Karen McIntyre, Editor01.08.24
The increased incorporation of ultrasonic bonding technology continues to offer improved fit in disposable hygiene products while reducing their overall environmental impact. As manufacturers of baby and adult care items are focusing on more customized designs, advancements in ultrasonics technology are allowing them to bond materials more quickly to drive down the costs and improve the breathability and flexibility of the end products.
While ultrasonics technology has been around for decades, not until recently, with the development of rotary horn technology, has the industry experienced the added benefit of speed which, in the past, had been a negative, according to Guy Gil, president, Chase Machine and Engineering.
When designing new products that can be manufactured with ultrasonic technology, issues like breathability and delamination are of less concern. Additionally, ultrasonic bond patterns may be selected that provide not only adequate weld strength but the desired flexibility, breathability and appearance as well, creating a superior product.
“As nonwoven materials continue to advance, more and more opportunities within the absorbent industry become available,” Gil adds. “Thinner, lightweight materials can often be bonded much faster which helps drive down the cost of manufacturing as well as improve the breathability and flexibility of the end product.”
According to Shivani Singh, marketing manager, Dukane Ultrasonics, Ultrasonics technology is also extending its reach beyond absorbent products, finding applications in diverse markets like filtration, automotive, and nonwoven applications. "Growth prospects are evident in industries such as EV power, medical and hygiene, where precise bonding, sealing, or cutting is essential for enhanced efficiency and product performance. Moreover, the packaging sector is experiencing a surge in the adoption of ultrasonics, particularly for bonding sustainable materials like papers and monolayer films.
Influencing Hygiene Product Design
Earlier this year, Unicharm announced it had incorporated ultrasonics into the design of its latest Lifree Ultra Slim Comfort Pants. These pants, which are part of the best-selling adult incontinence care brand “LIFREE,” feature the adoption of ultrasonic bonding technology in the waist area, allowing for easy lifting with minimal effort to provide a comfortable fit. This improvement also enhances compression rate and loading efficiency, improving delivery efficiency, thereby reducing the environmental impact. Additionally, by reducing the amount of hot melt adhesives used in the conventional bonding process, the pants become easier to recycle, contributing to the realization of a circular economy-oriented product design.
According to Ned Mansour, business unit director Nonwovens, Herrmann Ultrasonics, the ultrasonic anchoring of elastic threads in panel and cuff applications is achieved through technologies like its Elastic Threat Anchoring ETA solutions. “Eliminating glue addresses concerns such as maintenance, consumables and downtime. Implementing our ETA solution positively influences sustainability initiatives and enhances product quality, softness, and the overall customer experience,” he says.
Herrmann Ultrasonics offers production solutions tailored for applications demanding a reliable and uniform continuous bond between materials. Ultrasonics, its core focus, finds applications across a diverse range of industries. In these sectors, ultrasonics is increasingly adopted for bonding, laminating and cutting processes to enhance product quality and minimize maintenance, consumables and downtime concerns.
As products like pull-up adult diapers and pants and pants-type baby diapers continue to outpace tape-style products, the use of ultrasonics technology is growing in the hygiene market. Ultrasonics offers customers more flexibility to explore new designs and new features, allowing them to customize their products to meet individual user preference.
“We are seeing more and more customers in the absorbent products industry, among others, switching to ultrasonic technology,” says Sarah Karmilowicz, business development representative, Sonobond Ultrasonics. “Ultrasonics offer adaptability that proves essential for addressing a range of market demands and maintaining a competitive edge in the industry.”
This versatility empowers manufacturers to develop products that not only meet functional needs but also resonate with the ever-changing preferences of consumers. Consequently, businesses can distinguish their offerings, increase brand attractiveness and respond adeptly to the dynamic landscape of consumer expectations in the absorbent products market.
Ultrasonics technology enables precise bonding and waterproof seams, significantly improving the overall effectiveness and efficiency of absorbent products. This includes but is not limited to its use in hygiene items such as diapers, adult incontinence products and feminine hygiene goods. The accuracy provided by ultrasonics during the bonding process enhances the dependability of these products and reduces the potential for leaks, and ultimately elevating user comfort.
“Ultrasonics creates a seamless weld,” says Karmilowicz. “This optimizes comfort while creating a leak proof seal. The flexibility of ultrasonics allows for customization in design. Our pattern wheels allow users to customize the seam design. We have even made custom logo pattern wheels for customers.”
Sonobond maintains an innovative approach to ultrasonic technology, including its patented rotary bonding methods. The automotive industry and technical textiles sectors are increasingly adopting ultrasonic welding for joining and assembling various textile components. This includes applications such as seat covers and interior components where precision and strength are crucial. The pandemic led to an increased reliance on medical textiles and disposable PPE items.
Hygiene equipment supplier Andritz Diatec has also incorporated ultrasonic bonding technology into its line up. The neXbond ultrasonic bonding technology combines tensioned elastics entrapped between two layers of nonwoven fabrics to deliver a uniquely soft and skin-friendly waistband for diapers and leg cuffs without using glue or adhesives.
Compared to adhesives, the neXbond ultrasonic technology yields a top-quality bonding with no creep or product damage and with greater precision. The end user benefits from products that are gentle on the skin with a high quality of softness, breathability, elastic performance and a sense of discretion and high comfort because they adapt to every movement, rather than belts that include glues. Moreover, it minimizes allergic reactions and irritation on the skin, due to the chemical-free process.
Manufacturers are constantly redesigning their products to gain a competitive advantage not only in form, fit and function but also how they can have less of an environmental impact. Improved recycling, reduced packaging materials and the elimination of adhesives are all great benefits of using ultrasonic technology. As they continue to develop more green, sustainable and environmentally friendly consumer products, the practice of blending fibers is becoming more common. If the nonwoven material contains more than 70% synthetic material, ultrasonics may be a viable option for assembly without the need of adhesives or sewing.
“Ultrasonics minimizes energy consumption compared to thermal or adhesive processes by only using energy when ultrasonics are engaged. Another advantage to using ultrasonics is precision. Ultrasonics only bond materials based on the anvil pattern used and there is no overspill of bonds onto the material,” Mansour says. “This helps to minimizes rejects due to over-bonding which leads to an efficient and effective production process. This ensures sustainability is at the forefront of our solutions without interfering with the quality of the bonds.”
Herrmann’s ultrasonic bonding solutions positively affect hygiene products’ design and manufacturing processes, particularly enhancing the overall customer experience thanks to unmatched tactile softness achieved through ultrasonic bonding surpasses that of glue processes, he adds. “Other advantages to utilizing ultrasonics are streamlining manufacturing processes and reducing investments in equipment, zero ramp-up and cool down times, consumables, no cleanup and reduced downtime.”
The need for reduced downtime and increased innovation, has led Herrmann Ultrasonics to create the Microbond G4 System, which allows for customers to receive virtual support during downtime scenarios, all while minimizing service costs through rapid response times and reduced travel expenses. Herrmann can remotely access a line to solve problems regardless of their physical location; this feature allows Herrmann’s service technicians to respond rapidly. The feature allows the customer to share specific information, which maintains privacy and security on-site and safeguards the customer’s production by facilitating the upload of the latest backups, updates, and configuration files. The Microbond G4 System also has an add-on feature that allows for real time data trending during operations in real-time.
Dukane's patented ultrasonic elastic attachment empowers product designers to create products with superior fit by strategically positioning elastic strands in nearly any location, optimizing the fit, comfort, and overall performance of the product. Applications include elastic panel, waist band, containment flaps and combined backsheet lamination with leg cuff.
The company's ultrasonic bonding product portfolio for hygiene applications include high-speed Rotary sonotrodes, air loaded RAM (Rigid Acoustical Module) sonotrode’s and the OptiBonder equipped with Dukane;s exclusive Bond Balance Technology. This product lineup consists of tailored solutions, providing cost-effective options for both top tier and mid-tier processes in various ranges of operating frequencies. These products have been developed to address the need for cost effective bonding solutions to replace adhesives and meet sustainability goals set by manufacturers.
"Many companies are now discovering the benefits of our patented ultrasonic elastic attachment technology," says marketing manager Shivani Singh.
Additionally, the versatility of the modules offered in Duane’s hygiene product portfolio is driving the use of ultrasonics. These allow customers to have a more sustainable process while maintaining the flexibility they had with adhesives. "Our proprietary designs from our “creative minds” give our trusted partners the capability to achieve both sustainability and flexibility," Singh adds.
MS Ultrasonics sees increased demand for ultrasonics technology in markets like pants-style diapers and incontinence products where ultrasonic sealing replaces the use of tapes and adhesives. The company continues to work on cross seam applications for baby pants and incontinence products, according to Christian Unser, head of nonwovens sales, where the special features of these projects are a soft seam and speed greater than 300 meters per minute.
“As the age and number of older people increases, incontinence products will become even more important and the demand for comfort, softness and discretion is also particularly strong in this market,” he says. “Meanwhile, in the baby care areas, pants-type increasing in popularity among parents, which is reflected in the sizes and quantities required. An ultrasonically sealed diaper is much softer, does not rustle, is less bulky and reduces the size of the packaging.”
Beyond hygiene, areas of interest for MS Ultrasonics’ technology include wound care, packaging applications and filtration. Sonobond, meanwhile, highlights filtration and automotives as diverse growth areas.
“This technology provides distinct advantages within these industries, leading to its increasing prevalence,” Karmilowicz says. “The opportunities for growth are wide-ranging and varied, reflecting the versatility and applicability of ultrasonic solutions across different sectors.
Any industry that requires customization and design flexibility, such as personal absorbency products, automotive interiors, specialized filtration applications and more, offer significant growth potential for ultrasonic technology.”
Applications centered around PPE and filtration products are noticeably on the rise at Chase. “Since nonwovens are primarily used in these types of consumable products, and ultrasonics is an effective and cost-efficient method of assembly, the demand will certainly continue to drive growth for the foreseeable future,” Gil concludes.
While ultrasonics technology has been around for decades, not until recently, with the development of rotary horn technology, has the industry experienced the added benefit of speed which, in the past, had been a negative, according to Guy Gil, president, Chase Machine and Engineering.
When designing new products that can be manufactured with ultrasonic technology, issues like breathability and delamination are of less concern. Additionally, ultrasonic bond patterns may be selected that provide not only adequate weld strength but the desired flexibility, breathability and appearance as well, creating a superior product.
“As nonwoven materials continue to advance, more and more opportunities within the absorbent industry become available,” Gil adds. “Thinner, lightweight materials can often be bonded much faster which helps drive down the cost of manufacturing as well as improve the breathability and flexibility of the end product.”
According to Shivani Singh, marketing manager, Dukane Ultrasonics, Ultrasonics technology is also extending its reach beyond absorbent products, finding applications in diverse markets like filtration, automotive, and nonwoven applications. "Growth prospects are evident in industries such as EV power, medical and hygiene, where precise bonding, sealing, or cutting is essential for enhanced efficiency and product performance. Moreover, the packaging sector is experiencing a surge in the adoption of ultrasonics, particularly for bonding sustainable materials like papers and monolayer films.
Influencing Hygiene Product Design
Earlier this year, Unicharm announced it had incorporated ultrasonics into the design of its latest Lifree Ultra Slim Comfort Pants. These pants, which are part of the best-selling adult incontinence care brand “LIFREE,” feature the adoption of ultrasonic bonding technology in the waist area, allowing for easy lifting with minimal effort to provide a comfortable fit. This improvement also enhances compression rate and loading efficiency, improving delivery efficiency, thereby reducing the environmental impact. Additionally, by reducing the amount of hot melt adhesives used in the conventional bonding process, the pants become easier to recycle, contributing to the realization of a circular economy-oriented product design.
According to Ned Mansour, business unit director Nonwovens, Herrmann Ultrasonics, the ultrasonic anchoring of elastic threads in panel and cuff applications is achieved through technologies like its Elastic Threat Anchoring ETA solutions. “Eliminating glue addresses concerns such as maintenance, consumables and downtime. Implementing our ETA solution positively influences sustainability initiatives and enhances product quality, softness, and the overall customer experience,” he says.
Herrmann Ultrasonics offers production solutions tailored for applications demanding a reliable and uniform continuous bond between materials. Ultrasonics, its core focus, finds applications across a diverse range of industries. In these sectors, ultrasonics is increasingly adopted for bonding, laminating and cutting processes to enhance product quality and minimize maintenance, consumables and downtime concerns.
As products like pull-up adult diapers and pants and pants-type baby diapers continue to outpace tape-style products, the use of ultrasonics technology is growing in the hygiene market. Ultrasonics offers customers more flexibility to explore new designs and new features, allowing them to customize their products to meet individual user preference.
“We are seeing more and more customers in the absorbent products industry, among others, switching to ultrasonic technology,” says Sarah Karmilowicz, business development representative, Sonobond Ultrasonics. “Ultrasonics offer adaptability that proves essential for addressing a range of market demands and maintaining a competitive edge in the industry.”
This versatility empowers manufacturers to develop products that not only meet functional needs but also resonate with the ever-changing preferences of consumers. Consequently, businesses can distinguish their offerings, increase brand attractiveness and respond adeptly to the dynamic landscape of consumer expectations in the absorbent products market.
Ultrasonics technology enables precise bonding and waterproof seams, significantly improving the overall effectiveness and efficiency of absorbent products. This includes but is not limited to its use in hygiene items such as diapers, adult incontinence products and feminine hygiene goods. The accuracy provided by ultrasonics during the bonding process enhances the dependability of these products and reduces the potential for leaks, and ultimately elevating user comfort.
“Ultrasonics creates a seamless weld,” says Karmilowicz. “This optimizes comfort while creating a leak proof seal. The flexibility of ultrasonics allows for customization in design. Our pattern wheels allow users to customize the seam design. We have even made custom logo pattern wheels for customers.”
Sonobond maintains an innovative approach to ultrasonic technology, including its patented rotary bonding methods. The automotive industry and technical textiles sectors are increasingly adopting ultrasonic welding for joining and assembling various textile components. This includes applications such as seat covers and interior components where precision and strength are crucial. The pandemic led to an increased reliance on medical textiles and disposable PPE items.
Hygiene equipment supplier Andritz Diatec has also incorporated ultrasonic bonding technology into its line up. The neXbond ultrasonic bonding technology combines tensioned elastics entrapped between two layers of nonwoven fabrics to deliver a uniquely soft and skin-friendly waistband for diapers and leg cuffs without using glue or adhesives.
Compared to adhesives, the neXbond ultrasonic technology yields a top-quality bonding with no creep or product damage and with greater precision. The end user benefits from products that are gentle on the skin with a high quality of softness, breathability, elastic performance and a sense of discretion and high comfort because they adapt to every movement, rather than belts that include glues. Moreover, it minimizes allergic reactions and irritation on the skin, due to the chemical-free process.
An Efficient Process
A growing emphasis on sustainability across industries creates a favorable opportunity for the adoption of ultrasonic technology, Gil says. “This is noteworthy as ultrasonics frequently minimize the reliance on adhesives, offering a more eco-friendly approach to manufacturing processes. The reduction in adhesive usage not only aligns with sustainability goals by decreasing the environmental impact associated with adhesive production and disposal but also contributes to more resource-efficient and environmentally conscious manufacturing practices. As industries continue to prioritize sustainability, the eco-friendly attributes of ultrasonic technology position it as a promising solution for businesses seeking to enhance their environmental credentials.”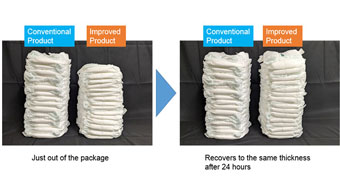
“Ultrasonics minimizes energy consumption compared to thermal or adhesive processes by only using energy when ultrasonics are engaged. Another advantage to using ultrasonics is precision. Ultrasonics only bond materials based on the anvil pattern used and there is no overspill of bonds onto the material,” Mansour says. “This helps to minimizes rejects due to over-bonding which leads to an efficient and effective production process. This ensures sustainability is at the forefront of our solutions without interfering with the quality of the bonds.”
Herrmann’s ultrasonic bonding solutions positively affect hygiene products’ design and manufacturing processes, particularly enhancing the overall customer experience thanks to unmatched tactile softness achieved through ultrasonic bonding surpasses that of glue processes, he adds. “Other advantages to utilizing ultrasonics are streamlining manufacturing processes and reducing investments in equipment, zero ramp-up and cool down times, consumables, no cleanup and reduced downtime.”
The need for reduced downtime and increased innovation, has led Herrmann Ultrasonics to create the Microbond G4 System, which allows for customers to receive virtual support during downtime scenarios, all while minimizing service costs through rapid response times and reduced travel expenses. Herrmann can remotely access a line to solve problems regardless of their physical location; this feature allows Herrmann’s service technicians to respond rapidly. The feature allows the customer to share specific information, which maintains privacy and security on-site and safeguards the customer’s production by facilitating the upload of the latest backups, updates, and configuration files. The Microbond G4 System also has an add-on feature that allows for real time data trending during operations in real-time.
Dukane's patented ultrasonic elastic attachment empowers product designers to create products with superior fit by strategically positioning elastic strands in nearly any location, optimizing the fit, comfort, and overall performance of the product. Applications include elastic panel, waist band, containment flaps and combined backsheet lamination with leg cuff.
The company's ultrasonic bonding product portfolio for hygiene applications include high-speed Rotary sonotrodes, air loaded RAM (Rigid Acoustical Module) sonotrode’s and the OptiBonder equipped with Dukane;s exclusive Bond Balance Technology. This product lineup consists of tailored solutions, providing cost-effective options for both top tier and mid-tier processes in various ranges of operating frequencies. These products have been developed to address the need for cost effective bonding solutions to replace adhesives and meet sustainability goals set by manufacturers.
"Many companies are now discovering the benefits of our patented ultrasonic elastic attachment technology," says marketing manager Shivani Singh.
Additionally, the versatility of the modules offered in Duane’s hygiene product portfolio is driving the use of ultrasonics. These allow customers to have a more sustainable process while maintaining the flexibility they had with adhesives. "Our proprietary designs from our “creative minds” give our trusted partners the capability to achieve both sustainability and flexibility," Singh adds.
MS Ultrasonics sees increased demand for ultrasonics technology in markets like pants-style diapers and incontinence products where ultrasonic sealing replaces the use of tapes and adhesives. The company continues to work on cross seam applications for baby pants and incontinence products, according to Christian Unser, head of nonwovens sales, where the special features of these projects are a soft seam and speed greater than 300 meters per minute.

Beyond hygiene, areas of interest for MS Ultrasonics’ technology include wound care, packaging applications and filtration. Sonobond, meanwhile, highlights filtration and automotives as diverse growth areas.
“This technology provides distinct advantages within these industries, leading to its increasing prevalence,” Karmilowicz says. “The opportunities for growth are wide-ranging and varied, reflecting the versatility and applicability of ultrasonic solutions across different sectors.
Any industry that requires customization and design flexibility, such as personal absorbency products, automotive interiors, specialized filtration applications and more, offer significant growth potential for ultrasonic technology.”
Applications centered around PPE and filtration products are noticeably on the rise at Chase. “Since nonwovens are primarily used in these types of consumable products, and ultrasonics is an effective and cost-efficient method of assembly, the demand will certainly continue to drive growth for the foreseeable future,” Gil concludes.