Karen McIntyre, Editor03.01.24
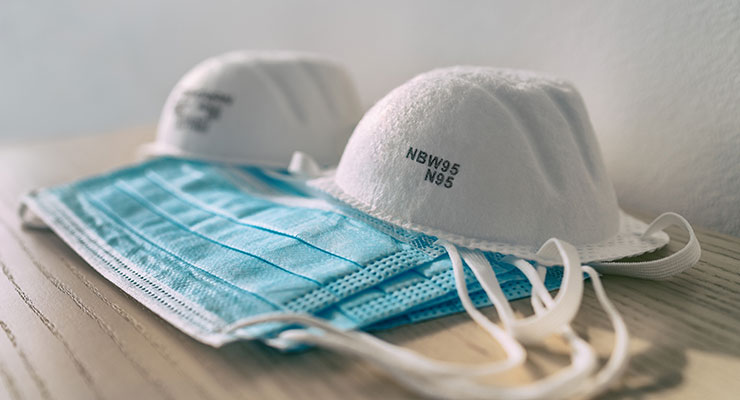
At the peak, face masks represented 33% of meltblown consumption; by 2028, the figure is expected to drop to 8%.
Investment and consumption in meltblown nonwovens saw unprecedented growth in 2020 and 2021 as the world raced to meet demand for materials for face masks and other PPE during the Covid-19 pandemic. As the dust has settled on the Coronavirus, the market for meltblown nonwovens is facing challenges of overcapacity, underutilization and intense competition as producers of the material fight for new application areas.
“Especially during the early stages of the Corona pandemic, a lot of companies around the globe invested in meltblown technology—some of them expanding their existing production capacity, others entering the market for the first time,” says Tobias Wölfel, head of sales, Filtration Products, Sandler. “The decline in demand for meltblown media for face masks did cause some of the companies in the latter category to exit the market. Nevertheless, there are new players on the market. Competition has increased in certain areas. However, this also offers the opportunity for companies such as Sandler to differentiate via a strong and innovative portfolio, as we do also offer pocket, mat, and pleat media made from polyester.”
According to a report published by Smithers last year, volumes within meltblown have decreased by more than 30% compared to the peak of the pandemic from 367,800 tons to 253,500 tons. This decrease came after demand led to a more than doubling of the market.
As consumption has decreased, so has production, particularly in the area related to face masks and investment in new machinery has been at an utter standstill. Now, the industry is facing the challenge of readjusting and identifying new sales channels for output on these lines. This should lead to CAGR in the range of 6.2% leading up to 2028, according to Smithers. The CAGR by volume is lower, but still attractive at 4.9%, pushing consumption worldwide to 332,500 tons in 2028.
Multiple factors will determine the landscape for meltblown nonwoven sales in the short and medium term across 13 end-uses. The main development will be one of correction; following the investments of 2020-21, there is significant overcapacity in global production. While meltblown lines used to make PPE are now being viewed as strategic industrial assets, there is still a need to close older production lines, or reduce prices. Asia will resume its position as the fastest growing region, although North America and Europe will see some benefit from reshoring of meltblown production.
Product mix is also returning a conventional, pre-pandemic situation where filtration, sorbents and insulation are the key areas for meltblown followed by wipes and medical nonwovens. Face masks, which accounted for 33% of all meltblown production by weight in 2020, are forecast to represent just 6% by 2028.
Polypropylene remains the most important material in this segment, 86.2% of demand by weight in 2023. Across the next five years the fastest growth will come for more durable polymers—polycarbonate and polyamide (nylon)—in specialist industrial applications. As in any segment that uses petrochemical inputs, meltblown manufacturing has had to react to economic sanctions and price rises in the wake of Russia’s invasion of Ukraine. In the short-term both disposable and durable meltblown sales are threatened by inflation and a drop in consumer purchasing power. Production costs have also increased, in Europe in particular, as Russian natural gas has been excluded from international energy markets.
Alkegen
LyPore is Alkegen’s new line of meltblown liquid filtration media, which is designed to meet the most critical application requirements, while providing high filtration efficiency, low-pressure drop and excellent dirt holding capacity. Alkegen’s new molecular filtration media, LydAir GP, offer superior performance with expanded capabilities. State-of-the-art manufacturing facilitates exceptional uniformity and layering of a wide range of functional adsorbents including activated carbon and ion exchange resins. Additionally particulate filter media can be laminated in line providing a combination media for both molecular and particle filtration. LydAir GP offers 20%-30% better performance per specific gram of media, which results in higher efficiency and product performance that can be engineered to meet specific application demands.Alkegen was formed in 2022 following the combination of two high performance specialty materials companies, Unifrax and Lydall, one of the world’s largest producers for nonwovens for high performance filtration and acoustical applications, in late 2021.
In the months leading up to the acquisition, Lydall invested approximately $40 million in meltblown nonwoven assets in response to increased demand for face mask material as well as long-term demand for filtration applications. The company added two meltblown lines in Rochester, NH, and one in Saint-Rivalain, France.
While initially targeted toward face masks and other Covid-19 applications, these lines currently support the wider need for improved air quality beyond Covid-19, the company’s innovation team is focused on developing new carbon-based, high-efficiency media for hospitals, airplanes, restaurants, office buildings and other public spaces.
Berry Global
During Covid-19, Berry was at the forefront of meltblown investment. In fact, the nonwovens leader had already made plans to add a new line in Asia prior to Covid, and stepped up these efforts by installing a new line in virtually every major region in the world.As meltblown demand returned to pre-Covid normalized levels, Berry worked to expand its role in other markets for meltblown like healthcare, air filtration, and multiple other markets.
Fitesa
Fitesa operates 11 pure meltblown lines in Brazil, the U.S., Germany and Italy to supply mainly the respiratory protection and wipes markets in these regions.According to Mariana Mynarski, corporate marketing, Fitesa, the demand for meltblown for respiratory protection peaked during the pandemic, as countries invested significantly in local production. During this period Fitesa aggressively invested to support the market needs. Since then, the demand has significantly reduced, and finished products resumed being imported from their original sources, mainly China, she adds.
Fitesa continues to focus on respiratory protection, delivering innovative solutions to help its customers compete in the market. A recent example is a new composite material that combines the filter and external layers of the face mask in one roll good, improving the production efficiency of its customers. Fitesa has also developed biobased external layers that help its customers increase the sustainable content of their finished products and reduce the carbon footprint of the finished product.
Hills Inc.
Meltblown machinery specialist Hills Inc. is operating a dedicated 500mm bico meltblown pilot line, which is being used for process development in Melbourne, FL. This is allowing manufacturers of meltblown nonwovens to develop differentiated products and new markets to help them stand out. Hills is working with meltblown producers to develop processes and modify equipment adding capabilities including: bicomponent fibers for combining polymer features to create unique (and branded) new products; fine fiber products for higher quality webs, finer fibers for higher quality webs; biopolymers and compostables such as PLA and PHA.Additionally, Hills is assisting material and process changes to allow meltblown to displace others materials such as foam.
“The overcapacity and weakened demand is forcing meltblown producers to be creative,” says business development manager Timothy Robson. “Through this, real innovation is opening up opportunities for new uses and markets that should see growth into the future.”
Covid created strong demand for a common type of meltblown; 3-5 micron PP webs that can be electrostatically charged for facemask filters or incorporated into SMS for hydrophobicity. After rapid investment in capacity, the market for this type of meltblown is saturated and will stay that way for some time, Robson adds.
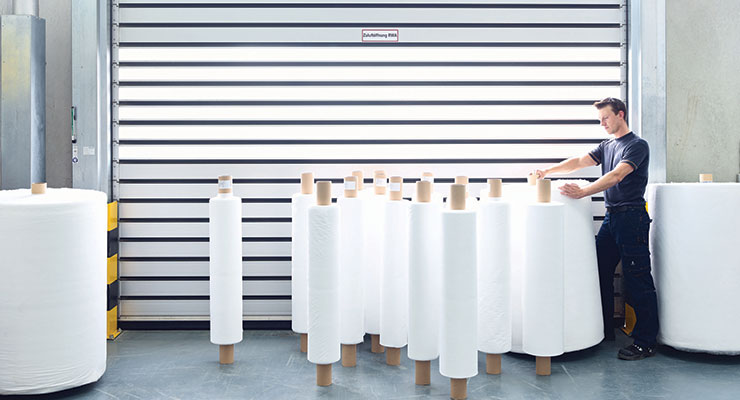
Oversupply continues to plague the meltblown market following an unprecedented surge in investment due to Covid-19.
Mogul
Mogul, which invested in its first meltblown line in 2000, added its fifth and sixth meltblown lines in 2021 to produce materials for N95 and higher efficiency masks as well as high efficiency filtration applications and other industrial applications. The company added its seventh meltblown line in Turkey in 2022, a 1.6 meter-wide Reicofil machine. The meltblown system is equipped with technology for electrostatic charging and supplies high-quality filter material that ensures a high degree of separation, low pressure loss and a high storage capacity. The plant brings an additional annual capacity of 550 tons for N95 material or 365 tons for N99 material to the market. In addition to PP, the new line is capable of running PBT, TPU and PLA polymers.While its first four lines mainly targeted the spill control market, the Reicofil meltblown technology is allowing the company to target both high efficiency masks and filters and running specialty polymers to enter new areas. As face masks demand has waned, the line is ramping up its activity in filtration.
According to commercial director Serkan Gogus, environmental concerns and climate change should drive volumes in filtration. In addition to filtration products, sorbent materials manufactured using meltblown nonwoven goods will be sought after products used in a wide range of areas such as hazardous and spill control, waste management and environmental protection purposes.
Sandler
Sandler started up a new meltblown line in 2021 in response to increased demand for the materials from the Coronavirus pandemic. As demand for materials in face masks and other healthcare-related areas has waned, the company has used its experience in other markets, like filtration, as well as its technological know-how in meltblown to move sales forward.According to Wölfel, regulations concerning facial coverings in public were suspended in most countries in late 2022-2023, leading to demand for nonwovens in these applications to also decrease. Despite this challenge, the meltblown market continues to be an attractive field of business, particularly in filtration.
“Sandler can draw on more than 20 years of experience in meltblown production, the primary application also being filtration,” says Wölfel. “We develop and produce a comprehensive spectrum of pocket as well as pleatable filter media, applied in HVAC, automotive filtration, synthetic vacuum cleaner bags, customized special filters for liquid filtration as well as medical and hygiene applications.”
For HVAC, Sandler media are used in filters classified up to EPA or MERV 16. These media are able to cover all efficiency ranges according to ISO 16890 or former norm EN779. Regarding automotive, meltblown media are used for cabin air applications, filter compounds or liquid filtration, but Sandler also has media for special applications in its portfolio. All of Sandler’s meltblown nonwovens are produced without any chemical additives.
Beyond filtration, Sandler is seeing opportunities for meltblown nonwovens in other technical applications such as industrial cleaning, insulation and support layers and even the food where the single properties of meltblown offer performance advantages.
“In doing so, we also expand our range of raw materials,” Wölfel says. “For example, we use the specific properties of high-performance granules to create specialized media for new areas, providing for example excellent technical properties, chemical-, and oxidation resistance. In close cooperation with customers and partners along the supply chain, we are also constantly working on developing more sustainable product alternatives to expand our product range. In this regard, we focus on both virgin as well as recycled raw materials. This holds true for fiber as well as granule-based raw materials.”
The current meltblown market is subject to various influences. Energy cost or raw material and logistics cost as well as political influences shape the market landscape on a global scale. Based on that, the relocation of commodities to countries with lower production cost will continue. European meltblown producers are forced to revise and strengthen their product portfolio. “I firmly believe that this will drive development in meltblown products to enable differentiation,” he says. “Ultimately, those who face the challenges in the best way with new and robust products will deal best with difficult conditions.”
Tessiture Radici
In early 2021, Radici Group with the help of the Italian government—added a sophisticated meltblown line in Gandino, Italy, to help the company in its efforts against the Covid-19 pandemic. Initially, the line was serving the need for surgical face masks and other PPE materials but, three years later, executives say they have had to be more creative in finding markets for the material.“Initially we started up capacity for face masks and we saw a lot of ups and downs during the pandemic,” says Stefano Frione, commercial director. “We benefitted from going into a lot of more sophisticated markets.”
In 2022, Radici set out to start diversifying the business, of course, looking within markets that are closer to its original strategy in the industrial market such as air and liquid where it acquired a some key accounts. “We have a seen a lot of interest but the business is still slow,” he says. “We expected recovery to be quicker but the market is quite complicated.”
Part of the problem, Frione adds, is there are a lot of meltblown manufacturers looking to expand in the filtration markets. Additionally, the existing players in these markets have been working hard to defend their marketshare.
The overcapacity has created very aggressive prices and it is not always about quality or performance in the lower tier and basic part of the market, he adds. This has really dragged down the prices.
Beyond filtration, Radici has been targeting its meltblown materials at other industrial markets where it already has a presence like roofing and building and industrial sorbents. “We are still in an early stage of these developments so we don’t really have feedback in terms of market trends,” he says. “We are positive because we found some good developments and we have a few projects in the pipeline.”