Karen McIntyre, editor02.02.16
Spunmelt capacity investment has not slowed. As recently as last month, new lines have been announced and currently there are at least 13 new lines, many of which will add nearly 20,000 tons of capacity, either starting up or under construction around the globe. This investment is truly global—spanning five continents—and shows that demand for spunmelt nonwovens continues to grow, driven largely by two factors, market growth and technological improvements.
“All of the investments are not surprising,” says industry consultant David Price. “They are being driven by strategic investments and some modernization. Depending on the region, the new lines are responding to growth in hygiene or they are replacing older lines.”
In May 2015, Price authored a report on the global spunbond/spunmelt market. He found that between 2009 and 2014, 47 high output production lines were added, totaling 750,000 tons of nameplate capacity. By 2019, at least another 330,000 tons of capacity will be installed, meeting demand in emerging and developed markets and increasing the availability of high-strength, lightweight nonwovens.
According to Price, hygiene demand continues to dominate consumption in this technology segment and in developing markets new customers are driving growth, while in developed regions manufacturers are adding new lines to increase the sophistication of their products and make them more cost effective.
Scott Tracey, president, health, hygiene & specialty at Berry Plastics, the company that purchased Avintiv, the world’s largest producer of nonwovens late last year, says, “Article designs and new applications are continually evolving toward the use of more nonwovens. In our opinion, this new capacity will capture this penetration with some disruption to the incumbent markets from oversupply on a temporary basis.”
While hygiene is considered a recession-proof business, economic factors have some effect. In developing regions, economic woes can limit new customer entry into the market while in more sophisticated regions they can force consumers to trade down to less premium products.
“Macro-economic conditions are weakening around the world, which in some regions is dampening the demand for spunmelt nonwovens,” says Raymond Dunleavy, director of sales and marketing for spunmelt maker Fitesa. “In some regions manufacturers have brought too much capacity onstream resulting in oversupply and depressed pricing. Additionally, in some regions spunmelt is being replaced by other ‘old technology’ fabrics that offer different physical characteristics. Fitesa’s success in the hygiene spunmelt market is a result of staying close to our customers, launching innovative fabrics to help them achieve competitive advantage and investing in modern state-of-the-art technology close to them to meet their needs.”
Earlier this year spunmelt machinery supplier Reicofil introduced a new option for nonwovens manufacturers looking to enter the spunmelt arena at a lower entry point than traditionally required with their machine. The German company’s latest technology, known as the S-TwinMB-S 2600 RF4s Compact Bico is available has a lower annual production capacity, and presumably a lower investment level, than other Reicofil lines, which typically produce 15,000-20,000 tons per year or more. This new option will pave the way for investment in developing countries that could possibly not handle the output or the investment associated with larger line.
Czech Republic-based Pegas Nonwovens chose this option for its second Egyptian line. In September that company said it would add the smaller line, a move that will allow it to use its existing infrastructure in Egypt and gradually increase its capacity to meet the needs of the market.
“The investment into this new production line represents another significant milestone in our company’s history,” says František Rezác, CEO and member of the board of Pegas Nonwovens. “It is an entirely new platform, the first of its kind in the nonwoven textile industry. We are thus fulfilling our long-term strategy based on installing state-of-the-art technology that enables the production of advanced products and confirm our position as one of the technological leaders in the segment of nonwoven textiles used in the production of disposable hygiene products.
“For further development of the company it is no less important that, together with the secured long term financing, we consider this type of production line, with its lower overall investment costs, lower demands on infrastructure and lower capacity to be an expansion technology platform which is suitable for penetration into new, especially developing markets,” he adds.
Everyone’s Game
Within the spunmelt category, perhaps no one has been as aggressive these past couple of years as Fitesa. The Brazilian-based nonwovens producer has announced a number of large-scale lines since acquiring the hygiene-related assets of Fiberweb in 2012, and its global capacity is now among the highest in the world.
With plants already in operation in Brazil, Peru, North Carolina, Washington, Italy, Spain, Germany and Sweden, Fitesa has announced plans to add new lines throughout the Americas and Europe.
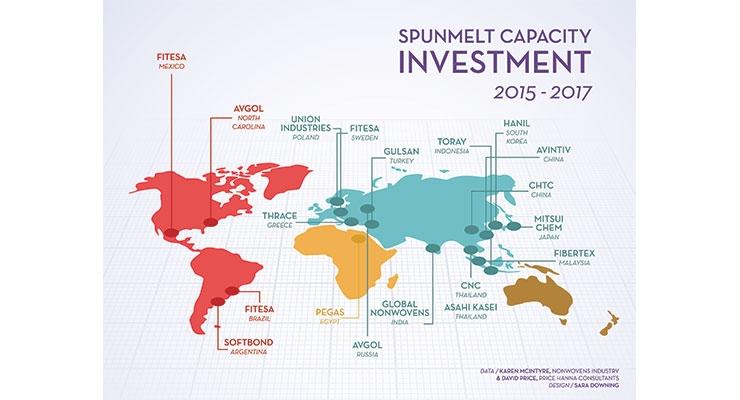
Fitesa’s most recent line announcement was made in December when the company confirmed rumors that it would add a 20,000 metric ton spunmelt line in Peine, Germany. The new line, which should begin operation in early 2017 and is part of a plan to help the company support its customers’ growth prospects in the hygiene market, executives said at the time of this announcement.
The German line was the first announcement related to a $160 million investment program announced in August 2015. This program will meet the needs of spunmelt customers in Europe, the U.S. and South America. Fitesa has not yet announced the locations for the other lines.
In 2014, Fitesa announced it would add a new line at its plant in San Jose Iturbide, Mexico. This new line, which should be complete late this year, will also be able to make 20,000 metric tons and largely serve the global hygiene markets. “The Mexican market is very integrated with the U.S. and will enable us to localize production of spunbond/spunmelt and establish a solid platform for exports,” says Dunleavy.
Meanwhile in its home country of Brazil, Fitesa announced in October 2014 that it would build a 20,000-ton line at a new site in Sao Paulo, Brazil. The new line will meet the growing demand from hygiene manufacturers in South America. “In South America, the penetration of hygiene products is still increasing, despite the recent macroeconomic challenges in the region. Our customers install new converting equipment to meet those needs and we support them with capacity expansions,” Dunleavy adds.
Brazil’s demand for spunbond/spunmelt accounts for more than 50% of total South American usage. Fitesa also operates a one-line plant in Peru, which was recently upgraded to make 5000 tons additional capacity.
One area where Fitesa has not yet entered the spunmelt race is Asia, although it does operate two airlaid lines and a thermal bonded line in China. Dunleavy says that Fitesa does continue to monitor this growing market. “However, capacity has been added at a faster rate to the extent that supply exceeds demand at this time and it will likely take a couple of years for supply and demand to become more balanced,” he says. “We remain alert to opportunities and are ready to enter when the right one arises for Fitesa to serve customers in the region.”
Asian Advances
While Fitesa has kept out of Asia, many nonwovens manufacturers have been successful in the region. Leading this charge is Fibertex Personal Care. In January, the Danish company said it would invest nearly $60 million in a new line in Malaysia. The investment, which is the company’s fifth line in the country, will increase its Asian capacity by more than 20% when it comes onstream in mid-2017.
Fibertex Personal Care was one of the first global manufacturers to establish a site in Asia in 2002 and the company continues to benefit from this role. Today, the company is among the three largest suppliers to the region and the largest non-Japanese supplier to Japan, according Mikael Staal Axelsen, group CEO of Fibertex Personal Care.
Axelsen says there are clear signs that the timing of the investment in the Asian market is right. While the consumption of hygiene products in the West only shows a moderate increase of 1-2%, the picture looks quite different in Asia. A growing number of people in the Southeast Asian countries, China and India are earning an income that enables them to focus more on personal hygiene. This results in an Asian market growing about 10% each year.
“At the new site we will have even more focus on value-added products and the improvement of existing products,” Axelsen says. “The consumers and thereby the industry require hygiene products that are lighter, softer and with finer structures, and we have reached an advanced stage in the processing improvement race which becomes more and more predominant in our business.”
Fibertex also makes about 50,000 tons of spunmelt capacity at its Denmark site. Its total output represents about 10% of the global spunmelt capacity.
Another spunmelt manufacturer with an ambitious Asian expansion plans is Toray Advanced Materials. The Korean manufacturer
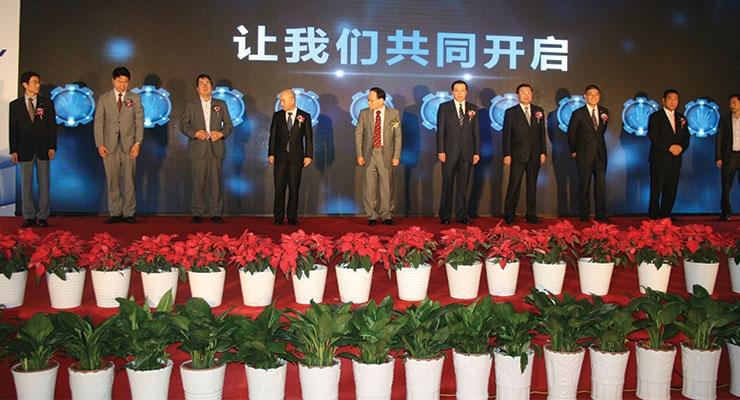
Toray recently completed work on its fourth Chinese spunmelt line.
recently completed its fourth Chinese line and is adding a second line in Indonesia. The fourth line in China, which is located at a facility in Nantong, made Toray’s operation there the largest nonwovens producer in Asia, according to the company, capable of making 77,000 tons of nonwovens per year.
Toray established the Chinese subsidiary in 2006 and added the second and third lines to it in 2010 and 2012. Meanwhile, its Indonesian site was established in 2012.
All of this investment is supporting growth in the Asian baby market. According to information supplied by Toray, demand for disposable baby diapers is forecast to rapidly grow from 14 billion pieces in 2012 to 38 billion pieces a year in 2020 in China due to improvements in people’s lifestyles. These improvements will influence major hygiene product manufacturers to expand their existing production facilities and leading medium-sized manufacturers to enter the market. Toray has been aggressively investing in China in response to strong demand for polypropylene spunbond in China as well as the requirements for high-performance materials for disposable diapers and to strengthen the cost competitiveness of its operation.
With the second Indonesian line, Toray’s capacity in Asia will surpass 150,000 tons and help it grow in the Southeast Asian (ASEAN) region.
“The ASEAN region is one of our most important and strategic markets, and Indonesia is the biggest market in ASEAN countries,” says export manager Evan Lee. “The Philippines, Malaysia and Vietnam market is the our next target market in ASEAN except for Indonesia.”
Lee has indicated that a third site will be imminent elsewhere in Asia but the company has yet to announce firm plans.
With the Asian market for polypropylene spunbond nonwovens expected to increase from 660,000 tons in 2016 to 936,000 tons in 2020—due to both explosive baby diaper needs in emerging ASEAN countries and adult diaper needs in Korea—the hygiene market is a good one to be in and much of Toray’s output in this region targets these markets.
“The Asian hygiene market is a good market in nonwovens with strong and stable growth, but many nonwovens companies focus on supplying their products to major diaper companies to aggressively expand their capacity, therefore sales are growing but the profits not so much,” Lee says. “We have a long-term investment plan in Asia and we are considering our next investment consistent with this.”
Elsewhere in Asia, Japanese producers have invested aggressively in Southeast Asia. Mitsui Chemicals and Asahi Kasei both have hygiene operations in Thailand, while local producers like CNC International has added a line in Thailand and Global Nonwovens has added the first large-scale spunmelt line in India.
Europe’s Hot Spot
Probably the most concentrated area of investment, Europe has a number of new lines including Fitesa’s new lines in Sweden and Germany, under construction. Union Industries, an Italian company, chose to make its foreign investment in Poland. The new line, which came onstream in late 2015, is a 3.2-meter-wide Reicofil 4 SSMS line that added 15,000 tons of capacity to Union’s total output. The new line should help Union growth in North, Central and Eastern Europe in the coming years. President Matteo Moltrasio says the company will evaluate the possibility of expanding outside Europe as the Polish line comes onstream.
Gulsan recently completed work on a new 20,000-ton spunmelt line in Turkey to support future growth and provide it with state-of-the-art technology. The line, a 4.2-meter six beam Reicofil 4+ nonwoven line, which began ramping up in December, will serve the hygiene and medical markets.
The new line brings Gulsan’s, which is based in Gaziantep, Turkey, global capacity to 105,000 tons. It most recently added a 20,000-ton line near Cairo, Egypt, its first foreign investment, which came onstream in October 2014.
Executives say the new investment decision for Turkey will to support Gulsan’s future growth in the industry and in the region with highly sophisticated and up-to-date production technologies to its business partners and reinforces the company’s position as one of the leading manufacturers of spunmelt materials in the EMEA (Europe, Middle East and Africa) region.
Meanwhile, Berry/Avintiv is adding significantly to its European operation. In Tarragona, Spain, Avintiv, which was purchased by Berry Plastics late last year, added two meltblown lines to convert a three-beam spunbond line to a five-beam spunmelt line. This investment added to the site’s output by 50% or 15,000 metric tons and responded to the evolving market demand for spunmelt nonwovens in personal care products across Europe, the Middle East and Africa.
Last year, Berry/Avintiv improved its profile in Northern Europe through the acquisition of Dounor in March 2015. Based in Neuville en Ferrain, France, Dounor operates six spunbond/spunmelt lines at one site, where it makes 40,000 tons of nonwovens per year.
Situated near major European ports, Dounor serves all of Europe, where 85% of its business is done, as well as customers in the Middle East and North Africa, where the remaining 15% of sales are conducted, according to the company. Its sales were estimated at about $100 million per year.
“The Dounor acquisition significantly improved our footprint in Europe,” says Tracey. “We are well-located to service customers throughout southern Europe from our state-of-the-art plant in Tarragona, Spain. At the same time our Neuville-en-Ferrain, France location and assets are well-aligned with the needs of our customers in North and Central Europe.”
These many sites—as well as its recent alliance with a major films supplier—gives Berry the ability to offer a wide range of solutions to its customers. “From a technology perspective, Berry Plastics brings a unique portfolio of products for specialty materials now including landing zone applications that have been highly sought-after by our customers worldwide,” Tracey adds.
Outside of Asia and Europe, Berry/Avintiv also has a strong South American presence with lines in Argentina, Colombia and Brazil, which were acquired from Companhia Providencia two years ago, and a significant North American operation with sites in North Carolina, Virginia and Mexico.
“The company is aligned with customers’ needs and well-positioned to support growth globally,” Tracey says. “Our business is balanced across our four regions with approximately 51% in North America, 16% in South America, 10% in Asia, and 23% in Europe, Middle East and India. All regions of the world continuously assess the areas for expansion where we can bring the most value to our customers.”
Speaking of customers, Tracey cites softness, high performance and fit to be the major trends in the hygiene space, and these trends have been approached by different customers in different ways. “We are fortunate to have an extremely talented group of scientists who work very closely with our customers to create unique combinations of resins, fibers, calenders, dies, finishing and processes specifically engineered to suit our customers’ varying needs.”
“All of the investments are not surprising,” says industry consultant David Price. “They are being driven by strategic investments and some modernization. Depending on the region, the new lines are responding to growth in hygiene or they are replacing older lines.”
In May 2015, Price authored a report on the global spunbond/spunmelt market. He found that between 2009 and 2014, 47 high output production lines were added, totaling 750,000 tons of nameplate capacity. By 2019, at least another 330,000 tons of capacity will be installed, meeting demand in emerging and developed markets and increasing the availability of high-strength, lightweight nonwovens.
According to Price, hygiene demand continues to dominate consumption in this technology segment and in developing markets new customers are driving growth, while in developed regions manufacturers are adding new lines to increase the sophistication of their products and make them more cost effective.
Scott Tracey, president, health, hygiene & specialty at Berry Plastics, the company that purchased Avintiv, the world’s largest producer of nonwovens late last year, says, “Article designs and new applications are continually evolving toward the use of more nonwovens. In our opinion, this new capacity will capture this penetration with some disruption to the incumbent markets from oversupply on a temporary basis.”
While hygiene is considered a recession-proof business, economic factors have some effect. In developing regions, economic woes can limit new customer entry into the market while in more sophisticated regions they can force consumers to trade down to less premium products.
“Macro-economic conditions are weakening around the world, which in some regions is dampening the demand for spunmelt nonwovens,” says Raymond Dunleavy, director of sales and marketing for spunmelt maker Fitesa. “In some regions manufacturers have brought too much capacity onstream resulting in oversupply and depressed pricing. Additionally, in some regions spunmelt is being replaced by other ‘old technology’ fabrics that offer different physical characteristics. Fitesa’s success in the hygiene spunmelt market is a result of staying close to our customers, launching innovative fabrics to help them achieve competitive advantage and investing in modern state-of-the-art technology close to them to meet their needs.”
Earlier this year spunmelt machinery supplier Reicofil introduced a new option for nonwovens manufacturers looking to enter the spunmelt arena at a lower entry point than traditionally required with their machine. The German company’s latest technology, known as the S-TwinMB-S 2600 RF4s Compact Bico is available has a lower annual production capacity, and presumably a lower investment level, than other Reicofil lines, which typically produce 15,000-20,000 tons per year or more. This new option will pave the way for investment in developing countries that could possibly not handle the output or the investment associated with larger line.
Czech Republic-based Pegas Nonwovens chose this option for its second Egyptian line. In September that company said it would add the smaller line, a move that will allow it to use its existing infrastructure in Egypt and gradually increase its capacity to meet the needs of the market.
“The investment into this new production line represents another significant milestone in our company’s history,” says František Rezác, CEO and member of the board of Pegas Nonwovens. “It is an entirely new platform, the first of its kind in the nonwoven textile industry. We are thus fulfilling our long-term strategy based on installing state-of-the-art technology that enables the production of advanced products and confirm our position as one of the technological leaders in the segment of nonwoven textiles used in the production of disposable hygiene products.
“For further development of the company it is no less important that, together with the secured long term financing, we consider this type of production line, with its lower overall investment costs, lower demands on infrastructure and lower capacity to be an expansion technology platform which is suitable for penetration into new, especially developing markets,” he adds.
Everyone’s Game
Within the spunmelt category, perhaps no one has been as aggressive these past couple of years as Fitesa. The Brazilian-based nonwovens producer has announced a number of large-scale lines since acquiring the hygiene-related assets of Fiberweb in 2012, and its global capacity is now among the highest in the world.
With plants already in operation in Brazil, Peru, North Carolina, Washington, Italy, Spain, Germany and Sweden, Fitesa has announced plans to add new lines throughout the Americas and Europe.
The German line was the first announcement related to a $160 million investment program announced in August 2015. This program will meet the needs of spunmelt customers in Europe, the U.S. and South America. Fitesa has not yet announced the locations for the other lines.
In 2014, Fitesa announced it would add a new line at its plant in San Jose Iturbide, Mexico. This new line, which should be complete late this year, will also be able to make 20,000 metric tons and largely serve the global hygiene markets. “The Mexican market is very integrated with the U.S. and will enable us to localize production of spunbond/spunmelt and establish a solid platform for exports,” says Dunleavy.
Meanwhile in its home country of Brazil, Fitesa announced in October 2014 that it would build a 20,000-ton line at a new site in Sao Paulo, Brazil. The new line will meet the growing demand from hygiene manufacturers in South America. “In South America, the penetration of hygiene products is still increasing, despite the recent macroeconomic challenges in the region. Our customers install new converting equipment to meet those needs and we support them with capacity expansions,” Dunleavy adds.
Brazil’s demand for spunbond/spunmelt accounts for more than 50% of total South American usage. Fitesa also operates a one-line plant in Peru, which was recently upgraded to make 5000 tons additional capacity.
One area where Fitesa has not yet entered the spunmelt race is Asia, although it does operate two airlaid lines and a thermal bonded line in China. Dunleavy says that Fitesa does continue to monitor this growing market. “However, capacity has been added at a faster rate to the extent that supply exceeds demand at this time and it will likely take a couple of years for supply and demand to become more balanced,” he says. “We remain alert to opportunities and are ready to enter when the right one arises for Fitesa to serve customers in the region.”
Asian Advances
While Fitesa has kept out of Asia, many nonwovens manufacturers have been successful in the region. Leading this charge is Fibertex Personal Care. In January, the Danish company said it would invest nearly $60 million in a new line in Malaysia. The investment, which is the company’s fifth line in the country, will increase its Asian capacity by more than 20% when it comes onstream in mid-2017.
Fibertex Personal Care was one of the first global manufacturers to establish a site in Asia in 2002 and the company continues to benefit from this role. Today, the company is among the three largest suppliers to the region and the largest non-Japanese supplier to Japan, according Mikael Staal Axelsen, group CEO of Fibertex Personal Care.
Axelsen says there are clear signs that the timing of the investment in the Asian market is right. While the consumption of hygiene products in the West only shows a moderate increase of 1-2%, the picture looks quite different in Asia. A growing number of people in the Southeast Asian countries, China and India are earning an income that enables them to focus more on personal hygiene. This results in an Asian market growing about 10% each year.
“At the new site we will have even more focus on value-added products and the improvement of existing products,” Axelsen says. “The consumers and thereby the industry require hygiene products that are lighter, softer and with finer structures, and we have reached an advanced stage in the processing improvement race which becomes more and more predominant in our business.”
Fibertex also makes about 50,000 tons of spunmelt capacity at its Denmark site. Its total output represents about 10% of the global spunmelt capacity.
Another spunmelt manufacturer with an ambitious Asian expansion plans is Toray Advanced Materials. The Korean manufacturer
Toray recently completed work on its fourth Chinese spunmelt line.
Toray established the Chinese subsidiary in 2006 and added the second and third lines to it in 2010 and 2012. Meanwhile, its Indonesian site was established in 2012.
All of this investment is supporting growth in the Asian baby market. According to information supplied by Toray, demand for disposable baby diapers is forecast to rapidly grow from 14 billion pieces in 2012 to 38 billion pieces a year in 2020 in China due to improvements in people’s lifestyles. These improvements will influence major hygiene product manufacturers to expand their existing production facilities and leading medium-sized manufacturers to enter the market. Toray has been aggressively investing in China in response to strong demand for polypropylene spunbond in China as well as the requirements for high-performance materials for disposable diapers and to strengthen the cost competitiveness of its operation.
With the second Indonesian line, Toray’s capacity in Asia will surpass 150,000 tons and help it grow in the Southeast Asian (ASEAN) region.
“The ASEAN region is one of our most important and strategic markets, and Indonesia is the biggest market in ASEAN countries,” says export manager Evan Lee. “The Philippines, Malaysia and Vietnam market is the our next target market in ASEAN except for Indonesia.”
Lee has indicated that a third site will be imminent elsewhere in Asia but the company has yet to announce firm plans.
With the Asian market for polypropylene spunbond nonwovens expected to increase from 660,000 tons in 2016 to 936,000 tons in 2020—due to both explosive baby diaper needs in emerging ASEAN countries and adult diaper needs in Korea—the hygiene market is a good one to be in and much of Toray’s output in this region targets these markets.
“The Asian hygiene market is a good market in nonwovens with strong and stable growth, but many nonwovens companies focus on supplying their products to major diaper companies to aggressively expand their capacity, therefore sales are growing but the profits not so much,” Lee says. “We have a long-term investment plan in Asia and we are considering our next investment consistent with this.”
Elsewhere in Asia, Japanese producers have invested aggressively in Southeast Asia. Mitsui Chemicals and Asahi Kasei both have hygiene operations in Thailand, while local producers like CNC International has added a line in Thailand and Global Nonwovens has added the first large-scale spunmelt line in India.
Europe’s Hot Spot
Probably the most concentrated area of investment, Europe has a number of new lines including Fitesa’s new lines in Sweden and Germany, under construction. Union Industries, an Italian company, chose to make its foreign investment in Poland. The new line, which came onstream in late 2015, is a 3.2-meter-wide Reicofil 4 SSMS line that added 15,000 tons of capacity to Union’s total output. The new line should help Union growth in North, Central and Eastern Europe in the coming years. President Matteo Moltrasio says the company will evaluate the possibility of expanding outside Europe as the Polish line comes onstream.
Gulsan recently completed work on a new 20,000-ton spunmelt line in Turkey to support future growth and provide it with state-of-the-art technology. The line, a 4.2-meter six beam Reicofil 4+ nonwoven line, which began ramping up in December, will serve the hygiene and medical markets.
The new line brings Gulsan’s, which is based in Gaziantep, Turkey, global capacity to 105,000 tons. It most recently added a 20,000-ton line near Cairo, Egypt, its first foreign investment, which came onstream in October 2014.
Executives say the new investment decision for Turkey will to support Gulsan’s future growth in the industry and in the region with highly sophisticated and up-to-date production technologies to its business partners and reinforces the company’s position as one of the leading manufacturers of spunmelt materials in the EMEA (Europe, Middle East and Africa) region.
Meanwhile, Berry/Avintiv is adding significantly to its European operation. In Tarragona, Spain, Avintiv, which was purchased by Berry Plastics late last year, added two meltblown lines to convert a three-beam spunbond line to a five-beam spunmelt line. This investment added to the site’s output by 50% or 15,000 metric tons and responded to the evolving market demand for spunmelt nonwovens in personal care products across Europe, the Middle East and Africa.
Last year, Berry/Avintiv improved its profile in Northern Europe through the acquisition of Dounor in March 2015. Based in Neuville en Ferrain, France, Dounor operates six spunbond/spunmelt lines at one site, where it makes 40,000 tons of nonwovens per year.
Situated near major European ports, Dounor serves all of Europe, where 85% of its business is done, as well as customers in the Middle East and North Africa, where the remaining 15% of sales are conducted, according to the company. Its sales were estimated at about $100 million per year.
“The Dounor acquisition significantly improved our footprint in Europe,” says Tracey. “We are well-located to service customers throughout southern Europe from our state-of-the-art plant in Tarragona, Spain. At the same time our Neuville-en-Ferrain, France location and assets are well-aligned with the needs of our customers in North and Central Europe.”
These many sites—as well as its recent alliance with a major films supplier—gives Berry the ability to offer a wide range of solutions to its customers. “From a technology perspective, Berry Plastics brings a unique portfolio of products for specialty materials now including landing zone applications that have been highly sought-after by our customers worldwide,” Tracey adds.
Outside of Asia and Europe, Berry/Avintiv also has a strong South American presence with lines in Argentina, Colombia and Brazil, which were acquired from Companhia Providencia two years ago, and a significant North American operation with sites in North Carolina, Virginia and Mexico.
“The company is aligned with customers’ needs and well-positioned to support growth globally,” Tracey says. “Our business is balanced across our four regions with approximately 51% in North America, 16% in South America, 10% in Asia, and 23% in Europe, Middle East and India. All regions of the world continuously assess the areas for expansion where we can bring the most value to our customers.”
Speaking of customers, Tracey cites softness, high performance and fit to be the major trends in the hygiene space, and these trends have been approached by different customers in different ways. “We are fortunate to have an extremely talented group of scientists who work very closely with our customers to create unique combinations of resins, fibers, calenders, dies, finishing and processes specifically engineered to suit our customers’ varying needs.”