Tara Olivo, associate editor06.08.15
Fiber options abound for manufacturers in the nonwovens industry. From cotton and cellulose to polyester and polypropylene, suppliers have an array of both natural and synthetic fibers to choose from. And, to keep up with demands, fiber producers competing in the nonwovens industry are continuing to hone their technologies, creating premium, tailor-made solutions for their customers.
A frequent category mentioned as an area of growth among fiber companies is hygiene, and that’s not surprising. The rapid growth of the aging population in countries around the globe is sure to support the increasing role—and need—that various fibers play in products such as adult incontinence items. And while synthetic fibers like polypropylene have dominated in diapers, cotton is beginning to make its way into hygiene applications, especially as consumers are eager for products deemed as natural and biodegradable.
Cotton: Nature’s Fiber
Soft, comfortable, natural. These are the three words consumers consistently associate with cotton, according to Jan O’Regan, director of strategic initiatives at Cotton Incorporated. It’s no wonder why companies in nonwovens would consider the fiber, especially for products that come in contact with skin.
With a stable cotton economic situation, supply and demand balance, O’Regan notes there’s been a tremendous amount of interest for cotton in nonwovens recently. “Since 2010, global cotton harvests have been strong and global inventories are plentiful. Right now we have an abundance of cotton worldwide. What this means for the nonwovens markets is stability in the market with affordable prices. As a result, cotton is experiencing high demand for product development and innovation in a variety of markets.”
While she says cotton has always had a place in the medical markets in nonwovens, being part of products such as wound dressings, the fiber most recently has taken over in feminine hygiene, diapers, and adult incontinence products. In fact, CVS launched its own private label feminine hygiene products last year called Pure Cotton.
O’Regan says the Pure Cotton fem hy items are made with 100% cotton fiber, and the film and adhesive are the only parts not made with the natural fiber.
“An increasing number of women are seeking more natural and healthier products,” she explains. “Cotton is hypoallergenic and thus, protects skin sensitive areas of the body from irritations that result from wearing plastic films next to the skin.”
Some other new products that contain cotton are Walmart Equate Options and Cottony brands of adult pads and liners, the HDIS Reassure brand 100% cotton adult products, and Target Up & Up diapers and wipes, O’Regan says.
Another example is Seventh Generation, which incorporates cotton in the backsheet of its baby diapers and is intended to be soft to the touch for moms and dads changing their babies.
While cotton offers a number of positives, including softness, sustainability and biodegradability, O’Regan adds, “It is also annually renewable. And, for those who see cotton as a fiber crop only, it is important to recognize that it is also a food crop, too. Furthermore, cotton is not just a single fiber, but a product line that includes mechanically cleaned cotton, which retains cotton’s natural oils and pectins; purified cotton, highly absorbent and hygienic; and linters, shorter fibers that are more compatible with wet laying and air laying.”
The aforementioned Seventh Generation diapers incorporate the mechanically cleaned True Cotton, produced by cotton manufacturer and supplier TJ Beall. The oils and pectins it retains make it “naturally hydrophobic but oleophilic,” O’Regan explains.
The new diapers—called Touch of Cloth—debuted exclusively at Target stores in the U.S. in the fall of 2014 and are now also being sold on Amazon.com.
Lawson Gary, COO at TJ Beall, says the company has been working to clean fibers without scouring or bleaching since his father built one of the first mote re-ginning facilities in the U.S.
“This process takes cotton gin waste and processes it into usable fibers for the traditional textile, technical textile, and currency paper markets,” Gary explains. “We used many of the theories developed in our mote re-ginning process and applied them to finer-cleaning equipment for our proprietary True Cotton manufacturing facility.”
True Cotton, which received an INDEX 14 Award from EDANA, was developed prior to TJ Beall’s partnership with Seventh Generation. “[Seventh Generation] immediately realized that we had developed a fiber with an unparalleled sustainability profile and that this was a perfect fit for their sustainable brand.”
Another player in the cotton market is Barnhardt, which produces a variety of purified cotton products for nonwovens. The company’s latest product is its High Q EcoBlend, which is a hybrid product comprised of long staple cotton fibers that have been recycled, according to Ginny Casstevens, Barnhardt’s director of sales & marketing – Nonwoven Fibers. “Not only does this product offer a stronger environmental profile, it also offers a lower cost solution for most nonwoven applications,” she says.
This year, Barnhardt announced that a majority of its products have earned the USDA Certified Biobased Product Label, which verifies that the amount of renewable biobased ingredients in its products meets or exceed levels set by the USDA. Among the certified products are Barnhardt’s High Q EcoBlend, High Q Ultra, HiLoft, HyDri and NeedleEze High Q.
According to the USDA’s BioPreferred program website, biobased products are “derived from plants and other renewable agricultural, marine, and forestry materials and provide an alternative to conventional petroleum derived products.” The goal of the program is to increase the purchase and use of biobased products.
“Our use of the label allows our products to be immediately identified as products that are helping to fulfill the purpose of the program, which is to reduce petroleum consumption, increase the use of renewable resources, better manage the carbon cycle and possibly contribute to reducing adverse environmental and health impacts,” Casstevens explains. “Additionally, the program is expected to promote economic development, creating new jobs and providing new markets for farm commodities.”
Casstevens agrees that the hygiene market is a growing area for cotton. Within this realm, Barnhardt’s HyDri fiber was designed specifically for applications—like topsheets or leg cuffs—where hydrophobicity is needed. Its HiLoft product also has a place in hygiene, acting as an absorbent, highly resilient purified cotton for use where liquid acquisition and capacities are desired.
“Barnhardt Purified Cotton is the only 100% natural, pure choice for applications that come into direct skin contact with some our most sensitive and intimate body parts such as in feminine hygiene and adult incontinence products as well as in baby diapers,” Casstevens says. “Unlike manufactured chemical-pulps such as rayon/viscose or lyocell/Tencel, cotton is 100% natural.”
It’s Tencel’s Time
Made from wood pulp, cellulosic fibers are another natural option for nonwovens, and Lenzing is the leading manufacturer in this area, producing Tencel and Viscose for nonwoven applications.
“Nonwovens are a key element of Lenzing’s overall strategy,” says Elisabeth Stanger, global director, business development hygiene for Lenzing. “Approximately 30% of our total fiber volume goes into nonwoven products.”
Lenzing has been focused on its lyocell fiber Tencel and will continue to do so in the future, and Stanger describes several benefits
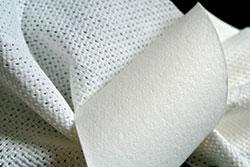
Tencel fibers are common in wipes.
of the fiber for nonwoven applications.
“Tencel has superior wet strength, is free of odor and suited for applications with various kinds of lotions, it is skin friendly and has received several certificates including medical tested. In addition Tencel is the most sustainable manmade cellulose fiber,” she says. “So in short Tencel is good to the skin and good to the planet as well.”
Last year, the company completed work on the largest production facility for lyocell fibers in the world. The factory, located in Lenzing, Austria, is the first in the industry that has one line capable of making 67,000 tons of material.
“Over the past few years Tencel has secured a permanent place on the market for a whole range of attractive applications,” Lenzing management board member and CCO Robert van de Kerkhof said in a statement. “Tencel can exploit its advantages in the apparel, home textile and innovative technical segments. The fiber offers good breathing properties, excellent wearing comfort, high fiber strength and above all an environmentally compatible production on the basis of the natural raw material, wood. For these reasons Tencel is also the premium cellulose fiber of the future.”
Lenzing has spent more than €100 million ($112 million) on research in lyocell technology, and the company says Tencel will remain a top research and development priority. Lenzing is even considering the construction of another Tencel jumbo production plant if demand for Tencel continues to develop as expected.
At the end of last year, Lenzing’s total annual Tencel production capacity amounted to about 220,000 tons manufactured at the Austrian sites in Lenzing and Heiligenkreuz, Austria, in Mobile, AL, and in Grimsby, U.K.
Recently, the company has been exploring the shoe business with Tencel. The fiber is being used for the first time in various shoe components in response to shoe manufacturers who are looking for eco-friendly and sustainable materials.
“The goal is to launch a shoe on the market in which all of the component parts are made with Tencel,” says Marina Crnoja-Cosic, segment manager of technical textiles for Lenzing. “Tencel has a good reputation when it comes to sustainability, and particularly when it comes to shoes, the function of moisture management, which Tencel fulfills to perfection, is a must.”
Austrian shoe brand Legero joined Lenzing at a press conference during the Techtextil 2015 trade fair in May. The shoe company is testing prototypes using Tencel. Also playing a role in the development of the shoes is the test and research institute Primansens, as well as the International Show Competence Center of Primansens in Germany, where all the prototypes were made.
As part of the first prototypes, nonwovens are used in the shoe lining as well as in the padding component of the shoe.
A Selection of Synthetics
Through its various subsidiaries, Indorama Ventures PCL, a world leading producer of intermediate petrochemicals, serves nonwovens markets in hygiene such as baby diapers, feminine care and wet wipes, as well as fibers for industrial applications such as filtration, geotextiles and shale oil and gas extraction. To stay ahead of the curve, the multinational consistently introduces new products. “Our vitality index, which is the ratio of revenue from new products brought to market in the last five years to total revenue...stands at above 25% today,” says Udey Gill, president – Polyester Business, Indorama Ventures PCL.
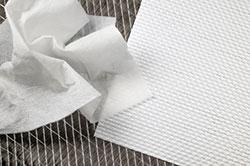
Trevira fibers continue to thrive in nonwovens.
Fast growing segments for polyester in nonwovens, according to Gill, are healthcare and air and water filtration. He says the fiber is also gaining market share in nonwovens versus others fibers “because of its ability to meet customer needs and its competitive cost.”
While there are overcapacity issues, mostly in China, Gill notes that the company’s high value-added businesses are seeing growing demand for in “innovative niche applications” in the hygiene, automotive and industrial areas. “Global demand continues to reach 6-7% per annum,” he adds.
One of Indorama’s subsidiaries is Germany-based Trevira. Within the nonwovens industry, the company is focusing on customized special solutions in polyester and bicomponent fibers. Among the company’s more recent product introductions are fibers made from PLA biopolymer. In 2010, Trevira formed a partnership with NatureWorks to produce Ingeo fibers.
“Fibers made from biopolymers (PLA/Ingeo) for a variety of nonwovens make up an essential element in our product program,” says Hartmann Huth, vice president Business Unit Staple Fibers, Trevira. “Trevira is the most important partner in staple fibers for NatureWorks, our supplier of raw materials. PLA is used for those products where the unique and ecological properties of PLA generate an added value.”
Huth also indicates that the company’s bicomponent fibers are key in the nonwovens business. “Initially used principally in hygiene products, they are appearing more and more in developments for customer projects aimed at technical applications, like filtration or insulation,” he says.
Trevira is also tackling flame retardant fibers for applications in soundproofing, insulation and automotives, as well as short-cut fiber specialties for end uses such as wallpaper and food packaging.
When it comes to the continued demand for polyester fibers, there are two drivers, according to Huth: technical progress and global megatrends such as the demand for sustainability. He says emerging countries are also playing a role due to rising disposable incomes.
In nonwovens, Trevira is seeing increasing potential in disposable hygiene products, technologies in the energy storage sector and filtration. “The new energy storage technologies need new battery separators, and to produce sufficient drinking water for a growing population, you need state-of-the-art filter technologies—these are applications for modern polyester fibers,” Huth says. Trevira is also observing increasing demand for flame retardant materials in emerging markets such as Asia, as well as “boom regions” like the Middle East.
FiberVisions, another Indorama company, develops, manufactures and markets polyolefin fibers for nonwoven, textile and industrial applications, including polypropylene and polyethylene monocomponent fibers and polypropylene or polyester core, polyethylene or polypropylene sheath bicomponent fibers. Its fibers are used in nonwovens made by carding, wetlay and airlaid web formation processes and consolidated by thermal bonding, air through bonding, needlepunching and spunlacing.
Shailesh Agrawal, FiberVisions’ joint vice president sales & marketing - Specialty Fibers, is seeing growth across the board for polyolefin fibers, but especially in hygiene and industrial applications.
In response to rising demand for bicomponent products, the company recently added to its capacity in North America, opening a facility in Covington, GA, at the end of last year. Agrawal says the company also has plans to expand in Asia. “Demand remains strong and supply is growing in line with demand,” Agrawal says. “Margins remain under pressure across the globe and various initiatives are needed to ensure that the business remains profitable.”
Wellman International Limited is another Indorama subsidiary. Earlier this year at Heimtextil 2015 in Frankfurt, Germany, the company launched a new ‘eco-fine’ fiber range, produced from European PCR (post consumer recycled) feedstock. According to Wellman, the launch of ‘eco-fine’ fibers, broadens the company’s fiber decitex range capability from 44 decitex to 1.7 decitex and significantly strengthens the company’s’ position as both the largest polyester staple fiber producer and PET recycler in Europe.
At Heimtextil the company featured eco-fine 1.7 siliconized, a premium, uniquely sustainable product offering the ultimate in luxury with enhanced drapability and a silk-like touch. This fiber range is ideal for select bedding and apparel applications and also complements the Wellman eco-core fiber filling product family, with the potential for coverstock production to offer a ‘complete’ offering to the customer.
DAK Americas, a supplier of polyester staple fibers, offers products for spunlace and needlepunch nonwovens in the hygiene, industrial and automotive sectors, and the company sees growth in all areas.
“In industrial and automotive, we see PSF growth at the expense of other materials due to the unique properties attributes of PSF. In hygiene, we see growth in medical and adult incontinence products,” says Mark Ruday, vice president, DAK Americas Fibers.
Polyester staple fibers in nonwovens are lightweight, soft, offer improved loft, provide bulk for fiberfill applications, they’re recyclable and moldable, hygienic and the general cost/value is a benefit compared to other fibers, according to Ruday.
Currently, DAK is considering more opportunities in addition to those already underway to expand and grow capacity to meet demand in the marketplace. In fact, last year the company announced it was increasing PSF production capacity at its Cooper River site near Charleston, SC. Phase one of the expansion was expected to be completed in mid-May, and will add an additional 12 ktons of capacity, Ruday says. Phase two was expected to commence following the completion of phase one, and DAK will be making announcements about timing and capacity increases soon. “Higher growth rates in certain applications and market demand is driving the need to add capacity,” he says.
Another player in the synthetic arena is Beaulieu Fibres International (BFI), a leading European producer of polypropylene staple fibers. The company offers a range of products for diverse segments in the nonwovens industry, serving customers in hygiene, geotextiles, floorcoverings, automotive, filtration and upholstery. “Our broad portfolio of PP staple fibers includes specialty fibers for automotive composites, Meraklon trilobal fibres for hygiene applications, and high tenacity fibers for geotextiles, to name just a few,” says Donald De Deygere, sales and marketing manager, Beaulieu Fibres International.
De Deygere says hygiene is an area of growth for PP fibers in nonwovens, and at last month’s Techtextil 2015 exhibition in Germany, the company launched Meraklon Ultrasoft Trilobal PP Fibres for the segment. The new fibers, which are available in 1.0 to 6.7 dtex for spunlaced and thermal calendared bonded technologies, are ideal for soft nonwoven fabrics that come in direct contact with skin. Also, because of its larger surface area, the fiber’s liquid retention capacity is increased. Target applications include topsheets and other parts for diapers and feminine napkins.
“With the trilobal fiber innovation, nonwovens’ producers can benefit from system cost reductions while maintaining the coverage and opacity performance required of lightweight fabrics aimed at the hygiene market,” De Deygere explains. “The unique defined cross section of the true trilobal shape achieves resilience which enhances fiber opacity and leads to a superior coverage effect and bulkiness in the finished nonwoven. This allows weight reduction of both the fiber and related nonwoven while overcoming the traditional loss of opacity associated with less material use.”
While De Deygere sees growth in all areas for PP fibers, he also highlights the automotive and geotextile sectors. “Within automotive, we are seeing growth in demand for PP fiber to support the increasing trend towards fiber-based thermoplastic products,” he says. “BFI has developed a range of PP fibers for each specific composite blend, that is for PET, natural, and mineral fiber. Each of these thermoplastic binder fiber families offers dimensional stability and excellent elongation capacity during the molding process.”
In geotextiles, he says the market is experiencing global growth, specifically in Asia’s emerging markets. The company’s HT8 fibers for “lightweight, state-of-the-art geotextiles” have potential to make difference in this market, according to De Deygere. “These are unique in offering high tenacity capabilities without compromising on elongation,” he explains. “The step-change in performance offered by BFI’s 4.4-6.7 dtex fibers reduces overall system cost, by allowing customers to maximize machine output and ensure desired performance with weight savings of 10-15% compared to standard geotextile fibers.” The company also recently added to its range to support heavier geotextiles meant for environmental and protection services, available in 8.9 dtex and 11 dtex.
Meanwhile, Fiberpartner of Vejle, Denmark, supplies a range of staple fibers for the nonwovens industry including solid, hollow and low melt polyester fibers, as well as polypropylene and bi-component fibers for thermo- and air through bonding.
At this year’s Techtextil trade fair the company launched a group of new products. Among them is a partial recycled bico-low melt fiber, which is targeted toward applications where customers are focusing on “greener” technology such as automotives, according to Thomas Wittrup, owner of Fiberpartner.
The company also debuted a new range of Airbonder fibers, which are bi-component fibers tailor-made and developed for the airlaid industry. “In this area bonding properties to pulp is the key factor,” Wittrup says.
A frequent category mentioned as an area of growth among fiber companies is hygiene, and that’s not surprising. The rapid growth of the aging population in countries around the globe is sure to support the increasing role—and need—that various fibers play in products such as adult incontinence items. And while synthetic fibers like polypropylene have dominated in diapers, cotton is beginning to make its way into hygiene applications, especially as consumers are eager for products deemed as natural and biodegradable.
Cotton: Nature’s Fiber
Soft, comfortable, natural. These are the three words consumers consistently associate with cotton, according to Jan O’Regan, director of strategic initiatives at Cotton Incorporated. It’s no wonder why companies in nonwovens would consider the fiber, especially for products that come in contact with skin.
With a stable cotton economic situation, supply and demand balance, O’Regan notes there’s been a tremendous amount of interest for cotton in nonwovens recently. “Since 2010, global cotton harvests have been strong and global inventories are plentiful. Right now we have an abundance of cotton worldwide. What this means for the nonwovens markets is stability in the market with affordable prices. As a result, cotton is experiencing high demand for product development and innovation in a variety of markets.”
While she says cotton has always had a place in the medical markets in nonwovens, being part of products such as wound dressings, the fiber most recently has taken over in feminine hygiene, diapers, and adult incontinence products. In fact, CVS launched its own private label feminine hygiene products last year called Pure Cotton.
O’Regan says the Pure Cotton fem hy items are made with 100% cotton fiber, and the film and adhesive are the only parts not made with the natural fiber.
“An increasing number of women are seeking more natural and healthier products,” she explains. “Cotton is hypoallergenic and thus, protects skin sensitive areas of the body from irritations that result from wearing plastic films next to the skin.”
Some other new products that contain cotton are Walmart Equate Options and Cottony brands of adult pads and liners, the HDIS Reassure brand 100% cotton adult products, and Target Up & Up diapers and wipes, O’Regan says.
Another example is Seventh Generation, which incorporates cotton in the backsheet of its baby diapers and is intended to be soft to the touch for moms and dads changing their babies.
While cotton offers a number of positives, including softness, sustainability and biodegradability, O’Regan adds, “It is also annually renewable. And, for those who see cotton as a fiber crop only, it is important to recognize that it is also a food crop, too. Furthermore, cotton is not just a single fiber, but a product line that includes mechanically cleaned cotton, which retains cotton’s natural oils and pectins; purified cotton, highly absorbent and hygienic; and linters, shorter fibers that are more compatible with wet laying and air laying.”
The aforementioned Seventh Generation diapers incorporate the mechanically cleaned True Cotton, produced by cotton manufacturer and supplier TJ Beall. The oils and pectins it retains make it “naturally hydrophobic but oleophilic,” O’Regan explains.
The new diapers—called Touch of Cloth—debuted exclusively at Target stores in the U.S. in the fall of 2014 and are now also being sold on Amazon.com.
Lawson Gary, COO at TJ Beall, says the company has been working to clean fibers without scouring or bleaching since his father built one of the first mote re-ginning facilities in the U.S.
“This process takes cotton gin waste and processes it into usable fibers for the traditional textile, technical textile, and currency paper markets,” Gary explains. “We used many of the theories developed in our mote re-ginning process and applied them to finer-cleaning equipment for our proprietary True Cotton manufacturing facility.”
True Cotton, which received an INDEX 14 Award from EDANA, was developed prior to TJ Beall’s partnership with Seventh Generation. “[Seventh Generation] immediately realized that we had developed a fiber with an unparalleled sustainability profile and that this was a perfect fit for their sustainable brand.”
Another player in the cotton market is Barnhardt, which produces a variety of purified cotton products for nonwovens. The company’s latest product is its High Q EcoBlend, which is a hybrid product comprised of long staple cotton fibers that have been recycled, according to Ginny Casstevens, Barnhardt’s director of sales & marketing – Nonwoven Fibers. “Not only does this product offer a stronger environmental profile, it also offers a lower cost solution for most nonwoven applications,” she says.
This year, Barnhardt announced that a majority of its products have earned the USDA Certified Biobased Product Label, which verifies that the amount of renewable biobased ingredients in its products meets or exceed levels set by the USDA. Among the certified products are Barnhardt’s High Q EcoBlend, High Q Ultra, HiLoft, HyDri and NeedleEze High Q.
According to the USDA’s BioPreferred program website, biobased products are “derived from plants and other renewable agricultural, marine, and forestry materials and provide an alternative to conventional petroleum derived products.” The goal of the program is to increase the purchase and use of biobased products.
“Our use of the label allows our products to be immediately identified as products that are helping to fulfill the purpose of the program, which is to reduce petroleum consumption, increase the use of renewable resources, better manage the carbon cycle and possibly contribute to reducing adverse environmental and health impacts,” Casstevens explains. “Additionally, the program is expected to promote economic development, creating new jobs and providing new markets for farm commodities.”
Casstevens agrees that the hygiene market is a growing area for cotton. Within this realm, Barnhardt’s HyDri fiber was designed specifically for applications—like topsheets or leg cuffs—where hydrophobicity is needed. Its HiLoft product also has a place in hygiene, acting as an absorbent, highly resilient purified cotton for use where liquid acquisition and capacities are desired.
“Barnhardt Purified Cotton is the only 100% natural, pure choice for applications that come into direct skin contact with some our most sensitive and intimate body parts such as in feminine hygiene and adult incontinence products as well as in baby diapers,” Casstevens says. “Unlike manufactured chemical-pulps such as rayon/viscose or lyocell/Tencel, cotton is 100% natural.”
It’s Tencel’s Time
Made from wood pulp, cellulosic fibers are another natural option for nonwovens, and Lenzing is the leading manufacturer in this area, producing Tencel and Viscose for nonwoven applications.
“Nonwovens are a key element of Lenzing’s overall strategy,” says Elisabeth Stanger, global director, business development hygiene for Lenzing. “Approximately 30% of our total fiber volume goes into nonwoven products.”
Lenzing has been focused on its lyocell fiber Tencel and will continue to do so in the future, and Stanger describes several benefits
Tencel fibers are common in wipes.
“Tencel has superior wet strength, is free of odor and suited for applications with various kinds of lotions, it is skin friendly and has received several certificates including medical tested. In addition Tencel is the most sustainable manmade cellulose fiber,” she says. “So in short Tencel is good to the skin and good to the planet as well.”
Last year, the company completed work on the largest production facility for lyocell fibers in the world. The factory, located in Lenzing, Austria, is the first in the industry that has one line capable of making 67,000 tons of material.
“Over the past few years Tencel has secured a permanent place on the market for a whole range of attractive applications,” Lenzing management board member and CCO Robert van de Kerkhof said in a statement. “Tencel can exploit its advantages in the apparel, home textile and innovative technical segments. The fiber offers good breathing properties, excellent wearing comfort, high fiber strength and above all an environmentally compatible production on the basis of the natural raw material, wood. For these reasons Tencel is also the premium cellulose fiber of the future.”
Lenzing has spent more than €100 million ($112 million) on research in lyocell technology, and the company says Tencel will remain a top research and development priority. Lenzing is even considering the construction of another Tencel jumbo production plant if demand for Tencel continues to develop as expected.
At the end of last year, Lenzing’s total annual Tencel production capacity amounted to about 220,000 tons manufactured at the Austrian sites in Lenzing and Heiligenkreuz, Austria, in Mobile, AL, and in Grimsby, U.K.
Recently, the company has been exploring the shoe business with Tencel. The fiber is being used for the first time in various shoe components in response to shoe manufacturers who are looking for eco-friendly and sustainable materials.
“The goal is to launch a shoe on the market in which all of the component parts are made with Tencel,” says Marina Crnoja-Cosic, segment manager of technical textiles for Lenzing. “Tencel has a good reputation when it comes to sustainability, and particularly when it comes to shoes, the function of moisture management, which Tencel fulfills to perfection, is a must.”
Austrian shoe brand Legero joined Lenzing at a press conference during the Techtextil 2015 trade fair in May. The shoe company is testing prototypes using Tencel. Also playing a role in the development of the shoes is the test and research institute Primansens, as well as the International Show Competence Center of Primansens in Germany, where all the prototypes were made.
As part of the first prototypes, nonwovens are used in the shoe lining as well as in the padding component of the shoe.
A Selection of Synthetics
Through its various subsidiaries, Indorama Ventures PCL, a world leading producer of intermediate petrochemicals, serves nonwovens markets in hygiene such as baby diapers, feminine care and wet wipes, as well as fibers for industrial applications such as filtration, geotextiles and shale oil and gas extraction. To stay ahead of the curve, the multinational consistently introduces new products. “Our vitality index, which is the ratio of revenue from new products brought to market in the last five years to total revenue...stands at above 25% today,” says Udey Gill, president – Polyester Business, Indorama Ventures PCL.
Trevira fibers continue to thrive in nonwovens.
While there are overcapacity issues, mostly in China, Gill notes that the company’s high value-added businesses are seeing growing demand for in “innovative niche applications” in the hygiene, automotive and industrial areas. “Global demand continues to reach 6-7% per annum,” he adds.
One of Indorama’s subsidiaries is Germany-based Trevira. Within the nonwovens industry, the company is focusing on customized special solutions in polyester and bicomponent fibers. Among the company’s more recent product introductions are fibers made from PLA biopolymer. In 2010, Trevira formed a partnership with NatureWorks to produce Ingeo fibers.
“Fibers made from biopolymers (PLA/Ingeo) for a variety of nonwovens make up an essential element in our product program,” says Hartmann Huth, vice president Business Unit Staple Fibers, Trevira. “Trevira is the most important partner in staple fibers for NatureWorks, our supplier of raw materials. PLA is used for those products where the unique and ecological properties of PLA generate an added value.”
Huth also indicates that the company’s bicomponent fibers are key in the nonwovens business. “Initially used principally in hygiene products, they are appearing more and more in developments for customer projects aimed at technical applications, like filtration or insulation,” he says.
Trevira is also tackling flame retardant fibers for applications in soundproofing, insulation and automotives, as well as short-cut fiber specialties for end uses such as wallpaper and food packaging.
When it comes to the continued demand for polyester fibers, there are two drivers, according to Huth: technical progress and global megatrends such as the demand for sustainability. He says emerging countries are also playing a role due to rising disposable incomes.
In nonwovens, Trevira is seeing increasing potential in disposable hygiene products, technologies in the energy storage sector and filtration. “The new energy storage technologies need new battery separators, and to produce sufficient drinking water for a growing population, you need state-of-the-art filter technologies—these are applications for modern polyester fibers,” Huth says. Trevira is also observing increasing demand for flame retardant materials in emerging markets such as Asia, as well as “boom regions” like the Middle East.
FiberVisions, another Indorama company, develops, manufactures and markets polyolefin fibers for nonwoven, textile and industrial applications, including polypropylene and polyethylene monocomponent fibers and polypropylene or polyester core, polyethylene or polypropylene sheath bicomponent fibers. Its fibers are used in nonwovens made by carding, wetlay and airlaid web formation processes and consolidated by thermal bonding, air through bonding, needlepunching and spunlacing.
Shailesh Agrawal, FiberVisions’ joint vice president sales & marketing - Specialty Fibers, is seeing growth across the board for polyolefin fibers, but especially in hygiene and industrial applications.
In response to rising demand for bicomponent products, the company recently added to its capacity in North America, opening a facility in Covington, GA, at the end of last year. Agrawal says the company also has plans to expand in Asia. “Demand remains strong and supply is growing in line with demand,” Agrawal says. “Margins remain under pressure across the globe and various initiatives are needed to ensure that the business remains profitable.”
Wellman International Limited is another Indorama subsidiary. Earlier this year at Heimtextil 2015 in Frankfurt, Germany, the company launched a new ‘eco-fine’ fiber range, produced from European PCR (post consumer recycled) feedstock. According to Wellman, the launch of ‘eco-fine’ fibers, broadens the company’s fiber decitex range capability from 44 decitex to 1.7 decitex and significantly strengthens the company’s’ position as both the largest polyester staple fiber producer and PET recycler in Europe.
At Heimtextil the company featured eco-fine 1.7 siliconized, a premium, uniquely sustainable product offering the ultimate in luxury with enhanced drapability and a silk-like touch. This fiber range is ideal for select bedding and apparel applications and also complements the Wellman eco-core fiber filling product family, with the potential for coverstock production to offer a ‘complete’ offering to the customer.
DAK Americas, a supplier of polyester staple fibers, offers products for spunlace and needlepunch nonwovens in the hygiene, industrial and automotive sectors, and the company sees growth in all areas.
“In industrial and automotive, we see PSF growth at the expense of other materials due to the unique properties attributes of PSF. In hygiene, we see growth in medical and adult incontinence products,” says Mark Ruday, vice president, DAK Americas Fibers.
Polyester staple fibers in nonwovens are lightweight, soft, offer improved loft, provide bulk for fiberfill applications, they’re recyclable and moldable, hygienic and the general cost/value is a benefit compared to other fibers, according to Ruday.
Currently, DAK is considering more opportunities in addition to those already underway to expand and grow capacity to meet demand in the marketplace. In fact, last year the company announced it was increasing PSF production capacity at its Cooper River site near Charleston, SC. Phase one of the expansion was expected to be completed in mid-May, and will add an additional 12 ktons of capacity, Ruday says. Phase two was expected to commence following the completion of phase one, and DAK will be making announcements about timing and capacity increases soon. “Higher growth rates in certain applications and market demand is driving the need to add capacity,” he says.
Another player in the synthetic arena is Beaulieu Fibres International (BFI), a leading European producer of polypropylene staple fibers. The company offers a range of products for diverse segments in the nonwovens industry, serving customers in hygiene, geotextiles, floorcoverings, automotive, filtration and upholstery. “Our broad portfolio of PP staple fibers includes specialty fibers for automotive composites, Meraklon trilobal fibres for hygiene applications, and high tenacity fibers for geotextiles, to name just a few,” says Donald De Deygere, sales and marketing manager, Beaulieu Fibres International.
De Deygere says hygiene is an area of growth for PP fibers in nonwovens, and at last month’s Techtextil 2015 exhibition in Germany, the company launched Meraklon Ultrasoft Trilobal PP Fibres for the segment. The new fibers, which are available in 1.0 to 6.7 dtex for spunlaced and thermal calendared bonded technologies, are ideal for soft nonwoven fabrics that come in direct contact with skin. Also, because of its larger surface area, the fiber’s liquid retention capacity is increased. Target applications include topsheets and other parts for diapers and feminine napkins.
“With the trilobal fiber innovation, nonwovens’ producers can benefit from system cost reductions while maintaining the coverage and opacity performance required of lightweight fabrics aimed at the hygiene market,” De Deygere explains. “The unique defined cross section of the true trilobal shape achieves resilience which enhances fiber opacity and leads to a superior coverage effect and bulkiness in the finished nonwoven. This allows weight reduction of both the fiber and related nonwoven while overcoming the traditional loss of opacity associated with less material use.”
While De Deygere sees growth in all areas for PP fibers, he also highlights the automotive and geotextile sectors. “Within automotive, we are seeing growth in demand for PP fiber to support the increasing trend towards fiber-based thermoplastic products,” he says. “BFI has developed a range of PP fibers for each specific composite blend, that is for PET, natural, and mineral fiber. Each of these thermoplastic binder fiber families offers dimensional stability and excellent elongation capacity during the molding process.”
In geotextiles, he says the market is experiencing global growth, specifically in Asia’s emerging markets. The company’s HT8 fibers for “lightweight, state-of-the-art geotextiles” have potential to make difference in this market, according to De Deygere. “These are unique in offering high tenacity capabilities without compromising on elongation,” he explains. “The step-change in performance offered by BFI’s 4.4-6.7 dtex fibers reduces overall system cost, by allowing customers to maximize machine output and ensure desired performance with weight savings of 10-15% compared to standard geotextile fibers.” The company also recently added to its range to support heavier geotextiles meant for environmental and protection services, available in 8.9 dtex and 11 dtex.
Meanwhile, Fiberpartner of Vejle, Denmark, supplies a range of staple fibers for the nonwovens industry including solid, hollow and low melt polyester fibers, as well as polypropylene and bi-component fibers for thermo- and air through bonding.
At this year’s Techtextil trade fair the company launched a group of new products. Among them is a partial recycled bico-low melt fiber, which is targeted toward applications where customers are focusing on “greener” technology such as automotives, according to Thomas Wittrup, owner of Fiberpartner.
The company also debuted a new range of Airbonder fibers, which are bi-component fibers tailor-made and developed for the airlaid industry. “In this area bonding properties to pulp is the key factor,” Wittrup says.