Karen McIntyre, Editor02.02.24
End of life options for absorbent hygiene products like diapers, feminine care products and wipes continue to be investigated by companies throughout the supply chain. Government legislation and consumer demand are motivating companies to find ways to keep plastic-based products out of landfills and waterways, with new options becoming available, but none are without challenges.
As companies like Procter & Gamble, Kimberly-Clark and Unicharm roll out pilot programs aimed out figuring out not just how to recycle these products, but also how to collect them, these companies continue to rely on partnerships, both public and private, to find the right solutions.
In 2018 Procter & Gamble announced it was embarking on a pilot scale operation, with its joint venture partner Fater, to collect and recycle used baby diapers in Italy. In the ensuing years, the message from P&G was that the company would expand this program into other counties like The Netherlands and India and use the recycled content for applications ranging from school desks to plastic bottle caps to clothing. However, more recently, the company has been reexamining this strategy.
At EDANA’s inaugural sustainability conference in Brussels, Belgium, late last year, Rodrigo Rosati, a P&G researcher, told audience members that despite prolonged investment, the company found it had reached the limits of the technology when it came finding new uses for recycled AHP waste. Finding the right application for recycled diaper materials has continued to pose challenges. “For any recycling operation, it is paramount that the quality of the product you get out can be sold,” he said. “Otherwise, you are just turning waste into waste at a big expense.”
Because the majority, 70-80%, of used diaper products are human waste, the challenge is not just what to do with the diaper waste but how to remove pathogens and pharmaceutical residue (such as diaper rash cream) from the product, which can require an extremely energy intensive process.
According to Rosati, P&G was able to achieve significant knowledge about what needs to be done in recycling efforts. It used a sterilization process to get rid of the pathogens contained in human waste, oxidization to get rid of pharmaceuticals and a dryer to get rid of the liquid.
“Even though this was not the viable solution we were wishing for, it provided many valuable learnings as we continued the journey,” he added.
Another challenge of recycling diaper waste is collection. Because families don’t want to store used and dirty diapers in their homes for prolonged periods of time, P&G piloted a smart bin collection program in Amsterdam, The Netherlands. This provided families with infants with a place to dispose their used diapers. What they found was that busy families did not always have the time nor motivation to travel distances to dispose of diaper waste.
“Through education, investment, communication with the consumer, only a fraction of participants stuck to the patterns of drop off,” Rosati says. “This has been explained by the distance from the household to the smart bin. It represents a burden in the very business lives of households with babies. We need to identify viable collection methods.”
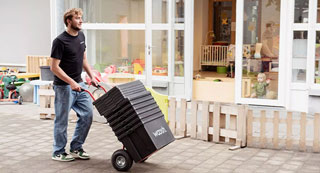
Woosh has partnered with Ontex to launch a diaper recycling
program in Belgium.
Despite these challenges, recent successes include the use of the plastic in composite materials replacing concrete and steel. The cellulose fibers can be used for the production of pet litter, pet care absorbent products, concrete and tarmac additives, brick manufacture, paper and cardboard, insulation materials and agricultural nutrients. Some companies are even examining the use of recycled diaper components in new absorbent products.
Studies also show that the success of diaper recycling depends on the AHP waste collection system in place, people's participation, population density in the collection area, and the technical specifications of the treatment plant e.g. capacity. Moreover, the transport distance from collection areas to the treatment plant and costs for landfilling and incineration, and criteria and rules for recognizing the end of waste and local market for recovered materials are important factors that need to be deeply analyzed before the implementation of the best practice.
Rather than focus on individual residences, Woosh, a Belgian start-up focused on diaper recycling,, announced last year a plan to deliver recyclable, disposable diapers and collects used diapers from more than 200 day care centers in Belgium with more than 5200 children. The company plans to expand the service to more than 1000 day care centers by the end of 2024. Together with waste companies, Woosh aims to set up the first diaper recycling facility in Belgium.
Woosh partnered with Ontex, the maker of Little Big Change diapers, to start this program.
“At Ontex, we aim to reduce our environmental footprint throughout our value chain. Diaper waste is the critical point in the value chain that we need to address, including in our home country Belgium. That is why we helped to launch Woosh and support it,” says Joel Santos, vice president, Strategy.
“We have made it our mission to make diaper recycling possible by providing enough critical mass of used, recyclable diapers to recycling companies,” says Jeff Stubbe, co-founder of Woosh. “Our service to day care centers started in Mechelen and has since expanded to all five provinces of Belgium’s Flanders region.”
The collection of used diapers is the first critical step in establishing the process for large-scale diaper recycling. Together with waste management partners willing to invest, Woosh wants to set up the first diaper recycling plant in Belgium. The diaper waste will be recycled into new raw materials. Until critical mass is reached the diapers will be collected and incinerated. “We want to move from incineration to diaper recycling as quickly as possible and are working with several partners, including the government, to make this happen, ” says Stubbe.
“This project contributes to the ambitions to make Belgium and the Flanders region a recycling hub on a European and global level. In addition to asbestos waste and plastics, diaper waste is a priority for the Flanders Region,” Stubbe adds.
The response from day care centers has been positive. “Thanks to Woosh’s service, we always have a sufficient number of quality diapers and do not have to ask parents to bring their diapers. It’s also nice to be able to contribute, knowing that our used diapers are collected with the aim of recycling disposable diapers in Belgium,” says Romina, manager of the day care center De Engeltjes in the city of Oudenaarde.
Ontex has collaborated with Woosh and other recycling companies to make its diapers more recyclable. Ontex supplies recyclable diapers from its Little Big Change subscription brand to Woosh, which handles distribution. Through the project Ontex also aims to reduce its Scope 3 emissions by replacing incineration of used diapers with the reuse of raw materials. The company aims to be carbon-neutral (Scope 1 & 2) by 2030 and has reduced its Scope 1 & 2 emissions by more than 40% between 2020 and last year.
A leader in diaper recycling technology with its circulation-based method, Japanese diaper maker Unicharm announced in November 2023 it was partnering with Havix Corporation to commercialize processing technology that can create the absorbent material used in adult incontinence products from recycled pulp culled from used diaper materials. Havix is also reportedly making nonwovens using the recycled pulp.
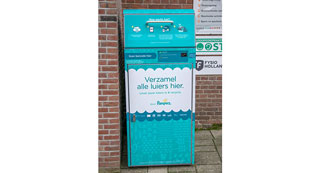
P&G has piloted Smart Bing collection sites for diapers in Amsterdam.
Unicharm first developed the recycling technology through its RefF (Recycle for the Future) project, started in 2015, aimed at recycling absorbent products. Through the use of ozone-based sterilization technology, the company successfully generated recycled pulp that is hygienic and safe and equivalent in quality to unused pulp. In 2022, Unicharm used this recycled pulp for the absorbent layer in its Lifree adult diaper brand and began testing these products in long term care facilities in the South Kyushu, Japan, region. Care facilities have reported that the pants perform similarly to products made from virgin pulp.
The success of this pilot program led Unicharm to seek a partner in Havix, a manufacturer of airlaid and thermal bonded nonwovens as well as absorbent core materials, to manufacture absorbent materials using the recycled pulp.
According to Unicharm, the circulation-based recycling method allows it to use the limited natural resources repeatedly rather than simply throwing them away.
The way the method works is first the diapers are finely ground up, washed and then separated by the materials—pulp and superabsorbent polymers. At this stage, the materials are still somewhat solid and smelly so the pulp is given a special ozone treatment to destroy the bacteria while the SAP is given an acid treatment that restores its absorbing capability. After those treatments, both pulp and SAP become clean and safe sufficiently enough to be reused to make new disposable diapers.
Unicharm’s efforts to restore SAP involved getting rid of all the moisture absorbents to return it to its original absorbent state. Up until now, it was commonly known to use calcium for removing moisture from SAP. However, with this method, the calcium would remain in the restored SAP which results in lowering its quality.
Unicharm worked on this problem by teaming up with scientists at Hokkaido University and they jointly developed a new method of removing moisture without lowering the quality of SAP by using acid. Researchers then applied the ozone treatment to the SAP as same as pulp to ensure that the restored SAP is completely safe and clean.
Like P&G, Unicharm has also focused on collection. The company has partnered with the Japanese city of Shibushi, to collect used disposable diapers separately from other garbage. Used diapers are put in a special plastic bag which is then placed in a garbage can specially designed for diapers. This has allowed people in Shibushi to transform approximately one-fifth of their total “wastes,”the amount of used diapers, into a renewable “resource.”
Unicharm reports that the number of local communities interested in partnering with it for diaper recycling is growing.
Meanwhile, in Australia, Kimberly-Clark is partnering with CSIRO, Australia’s national science agency and one of South Australia’s largest composters to collect and recycle used Huggies diapers. The first trial of its kind in Australia, The Nappy Loop has been underway in South Australia since July 2022 and uses anaerobic digestion to turn the organic materials in used Huggies nappies into nutrient-rich compost, as well as bioenergy that is captured and used to power the recycling process.
Kimberly-Clark ANZ managing director Belinda Driscoll says: “As Huggies is the most popular diaper brand in Australia, we not only set the standards in baby care, our goal is to set the standards for our industry in sustainability too. We believe we have a responsibility to lead by example and find better solutions for the community and our planet.”
“Families and day care centers across the country rely on the convenience and performance of disposable diapers and while we work to innovate and create more sustainable products, recycling is one solution for disposable diaper waste. Identifying a recycling solution that works hasn’t been easy due to the availability of technology and collection systems. Today is a very proud day for us, announcing that we have trialed right here in Australia, and it represents a big step in Kimberly-Clark ANZ’s sustainability strategy,” Driscoll adds.
The Nappy Loop trial has adopted a B2B model, with Solo collecting used Huggies nappies from G8 Education’s Welly Road Early Learning Centre in Mount Barker and delivering them to the Peats composting facility for processing. Utilizing anaerobic digestion, the organic material in the used nappies is transformed into nutrient-rich compost while the plastic components are separated and evaluated for future recycled products. In addition, the anaerobic digestion process creates bioenergy which is captured and used to power the Peats composting facility.
CSIRO’s principal research scientist Dr. Anu Kumar says: “CSIRO is working with Kimberly-Clark Australia to provide scientific validation of The Nappy Loop pilot to help tackle waste. Our research for this Australian trial will help inform the team on the potential scaling of the program to help reduce the amount of nappies ending up in landfill.”
Capable of automatically sorting garments by composition and color, the new line meets the needs of both post-consumer and post-industrial waste markets. The line also removes hard parts such as buttons and zippers to prepare the material for further processing in an Andritz tearing machine.
The automated textile sorting line at Nouvelles Fibres Textiles is dedicated to industrial-scale production, customer trials and projects, and the R&D activities of the partners. It will process textile waste to produce recycled fibers for the spinning, nonwovens, and composites industries.
Automated sorting was the last missing link needed to develop a complete ecosystem in France, where the fashion industry, social and solidarity economy actors, waste management companies, and textile producers from different sectors are working together towards a textile circular economy.
Eric Boel, general manager, Nouvelles Fibres Textiles says, “The opening of the new line marks a milestone in our efforts to turn textile waste into resources. And we are already laying the foundations for a second material preparation plant with a capacity to process 25,000 tons of post-consumer textiles per year.”
In December, Sfilacciatura Negro started up an Andritz textile recycling line at its plant in Biella, Italy. Designed for processing post-consumer textile waste with automatic removal of hard parts, the tearing line supports the company’s expansion into new recycling segments.
In view of the growing demand for sustainable fibers in the re-spinning and nonwoven industries, Sfilacciatura Negro Biella decided to expand its recycling capabilities. The company has extensive experience in recycling industrial textile waste and already operates two tearing lines. Based on its long-term collaboration with Andritz, it is now stepping into the recycling of post-consumer clothing waste.
“Our approach is based on circularity. We make new fibers from textile waste that would otherwise end up in landfills,” Tiziano Negro, CEO of Sfilacciatura Negro, explains and adds, “Having worked with Andritz for a long time and knowing their expertise in both textile recycling and nonwovens, we are convinced they are the right partner to support our company in our ambitious diversification project.”
The new generation recycling line Andritz supplied to Sfilacciatura Negro is the result of 10 years of close cooperation, trials in its technical center, and visits to customer lines in Spain and Portugal. Andritz has tailored a complete line from feeding of sorted waste bales to baling of the recycled fibers. It is designed for highly efficient, energy-saving operation and features automated separation of hard points while maintaining a very good material yield. An automated filtration unit is provided for airflow and dust management. Only one operator is needed to manage the entire line up to the recycled fiber baler. The baler can produce film-wrapped and tied bales with a weight of up to 350 kg.
As companies like Procter & Gamble, Kimberly-Clark and Unicharm roll out pilot programs aimed out figuring out not just how to recycle these products, but also how to collect them, these companies continue to rely on partnerships, both public and private, to find the right solutions.
In 2018 Procter & Gamble announced it was embarking on a pilot scale operation, with its joint venture partner Fater, to collect and recycle used baby diapers in Italy. In the ensuing years, the message from P&G was that the company would expand this program into other counties like The Netherlands and India and use the recycled content for applications ranging from school desks to plastic bottle caps to clothing. However, more recently, the company has been reexamining this strategy.
At EDANA’s inaugural sustainability conference in Brussels, Belgium, late last year, Rodrigo Rosati, a P&G researcher, told audience members that despite prolonged investment, the company found it had reached the limits of the technology when it came finding new uses for recycled AHP waste. Finding the right application for recycled diaper materials has continued to pose challenges. “For any recycling operation, it is paramount that the quality of the product you get out can be sold,” he said. “Otherwise, you are just turning waste into waste at a big expense.”
Because the majority, 70-80%, of used diaper products are human waste, the challenge is not just what to do with the diaper waste but how to remove pathogens and pharmaceutical residue (such as diaper rash cream) from the product, which can require an extremely energy intensive process.
According to Rosati, P&G was able to achieve significant knowledge about what needs to be done in recycling efforts. It used a sterilization process to get rid of the pathogens contained in human waste, oxidization to get rid of pharmaceuticals and a dryer to get rid of the liquid.
“Even though this was not the viable solution we were wishing for, it provided many valuable learnings as we continued the journey,” he added.
Another challenge of recycling diaper waste is collection. Because families don’t want to store used and dirty diapers in their homes for prolonged periods of time, P&G piloted a smart bin collection program in Amsterdam, The Netherlands. This provided families with infants with a place to dispose their used diapers. What they found was that busy families did not always have the time nor motivation to travel distances to dispose of diaper waste.
“Through education, investment, communication with the consumer, only a fraction of participants stuck to the patterns of drop off,” Rosati says. “This has been explained by the distance from the household to the smart bin. It represents a burden in the very business lives of households with babies. We need to identify viable collection methods.”
Wasting Away
According to industry estimates, absorbent hygiene waste currently represents about 2-3% of the total municipal solid waste, and represents up to 15-25% of the residual waste stream in some treatment facilities. As manufacturers have looked at recycling these materials as a way to reduce their strain on landfills, they have found that the separation of AHP waste into its different material components—plastic, pulp and superabsorbent materials—which can be recycled into secondary raw materials—presents challenges Additionally, the presence of human waste, which comprises about 70% of used diapers, affects colorization, purity and odor making potential after-life markets limited.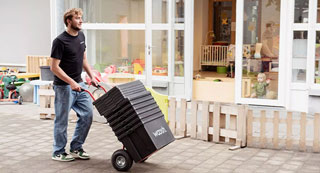
Woosh has partnered with Ontex to launch a diaper recycling
program in Belgium.
Studies also show that the success of diaper recycling depends on the AHP waste collection system in place, people's participation, population density in the collection area, and the technical specifications of the treatment plant e.g. capacity. Moreover, the transport distance from collection areas to the treatment plant and costs for landfilling and incineration, and criteria and rules for recognizing the end of waste and local market for recovered materials are important factors that need to be deeply analyzed before the implementation of the best practice.
Rather than focus on individual residences, Woosh, a Belgian start-up focused on diaper recycling,, announced last year a plan to deliver recyclable, disposable diapers and collects used diapers from more than 200 day care centers in Belgium with more than 5200 children. The company plans to expand the service to more than 1000 day care centers by the end of 2024. Together with waste companies, Woosh aims to set up the first diaper recycling facility in Belgium.
Woosh partnered with Ontex, the maker of Little Big Change diapers, to start this program.
“At Ontex, we aim to reduce our environmental footprint throughout our value chain. Diaper waste is the critical point in the value chain that we need to address, including in our home country Belgium. That is why we helped to launch Woosh and support it,” says Joel Santos, vice president, Strategy.
“We have made it our mission to make diaper recycling possible by providing enough critical mass of used, recyclable diapers to recycling companies,” says Jeff Stubbe, co-founder of Woosh. “Our service to day care centers started in Mechelen and has since expanded to all five provinces of Belgium’s Flanders region.”
The collection of used diapers is the first critical step in establishing the process for large-scale diaper recycling. Together with waste management partners willing to invest, Woosh wants to set up the first diaper recycling plant in Belgium. The diaper waste will be recycled into new raw materials. Until critical mass is reached the diapers will be collected and incinerated. “We want to move from incineration to diaper recycling as quickly as possible and are working with several partners, including the government, to make this happen, ” says Stubbe.
“This project contributes to the ambitions to make Belgium and the Flanders region a recycling hub on a European and global level. In addition to asbestos waste and plastics, diaper waste is a priority for the Flanders Region,” Stubbe adds.
The response from day care centers has been positive. “Thanks to Woosh’s service, we always have a sufficient number of quality diapers and do not have to ask parents to bring their diapers. It’s also nice to be able to contribute, knowing that our used diapers are collected with the aim of recycling disposable diapers in Belgium,” says Romina, manager of the day care center De Engeltjes in the city of Oudenaarde.
Ontex has collaborated with Woosh and other recycling companies to make its diapers more recyclable. Ontex supplies recyclable diapers from its Little Big Change subscription brand to Woosh, which handles distribution. Through the project Ontex also aims to reduce its Scope 3 emissions by replacing incineration of used diapers with the reuse of raw materials. The company aims to be carbon-neutral (Scope 1 & 2) by 2030 and has reduced its Scope 1 & 2 emissions by more than 40% between 2020 and last year.
A leader in diaper recycling technology with its circulation-based method, Japanese diaper maker Unicharm announced in November 2023 it was partnering with Havix Corporation to commercialize processing technology that can create the absorbent material used in adult incontinence products from recycled pulp culled from used diaper materials. Havix is also reportedly making nonwovens using the recycled pulp.
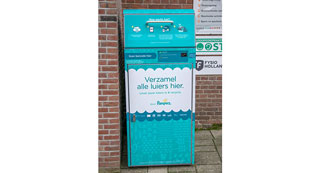
P&G has piloted Smart Bing collection sites for diapers in Amsterdam.
The success of this pilot program led Unicharm to seek a partner in Havix, a manufacturer of airlaid and thermal bonded nonwovens as well as absorbent core materials, to manufacture absorbent materials using the recycled pulp.
According to Unicharm, the circulation-based recycling method allows it to use the limited natural resources repeatedly rather than simply throwing them away.
The way the method works is first the diapers are finely ground up, washed and then separated by the materials—pulp and superabsorbent polymers. At this stage, the materials are still somewhat solid and smelly so the pulp is given a special ozone treatment to destroy the bacteria while the SAP is given an acid treatment that restores its absorbing capability. After those treatments, both pulp and SAP become clean and safe sufficiently enough to be reused to make new disposable diapers.
Unicharm’s efforts to restore SAP involved getting rid of all the moisture absorbents to return it to its original absorbent state. Up until now, it was commonly known to use calcium for removing moisture from SAP. However, with this method, the calcium would remain in the restored SAP which results in lowering its quality.
Unicharm worked on this problem by teaming up with scientists at Hokkaido University and they jointly developed a new method of removing moisture without lowering the quality of SAP by using acid. Researchers then applied the ozone treatment to the SAP as same as pulp to ensure that the restored SAP is completely safe and clean.
Like P&G, Unicharm has also focused on collection. The company has partnered with the Japanese city of Shibushi, to collect used disposable diapers separately from other garbage. Used diapers are put in a special plastic bag which is then placed in a garbage can specially designed for diapers. This has allowed people in Shibushi to transform approximately one-fifth of their total “wastes,”the amount of used diapers, into a renewable “resource.”
Unicharm reports that the number of local communities interested in partnering with it for diaper recycling is growing.
Meanwhile, in Australia, Kimberly-Clark is partnering with CSIRO, Australia’s national science agency and one of South Australia’s largest composters to collect and recycle used Huggies diapers. The first trial of its kind in Australia, The Nappy Loop has been underway in South Australia since July 2022 and uses anaerobic digestion to turn the organic materials in used Huggies nappies into nutrient-rich compost, as well as bioenergy that is captured and used to power the recycling process.
Kimberly-Clark ANZ managing director Belinda Driscoll says: “As Huggies is the most popular diaper brand in Australia, we not only set the standards in baby care, our goal is to set the standards for our industry in sustainability too. We believe we have a responsibility to lead by example and find better solutions for the community and our planet.”
“Families and day care centers across the country rely on the convenience and performance of disposable diapers and while we work to innovate and create more sustainable products, recycling is one solution for disposable diaper waste. Identifying a recycling solution that works hasn’t been easy due to the availability of technology and collection systems. Today is a very proud day for us, announcing that we have trialed right here in Australia, and it represents a big step in Kimberly-Clark ANZ’s sustainability strategy,” Driscoll adds.
The Nappy Loop trial has adopted a B2B model, with Solo collecting used Huggies nappies from G8 Education’s Welly Road Early Learning Centre in Mount Barker and delivering them to the Peats composting facility for processing. Utilizing anaerobic digestion, the organic material in the used nappies is transformed into nutrient-rich compost while the plastic components are separated and evaluated for future recycled products. In addition, the anaerobic digestion process creates bioenergy which is captured and used to power the Peats composting facility.
CSIRO’s principal research scientist Dr. Anu Kumar says: “CSIRO is working with Kimberly-Clark Australia to provide scientific validation of The Nappy Loop pilot to help tackle waste. Our research for this Australian trial will help inform the team on the potential scaling of the program to help reduce the amount of nappies ending up in landfill.”
Textile Firms Focus on Recycling
With demand for recycled fibers growing within the woven and nonwovens industries, textile companies are focusing on recycling used textiles. In November, Nouvelles Fibres Textiles started up France's first industrial plant for automated sorting and recycling of textile waste in Amplepuis. The plant is the result of a partnership between textile recycling company Nouvelles Fibres Textiles, waste sorting specialist Pellenc ST and international technology group Andritz, a specialist in textile recycling machinery and processes. These efforts are seeking to tackle the challenge of textile waste in the European Union. The EU's strategy for sustainable and circular textiles aims to ensure that by 2030 textile products are made to a great extent of recycled fibers and incineration and landfilling of textiles are minimized.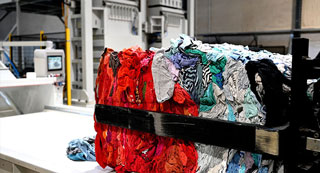
The automated textile sorting line at Nouvelles Fibres Textiles is dedicated to industrial-scale production, customer trials and projects, and the R&D activities of the partners. It will process textile waste to produce recycled fibers for the spinning, nonwovens, and composites industries.
Automated sorting was the last missing link needed to develop a complete ecosystem in France, where the fashion industry, social and solidarity economy actors, waste management companies, and textile producers from different sectors are working together towards a textile circular economy.
Eric Boel, general manager, Nouvelles Fibres Textiles says, “The opening of the new line marks a milestone in our efforts to turn textile waste into resources. And we are already laying the foundations for a second material preparation plant with a capacity to process 25,000 tons of post-consumer textiles per year.”
In December, Sfilacciatura Negro started up an Andritz textile recycling line at its plant in Biella, Italy. Designed for processing post-consumer textile waste with automatic removal of hard parts, the tearing line supports the company’s expansion into new recycling segments.
In view of the growing demand for sustainable fibers in the re-spinning and nonwoven industries, Sfilacciatura Negro Biella decided to expand its recycling capabilities. The company has extensive experience in recycling industrial textile waste and already operates two tearing lines. Based on its long-term collaboration with Andritz, it is now stepping into the recycling of post-consumer clothing waste.
“Our approach is based on circularity. We make new fibers from textile waste that would otherwise end up in landfills,” Tiziano Negro, CEO of Sfilacciatura Negro, explains and adds, “Having worked with Andritz for a long time and knowing their expertise in both textile recycling and nonwovens, we are convinced they are the right partner to support our company in our ambitious diversification project.”
The new generation recycling line Andritz supplied to Sfilacciatura Negro is the result of 10 years of close cooperation, trials in its technical center, and visits to customer lines in Spain and Portugal. Andritz has tailored a complete line from feeding of sorted waste bales to baling of the recycled fibers. It is designed for highly efficient, energy-saving operation and features automated separation of hard points while maintaining a very good material yield. An automated filtration unit is provided for airflow and dust management. Only one operator is needed to manage the entire line up to the recycled fiber baler. The baler can produce film-wrapped and tied bales with a weight of up to 350 kg.