb and Fibrella Zorb+ bring added value benefits to the critical care environment. Fibrella Zorb is an absorbent lightweight top layer with a new texture utilizing Suominen’s unique patterning, while Fibrella Zorb+ is a highly absorbent structure designed for use around the incision site for fenestrations in surgical drapes.
“Fibrella Zorb is a good example of nonwoven specifically developed for fluid management in critical zones of surgical drapes,” says Marika Mäkilä, product manager for medical end-applications, Suominen. “It offers a highly cost-effective element of a single-use drape with optimal safety and infection control.”
Fibrella Perf, which was previously only available in South America, is a range of nonwovens for wound care and gentle cleansing. The nonwoven material has an apertured structure, which makes it very soft and skin friendly. Fibrella Perf for medical applications is now manufactured at all of Suominen’s manufacturing sites around the world.
New Surgical Gown
Halyard Health, the former Kimberly-Clark Healthcare which spun-off of K-C in 2014, produces a range of medical products made using nonwoven materials including surgical gowns, surgical drapes, sterile wrap, surgical masks and apparel.
In medical and surgical settings, Halyard’s Mike Tuck, vice president, Global Product Supply, says nonwovens provide protection from liquids while remaining breathable. “These fabrics are ideal for use in hospitals because they provide a higher level of protection and enhanced sterility over cotton, linen, and paper-based products.”
Most recently the company introduced the Aero Chrome Performance Surgical Gown. The nonwoven gown uses Halyard’s proprietary Cool Shield Core technology fabric that Tuck says is “light, protective and also tear resistant, providing a full range of motion without ripping or tearing to ensure clinicians have the necessary level of perioperative protection for the toughest procedures.”
He claims that the new surgical gown is more breathable than leading competitive surgical gowns in the AAMI 4 level category. “Its unique breathable back panel maximizes airflow through the surgical gown. The unique Aero Chrome fabric allows moisture vapor to escape while providing a high performance barrier. Aero Chrome surgical gowns provide the highest protection in surgical gowns while being the lightest in its category.”
On the one hand, the increasing prevalence of hospital acquired infections (HAIs) is driving growth in the market, where products such as disposable drapes and gowns are playing an important role in reducing the rate of HAIs. On the other hand, rapidly increasing aging populations throughout the world are giving a boost to the adult incontinence market.

Nonwovens are gaining ground in many medical segments.
“It is forecasted by independent research firms that the demand for medical nonwovens is growing even in developed regions,” says Lynda Kelly, SVP Care Business area, Suominen. “In North America, demand for nonwovens for medical products is projected to grow roughly 5%, while in Europe the estimated annual growth rate is around 3%. These growth forecasts are supported by the current global health and well-being megatrends: an increase in the number of pandemics and hospital-acquired infections, as well as the challenges and changing operating models faced by the healthcare sector.”
However, she adds, emerging markets are currently growing the fastest. In fact, the company recently made an investment at its Paulínia site in Brazil which will allow the company to serve its South American medical customers with new products.
Another emerging region playing an important role is Asia, where medical nonwovens are becoming more prevalent, and which is showing strong economic growth rates that are leading to increasing living standards, according to Dr. Frank Heislitz, CTO, Freudenberg Performance Materials. “This development creates demand for products, which were not consumed in the past.”
Berry Plastics is also seeing more interest for nonwovens in these geographies. “In developing markets, such as China and Brazil, where the adoption of single-use nonwovens products are just gaining momentum, the growth rates are much larger but off of a smaller base,” says David Parks, SVP - Marketing, Strategy & Business Development for the Health, Hygiene and Specialties division of Berry Plastics.
Berry Integrates Avintiv
Berry Plastics’ $2.45 billion purchase of Avintiv last year has brought new and complementary assets to Berry’s already established range of solutions in the healthcare market. Together, the companies supply a full range of medical barrier fabrics utilizing a combination of all core nonwoven technologies as well as film laminate components. End use applications include surgical drapes and gowns, facemasks, scrubs, headwear and footwear, isolation gowns, and CSR wrap, according to Parks.
“The heritage Avintiv nonwoven materials used in medical products are complementary to Berry film products serving the healthcare market,” Parks says. “The two portfolios are being combined in order to offer customers a more complete solution for their infection prevention needs. The combined portfolio not only provides fabrics used in medical products but also the packaging materials used to protect them and maintain sterility where applicable.”
As Berry continues to integrate Avintiv’s assets into its existing portfolio, it’s also
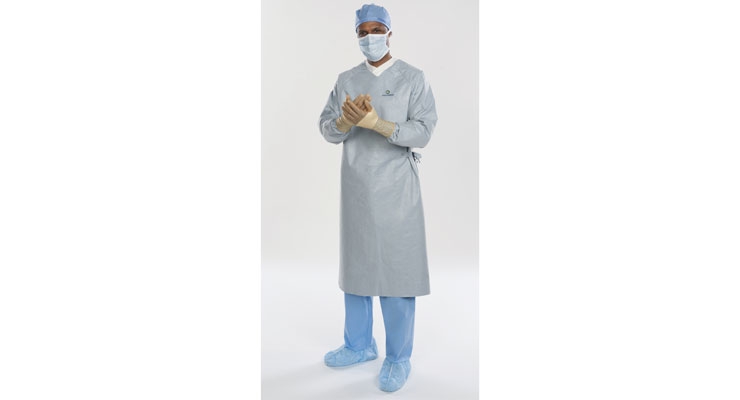
Advances in spunmelt technology a making them ideal for medical apparel.
The asset is expected to be up and running in 2018.
Meanwhile, a recent €25 million ($28 million) investment in Europe, at the company’s Tarragona, Spain, and Terno, Italy, facilities, primarily target hygiene, though some capabilities benefit applications in the healthcare market, according to Parks.
Attention on Advanced Wound Care
While surgical drapes and gowns made from spunmelt make up a majority of products in the medical nonwovens sector, Freudenberg Performance Materials has focused on producing drylaid nonwovens for its medical products which include advanced wound care, traditional wound care, stoma care and transdermal solutions.
Most recently, the company has put forth major efforts in the advanced wound care segment.—its 2015 acquisition of polyurethane foam manufacturer Polymer Health Technologies of the U.K. allowed it to expand its expertise in this piece of the medical market.
“Now we manufacture both components for nonwoven-foam laminates in-house,” says Dr. Heislitz. “By investing in cleanroom lamination capabilities in the U.K., we have strengthened the synergies of these two technologies, nonwovens and foam.”
These offerings provide excellent absorption and retention characteristics for modern wound dressings that are used to treat complex, hard-to-heal wounds such as pressure sores and diabetic foot or leg. “The systems absorb wound exudate and create an ideal environment for the healing of chronic wounds. They thus contribute to the quality of life of patients and support the healing process. Both treatment time and costs can be significantly reduced,” he adds.
One of Freudenberg’s most recent innovations for hydrophilic polyurethane foams include customized, antimicrobial polyurethane foam systems for medium to strong extruded wounds such as decubitus and second degree burns. “The antimicrobial effect contributes to reducing the bacterial load in infected wounds. It also acts as a barrier in wounds with high and renewed risk of infection,” Heislitz says.
The rising trend of antimicrobials has influenced Freudenberg’s decision to invest in a corresponding finishing process. In early 2017, the company will be producing advanced, flexible fabrics for Class III medical devices, and will have an ISO 13485 quality management system in place, which is tailored to the industry’s quality expectations and regulatory requirements.
Mogul Makes Investments
Turkish producer Mogul manufactures a vast range of nonwovens for the medical market including polypropylene (PP) spunbond for basic masks, caps and shoe covers; polyester (PET) spunbond for blood filtration, meltblown and SMS for face masks and patient gowns, spunlace for gauzes, and new cross lap technology that targets tapes and bandages.
In April, Mogul launched a new product line comprising polyester based thermoplastic polyurethane (TPU) fabrics under the Elastex brand of nonwovens, which will serve the medical market as well as applications for other nonwovens markets such as hygiene, food packaging, automotives and others.
A highly elastic product for use where good stretching capabilities are needed, Mogul ElastexTPU products are designed to provide maximum elongation and maximum elastic recovery. Besides its elastic characteristics, ElastexTPU has high air permeability and is resilient to abrasion, puncture, aging and ultraviolet light. Available in weights ranging from 40-400 gsm, ElastexTPU nonwovens are made without solvents and are thereby kind to the skin when used in clothing, as protective covering for mattresses and other healthcare applications, according to the company.
In addition to enhancing its product range, Mogul has also expanded its international footprint. A year ago the company announced plans to establish its first foreign operation in South Carolina. According to Serkan Gogus, Mogul’s CEO, a new spunlace line installed at the site will start in the last quarter of this year, producing 14,000 metric tons of capacity.
“After 18 years in nonwovens and being among the top 40 companies, we believed it is time to move overseas in order to grow as a global player,” Gogus says. “The decision to invest in the U.S. had various reasons. Since the beginning, the U.S. has always been among our major export markets and we have developed a good customer base and reputation in the marketplace. If you look at the global economy, you see uncertainty and problems in most parts of the world while the U.S. is the only economy that is sound and growing.
“Other advantages to investing in South Carolina were available that attracted our attention. We also see South Carolina as an export base to South America and APAC region,” he adds.
The Andritz Nonwoven-supplied neXline spunlace line in Gray Court, SC, with in-line carding configuration, will produce lightweight fabrics at very high speeds for applications in the medical and wipes sectors.
Mogul also recently announced the addition of a new facility in Luleburgaz, Turkey, located outside of Istanbul. The company already operates two plants in Gaziantep, Turkey, which is a considerable distance away from Luleburgaz.
An Andritz neXline spunlace line will be installed at the Luleburgaz plant, and it is designed with a crosslapped configuration in order to cater to a great variety of end uses such as applications for the automotive sector, artificial leather, dry wipes or roofing substrates. The crosslap line will also target medical applications such as tapes, bandages and gauzes, Gogus says. Mogul also invested in an Andritz spunjet line for Luleburgaz to produce technical nonwovens from splittable bi-component filaments, but will also target some niche applications for medical.
“Istanbul is the heart of industry and trade in Turkey, and we wanted to be close to customers. That’s why we chose Luleburgaz,” he says.
The crosslap line is expected to start-up in the third quarter of this year, and the hybrid line is expected to begin production in the fourth quarter.
Suominen Focused on Growth
Finnish nonwovens supplier Suominen has continued to outline details of its three-year investment program that kicked off in 2015, and which focuses on profitable growth and creating a more balanced product portfolio so that its share of products with a higher added value will increase.
Initial steps in the program were investments made to existing lines in Alicante, Spain, and Paulínia, Brazil, where Suominen has expanded offerings in medical products, as well as nonwovens with higher added value, according to Kelly.
Meanwhile, a move that is reported as the largest portion of Suominen’s overall growth strategy is the $60 million investment in a new Andritz-supplied wetlaid line in Bethune, SC, that is currently being installed and will target a number of nonwoven applications including medical. When installed, the production line will utilize the latest wetlaid web forming and hydroentanglement technologies, while the company will also expand on its selection of finishing treatments and chemical substances such as color.
“At Bethune, the investment in a new production line will take the wetlaid technology to a totally new level in our industry,” says Kelly. “The new production line will supply nonwovens for several applications, including household and workplace wiping, medical products, flushable wipes and personal care applications. It is not by chance that Suominen is investing in these carefully selected market segments: They are growing markets and we know what are the needs in these applications.”
Kelly says this new line will offer a range of basis weights and will be able to produce nonwovens made of “100% cellulosic fibers to reinforced composite products and 100% synthetic fiber products with a wide array of features.”
Along with this investment, a recent flurry of product introductions has been central in implementing the company’s growth strategy. Last November, Suominen launched three new products targeting medical and healthcare: Fibrella Zorb, Fibrella Zorb+ and Fibrella Perf.
Fibrella Zorb and Fibrella Zorb+ nonwovens are designed for use in the operating rooms (OR) in hospitals for critical surgical applications. Used as specially tailored additions to standard draping techniques to isolate the patient and OR staff, Fibrella Zorb and Fibrella Zorb+ bring added value benefits to the critical care environment. Fibrella Zorb is an absorbent lightweight top layer with a new texture utilizing Suominen’s unique patterning, while Fibrella Zorb+ is a highly absorbent structure designed for use around the incision site for fenestrations in surgical drapes.
“Fibrella Zorb is a good example of nonwoven specifically developed for fluid management in critical zones of surgical drapes,” says Marika Mäkilä, product manager for medical end-applications, Suominen. “It offers a highly cost-effective element of a single-use drape with optimal safety and infection control.”
Fibrella Perf, which was previously only available in South America, is a range of nonwovens for wound care and gentle cleansing. The nonwoven material has an apertured structure, which makes it very soft and skin friendly. Fibrella Perf for medical applications is now manufactured at all of Suominen’s manufacturing sites around the world.
New Surgical Gown
Halyard Health, the former Kimberly-Clark Healthcare which spun-off of K-C in 2014, produces a range of medical products made using nonwoven materials including surgical gowns, surgical drapes, sterile wrap, surgical masks and apparel.
In medical and surgical settings, Halyard’s Mike Tuck, vice president, Global Product Supply, says nonwovens provide protection from liquids while remaining breathable. “These fabrics are ideal for use in hospitals because they provide a higher level of protection and enhanced sterility over cotton, linen, and paper-based products.”
Most recently the company introduced the Aero Chrome Performance Surgical Gown. The nonwoven gown uses Halyard’s proprietary Cool Shield Core technology fabric that Tuck says is “light, protective and also tear resistant, providing a full range of motion without ripping or tearing to ensure clinicians have the necessary level of perioperative protection for the toughest procedures.”
He claims that the new surgical gown is more breathable than leading competitive surgical gowns in the AAMI 4 level category. “Its unique breathable back panel maximizes airflow through the surgical gown. The unique Aero Chrome fabric allows moisture vapor to escape while providing a high performance barrier. Aero Chrome surgical gowns provide the highest protection in surgical gowns while being the lightest in its category.”