Karen McIntyre, Editor04.04.24
Andritz Focuses on Lightweight Products
Andritz has been a leading supplier in the needlepunch industry for over 50 years, and the company continues to innovate and develop new, innovative solutions for customers and market needs. The company offers solutions across various sectors, including automotive, geotextiles, construction, filtration, synthetic leather, wadding/bedding, stitch-bonding and many more.Andritz’s latest development, the neXloom eXcelle Elliptica-Type DF-4 needleloom offers higher quality, lower weight materials without fabric delamination. The high speed line can produce materials as light as 40 gsm at speeds higher than 25 meters per minute for applications like the automotives industry because they offer excellent fiber displacement and visual surface aspects. The looms can offer large widths up to 6.75 meters. Andritz oil-lubrication technology in combination with the renowned Andritz needleloom frame reduces maintenance and extends the service life thanks to a compact, simple, reliable, and proven design.
Additionally, the ProWin system offers advancements in web weight evenness control, combining technologies for optimal fiber weight profiling and enhancing production efficiency. This device is used to optimize CV% processes, provide a faster return on investment, and save significant raw materials, up to 7% fibers a year. Patented ProWin also minimizes the level of instantaneous acceleration which offers as a result that the same battforming Equipment can run faster with less mechanical stress and a more optimized product regularity.
The ProWin system can work with whatever the fibers are addressing the numerous market applications and weights’ range; ProWin can reduce the CV% by three times at least when compared to conventional non ProWin lines, setting the benchmark for web weight regularity on crosslaid applications.
Committed to sustainability, Andritz lines can process 100% recycled fibers, supporting eco-friendly production without compromising quality. These initiatives cater to a wide range of applications, from technical felts to automotive interiors, emphasizing Andritz’s role in promoting environmental stewardship alongside technological innovation. As the nonwovens industry evolves, Andritz’s commitment to quality, innovation and sustainability ensures it remains at the forefront, ready to meet the market's future demands.
Autefa Offers Precision
As a turnkey supplier of nonwoven lines and machines, Autefa Solutions offers needlepunching lines, aerodynamic web forming lines, hydroentanglement lines and thermal bonding lines. The production of papermaking felts requires the highest precision, especially in the needling process over the entire working width. Autefa Solutions achieves this with specially designed rigid steel frames that allow minimal vibration even at working widths of up to 17 meters. The continuous stroke frequency of 1200 rpm results in a surface quality that meets the specified requirements.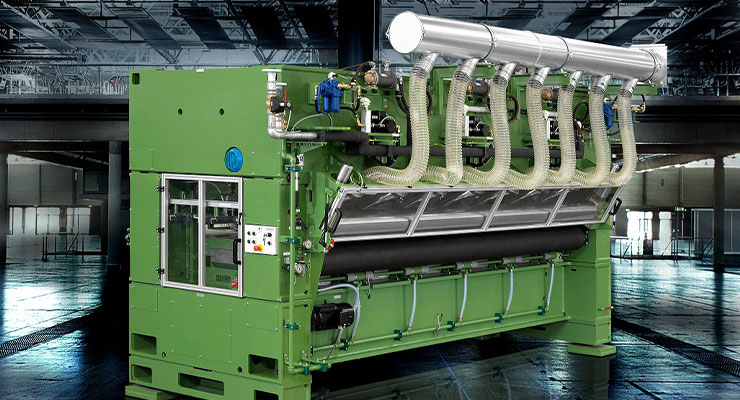
In needlepunching lines for papermakers' felts, Autefa's offers technologies ranging from fiber preparation to finish needlepunching to meet defined requirements in the most effective way. After gentle fiber preparation, the Masterfelt carding machines come into play, guaranteeing the highest fiber blending effects without stressing individual fibers. The downstream combination of the Topliner crosslapper with the patented Closed-Loop System and WebMax web profile control system prevents excessive fabric weight in the edge areas, known as the “smile effect,”and ensures excellent fabric uniformity. Several measuring points are distributed throughout the line for process monitoring.
Autefa’s NL16 Stylus Variliptic pre-needleloom offers an improved fabric surface, higher production speeds, less distortion, less shrinkage, and better uniformity. Finally, the NL19 Finishing needleloom Stylus is used to achieve the desired surface quality. Together they form the core of the high-end production lines, which are individually tailored to customer requirements in terms of working width, number and arrangement of needle zones, needle patterns, stroke frequency, feed tables and fabric tensioning systems. Integrated, fully automatic fabric production according to recipe, with precise stops for bonding and fabric tension control, represents the state of the art.
André Imhof, CEO of Autefa Solutions Austria GmbH, explains: “The double closed-loop system, which offers the best CV-value increases speed and improves productivity. With Service 4.0, we offer comprehensive support through service contracts, 24/7 remote access and technical assistance. We are committed to achieving superior surface quality and offer customized needle board patterns using the i- Point needle simulation tool to improve the capacity and quality of needlepunched fabrics.
“Our recipe sequence control ensures that all machine adjustments are made in the right order and at the right time during product changeovers. This enables our customers to reduce production waste during product changeovers by up to 70%. This not only contributes to sustainability, but also significantly increases profitability. Our customers are so convinced that they have entrusted us in 2023, with the production of a total of two complete papermaking felting lines, including finishing needle machines, for locations in Europe and Asia.”
Dilo Offers Technology for New Applications
“During the past decades, a lot of progress has been possible in the development of needling technology on the basis of staple fibers. Machine builders have been successful with web forming and consolidation to give a considerable increase in product quality, foremost homogeneity, production capacity and efficiency,” says J.P. Dilo, CEO of DiloGroup. “The awareness in the public of the importance of needling according to statistical production data of an abundance of applications was not always present. For years, there was a head-to-head race of nonwovens from staple fiber and endless filaments reflected in the respective production data.”A similar competition took place between hydroentangling (spunlace) and needle technologies, which focused on different applications until recently. This is because needling initially targeted higher weight applications—above 100 gsm—while hydroentangled applications were generally in the lower weight ranges between 30-100 gsm. This allowed hydroentangled materials to grow significantly in hygiene products. However, more recently, developments in intensive needling with the finest needle barbs have allowed the creation of lower weight needled fabrics. This has also allowed needled fabrics to be made more economically than hydroentangled fabrics when comparing the cost per kg of the two lightweight nonwovens types.

According to trials run by Dilo, calculations of production costs show that cost reductions mainly depend on product weight and can to be expected to be in the range of 25-50% when needling instead of hydroentangling is applied, depending on fiber and production parameters. For the production of wipes, on lines ranging from 3.6-3.8 meters, hydroentangling can use more than twice the power of needling, which does not use gas or water. Additionally, needlepunch uses less fiber material because waste is easier to recycle.
High pressure pumps are needed in hydroentangling lines in order to penetrate the fleece and specialty pumps provide high pressure and flow rates. In contrast to a needle made from steel which is useful for several hundred millions of strokes, the water jet loses its complete kinetic energy after it has penetrated the fleece once, leading to increased energy consumption.
To illustrate its recent developments, Dilo has reinstalled its “MicroPunch” demonstration line at its research center in Eberbach, Germany, where it offers tests and product developments for various applications in order to demonstrate the range of qualities and economics. Afterward, the engineering of complete lines is possible depending on the product features.
MicroPunch material remains soft while still offering good abrasion resistance. Other possible application areas include lightweight decorative materials for example as a thin surface material or a mouldable sandwich construction, interlinings and linings in clothing and shoe material.
Apart from the needling process which gives the basic physical strength, stiffness, thickness and wearing resistance, additional finishing technologies may be applied like calendering, through-air or decatizing as well as printing.
Trützschler Group Offer T-Supreme Line
Trützschler Group’s T-Supreme needlepunching line is the result of a joint collaboration with Texnology, which was announced at Techtextil 2022. More recently, Trützschler has established a T-Suprema needlepunching line at its technical center in Egelsbach, Germany.T-Suprema is dedicated to achieving high product quality and system efficiency within the field of premium needlepunched nonwovens – serving as the fundamental component for applications like geotextiles, automotive textiles, filter media, and various industrial uses.
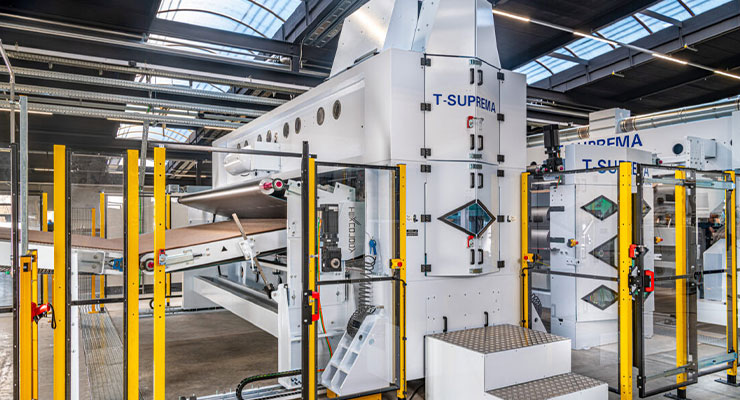
Needlepunch Investment Continues
While investment in needlepunch technology has leveled in recent months, new investments continue to be made, many of which target lighter weight applications, made possible by new research and development efforts. Some of these include:AJ Nonwovens—In 2023, AJ Nonwovens officially inaugurated its new plant in Waco, TX. The event was marked with a ribbon cutting ceremony.
The ultramodern plant is equipped with the latest state-of-the-art needlepunch technologies, which will significantly increase the company's production capacity. The new facility represents a major investment and demonstrates the company's ongoing commitment to growth and expansion.
“With state-of-the-art machinery, climate control, and competitive wages, we hope to be part of the Waco landscape for a long time to come,” says CEO Kevin Frank.
The plant in Waco has been designed for fast collaboration with customers, high quality products, and responsiveness. Waco is a prime location to help the company achieve those goals. AJ Nonwovens president Neil Johnson says: “Our workforce will be highly skilled, able to make decisions on the fly, and supportive. We found those characteristics intrinsic to the Waco community.”
The Waco plant is a model of sustainability and energy efficiency, with environmental initiatives integrated into its design. AstenJohnson is committed to minimizing its impact on the environment while delivering superior quality products, in keeping with its sustainability initiatives.
This opening marks a major milestone in the company's history and paves the way for new opportunities for growth and success. The AJ Nonwovens plant is poised to stimulate the local economy and bring lasting benefits to the Waco community and its residents.
Foss Flooring—Foss produces flooring from recycled plastic for a wide range of applications. Its latest needlepunch investment started up in early 2023.
The new 5.3 meter loom, type SDV, allows Foss Floors to meet the growing customer demand for high-quality products. Every year Foss reuses over 18 million kg (40 million pounds) of plastic to make its floor coverings, which translates into 2 billion plastic bottles recycled into carpet.
This is the second velour loom supplied by Andritz to Foss Floors in four years.
Kevin Nasser, general manager operations at Foss Floors, says: “We bought our first velour loom from Andritz in 2019 and have been very satisfied with the operation and performance of the machine as well as the quality of products. This was, of course, an important consideration in the choice of supplier for our new investment. We relied on Andritz during a supply chain crisis to deliver a necessary machine on time to fulfill the growing demand for our velour product line. The Andritz team fulfilled their promise, and we are more than satisfied with the performance of our new SDV loom!”
Foss Floors is a well-known leader in needlepunched felt products in North America. Its facilities are located in Rome and Chatsworth, GA, and it distributes a vast array of flooring products worldwide. One of the company’s key strengths is its agility for product diversification to satisfy customer needs. Foss Floors also strongly expresses its unwavering commitment to environmentally sustainable manufacturing.
Freudenberg Performance Materials—In 2023, Freudenberg completed work on a new needlepunch line at the Slovenian facility it acquired from Filc in response to increased demand.
The company acquired Filc in early 2020, an action that has not only made the company stronger in needlepunch technology but also broadened its product lineup in roofing and construction and made it more competitive in automotives. At the time of the acquisition, Freudenberg executives said that Filc was especially skilled in needlepunch composites as well as coating abilities.
TWE—In recent months, TWE has worked to modernize its manufacturing sites in Europe, the U.S. and Asia with an aim to enhance efficiency and increase production capacity to effectively meet the growing demand for its products while maintaining a competitive edge.
In the U.S., TWE has added a new needlepunch line to produce high quality products in the field of exterior automotive parts efficiently, and in China, the company has constructed a new line for its highly successful CaliWeb Material, a high-performance nonwoven that replaces foam and provides benefits such as enhanced climatization and low VOCs. This reflects the company’s commitment to providing environmentally-friendly cutting-edge solutions to its customers and expanding its capabilities in the Chinese market.
Yanpai Filtration Technology—Last year, Yanpai Filtration Technology Co., Ltd., China, announced it had ordered batt forming equipment with an aXcess card and crosslapper from Andritz for a needlepunch line producing PTFE filtration products at its site in Tiantai. The PTFE felts will be used as smoke filters in waste incineration plants.
This is now the third order that Andritz has received from Yanpai over the past three years. The first contract—awarded in 2019—was for three complete needlepunch lines (including one PTFE batt forming line), and just recently, Yanpai ordered four new lines containing aXcess and eXcelle equipment.
Vincent Chen, vice president, Yanpai, says: “After years of strong presence in the filtration industry, Yanpai has become the main supplier of filtration and separation materials in China, with the ability to provide customers with high quality, customized, and also complete series of industrial filtration materials for separation tasks. We began our collaboration with Andritz in 2019 and have always been very satisfied with the high quality of machines, process knowledge, and comprehensive technical support from Andritz. This gave us the confidence to award Andritz an order for four new needlepunch lines at the beginning of 2022 and now also the batt forming equipment for the PTFE line.”
Yanpai is a leading Chinese producer of nonwoven filters for dust and air treatment and of woven filter fabrics used in solid/liquid separation applications. Established in 1990, Yanpai was at the forefront of development work on new industrial filtration fabrics. Today, Yanpai has facilities in China and the U.S.