Karen McIntyre, editor04.12.16
What are nonwovens role in the composites market? The answer depends on the end use market. From automotives to roofing to adult incontinence, nonwovens are teaming up with a range of other products to offer flexibility, lower costs, lighter weights and many other benefits. The combination of nonwovens with other technologies or with other nonwovens continues to open up new doors to the industry. Here is a round up of recent developments of nonwovens in the composites market.
R3 Composites Turns to Nonwovens Production
Compression molder and compounder R3 Composites has established a nonwovens operation that will largely serve its own composites business, which supplies injected molded materials to the automotives market.
Carver Non-Woven Technologies will be headquartered in Fremont, IN, in a renovated plant where it will begin commercial production in July.
Calling the nonwovens process not proprietary but unique, president Mark Glidden said the new company will concentrate on five blends of materials. “Our ability to homogeneously blend different materials is what will set us apart,” he says. “We have been able to come up with a matrix of a natural fiber carbon system that offers lightweight and mechanical properties. The result is lower gsm materials that have two or three times mechanical properties at similar blends.”
This is the first time that R3 is using nonwovens in its composite structures. The company decided to manufacture its own product because it allows them to achieve the flexibility and lightweightedness necessary and to control the production process from start to finish.
Glidden also had some quality concerns with sourcing nonwovens externally. “There can be a weight difference between what you order and what you receive,” he says. “A plus or minus differential of 20% would be common in the industry. We are able to have a plus or minus 5% variance. That is very significant.”
Of course this upped the initial investment for Carver but Glidden thinks the ability to significantly decrease weights, increase mechanicals and have control of the fiber opening process from the get go justifies this multimillion investment.
“We think with our technology we can get people to look more to nonwovens and away from traditional things they have been using in the past,” he says. “We did this by maintaining quality of fiber all the way through the system. Understanding that nonwovens is essentially the entanglement of fibers, we want to make sure these fibers are entangled as closely together as possible.”
For door panels, a key application for the technology, this technology has allowed R3/Carver to make products as light as 600 gsm that are able to compete with earlier generation products that are as high as 1200 gsm.
“The general usage of nonwovens is a smart move economically,” says Gary Balthes, president of nonwovens consultancy Indyco. “Then, the flexibility with how you build the blends of fibers and layer them differently in the matrix adds to the benefits.”
Within automotives, the development of lighter weight, similarly performing products is crucial as new fuel economy standards dictate car design.
“There are only so many ways to adjust the air train to get mileage down. You have to move into aerodynamics and then weight,” says Glidden.
Elsewhere in the car, the R3/Carver technology can be applied to underbody aeroshielding. Other applications for the technology include building products and furniture.
Conwed Plastics Offers Netting Solutions
Conwed Plastics’ co-extruded netting allows its customers to design the most advanced, flexible and strong composites. Co-extrusion is a multi-layer extruded netting than can be subsequently oriented where different polymers can form different layers on the same netting configuration. It is a square netting construction and Conwed has the ability to build netting with A/B, A/B/A, and A/B/C layer combinations.
Conwed’s Thermanet Heat-Activated Reinforcement Netting brings together two or more substrates into a single, improved composite structure. Adhesive properties are actually built into the netting to bond and strengthen a diverse range of materials. This technology offers a wide range of product configurations, providing design versatility to match strict performance requirements and can be laminated with a variety of materials.
Conwed’s Rebound elastomeric netting is used in elastic nonwoven composites for waistbands and side panels in adult incontinence underwear and briefs. Depending on the final product application, manufacturers, converters, and laminators may produce composites with film, foam, paper, membrane, nonwoven, tissue and other fabrics used in various industrial and consumer applications. These composites can provide customized drapability, flexibility, elasticity and recovery based on the versatility of its elastomeric netting.
Chomarat and Norafin Develop Roofing Felt
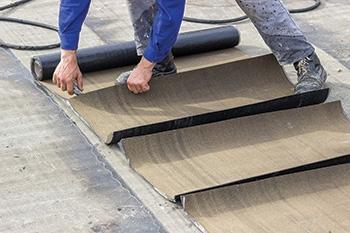
Nonwovens have merged with other materials to offer solutions to the roofing market.
Chomarat has launched a new generation of reinforcements for roofing felt—Rotaflam Neo, which was developed in collaboration with spunlace manufacturer Norafin. Billed as the only reinforcement on the market offering the benefits of both glass and polyester, Rotaflam Neo also combines the performances of laid scrim (strength and dimensional stability) and nonwoven materials (puncture, fire and tear resistance ) in a single layer.
Rotaflam Neo is made up of a fiberglass and/or polyester-based laid scrim, a nonwoven and a glass veil. The nonwoven is made through hydroentanglement, which guarantees the performances of the laid scrim. Using a laid scrim that combines glass and polyester offers two benefits—thanks to its intrinsic properties, the glass adds stability on the roof but also on the membrane production lines, while the polyester brings elongation and strength.
By combining their know-how, the two companies can offer a reinforcement that rises to the challenges of the waterproofing market, offering improved performance while reducing the thickness of the membranes. The reduced weight of the bitumen significantly cuts the production costs of the membranes. Moreover, the membranes produced with Rotaflam Neo pass all the European fire resistance tests (BROOF T1,T2, T3). Rotaflam Neo improves the fire resistance of the waterproofing membrane and does away with the need to include certain chemical additives in the formulation, which also reduces the environmental impact of this solution.
Johns Manville Composites Business Targets Many Applications
Johns Manville’s composite panels using its own nonwovens can optimize performance, mass and value. At the outer layer, a surfacing veils provide a smooth finish that can also be painted for protection from the elements, and thicker, nonwoven glass mats can be applied as sub-surface layers that cover honeycomb cores. Polyester spunbond or glass fiber nonwoven materials can also be used as a compressed core to increase mechanical properties with minimal weight.
The company reports that the global demand for composite structures is growing rapidly. JM has applied this technology to windmill blades, automotive headliners, lightweight body panels, forming parts and structural elements, panel boards for trucks and trailers, honeycomb acoustic panels in office spaces and ship and railroad building.
Mogul Nonwovens
Turkey-based Mogul Nonwovens offers a number of composite materials for a range of industries. Its PEVA film, available in widths of 160 cm, is available in combination with its nonwoven fabrics and can be used in many applications ranging from dust covers and shower curtains to garment bags and medical products.
Meanwhile its coated and medical fabrics allow the company to make hydrophilic water repellent stiffened and fire-resistant grades. Its PP/PE extrusion coated and laminated fabrics are marketed under the Integrale brand name and the technology ranges include a spunbond/meltblown, sandwich coated and backside coated and combinations with plastics, net raffia and woven materials.
Finally, Mogul’s Allucoat range fabrics are a metallized form of nonwoven fabrics. Mogul offers PP and PET spunbond and SMS fabrics in this range. Applications are packaging, building industry, agriculture, insulation. Allucoat fabrics have light reflective properties, and 270 cm max width for metallized fabrics in a wide range of grammages are available.
R3 Composites Turns to Nonwovens Production
Compression molder and compounder R3 Composites has established a nonwovens operation that will largely serve its own composites business, which supplies injected molded materials to the automotives market.
Carver Non-Woven Technologies will be headquartered in Fremont, IN, in a renovated plant where it will begin commercial production in July.
Calling the nonwovens process not proprietary but unique, president Mark Glidden said the new company will concentrate on five blends of materials. “Our ability to homogeneously blend different materials is what will set us apart,” he says. “We have been able to come up with a matrix of a natural fiber carbon system that offers lightweight and mechanical properties. The result is lower gsm materials that have two or three times mechanical properties at similar blends.”
This is the first time that R3 is using nonwovens in its composite structures. The company decided to manufacture its own product because it allows them to achieve the flexibility and lightweightedness necessary and to control the production process from start to finish.
Glidden also had some quality concerns with sourcing nonwovens externally. “There can be a weight difference between what you order and what you receive,” he says. “A plus or minus differential of 20% would be common in the industry. We are able to have a plus or minus 5% variance. That is very significant.”
Of course this upped the initial investment for Carver but Glidden thinks the ability to significantly decrease weights, increase mechanicals and have control of the fiber opening process from the get go justifies this multimillion investment.
“We think with our technology we can get people to look more to nonwovens and away from traditional things they have been using in the past,” he says. “We did this by maintaining quality of fiber all the way through the system. Understanding that nonwovens is essentially the entanglement of fibers, we want to make sure these fibers are entangled as closely together as possible.”
For door panels, a key application for the technology, this technology has allowed R3/Carver to make products as light as 600 gsm that are able to compete with earlier generation products that are as high as 1200 gsm.
“The general usage of nonwovens is a smart move economically,” says Gary Balthes, president of nonwovens consultancy Indyco. “Then, the flexibility with how you build the blends of fibers and layer them differently in the matrix adds to the benefits.”
Within automotives, the development of lighter weight, similarly performing products is crucial as new fuel economy standards dictate car design.
“There are only so many ways to adjust the air train to get mileage down. You have to move into aerodynamics and then weight,” says Glidden.
Elsewhere in the car, the R3/Carver technology can be applied to underbody aeroshielding. Other applications for the technology include building products and furniture.
Conwed Plastics Offers Netting Solutions
Conwed Plastics’ co-extruded netting allows its customers to design the most advanced, flexible and strong composites. Co-extrusion is a multi-layer extruded netting than can be subsequently oriented where different polymers can form different layers on the same netting configuration. It is a square netting construction and Conwed has the ability to build netting with A/B, A/B/A, and A/B/C layer combinations.
Conwed’s Thermanet Heat-Activated Reinforcement Netting brings together two or more substrates into a single, improved composite structure. Adhesive properties are actually built into the netting to bond and strengthen a diverse range of materials. This technology offers a wide range of product configurations, providing design versatility to match strict performance requirements and can be laminated with a variety of materials.
Conwed’s Rebound elastomeric netting is used in elastic nonwoven composites for waistbands and side panels in adult incontinence underwear and briefs. Depending on the final product application, manufacturers, converters, and laminators may produce composites with film, foam, paper, membrane, nonwoven, tissue and other fabrics used in various industrial and consumer applications. These composites can provide customized drapability, flexibility, elasticity and recovery based on the versatility of its elastomeric netting.
Chomarat and Norafin Develop Roofing Felt
Nonwovens have merged with other materials to offer solutions to the roofing market.
Rotaflam Neo is made up of a fiberglass and/or polyester-based laid scrim, a nonwoven and a glass veil. The nonwoven is made through hydroentanglement, which guarantees the performances of the laid scrim. Using a laid scrim that combines glass and polyester offers two benefits—thanks to its intrinsic properties, the glass adds stability on the roof but also on the membrane production lines, while the polyester brings elongation and strength.
By combining their know-how, the two companies can offer a reinforcement that rises to the challenges of the waterproofing market, offering improved performance while reducing the thickness of the membranes. The reduced weight of the bitumen significantly cuts the production costs of the membranes. Moreover, the membranes produced with Rotaflam Neo pass all the European fire resistance tests (BROOF T1,T2, T3). Rotaflam Neo improves the fire resistance of the waterproofing membrane and does away with the need to include certain chemical additives in the formulation, which also reduces the environmental impact of this solution.
Johns Manville Composites Business Targets Many Applications
Johns Manville’s composite panels using its own nonwovens can optimize performance, mass and value. At the outer layer, a surfacing veils provide a smooth finish that can also be painted for protection from the elements, and thicker, nonwoven glass mats can be applied as sub-surface layers that cover honeycomb cores. Polyester spunbond or glass fiber nonwoven materials can also be used as a compressed core to increase mechanical properties with minimal weight.
The company reports that the global demand for composite structures is growing rapidly. JM has applied this technology to windmill blades, automotive headliners, lightweight body panels, forming parts and structural elements, panel boards for trucks and trailers, honeycomb acoustic panels in office spaces and ship and railroad building.
Mogul Nonwovens
Turkey-based Mogul Nonwovens offers a number of composite materials for a range of industries. Its PEVA film, available in widths of 160 cm, is available in combination with its nonwoven fabrics and can be used in many applications ranging from dust covers and shower curtains to garment bags and medical products.
Meanwhile its coated and medical fabrics allow the company to make hydrophilic water repellent stiffened and fire-resistant grades. Its PP/PE extrusion coated and laminated fabrics are marketed under the Integrale brand name and the technology ranges include a spunbond/meltblown, sandwich coated and backside coated and combinations with plastics, net raffia and woven materials.
Finally, Mogul’s Allucoat range fabrics are a metallized form of nonwoven fabrics. Mogul offers PP and PET spunbond and SMS fabrics in this range. Applications are packaging, building industry, agriculture, insulation. Allucoat fabrics have light reflective properties, and 270 cm max width for metallized fabrics in a wide range of grammages are available.