Exclusive data from the forthcoming Smithers report—The Future of Global Nonwovens to 2029—show that in 2023, North American demand for automotive nonwovens will reach a projected 66,400 tons, with a value of $441.1 million. Smithers forecasts a compound annual growth rate (CAGR) of just over 10% for the next five years, with value rising to $657.6 million (at constant pricing). Consumption growth will be slower, increasing to 82,100 tons in 2029.
With the automotive industry transitioning from liquid fuel internal combustion engine-based vehicles to EVs, the timing for this transition will affect nonwovens demand in some cases, according to Phil Mango, nonwovens consultant, Smithers.
“Electric vehicles require no fuel filters, which use nonwovens,” he says. “They also do not use oil filters. They will still use air filters, both for cabin air and possibly for the battery. While engine noise is lower for EVs, outside noise is more noticeable. Insulation locations, and types may change, but nonwoven usage will most likely increase.”
The net nonwoven usage difference for EVs versus internal combustion vehicles is projected to be net volume gains but differing in products and performance requirements, he adds. “Discounting the changes for EVs versus internal combustion vehicles, there are some factors that are common to both types of vehicles. First, global economic conditions (Covid, Ukraine, labor issues, chip shortages) resulted in slower vehicle production since 2020. In fact, 2023 motor vehicle production is still lower than 2019. If an expected recovery in global economic conditions materializes in the next five years, there should be a corresponding increase in vehicle production,” he explains.
Meanwhile, a long-term driver for nonwovens usage in automotives has been the need to reduce weight, to increase miles per gallon or miles per charge. “Many governments have regulated this need. Nonwovens are typically lighter in weight than competitive products,” Mango says.
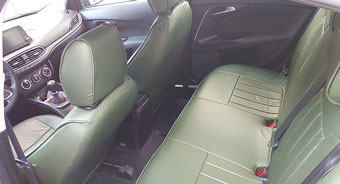
Mogul’s Madaline Ultraleather is used in seating applications.
Serkan Gögüs, CEO of Turkish nonwovens producer Mogul, also expects these factors to expand the role of nonwovens in the automotive market. Sustainability is changing car designs and manufacturers are trying to use materials that are recyclable, and they are trying to use similar type raw materials to simplify the recycling process. Another big driver is weight reduction, which gives an advantage to nonwovens since they can provide similar or better performance at lighter weights, he says.
Although the electrification of cars and new car concepts will completely change car designs—with most filters, especially used for fuel, being eliminated—Gögüs says there will be new requirements such as brake dust filters, cabin air filters and e-axle fluid filters. Additionally, the elimination of engine noise now makes some sounds like ground noise become more apparent, which requires different acoustical performance and requirements.
“Automotive is in sort of a standby period due to the chip problem, and there’s an unmet demand which will create a production boom when the problem is fully solved,” says Gögüs. “The EV era will shape the future of the industry. Sustainability and new demands created by EV vehicles will increase demand for nonwovens.”
For this market, Mogul currently offers a range of different materials that are being used for acoustics, airbag liners, seat inside liners, trim parts, headliners and cabin air filters, etc. It is also aiming to increase its offerings for filtration, acoustical insulation and seat covers.
In visible areas in the vehicle interior, Mogul is seeing an increasing trend for microfiber-based specialty materials in seating applications and headliners. “Our revolutionary fabric Madaline’s new range Ultraleather is developed specifically for such applications,” he says.
Meanwhile, Osaka, Japan-based Toray Industries has focused on acoustic materials for the automotive industry. The growth of EVs requires nonwovens to have not only lightweight performance, but also a change in the required sound absorption range, i.e., the change from engine noise to motor noise and road noise, according to Tatsuya Bessho, manager of corporate communications, Toray. “In this sense, we believe that the growth of EVs is positive for the nonwoven industry,” he says.
Toray offers the sound acoustic insulation Airlite, a material that enhances passenger comfort by suppressing noise from driving, vibrations and from outside vehicles. Last year the company announced that its subsidiaries Toray Textiles Central Europe s.r.o. (TTCE) and Toray Advanced Materials Korea Inc. (TAK) set up new facilities in the Czech Republic to expand the scope of its Airlite automotive interior sound acoustic insulation business in Europe. The investment went online in October 2022 with an annual production capacity of 1200 metric tons.
Airlite is a meltblown nonwoven sound-absorbing material made of lightweight polypropylene and polyester. Airlite delivers exceptional sound absorption across a broad frequency range. It is lighter than conventional counterparts, thereby reducing energy consumption from driving.
The new Airlite facilities will complement TTCE’s airbag fabric operations, helping it to expand its automotive materials business. TAK looks to leverage the new facilities to bolster its automotive interior sound-absorbing materials business in Europe and step-up efforts to serve automakers and leading parts manufacturers as Europe’s electric vehicle market grows.
“The demand for comfort in vehicle interiors is increasing year by year, and sound-absorbing materials play a very important role in this context,” Bessho explains. “In other words, sound-absorbing materials play an important role not only in conventional engine noise suppression, but also in suppressing external noise in electric vehicles.”
Getting Greener
Sage Automotive Interiors, a South Carolina-based manufacturer of material for automotive interiors, has focused on acquisition to boost its role in the automotive market since it was spun-off from Milliken & Company in 2009. At the time, Sage was predominantly producing A-surface textiles for seating in automotive vehicles in North America. “Since then, we have expanded quite significantly both geographically and product wise,” says Dirk Pieper, Chairman of Sage Automotive and Lead Executive Officer of Asahi Kasei.In 2015, Sage acquired Miko S.r.l., an Italian maker of suede-like automotive interior fabrics called Dinamica, a microfiber obtained from recycled PET fibers. According to Pieper, Dinamica is a very high-end nonwoven suede material that goes into a number of luxury high-end vehicles. Since the acquisition, the brand has grown significantly in Europe, North America and China. “It was probably about a $35 million company, and this next year it will be over $300 million, so it’s had expansive growth,” he says.
After being acquired by Asahi Kasei in 2018, Sage went on to purchase the automotive fabrics business of Adient plc for $175 million in 2020. Adient is one of the leading suppliers in the European market for automotive seat fabric. With this acquisition, Sage gained several operating sites around the world centered in Europe.
“We’ve grown from about a $250 million company to about $900 million and will probably reach $1 billion by 2024/2025,” Pieper says.
Among its efforts to expand its sustainable offerings, Sage’s parent company Asahi Kasei recently invested in U.S.-based startup Natural Fiber Welding (NFW), a producer of non-petroleum-based leather alternative for car interiors. As part of Asahi Kasei’s medium-term growth strategy and in close cooperation with Sage, this strategic partnership enables another major step to support global automotive OEMs in reducing the environmental burden of automobiles.
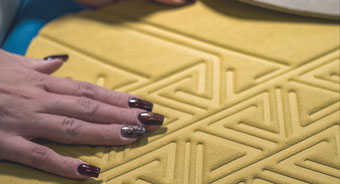
Sage Automotive’s Dinamica product is a high-end nonwoven suede material for automotive interiors.
“Being the largest automotive interior supplier, we’re always looking for more sustainable methods,” Pieper says. “The unique feature of Mirum, and the reason that we’ve invested in NFW, is because people are really looking for the true sustainable solution with a very good end-of-life where the product can actually be recycled. Mirum is the product today that does that, and we have not discovered another product out there that qualifies for this type of end-of-life that is truly recyclable.”
When Mirum is cut into seat parts, for example, all the scrap waste can be put back into the manufacturing process and remain in the new Mirum, he says. “That’s pretty unique because you can’t do that today with leather, PVC or polyurethane, so all those factors really allow it for the consumer who wants to be in a vehicle and sit on a truly sustainable material. We believe that Mirum offers the best solution.”
According to nonwovens producer Ahlstrom, the role of the nonwoven in the automotive market above all has changed: it is now a product family in which the stakeholders of the automotive business rely on to go ‘greener.’
“Nonwovens are everywhere in the car; hence they are a key element to the success of the industry transformation towards a lesser impact on the environment,” says Maxence Decamps, key account manager, Sales Industrial Nonwovens, Ahlstrom. “Innovative and agile nonwovens manufacturers can partner with the automotive supply chain to address this deep transformation journey. That’s what Ahlstrom does.”
For electric vehicles, the challenge is to keep as much energy as possible to drive more kilometers. “Nonwovens are so predominant in the car structure that they can participate efficiently to the weight loss of upcoming car models,” says Arnaud Lerailler, sales manager, Industrial Nonwovens, Ahlstrom.
Earlier this year Ahlstrom introduced a new range of renewable and sustainable filtration solutions for automotive applications.
Ahlstrom ECO is a new filter media that utilizes lignin-based impregnation, replacing fossil-based resin. “The resin contains a significant amount of bio-based renewable lignin, while the mechanical properties and durability of the filter media, even in challenging environments, are maintained,” says Noora Blasi, marketing manager Filtration, Ahlstrom. “Ahlstrom ECO supports the increased sustainability demands of the global transportation market and offers a new choice for filter manufacturers.”
According to Ahlstrom’s initial estimates, the new lignin-based impregnated filter media displays a lower carbon footprint than a standard fossil-based resin media. Additionally, the lignin-based impregnation recipe brings a significant reduction, between 50-70%, of formaldehyde emissions during the curing process.
In May, Ahlstrom ECO was selected as the New Product of the Year by the America Filtration Society (AFS). The Product of the Year award is given to a company introducing the most significant new product in the previous year.
Freudenberg Performance Materials sees the role of nonwovens expanding in the automotive market due to the need of lightweight construction and sustainability.
“Sustainability is one of the main drivers for the strong growth of the automotive market,” says Dr. Frank Heislitz, CEO, Freudenberg Performance Materials. “Particularly important are recyclable, low VOC/FOG or VOC/FOG free and lightweight solutions. Nonwovens are excellently suited for solutions in these areas and offer a high performance at the same time.”
Freudenberg’s nonwovens for the automotive industry use a good share of recycled raw materials. For instance, Freudenberg´s spunlaid nonwovens based on Lutradur technology for automotive carpets, insert mats and interior and trunk linings contain up to 90% of recycled polyester. “Our unique multi-layer material for molded underbody panels and wheel liners are 100% recyclable and can be utilized in closed loop systems,” says Dr. Heislitz.
Freudenberg also claims its nonwovens for the automotive industry are lighter than conventional materials. They help save fuel and reduce CO2 emission. Freudenberg’s nonwovens based on Lutraflor technology can be used for automotive carpets, insert mats and interior and trunk linings. Compared to conventional automotive carpets, these nonwovens provide weight savings of up to 40%. Other offerings that offer weight savings include Freudenberg’s unique multi-layer material for molded underbody panels and wheel liners, Evolon microfilament textiles, acoustic pads and headliner facing materials, which are also used for trunk liners and seat backs.
In terms of aesthetics and resilience, Heislitz says that nonwovens have been steadily improving in quality, durability, visual appearance, and overall touch and feel. “Although printed nonwovens used to be mostly considered a price-effective alternative to knit materials, various technology advancements significantly increased the attractiveness of nonwovens compared to knit beyond pure price considerations,” he says.
Further developed printing technologies like Freudenberg’s new HLP 3.0 and embossing technology allow for new and unique designs which can only be realized using nonwoven base materials. “These advancements in technologies open new opportunities for OEMs to bring individualized design at competitive prices into their cars. Furthermore, the ability to use recycled PES fibers for Freudenberg’s facings materials allows to lower CO2-emissions and provide a sustainability angle to eco-conscious OEMs,” says Dr. Heislitz.