Tara Olivo, associate editor10.13.15
Converting companies are an integral part of the nonwovens supply chain. For all of the advantages the industry’s products provide, a lot has to happen prior to their end use. Nonwovens need to be cut into a variety of shapes and sizes, scaled down to become a single-use product, as well as printed, packaged and more. Sometimes the process is simple, and sometimes more complex, with converting companies using the latest technology to add value to products and make them easier to use. The following is a compilation of capabilities and services of some the nonwovens industry’s leading converters.
Athea Packaging
Athea Packaging is a leader in specialty wipes and liquid contract packaging, offering an extensive variety of product formats to serve numerous end-user markets in the OEM and private label channels. Its manufacturing capabilities include custom wipe converting, custom formulation development, blending services, on-site chemists and formula-substrate compatibility testing, graphics, and technical and regulatory support.
www.athea.com
Beckmann Converting
Beckmann Converting continues to upgrade its high tech, ultrasonic laminating equipment, both in bonding capability and in web handling, to create wide web, multi-layer and multi-function composites.
Upgrades have allowed the company to process more efficiently, and to process more types of raw materials. Beckmann operates as a contract or toll laminator and is able to create, from two-layer composites to six-layer composites. It can create them as wide as 120 inches and slit in line, to any width a customer or its next step converter requires. These composites can be combinations of nonwovens, films, knits, wovens, or meshes.
Ultrasonic laminating has a unique place in the creation of multi-layer composites because nothing other than the original materials are used in that process. This makes it a true “green” process. As long as there is sufficient thermoplastic content in the layers to be laminated, the ultrasonic energy melts the materials at the bonding points, making it the bonding link of the individual layers, unlike adhesive bonding, which introduces foreign substances into the composites. Because ultrasonic lamination is a “point bonding process,” all of the properties of the raw material layers, in between the bond points, are the same as before lamination, which include properties such as strength, loft, breathability, filtration and chemical resistance. Beckmann has successfully produced multi-layer composites for applications such as filtration, environmental, protective apparel, protective covers, healthcare products, cleanroom wipes and many more.
www.beckmannconverting.com
Berk Wiper International
Boyertown, PA-based Berk Wiper manufactures nonwoven wipes, toilet tissue and paper towels on 16 production lines 24 hours per day. The company is an expert in converting an assortment of materials including DRC, spunlace, airlaid, hydroentangled nonwovens, meltblown, needlepunch, TAD, tissue and towel.
The Berk family has been in the wipes converting business since 1975 and has established a reputation of producing high quality products at reasonable prices. CEO Larry Berk and his brother Jeff Berk, who is president and head of sales, have run Berk Wiper since 2000.
The company’s most recent transformation was a name change from Berk Wiper Converting to Berk Wiper International, which Larry says better reflects the company’s international presence. The company also recently moved to the new Boyertown location, which gives it more space and better process flow.
Just over half of Berk’s business serves the nonwovens industry. A big portion of this business is in the medical washcloth field, but the company also converts wipes for every market including jan-san, food service, healthcare, automotive and industrial. Its capabilities include flat sheeting, interfolding, 1/2, 1/4, 1/6 and 1/8 folding, perforating, laminating and slitting.
Because Berk offers no minimum runs, this has allowed the company to work with some entrepreneurs on many interesting products. The latest of these is a product called Food Fresh liners, a patent-pending absorbent wipe that is placed in takeout containers to absorb moisture, keeping food fresh.
Berk says one of the best parts of being in the business is working with entrepreneurs on new ideas for wipes that solve his customers’ problems. He works closely with his R&D team on ways to improve the company’s offerings. The innovation of the nonwovens manufacturers has helped him immensely, he adds. “Almost every day we are seeing a new substrate, technology or a new way to package materials. I really have to hand it to these nonwoven producers.”
www.berkwiper.com
Connecticut Clean Room Corporation
Connecticut Clean Room Corporation (CCRC) is a master distributor, converter and manufacturer of products for the cleanroom industry and most recently expanded into the industrial market. Founded in 1979 in Bristol, CT, CCRC has grown from a mere 3500 square foot operation to over 40,000 square foot of office, manufacturing and warehouse space.
CCRC’s slitter/sheeter is located in a cleanroom that accommodates material with a web width of 48 inches. Cleanroom paper, Tyvek, vinyl sheets and several other materials are currently being cut at very close tolerances. This equipment has dual unwinds and weight capability of 2000 lb. per roll.
Two precision guillotines cut to tolerances of +/- .005 and can trim and cut stacks as small as 1.250 inches square to a maximum of 45 inches wide. A variety of materials are cut ranging from paper to cardstock, plastics and other customer provided materials.
CCRC has several slitter/rewinders than can accommodate multiple ID’s and ODs with rewinding on both plastic and corrugated cores. Additionally, it has proprietary equipment that allows for slitting a variety of nonwoven and specialty materials from 6-35 inches of multiple sheets from a maximum web width of 36 inches. All products are cut, trimmed and packaged in a clean environment.
CCRC’s auto punch has both round and oval capabilities along with a paper drill, corner rounder and spiral inserter for notebooks. It also maintains a 25-ton traveling head press that allows for die-cutting of various materials to customer specifications. CCRC’s automated bagger has print capabilities that allows for printing the customer’s name and product information on each bag. This equipment is also located in a clean environment.
CCRC’s ability to cut small runs for companies needing specialty converting with quick turnaround time is unmatched in the industry. CCRC fills the void for customers that don’t have large volume needs.
www.ctcleanroom.com
Converted Products
In 1993, Converted Products, Incorporated (CPI) opened for business with the simple idea of providing quality contract converting services in slitting and die cutting. Twenty years later, CPI has kept that same simple premise but has expanded its contract services to include wider width, high speed slitting, hot melt laminating, traverse (spool) winding, rotary and flat bed die cutting, warehousing/logistics and product/process development. Operating in an ISO9001 process, Converted Products’ 140,000 square foot facility is located on the northwest side of Milwaukee, WI.
CPI’s slitting capabilities include score, shear, razor, single knife and rotary, widths ranging from 1/8 to 136 inches and experience with a wide variety of flexible materials. In 2014, CPI upgraded its equipment by installing two new slitter/rewinders. President and founder of CPI, Chris Gorenc says, “We had the opportunity to keep our equipment on the leading edge by installing a high speed turret winder for our long running jobs and also installing a duplex winder that can handle nearly every type of material while improving our efficiencies and quality from our existing equipment.”
Also expanding in 2014 is CPI’s hot melt laminating capacity. While partnering with ITW Dynatec once again, CPI’s hot melt spray laminating capabilities include two or three ply, add-on levels from ½ gsm to 25 gsm, widths up to 112 inches, inline slitting and particulate dispensing. Gorenc says, “With the success we were seeing from the filtration and industrial market places for lower add-on applications, we realized the need to expand our hot melt laminating capacity and update our technology.”
Brought online in September 2013 was another slitter/spooler with a valuable slitting feature. The slitting station was designed to allow for bringing in wide parent rolls (up to 52 inches) and slitting/spooling accordingly. This feature allows the operator to pass back through any off cuts due to spool demand. This process saves time and money on pre slitting from the mill or at CPI.
“We saw this as a great opportunity to save our customers time and money,” says Gorenc. “That’s really why we are in business, to serve our customers by providing quality service, at a competitive price with innovative converting capabilities.”
www.convertedproducts.com
E&T Converters
E&T Converters was founded in 1972, with the goal to provide the best possible converting services at the most competitive price. Because it has so many years of experience in the converting business, its staff is able to offer a wide variety of slitting capabilities. This enables the company to provide contract converting for virtually any market. In 1989, E&T built a new 230,000 sq. foot state-of-the-art building with a rail site so that it could effectively manage the many needs of its customers. E&T is family owned and takes pride in its quality, service and value offered to all of its customers.
www.eandtconverters.com
JX Nippon
JX Nippon ANCI, Inc. the manufacturer of the original CLAF and Milife fabrics, exhibited at Pack Expo last month in Las Vegas.

Among the products that the company displayed are CLAF fabrics for produce packaging, Milife for luxury gift packaging and several composite fabrics for a range of applications. After years of successfully providing packaging fabrics designed to keep vegetables at their optimal level of freshness during packing and shipping, the engineers at JX Nippon have extended their focus into other packaging applications. Products designed for medical, pet care, automotive and construction applications are among those which the company had on display.
In addition, JX Nippon has two products being featured at this month’s IFAI Disaster and Mitigation Response display at IFAI in Anaheim, CA. The two products demonstrate some of the converting capabilities employed at JX Nippon and show novel end uses for the company’s products. One of the products is a unique lamination of CLAF and metalized film for use as an emergency blanket, and the other is an oil boom product which uses CLAF to speed the absorption of petro-chemicals at spill sites.
www.jxanci.com
Micrex Corporation
Micrex Corporation is the developer and manufacturer of the Micrex/Microcreper family of compressive treatment machinery for nonwovens, paper, films, composites and textiles. Companies worldwide use Micrex technology to add softness, bulk, drape, absorbency, extensibility, and stretch to a wide range of products.
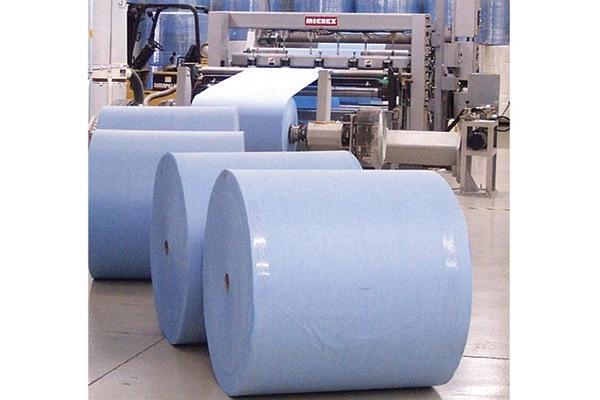
Micrex expands upon its capabilities by providing product development through the Micrex Innovation Lab. This integrates with contract Microcreping services for those firms whose current needs do not yet require the purchase of a dedicated Micrex/Microcreper system. Micrex is prepared to support projects from initial development through large-scale production. All nine configurations of Micrex/Microcreper are available for contract production.
www.micrex.com
National Wiper Alliance
National Wiper Alliance (NWA) is the largest operation in the U.S. focused on nonwoven dry wipes converting and private labeling. Operating out of its 500,000 square foot state-of-the-art facility located just outside Asheville, NC, NWA has over 30 converting lines offering slitting, inner folding, folding, sheeting, and perforating—both with core and coreless, as well as printing—with both inline and dedicated print lines. Additional in-house services offered include: product development, quality control department with product testing, warehousing, customer inventory management, and distribution and logistical support.
Products converted by NWA can be found in the retail, aerospace, automotive, industrial, food service, hospitality, medical, government, military, and janitorial markets.
NWA is proudly registered to ISO 9001:2008 standards.
www.nationalwiper.com
Nonwovens of America
Nonwovens of America, Inc. (NOA), is located in Swannanoa, NC, and operates a 5.4-meter air-lay needlepunch line and runs colors in a weight range of 3.5 ounces per square yard to 34 ounces per square yard. NOA just completed the installation of an inline calendar. In addition to the needlepunch line, NOA provides custom converting services which include a 10-color, 99” wide rotary screen print line, blanket lines, slitting and re-rolling. NOA offers toll converting services on the needlepunch line as well as all other converting service. The main areas of focus are automotive, retail, geotextile, industrial and emergency blankets. NOA provides in-house customer service, product development, warehousing, logistics and distribution support.
www.nonwovensofamerica.com
Rockline Industries
Rockline Industries is the biggest and most diverse turnkey contract manufacturer of wet wipes worldwide. It has been a family-owned and run business since its founding in 1976. After nearly 40 years of relentless innovation and effort, it is now a 2000-person global operation boasting the most comprehensive range of converting equipment in the business. The word “urgency” describes the sense with which it seeks to earn recognition by its customers as the unmatched leader in contract manufacturing. This urgency involves five basic imperatives — Renew (invest all earnings in continuous improvement), Respect (treat others as we want to be treated); Integrity (do the right thing); Teamwork (individual goals are secondary to team goals); and Excellence (best in class). Rockline fosters a culture of integrity, service and personal growth. The company delivers excellence in its products, process and services. It doesn’t compromise integrity for financial gain. Its partnerships are managed with the utmost respect.
Rockline embraces continuous change through product innovation and capital reinvestment and form a dedicated and passionate team from management on down. Its values are applied to all stakeholder relationships—from customers, associates, and suppliers on out to the communities at large whose needs it meets with uncompromising effort. It works every day to confirm just how much Rockline values each and every one of them. Rockline understands this is the only way to build and sustain the reputation it seeks within the industry. In the words of its CEO Randy Rudolph, “We won’t make a product we wouldn’t buy for ourselves. We aim for the sweet spot. Rockline is big enough to give our customers the resources and vision of a global company, yet we are small enough to value each and every customer.”
Integrity: Every Rockline associate is asked, “Do what you think is right – every day.” These simple words can make for tough choices, but Rockline says it will never stop trying to do the right thing. The company has a reputation in the wipes industry, for example, of uncompromising integrity with respect to maintaining strict confidentiality to protect and preserve intellectual property for the ongoing business security of its customers.
Innovation: At Rockline, its core strength is the quality and innovation of its product. The focus of its contract manufacturing group is to deliver excellence in customer service by supporting its customers with custom manufacturing and cutting-edge product and packaging while strengthening its speed to market. This is supported by a winning combination of technical leadership along with the most diverse manufacturing platforms in the wet wipes industry. It listens, innovates and collaborates with its valued customers to deliver customer specific solutions that leverage its expertise in material, manufacturing and innovation.
Sustainability (www.rocklineind.com/environmental-sustainability): Rockline is aggressively moving from fossil fuels toward clean, low carbon energy, designing waste and inefficiency out of its system, and embracing strategies like reuse, recycling, and energy recapture to reduce landfill use and waste water production. Rockline strives for Ecological Intelligence in its end products, using less material where it can, and sourcing natural and recycled materials wherever possible. It is Rockline’s commitment and passion to put its own reputation on the line every day, to measure and report its own progress so customers don’t have to. That’s what sustainability means to them.
Values: Rockline says its values define them. They reinforce to all of their stakeholders—customers, associates, suppliers and communities—just how much Rockline appreciates them. They allow Rockline to build a value-based business and reputation within the industry at large. Within the contract manufacturing sector, its values ensure that Rockline maintains a global recognition as the premier supplier in the industry, producing innovative solutions, ensuring mutually profitable partnerships and providing customers with important and trusted services that create lasting relationships.
www.rocklineind.com
U.S. Nonwovens Corp.
U.S. Nonwovens Corp. is a pharmaceutical-grade wet wipe contract manufacturer, exceeding FDA and EPA standards. The company offers cutting edge R&D, tech transfer, stability, validation, ramp-up, auto-production, quality control, quality assurance, micro, and training in state-of-the-art wind-powered facilities, managed by pharma industry professionals, covering every type of OTC, cosmetic, personal care, or home care wipe imaginable, in every wipe format. Customers include global CPG and pharmaceutical companies, to the world’s largest retailers.
www.usnonwovens.com
Web Industries
Web Industries continues to focus on adding capabilities and increasing capacity to offer consumer product and health care companies the ability to combine multiple converting and manufacturing steps and outsource them to a single location. Web’s latest acquisition is a high-speed, wide-width converting line that accepts and produces “Jumbo Rolls” of up to 60 inches OD x 80 inches width. These jumbo rolls support longer manufacturing runtimes and lower input and production costs.
“The ability to handle 60-inch OD rolls is an exciting addition to our existing large-format, high-speed slitting, spooling, and printing portfolio, and it offers our customers the ability to increase their operational efficiencies,” says James Oas, director of operations-consumer products market. “A 60-inch roll contains 57% more material in area than a 48-inch roll, and this increase can have a huge impact on client’s downstream manufacturing throughput.”
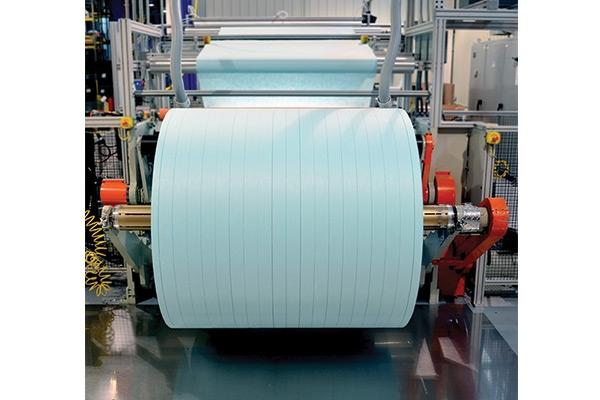
This equipment is located at Web’s Fort Wayne facility, which already houses some of the largest converting lines in the world. Web Fort Wayne also provides high-speed wide-web flexographic printing services, with tight dimensional pattern registration and precision inline slitting. The company’s printing assets can handle complex graphics while controlling image bleed-through on nonwovens as light as 10gms, giving customers the option of having their materials printed and slit and then spooled under one roof.
By combining contract converting, spooling, printing, and supply chain management services in a single location, Web Industries offers CPG and health care companies the speed-to-market and manufacturing efficiency advantages they need to be successful in the marketplace.
www.webindustries.com
Athea Packaging
Athea Packaging is a leader in specialty wipes and liquid contract packaging, offering an extensive variety of product formats to serve numerous end-user markets in the OEM and private label channels. Its manufacturing capabilities include custom wipe converting, custom formulation development, blending services, on-site chemists and formula-substrate compatibility testing, graphics, and technical and regulatory support.
www.athea.com
Beckmann Converting
Beckmann Converting continues to upgrade its high tech, ultrasonic laminating equipment, both in bonding capability and in web handling, to create wide web, multi-layer and multi-function composites.
Upgrades have allowed the company to process more efficiently, and to process more types of raw materials. Beckmann operates as a contract or toll laminator and is able to create, from two-layer composites to six-layer composites. It can create them as wide as 120 inches and slit in line, to any width a customer or its next step converter requires. These composites can be combinations of nonwovens, films, knits, wovens, or meshes.
Ultrasonic laminating has a unique place in the creation of multi-layer composites because nothing other than the original materials are used in that process. This makes it a true “green” process. As long as there is sufficient thermoplastic content in the layers to be laminated, the ultrasonic energy melts the materials at the bonding points, making it the bonding link of the individual layers, unlike adhesive bonding, which introduces foreign substances into the composites. Because ultrasonic lamination is a “point bonding process,” all of the properties of the raw material layers, in between the bond points, are the same as before lamination, which include properties such as strength, loft, breathability, filtration and chemical resistance. Beckmann has successfully produced multi-layer composites for applications such as filtration, environmental, protective apparel, protective covers, healthcare products, cleanroom wipes and many more.
www.beckmannconverting.com
Berk Wiper International
Boyertown, PA-based Berk Wiper manufactures nonwoven wipes, toilet tissue and paper towels on 16 production lines 24 hours per day. The company is an expert in converting an assortment of materials including DRC, spunlace, airlaid, hydroentangled nonwovens, meltblown, needlepunch, TAD, tissue and towel.
The Berk family has been in the wipes converting business since 1975 and has established a reputation of producing high quality products at reasonable prices. CEO Larry Berk and his brother Jeff Berk, who is president and head of sales, have run Berk Wiper since 2000.
The company’s most recent transformation was a name change from Berk Wiper Converting to Berk Wiper International, which Larry says better reflects the company’s international presence. The company also recently moved to the new Boyertown location, which gives it more space and better process flow.
Just over half of Berk’s business serves the nonwovens industry. A big portion of this business is in the medical washcloth field, but the company also converts wipes for every market including jan-san, food service, healthcare, automotive and industrial. Its capabilities include flat sheeting, interfolding, 1/2, 1/4, 1/6 and 1/8 folding, perforating, laminating and slitting.
Because Berk offers no minimum runs, this has allowed the company to work with some entrepreneurs on many interesting products. The latest of these is a product called Food Fresh liners, a patent-pending absorbent wipe that is placed in takeout containers to absorb moisture, keeping food fresh.
Berk says one of the best parts of being in the business is working with entrepreneurs on new ideas for wipes that solve his customers’ problems. He works closely with his R&D team on ways to improve the company’s offerings. The innovation of the nonwovens manufacturers has helped him immensely, he adds. “Almost every day we are seeing a new substrate, technology or a new way to package materials. I really have to hand it to these nonwoven producers.”
www.berkwiper.com
Connecticut Clean Room Corporation
Connecticut Clean Room Corporation (CCRC) is a master distributor, converter and manufacturer of products for the cleanroom industry and most recently expanded into the industrial market. Founded in 1979 in Bristol, CT, CCRC has grown from a mere 3500 square foot operation to over 40,000 square foot of office, manufacturing and warehouse space.
CCRC’s slitter/sheeter is located in a cleanroom that accommodates material with a web width of 48 inches. Cleanroom paper, Tyvek, vinyl sheets and several other materials are currently being cut at very close tolerances. This equipment has dual unwinds and weight capability of 2000 lb. per roll.
Two precision guillotines cut to tolerances of +/- .005 and can trim and cut stacks as small as 1.250 inches square to a maximum of 45 inches wide. A variety of materials are cut ranging from paper to cardstock, plastics and other customer provided materials.
CCRC has several slitter/rewinders than can accommodate multiple ID’s and ODs with rewinding on both plastic and corrugated cores. Additionally, it has proprietary equipment that allows for slitting a variety of nonwoven and specialty materials from 6-35 inches of multiple sheets from a maximum web width of 36 inches. All products are cut, trimmed and packaged in a clean environment.
CCRC’s auto punch has both round and oval capabilities along with a paper drill, corner rounder and spiral inserter for notebooks. It also maintains a 25-ton traveling head press that allows for die-cutting of various materials to customer specifications. CCRC’s automated bagger has print capabilities that allows for printing the customer’s name and product information on each bag. This equipment is also located in a clean environment.
CCRC’s ability to cut small runs for companies needing specialty converting with quick turnaround time is unmatched in the industry. CCRC fills the void for customers that don’t have large volume needs.
www.ctcleanroom.com
Converted Products
In 1993, Converted Products, Incorporated (CPI) opened for business with the simple idea of providing quality contract converting services in slitting and die cutting. Twenty years later, CPI has kept that same simple premise but has expanded its contract services to include wider width, high speed slitting, hot melt laminating, traverse (spool) winding, rotary and flat bed die cutting, warehousing/logistics and product/process development. Operating in an ISO9001 process, Converted Products’ 140,000 square foot facility is located on the northwest side of Milwaukee, WI.
CPI’s slitting capabilities include score, shear, razor, single knife and rotary, widths ranging from 1/8 to 136 inches and experience with a wide variety of flexible materials. In 2014, CPI upgraded its equipment by installing two new slitter/rewinders. President and founder of CPI, Chris Gorenc says, “We had the opportunity to keep our equipment on the leading edge by installing a high speed turret winder for our long running jobs and also installing a duplex winder that can handle nearly every type of material while improving our efficiencies and quality from our existing equipment.”
Also expanding in 2014 is CPI’s hot melt laminating capacity. While partnering with ITW Dynatec once again, CPI’s hot melt spray laminating capabilities include two or three ply, add-on levels from ½ gsm to 25 gsm, widths up to 112 inches, inline slitting and particulate dispensing. Gorenc says, “With the success we were seeing from the filtration and industrial market places for lower add-on applications, we realized the need to expand our hot melt laminating capacity and update our technology.”
Brought online in September 2013 was another slitter/spooler with a valuable slitting feature. The slitting station was designed to allow for bringing in wide parent rolls (up to 52 inches) and slitting/spooling accordingly. This feature allows the operator to pass back through any off cuts due to spool demand. This process saves time and money on pre slitting from the mill or at CPI.
“We saw this as a great opportunity to save our customers time and money,” says Gorenc. “That’s really why we are in business, to serve our customers by providing quality service, at a competitive price with innovative converting capabilities.”
www.convertedproducts.com
E&T Converters
E&T Converters was founded in 1972, with the goal to provide the best possible converting services at the most competitive price. Because it has so many years of experience in the converting business, its staff is able to offer a wide variety of slitting capabilities. This enables the company to provide contract converting for virtually any market. In 1989, E&T built a new 230,000 sq. foot state-of-the-art building with a rail site so that it could effectively manage the many needs of its customers. E&T is family owned and takes pride in its quality, service and value offered to all of its customers.
www.eandtconverters.com
JX Nippon
JX Nippon ANCI, Inc. the manufacturer of the original CLAF and Milife fabrics, exhibited at Pack Expo last month in Las Vegas.
In addition, JX Nippon has two products being featured at this month’s IFAI Disaster and Mitigation Response display at IFAI in Anaheim, CA. The two products demonstrate some of the converting capabilities employed at JX Nippon and show novel end uses for the company’s products. One of the products is a unique lamination of CLAF and metalized film for use as an emergency blanket, and the other is an oil boom product which uses CLAF to speed the absorption of petro-chemicals at spill sites.
www.jxanci.com
Micrex Corporation
Micrex Corporation is the developer and manufacturer of the Micrex/Microcreper family of compressive treatment machinery for nonwovens, paper, films, composites and textiles. Companies worldwide use Micrex technology to add softness, bulk, drape, absorbency, extensibility, and stretch to a wide range of products.
www.micrex.com
National Wiper Alliance
National Wiper Alliance (NWA) is the largest operation in the U.S. focused on nonwoven dry wipes converting and private labeling. Operating out of its 500,000 square foot state-of-the-art facility located just outside Asheville, NC, NWA has over 30 converting lines offering slitting, inner folding, folding, sheeting, and perforating—both with core and coreless, as well as printing—with both inline and dedicated print lines. Additional in-house services offered include: product development, quality control department with product testing, warehousing, customer inventory management, and distribution and logistical support.
Products converted by NWA can be found in the retail, aerospace, automotive, industrial, food service, hospitality, medical, government, military, and janitorial markets.
NWA is proudly registered to ISO 9001:2008 standards.
www.nationalwiper.com
Nonwovens of America
Nonwovens of America, Inc. (NOA), is located in Swannanoa, NC, and operates a 5.4-meter air-lay needlepunch line and runs colors in a weight range of 3.5 ounces per square yard to 34 ounces per square yard. NOA just completed the installation of an inline calendar. In addition to the needlepunch line, NOA provides custom converting services which include a 10-color, 99” wide rotary screen print line, blanket lines, slitting and re-rolling. NOA offers toll converting services on the needlepunch line as well as all other converting service. The main areas of focus are automotive, retail, geotextile, industrial and emergency blankets. NOA provides in-house customer service, product development, warehousing, logistics and distribution support.
www.nonwovensofamerica.com
Rockline Industries
Rockline Industries is the biggest and most diverse turnkey contract manufacturer of wet wipes worldwide. It has been a family-owned and run business since its founding in 1976. After nearly 40 years of relentless innovation and effort, it is now a 2000-person global operation boasting the most comprehensive range of converting equipment in the business. The word “urgency” describes the sense with which it seeks to earn recognition by its customers as the unmatched leader in contract manufacturing. This urgency involves five basic imperatives — Renew (invest all earnings in continuous improvement), Respect (treat others as we want to be treated); Integrity (do the right thing); Teamwork (individual goals are secondary to team goals); and Excellence (best in class). Rockline fosters a culture of integrity, service and personal growth. The company delivers excellence in its products, process and services. It doesn’t compromise integrity for financial gain. Its partnerships are managed with the utmost respect.
Rockline embraces continuous change through product innovation and capital reinvestment and form a dedicated and passionate team from management on down. Its values are applied to all stakeholder relationships—from customers, associates, and suppliers on out to the communities at large whose needs it meets with uncompromising effort. It works every day to confirm just how much Rockline values each and every one of them. Rockline understands this is the only way to build and sustain the reputation it seeks within the industry. In the words of its CEO Randy Rudolph, “We won’t make a product we wouldn’t buy for ourselves. We aim for the sweet spot. Rockline is big enough to give our customers the resources and vision of a global company, yet we are small enough to value each and every customer.”
Integrity: Every Rockline associate is asked, “Do what you think is right – every day.” These simple words can make for tough choices, but Rockline says it will never stop trying to do the right thing. The company has a reputation in the wipes industry, for example, of uncompromising integrity with respect to maintaining strict confidentiality to protect and preserve intellectual property for the ongoing business security of its customers.
Innovation: At Rockline, its core strength is the quality and innovation of its product. The focus of its contract manufacturing group is to deliver excellence in customer service by supporting its customers with custom manufacturing and cutting-edge product and packaging while strengthening its speed to market. This is supported by a winning combination of technical leadership along with the most diverse manufacturing platforms in the wet wipes industry. It listens, innovates and collaborates with its valued customers to deliver customer specific solutions that leverage its expertise in material, manufacturing and innovation.
Sustainability (www.rocklineind.com/environmental-sustainability): Rockline is aggressively moving from fossil fuels toward clean, low carbon energy, designing waste and inefficiency out of its system, and embracing strategies like reuse, recycling, and energy recapture to reduce landfill use and waste water production. Rockline strives for Ecological Intelligence in its end products, using less material where it can, and sourcing natural and recycled materials wherever possible. It is Rockline’s commitment and passion to put its own reputation on the line every day, to measure and report its own progress so customers don’t have to. That’s what sustainability means to them.
Values: Rockline says its values define them. They reinforce to all of their stakeholders—customers, associates, suppliers and communities—just how much Rockline appreciates them. They allow Rockline to build a value-based business and reputation within the industry at large. Within the contract manufacturing sector, its values ensure that Rockline maintains a global recognition as the premier supplier in the industry, producing innovative solutions, ensuring mutually profitable partnerships and providing customers with important and trusted services that create lasting relationships.
www.rocklineind.com
U.S. Nonwovens Corp.
U.S. Nonwovens Corp. is a pharmaceutical-grade wet wipe contract manufacturer, exceeding FDA and EPA standards. The company offers cutting edge R&D, tech transfer, stability, validation, ramp-up, auto-production, quality control, quality assurance, micro, and training in state-of-the-art wind-powered facilities, managed by pharma industry professionals, covering every type of OTC, cosmetic, personal care, or home care wipe imaginable, in every wipe format. Customers include global CPG and pharmaceutical companies, to the world’s largest retailers.
www.usnonwovens.com
Web Industries
Web Industries continues to focus on adding capabilities and increasing capacity to offer consumer product and health care companies the ability to combine multiple converting and manufacturing steps and outsource them to a single location. Web’s latest acquisition is a high-speed, wide-width converting line that accepts and produces “Jumbo Rolls” of up to 60 inches OD x 80 inches width. These jumbo rolls support longer manufacturing runtimes and lower input and production costs.
“The ability to handle 60-inch OD rolls is an exciting addition to our existing large-format, high-speed slitting, spooling, and printing portfolio, and it offers our customers the ability to increase their operational efficiencies,” says James Oas, director of operations-consumer products market. “A 60-inch roll contains 57% more material in area than a 48-inch roll, and this increase can have a huge impact on client’s downstream manufacturing throughput.”
By combining contract converting, spooling, printing, and supply chain management services in a single location, Web Industries offers CPG and health care companies the speed-to-market and manufacturing efficiency advantages they need to be successful in the marketplace.
www.webindustries.com