Tara Olivo, associate editor08.06.15
A.Celli Nonwovens
A.Celli Nonwovens’ Iridium technology, which made its world premiere in 2013, is developed to offer the highest quality printing onto
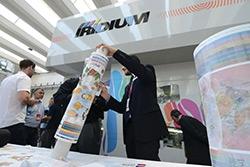
different kinds of substrates including nonwovens, PP/PE film and tissue with a wide range of basis weights. This technology enhances the process chain, offering roll goods producers the possibility to add aesthetic benefits to their products, empowering their brands with high definition designs and images. The technology offered by A.Celli Nonwovens enables multi-color printing using UV, water-based and solvent-based techniques.
This flexo printing technology works web widths that go from 300 mm up to 2800 mm and runs at a speed of up to 1000 m/min, depending on the substrate, and can host from two to 10 color decks.
Among the machine’s main features are automatic pressure adjustment, smart/automatic register, deck washing system, plate and central impression drum cleaning systems and automatic sleeves change.
The company says the success of this new technology is confirmed by another order recently confirmed by an important North American industrial group that has decided to remain anonymous at this time and whose trust in A.Celli Nonwovens technology is the best proof of the Italian group’s winning business strategy.
“Adding this order to our portfolio is not just an important milestone in commercial terms, but also allows us to set the first building block in a recent market for our company—printing,” comments Alessandro Celli, president and CEO of A.Celli Nonwovens. “This order is another strong signal of the wide-ranging versatility and high technological level of A.Celli equipment; a further tangible sign of the answers we are able to supply to our customers’ needs.”
www.acelli.it
Andritz Nonwoven
The original Wetlace process has been developed by Andritz and combines wetlaid and hydroentanglement technologies. It has proven to be ideal for producing flushable wipes from 100% natural and/or renewable raw materials without chemical binders. The material needs excellent dry tensile strength during production. The end-user expects a wet wipe that does not disintegrate before and during use. Once flushed, however, this stability has to disappear completely. These contradictory properties are achieved with innovative wetlace technology that even excels the latest EDANA/INDA flushability standards. Wetlaid production is perfect in terms of achieving excellent web uniformity. Hydroentanglement creates entangling of the fibers without any chemical binders or thermoplastic fibers.
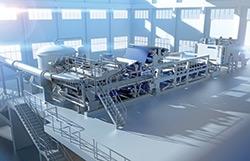
In addition, Andritz has developed a process to apply special and unique artwork to flushable wipes. This unique patterning process will allow wipes producers to clearly differentiate their product in ways that will resonate with consumers.
The patterning of flushable wipes is technically very challenging due to the weakness of the flushable substrate, which must have only enough strength for the intended purpose and then be able to disperse completely in water with no residual wet strength. This Andritz patterning solution is also compatible with 100% cellulose-based nonwovens, while other techniques require the use of thermoplastic fibers or chemical binders. It fits perfectly with the sustainable trend in flushable wipes, more and more of which are 100% cellulose-based and contain a majority of wood pulp fibers blended with short artificial cellulose fibers. This powerful and innovative solution for patterning of flushable substrates allows an almost unlimited number of possible patterns.
www.andritz.com/nonwoven
Aurizon Ultrasonics
Aurizon Ultrasonics, a market leader in high-speed rotary ultrasonics, has introduced its patented process of attaching elastic strands to nonwovens, eliminating the costs and issues associated with adhesives. The process supports line speeds up to 2000 feet or 600 meters per minute. Even when line disruptions occur, the ultrasonic system continuously attaches the elastic strands. The end result is elastic strands are secured within the nonwoven substrate, eliminating creep and allowing for maximum product performance. By eliminating glue, the end user experiences a softer feel and greater comfort, the elastic performs better without creep, production lines do not need to shut down due to contamination and the high cost and issues from buying adhesives are eliminated.
Aurizon’s platforms of 20 kHz and 30 kHz rotary ultrasonic systems enable this exciting new capability. Stretch elastic strands and
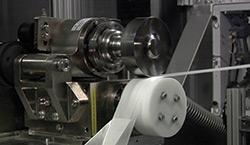
nonwoven substrates pass through the high-speed rotary ultrasonic drum and anvil entrapping the elastic strands between the nonwoven substrates without adhesive. This is truly a game changing technology that is tested, commercialized and available today.
In addition to elastic strands entrapped in nonwovens, Aurizon can bond many different substrates for many applications for nonwoven products including feature attachment, core bonding, acquisition layers and backsheets. At Aurizon’s facility in Kimberly, WI, trials can be conducted using the customer’s substrates to demonstrate the elastic entrapment and many other ultrasonic bonding capabilities.
www.aurizonultrasonics.com
Diaper Recycling Technology
Diaper Recycling Technology is a technology company solely focused on advanced diaper recycling solutions. Its advanced recycling technology is used within hygiene plants (Adult-Baby-Fem) to reclaim pulp, SAP and plastic from rejected products.
Diaper Recycling’s technology offers hygiene producers superior performance in the following areas: (1) No measurable SAP damage; (2) Best in class purity of PE/PP stream; (3) Best in class purity of SAP stream; (4) Best in class purity of fiber stream; (5) No mixing of raw materials (In-Line system) ensuring zero contamination risk without compromising existing raw material tracking systems; (6) Significantly reduced space requirements within a factory with in-line systems requiring as little as two square meters; (7) Lowest energy in class (8 - 10 KW) due to a revolutionary air-less process; and (8) No impact on installed HVAC/utility loadings.
Diaper Recycling Technology’s combined equipment portfolio including inline and central configurations offers end-users a financially viable business proposition independent of their factory size. The company’s breakthrough technology has been specifically developed to support hygienic producers to achieve environmental targets through the elimination of landfill; burning/incineration; transportation; and all environmental aspects in relation to non-recovered products at product B processing sites.
Diaper Recycling Technology invites hygiene producers to send samples of rejected diapers for initial testing where it can analyze the separation performances allowing detailed project NPV/ RORs to be calculated.
www.diaperrecycling.technology
Diatec
“Evolutionary” is the right expression to describe Diatec’s recent product updates in the converting machinery segment. For over 20 years, Diatec has established itself in the world as a designer and builder of converting machinery for sanitary products, including baby diapers, adult incontinence products, sanitary napkins, panty shields and underpads.
Over the last year Diatec has invested in the development of its technology by developing know-how in disposable products in absorbent food pad production. This new product is used on food packaging to absorb fluids released by meat and fish inside a tray.
Diatec machines can be used as food pad lines with airlaid film or with fluff core through a vacuum forming system, following the customer’s needs.
Diatec technology also developed a new section in laminating lines for the production of high quality laminates up to 3200 mm wide. Three different sealing technologies are offered: ultrasonic, thermal bonding and hot melt. Nonwovens, breathable polyethylene layers, metal coatings, aluminized layers and nettings are usually used in roofing and house construction. The industry studies and technological developments in laminating machines gives customers access to more areas including mobiltech, med-hygienictech and clothtech.
At the same time, Diatec gives its customers the possibility to manage different kinds of raw materials, developing a complete range of spool winding machines and unwinding units for different sizes of materials between 35 and 190 mm at a linear speed up to 650 m/min. Thanks to spool technology, Diatec gives customers convenient packaging for handling, storage and unwinding solutions.
www.diatec.it
Dienes
As a worldwide leading manufacturer for industrial slitting technology, Dienes sets once again a new standard with the innovative DS 6 in the field of knife holders. The DS 6 is the culmination of Dienes’ 100 years experience and know-how from more than 500,000 produced knife holders. Whether it is with manual or semi-automatic operation, the DS 6 impresses with its extremely high stability with very small cutting width from 30 mm and speeds up to 2000 m/min. Adding to this is the worldwide unique cutting pressure positioning, its high longevity, as well as its comprehensive compatibility.
Due to the Dienes honeycomb structure and the long guide bodies, the compact and light design of the DS 6 is extremely sturdy. This means the user can expect the highest accuracy even for small cutting widths, and additional benefits from an increased durability. Furthermore, the DS 6 with its high variability is suited to many sophisticated fields of application, like the processing of paper, foil, nonwoven material and non-ferrous metal foil. Dienes’ unique patented cutting pressure positioning prevents the stick-slip effect with the balanced pressure distribution on the knives.
The fact that its new knife holder is trendsetting on the market is also demonstrated by the other product features of the DS 6. For example, it has an integrated patented adjusting slide, which enables precise and reproducible positioning of the holder towards the bottom knife. The setting of the shear angles is possible in two ways: Conventionally with a plate on the retainer as well as from the front with the Dienes angle supports. The quick-change heads ensure a simplified, timesaving and above all safe removal during maintenance and knife exchange – the knife head and the integrated 360 degree guard can be completely removed and inserted as one unit. Furthermore, this unit can be used in both directions, so that the knife holder is suitable for all feed-ins or can be quickly repositioned. In addition, the knife holder has a forced sequence control for the cutting pressure positioning. Alternatively, however, supply via two separate compressed air circuits for individual adjustment of vertical and horizontal stroke can be selected, so that the cutting pressure can be set even more accurately and reproducibly.
Operation of the DS 6 is intuitive, comfortable and wholly flexible by being usable from all sides. Its design is vibration absorbing and it has comprehensive rust and dust protection for maximum sturdiness. Furthermore, it is compatible with almost all existing slitting systems and is thus ideally suited to easily update existing machines and make them future-proof.
The DS 6 knife holders are available as version M with manual depth adjustment as well as version S with semi-automatic design. The innovative depth adjustment of the DS 6-S provides particular comfort, as it is done step-by-step via a display, which has an integrated teach-in phase. The user thus benefits from even higher accuracy and traceability. At the same time, operating errors are minimized.
www.dienes.de
DiloGroup
DiloGroup offers universal and customized modern nonwovens lines characterized by high capacity, a wide range of applications, ease of operation and excellent maintenance.
Dilo machines are used for production of the complete range of staple fiber nonwovens, including technical applications, automotive and household, medicine and hygiene, decorative felts and floor coverings, but also base material for coatings, composites and high-tech applications.
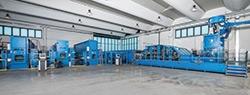
There is a constant demand for nonwoven lines used for needled filter material. The increasing need for environmental protection and sustainability led to a requirement for high quality needled filters in growing numbers and with special characteristics. This is an ever-growing challenge for Dilo machines and their technology.
Dilo installations for the production of geotextiles represent another significant application area. Due to the required strength values and homogeneity in longitudinal, cross and diagonal directions, these installations can include drafting systems before and after preneedling. In Dilo lines the finish needling from both sides is done either in a double needleloom OUG or in two subsequent needlelooms with alternating needling directions. These needlelooms are delivered as universal or high capacity machines with a wide range of stroke frequencies, needle patterns and in working widths exceeding 8.000 mm where required.
For the production of nonwovens used in the car, Dilo offers lines for flat and structured felts. The focus is still on velour, needled on the DI-LOUR machines. For the production of felts used as sound and heat insulation in the car, Dilo machines are often equipped with the DI-DUST system, as these felts are produced with recycled fibers and filling material. DI-DUST is a cleaning system that automatically discharges fiber dust.
A special installation is a line for production of the so-called wheelhouse linings. In this case, two parallel card/crosslapper lines produce the base and the cover felts. The intermediate layer consists of flakes of recycled automotive carpet. This construction results in excellent strength values in the subsequent thermal molding.
Machines and lines for the production of wipes, for needling spunbonds, for medical and hygiene applications represent further challenges that are met by DiloGroup.
DiloGroup also offers nonwoven machines for the needling of metal and inorganic fibers, for fibers used in high performance and high temperature applications as well as machines for tubular felts.
Endless tubes and narrow belts are indispensable technical nonwovens, and not only as paper machine felts. For this application Dilo offers wide needle looms, including the new machine design PMA, which allows single or double sided needling of tubular felts in a range of 2 to 8 meters wide and a circumference up to 9 m. This machine offers new fields of application for example as transport aprons in the textile and food industries, high capacity felts in metallurgy and highly efficient handling techniques provided by endless needlefelt belts.
The demands on the fibers used, in terms of processability, mechanical and textile properties are steadily increasing.
DiloGroup delivers highly efficient production lines from fiber opening to finished roll goods in all working widths. The card capacity which determines the efficiency of the whole line is between 300 and 550 kg per meter of working width depending on fiber type and fineness. Working widths can be more than 5500 mm.
Universal crosslappers of all types have been tuned to the process and work with modern apron technology, highly efficient drives, apron guiding and web guiding technology of the Dilo Webguide system to reach the highest web infeed speeds.
If high web regularity is required, web profile adjustment is realized with a CV1 system installed between card exit and crosslapper entry, controlled by a batt weight measurement system at the end of the line. Longitudinal and cross cutting as well as winding are carried out with subsequent machines. Sometimes an accumulator is used to ensure continuous production without stop during roll change.
DiloGroup engineers special machine systems for all these applications. The components for opening and blending - DON - and for card feeding - MultiFeed – are able to deliver exact webs to the universal card MultiCard even when low weights are processed and the working widths of the card increase.
www.dilo.de
Everwear
Engineered from the knife out, Everwear Knife Rolls, Anvil Rolls, and Cutting Modules have reliability, speed and productivity built into
their design. Every specification, material selection and feature of an Everwear roll and cutting module is for the optimal performance of the knife. A user’s benefit is less downtime for knife changes and adjustments, increasing productivity.
Machine builders maximize knife life in converting machinery by including an Everwear cutting module intotheir design. Everwear’s design philosophy gives machine builders who are looking for fast, reliable cutting, a low maintenance platform.
Producers with existing lines—whether the need is to replace outdated crush-cut technology or if a new product requires a different module—Everwear will customize a roll or cutting module to help them realize their production goals.
www.everwear.com
Formfiber Denmark
Formfiber Denmark’s patented Spike AirCarding Forming Equipment delivers innovative airlaid nonwovens technology, designed to efficiently form carding length or shorter fibrous raw materials. If a customer’s mat product application requires heavy basis weight mats up to 10,000 gsm, Spike AirCarding is an ideal technology, which can also be used for applications that require a low-basis weight web of 10 gsm or more.
Spike AirCarding formers are being applied to applications with production line speeds of up to 600 mpm for low basis weight webs, to deliver consistently good formation, with short fiber lengths, and superior productivity.
Formfiber Spike AirCarding Technology offers the following commercial advantages: substantially higher forming capacities, per Meter Width of Former; substantially lower forming air consumption; form natural or synthetic fibers with lengths from 1 to 102 mm (4.0”); form and then thermally bond mat products with a finished mat thickness of 400 mm (15.75”) or less; and forming zone widths of 600 to 5000 mm (24” to 197”).
Formfiber Corporate facilities in Denmark provide test plant facilities for its clients’ product development trials.
www.formfiber.dk
Hills, Inc.
Hills, Inc. offers advanced fiber extrusion equipment to produce spunbond and meltblown fabrics, as well as staple fiber and continuous filament materials. Customers use Hills’ extrusion technologies to produce the world’s most complex multi-component fiber cross sections with unprecedented combinations of polymers. Applications include micro fibers with practically any geometry for applications such as filtration, artificial leather, industrial fabrics, and medical uses. The same advanced concepts are being pursued in areas such as carbon fiber precursor, new membrane materials, and high quality textile fabrics using spunbond and staple nonwovens.
Recent Hills programs in nonwovens include the following: Hills spunbond machines use a proprietary high-speed slot aspirator especially suited to high-performance polymer applications such as primary carpet backing, roofing membrane substrate, artificial leather substrate and filtration media. When combined with Hills’ knowledge and unique capabilities in multi-component extrusion technology, the flexibility of Hills’ equipment makes many of these applications possible on the same machine. In addition, Hills has recently introduced patent-pending high loft and high stretch spunbond fabrics with diverse applications including barrier fabrics (such as thermal, acoustic, particle or shock barrier), distribution layers, and MD & CD stretch fabrics without the use of elastic polymers.
Hills meltblown machines employ proprietary die technology to make a variety of high-value products including sub-micron and nano-products as well as multi-component products. Hills’ dies are available with hole counts to 100+hpi, and unlimited capillary L/D which allow custom designs to precisely fit the customer’s polymer and product needs.
In addition to production equipment, Hills laboratory and pilot extrusion machines for the above processes are available and are presently running in many private and public R&D centers around the world.
www.hillsinc.net
ITW Dynatec
ITW Dynatec, a global supplier of hot melt equipment and solutions, is launching the latest Ultra SCS (Strand Coating System).
Coming soon to the market, this revolutionary strand applicator can provide customers with the highest line efficiencies. The new technology features a patent pending design and the most accurate and highest efficiency adhesive coating on strands ever designed to provide customers with the best product performance and less product issues. Its new Ultra SCS also features: next level high-speed technology (up to 1400 pads per minute – 700 MPM); Rapid Change-Over (RCO) design for quick maintenance solutions; Ultra-Stitch and Ultra-Touch nozzle designs to meet multiple requirements; integrated hardened steel elastic strand guides for extended long life; large adhesive orifices for less plugging and higher line efficiency; optimized Ultra-Apex module technology for fastest response and longest cycle life; and lowest usage of adhesive available with total creep strength down to 1% (even as low as 15 grams/linear meter/strand). The Ultra SCS was developed with CFD modeling (Computational Fluid Dynamics).
Recent tests indicated that when new creep data was compared to older data (latest competitors offering), Ultra-SCS performance surpassed expectations. “It blew any other trial creep results out of the water,” says one of ITW Dynatec’s global customers.
www.itwdynatec.com
Jiangsu Yingyang Nonwoven Machinery
Situated in Changsu Province, Jiangsu Yingyang Nonwoven Machinery Co. Ltd. (YY) was founded in 1993 and has grown into one of the largest single site nonwoven machinery makers in the world.
YY covers all variations of nonwovens including opening, lending, carding systems, airlaid systems, needlepunch, thermal bond, spunbond, and vertical lapping and other associated nonwoven systems.
Over 90% of all machinery is made totally in the factory including card cylinders, all machine frames, needle boards and all electrical control systems. Carding machine capacities are up to 1200 kg per hour dependent on fiber types. Needle looms up to 11 meters in width are available as well as multi head looms and Random Velour units. All types of patterning looms are available. For thermal bonding both through air and conventional ovens are made with various airflow systems to suit customers needs. Spunbond units up to 6.2 m width are available.
VLS is the newly patented Vertical Lapping system from YY and this new design gives larger thickness options, higher speeds and lower capital cost than any previous system.
For testing purposes YY has a 3.6 meter needling line available with up to nine looms and a full production size VLS vertical lapping at 2.5 meter width able to run any fiber from customers.
All lines made for the Western markets are totally built and tested with material if required by the customer prior to shipping. In both Europe and North America, YY has both bases holding spare parts as well as locally based trained engineers as and when service is needed.
www.china-nonwovens.com
Kansan
Kansan is continuing to shape the global wet wipes industry’s landscape by developing a new cross fold converting machine, “Flexiwork” with an advanced stacking system and the capacity for up to 600 cuts per minute.
Flexiwork is available with one, two, three or four roll units which work individually yet in complete harmony. With Flexiwork, manufacturers are able to produce two different types of wet wipes in terms of dimension and lotion while at the same time diverting to the two packaging machines.
In addition, if there is any issue within a unit, other parts of the machine are able to carry on. In other words, without stopping the whole machine that particular area can be troubleshooted. While the dimensions of the machine are significantly reduced compared to others, it is designed to be user friendly, requires less maintenance and all the units are easily accessible.
As a part of the continuous development strategy, the R&D department of Kansan enhanced the Automatic Flow Pack Machine, Acurapack 120, to offer its clients less wastage and more comfort.
Based on client feedback, the equalizer conveyor has been redesigned to minimize packaging and nonwoven material waste while the communication with the converting machine has been improved.
Thanks to the heat distribution in the jaw system homogenization, product with opp mat and pet packaging materials can be produced 10% faster. With enhanced die cut system, knives will last longer and overall, operators are able to operate only with few adjustments.
www.kansanmak.com
Lemtech
Located in Paterson, NJ, for over 20 years, Lemtech has offered polyband web spreader rolls, a wide range of machine parts/assemblies for Lembo equipment and decades of process expertise. The Lemex Expander roll is effective in spreading a wide
range of substrates, including but not limited to acrylics, polyethylene, polyester, polypropylene, vinyls, cotton, knits and synthetics. One of the advantages of a polyband spreader roll over other spreader roll is the even spreading action imparted on the substrate. Additionally, repair of the roll due to band wear/damage can be done in the machine in a matter of minutes where most other spreader rolls need to be removed from the machine and sometimes returned to the manufacturer for repair. The spreader rolls can typically operate as idler rolls, but a drive option is available for low-tension applications.
www.webspreading.com
Mobi-Air
Mobi-Air, makers of Mobi-Flex, the hygiene industry’s most advanced filtration platform, supports hygiene manufacturers meet their environmental, financial and operational targets through low energy, state-of-the-art flexible equipment solutions. The Mobi-Air equipment platform is still the world’s only true hybrid filter technology offering the best of both bag-house and drum-filter technology and break-through performances to the end-user.
Mobi-Air designed the entire utility and filtration concept from the ground up, putting all of its engineering expertise together into one all new visionary filtration platform. That forward-thinking platform, today, offers the end user: (1) The world’s first flexible hybrid platform with superior drum-filter and dust-collector technologies and no downside; (2) Multi-business unit compatibility with a single equipment platform; (3) Instant mobility with assembly-free vertical start-up; (4) The highest filtration performance in its class; (5) The lowest energy-consumption in its class; (6) The highest safety in its class; and (7) Industry first plug & play modularity.
New hybrid filtration technology offers end-users a “hybrid” filtration solution offering both a compact equipment solution of far smaller size than even latest generation drum filter technology and a wide process window similar to bag-house technology. Mobi-Air’s filtration technology not only provides world class air filtration levels up to 99.999995 @ 0.3 micro; the low energy filtration process provides best in class energy consumption achieved through low pressure-drop hi-surface-area media of up to 1500 square meters; next generation 64BT CFD modeled processes ensuring best in class performance.
Newly developed zero energy plug-in HVAC modules coming later in 2016 create an ideal factory work environment with minimal operating costs.
www.mobiair.technology
Mondon
Mondon’s automatic turret unwinder TUW Series offers a quick-change function which means that a new roll begins automatically when the previous one is finished. Thus, producing lines never stop. The nonstop process aims to unwind the reel without stopping the downstream coating or laminating process of the line. During the unwinding process, a new roll can be loaded in hidden time thanks to roll down end and dedicated cartridge. Moreover, the TUW Series ensures a constant speed to maintain tension in the line process. Specially engineered to improve process performance, TUW Series ensures easy installation, easy handling and durability for users.
Downstream in the process area, Mondon installs its TW Series winders, achieving high productivity and first-class results. This turret winder supports two shafts to unload a bobbin while rewinding a new one. The TW Series Winder combines performance with durability and first-rate technology. TW Series technology permits users to wind large bobbins or small rolls thanks to a multi-cut station. TW Series Winder control is performed thanks to a network application with the upstream processing line. Due to its non-stop process, the winder avoids the transition sequences. The accuracy of the TW Series turret winder rotation is a key factor to maintain a very constant tension in the product and to deliver the highest quality reels.
Mondon also manufactures slitter rewinders, short rolls winder and spooling lines, completed with packing and palletizing modules.
www.mondon.com
Nanoval
Nanoval uses a specific effect by which a steadily accelerated gas running in parallel to a liquid stream attenuates it until it splits up by bursting, forming a multitude of continuous filaments in a split-swinging effect. It is also used for disintegrating metal melts to form powders. The atomized powders are increasingly used in three-dimensional printing as in additive manufacturing.
Due to the splitting action, the gas-dynamic Nanoval effect can use large spin nozzles even for fine filaments. Functional particles like
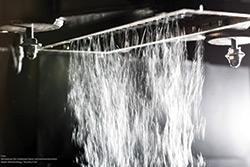
superabsorbent polymers (SAP) or wood particles in cellulose can be incorporated in the filaments as the larger nozzles do not block.
Nanoval has already spun cellulosic webs with up to one-third of wood particles and two-thirds of pulp or waste paper in a Lyocell process improving flushability of wipes. Cellulosic nonwovens can reinforce paper so that both components are biodegradable.
In polymers like polypropylene, fine filaments in the micro-nano range can be produced to nonwovens for filters at high retention and low pressure drop.
The process and equipment are robust and energy consumption compared to conventional systems like meltblown is lower, throughput in kg/m*h is higher.
www.nanoval.de
Nordson Corporation
Nordson continues to help disposable hygiene product manufacturers cost-effectively produce high-quality, high-performance baby diapers, adult incontinence garments and feminine hygiene items. Enabling variable material dispense capability – different add-on weights or patterns from a single applicator in a single pass – is one tool to help improve product quality and reduce material costs. Nordson offers several variable dispense applicators to meet different manufacturing needs.
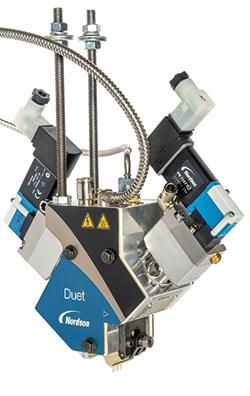
Duet applicators for elastic attachments deliver different add-on weights from a single applicator, so heavier add-on weights can be applied to the ends and lighter add-on weights in the center of elastic strands. The heavier add-ons assure strong, reliable bonds while the lighter add-on in the middle helps improve product performance and comfort. Patented, dual-module Duet applicators can offer up to 30% savings in adhesive-related costs compared to traditional applicators by reducing center add-on weights.
Using Nordson Allegro and/or SureWrap elastic attachment nozzles further optimizes adhesive use and improves product quality. And, Duet applicators incorporate Nordson’s patented Universal clamping feature for quick, easy nozzle changes.
Trio triple shim applicators produce patterns with different add-on weights in both machine and cross-web directions from a single applicator. Additionally, Trio applicators can apply multiple materials simultaneously and dispense coating-on-coating patterns. This flexibility with variable add-on weights and patterns helps disposable hygiene product manufacturers meet varying functional and sensory performance needs more cost- and production-efficiently.
Production efficiency delivered by Nordson’s variable dispense applicators is further enhanced with quick-exchange components, such as filters and modules, that simplify maintenance and increase production up-time.
www.nordson.com/nonwovens
Optima Packaging Group
The new Optima LS Stacker processes up to 1600 units per minute and forwards them in stacks of up to 100 units to the downstream packaging machines. This is quite an achievement considering the weight of the bundled bed liners, incontinence products or other nonwoven stacks to be transported through the machine –up to 5kg per bundled stack.
Due to the high speeds, considerable g-forces are exerted on the product mover and the guides of the Optima LS Stacker. These forces are compensated by way of the inherent magnetic fields of the linear drives. With the new drives and output, the stacker enters the domain of diaper packaging speeds and can therefore also find application there.
Newly designed cassettes on the Optima LS Stacker take up the products. Instead of base plates, the new cassettes use intermeshing forks. These can be adjusted as needed to suit the pitch of the freely adjustable mover. Format changes can therefore be made “on the fly” at the push of a button.
A further feature of the new Optima LS design is the so-called tightening function. The product stack which is in the cassette is held and calibrated for a specific force.
The new mover cassettes are compatible with existing packaging processes—the typical “standard” transfer is unaffected. The new Optima LS Stacker can be intelligently combined with various packaging machines supplied by Optima nonwovens.
www.optima-packaging-group.de
Osprey Corporation
Osprey Corporation has implemented industrial level remote connectivity into its electrical control systems that allows remote programming and monitoring of ethernet and serial connected devices from its headquarters in Atlanta, GA, or from anywhere in the world. Osprey can assist with basic commissioning of the equipment, troubleshooting equipment in operation or major system changes that may arise during the lifecycle of the equipment. This can reduce the time and travel expenses related to the service and support of its equipment installed globally.
A DIN rail mounted industrial router communicates with ethernet and serial connected automation devices inside the control panel including PLCs, HMIs, motor controls, etc. To make these devices remotely accessible, the router makes a secure outbound connection to a cloud based Virtual Private Network (VPN) server. Osprey can then connect to the cloud-based server, which verifies credentials and completes an encrypted VPN pathway between the Osprey engineer and the connected equipment.
An optional GSM modem and service from a cellular internet provider allows locations without an available hardwired network connected to the internet to also benefit. Other optional features include historical data logging for troubleshooting and custom web interfaces for remote monitoring of equipment by authorized plant personnel.
www.ospreyfilters.com
ProJet
ProJet BV applies decades of experience to deliver process belt cleaning solutions worldwide. Consistent belt cleanliness applies to all companies producing nonwoven roll goods with airlaid, drylaid, meltblown, spunbond, spunlaced or wetlaid nonwoven forming technologies.
ProJet “PowerCleaner” advantages include: high-pressure (up to 5,100 psig) and low water volume (about 0.26 gpm per nozzle) to efficiently clean process belts without chemical additives; no contaminated water mist is expelled into the process area; belt cleaning and drying is accomplished simultaneously; contamination is collected and transferred to a save all pan with a vacuum pick up system without an auxiliary vacuum pump; and automatic nozzle cleaning, head flushing, and system maintenance is accomplished without interrupting continuous production.
ProJet provides complete, turn-key fabric cleaning solutions, which include: mechanical and electrical control engineering services; customized solutions for each unique belt cleaning application; door to door delivery services; on-site installation supervision services are provided by ProJet Engineers; and best in the business customer service after the sale.
www.pro-jet.nl
Rando Machine Corporation
Rando Machine Corporation is an expert in airlaid technology and web formation. Its latest technology helps manufacturers improve
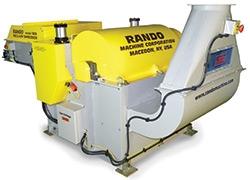
upon their finished-waste material by either increasing efficiency in the fibers disposal process or reclaiming the fiber by adding it back into the production line.
From soft to hard edge trimmings, its new Rando Waste Shredder/Refiberizer is outfitted with state-of-the-art technology to help break down material into small, uniform tufts to be reintroduced to production and contribute to a finished product.
Discarding the material that is trimmed from the finished product takes a heavy expense on organizations as they pay outside services to remove and dispose of the excess material. Purchasing a Rando Waste Shredder/Refiberizer eliminates this need by providing a manufacturer the opportunity to reclaim and repurpose the excess “skeletons” back into the finished product. The Rando Waste Shredder/Refiberizer will not only save money by removing this expense, but also provide an additional, usable source of reclaimed fiber material that can be reintroduced into the production line accordingly reducing overall fiber costs. Therefore, our new machine provides an attractive solution for organizations looking to save money and improve environmental practices.
After exceeding expectations during its pilot program and operating at full capacity for a major manufacturer, Rando is proud to announce that it will be adding this machine into its laboratory line in the near future.
www.randomachine.com
Sandvik Hyperion
Sandvik Hyperion is a global company specialized in hard and super-hard applied materials, belonging to the Sandvik Group. Within the nonwovens market, Sandvik Hyperion is a leading company in rotary cutting solutions for the hygiene business. The high quality of its products, combined with the engineering service, customer assistance and global/local service, make it easy to find the right solution for customers’ needs.
In the continuous effort to stay closer to its customers and serve them locally, Sandvik Hyperion is opening its new maintenance center in China, located in the Sandvik factory of Wuxi. The maintenance center is aimed to serve the Asian market for after sales service needs, like rotary cutter inspection and resharpening, anvil regrinding and frame maintenance. The Sandvik maintenance center in China adds to the established centers in the U.S., Brazil and France.
The hygiene business is evolving to higher converting line speeds, more difficult raw materials to cut, innovative manufacturing processes, new cutting profiles which all require reliable cutting solutions. Sandvik Hyperion is able to assist customers with a full range of services to ensure stable and long lasting performance. Particularly in the vibration control area, Sandvik Hyperion, in partnership with Sandvik Teeness, has developed and patented a tuned mass damper. It consists of a passive dampening system working at a pre-set frequency range which dampens the vibrations of moving parts of a cutting unit, maximizing their lifetime. Field test results show cutter lifetime multiplied by two and anvil lifetime by three.
www.hyperion.sandvik.com
Schober Technologies
Schobertechnologies is launching the redesigned SL106 - Sheetline (Rotary Sheetfed Converting Machine). The SL106 is equipped with a high-speed belt stream feeder combined with a well proven suction head technology, a heavy duty die cutting station as well as a robot-automated stacking, counting and piling system.
Most of the features, which have proven their efficiency in the web-fed die cutting machine such as the pre-set and calibrated cutting pressure adjustment, high-precision bearing assemblies and housings for low temperature running, vibration-free design and micrometric die wear compensation adjustment (GCS), have been integrated in the die cutting station of the SL106.
In addition, the converting station is equipped with a vacuum controlled magnetic cylinder tool and the new and unique gripper sheet guiding system, which ensures high-precision finishing of pre-printed sheets. The products are separated from the matrix immediately after the cutting process and redirected to the robot-automated stacking unit by a conveyor belt.
Magnetic dies guarantee the shortest set-up time as well as the highest productivity even for short runs.
The unique design of the die cutting station and its accessibility allows the possibility to integrate additional finishing tools at a later stage. The robot-automated stacking system is capable of handling different types of products combined within the same printing image. These can be heavily nested and can be a combination of large and small products.
Product specific fast exchangeable pick-up plates collect products at synchronized speed and stack them non-stop into a twin piling cassette system.
The SL106 is designed for a sheet size of 106 x 78 cm and a foil thickness starting at 50mμ. High functionality and availability, flexibility and accuracy are the characteristics of this high performance production machine.
www.schobertechnologies.de
Schott & Meissner
German machinery manufacturer Schott & Meissner, an expert in the field of “heat treatment” for the nonwoven and composites industries since 1986, now has two different kinds of machinery for producing ADL products on the market—the ADL-Air Trough Drum and the ADL-Speedliner single belt oven.
According to Schott & Meissner, both machines have their own advantages and meet the performance demands of each customer. The ADL-Air-Trough DrumDryer is available in various drum sizes up to 3m, with a very high air velocity and the company’s innovative air distribution system. These highly developed systems guarantee its customers excellent temperatures and air speeds over the complete width and treatment length. The arrangement of this Omega-type is space-saving and especially for light webs up to 100 gsm webs designed.
ADL-Speedliner is the new machine in Schott & Meissner’s scope of supply. This oven type is not limited by the treatment length of a drum diameter and can be increased in modular form to reach line speeds up to 400 meters per minute. This type of ADL-machine is also for higher web weights, and has the advantage of a very soft hand, due to the high air volume at a low operating pressure. This is all rounded out by a new guiding and air flow system.
To protect the environment and reduce energy costs, the Schott & Meissner ADL-Speedliner can be equipped with a Heat-Recovery System, which allows the customer to save not only energy but also increase the performance of the oven.
The company says both systems are already producing materials all over the world and satisfy their customers and the demands on the end users.
www.schott-meissner.de
Shemesh Automation
Shemesh Automation Wet Wipes is a world-leading manufacturer of round wipes packaging machinery. With over 25 years experience, it is uniquely positioned to offer dedicated expertise and support to the wet wipes market and provides innovative, high quality solutions not found elsewhere.
Products supported include rigid canister or bucket packs and ready-made/pre-made flexible pack bags, stand up pouches & refills. Equipment modules manufactured include feeders, wipes canister loaders, liquid fillers, sealers, cappers, labelers, form fill & seal case packers and full quality control.
Rigid packages include inline turnkey systems. Starting at 60ppm and running up to 200ppm these systems feature the company’s flagship canister loader—the SAS Series. Officially launched in 2013 and with more than 15 units already installed globally, the SAS Series is the only truly proven vertical nonwovens donuts canister stuffer in the world.
The Xpander and Xpander Plus round wipes packers offer an all-in-one Monoblock design. These innovative systems boast the only technology in the world to date capable of delivering complete, 30-35ppm, round wipes packing all in a strikingly small footprint. The Xpander serves both entry-level operators and high volume wet wipes manufacturers looking to diversify production.
Flexible packages include the Fortress, which is designed to create flexible packs from a master roll of film. It forms the bag, loads the wipes, fills, seals and discharges the finished product. The Fortress provides two levels of efficiency through the economic use of raw materials and savings gained from process automation.
The SAW-MB200, an all-in-one monoblock packer, is designed for ready-made bags. With the SAW-MB200, bags are stacked in a magazine and fed into a rotary index table where they are opened, loaded with wipes, liquid filled, sealed and discharged.
The Fortress and SAW-MB200 are made to service the jumbo rolls, standard wet wipes in flexible packs and refill markets.
www.sawetwipes.com
Sonobond Ultrasonics
Sonobond Ultrasonics’ units seal, sew, and trim—all in one quick pass. Their high-frequency vibratory waves produce safer medical garments and disposable items with bonded edges and secure seams without stitch holes, glue gaps, fraying or unraveling to meet tough OSHA regulatory requirements for barrier seams. No thread, glue, or other consumables are required. Sonobond manufactures a wide variety of machines that handle multiple nonwoven and synthetic material assembly applications.
The SeamMaster Ultrasonic Sewing Machines are a complete line of continuous-bonding models that operate like traditional sewing machines. The line includes general purpose units, table-mounted cutters/sealers, and modules for OEMs. All units utilize a patented rotary operation, where both horn and pattern wheel rotate at the same time, providing ultra-reliable and soft-to-the-touch seams achieved up to four times faster than with conventional sewing machines and 10 times faster than with adhesive methods.
The SeamMaster High Profile Ultrasonic Sewing Machine is now the most popular unit in the line due to its large pattern wheel, high clearance and ability to accommodate bulky materials and hand-guided operations with tight tolerances and curves. In fact, this machine is used by most major body armor manufacturers to seal the outer nylon shell of ballistic vests and produce a bond so reliable that it complies with National Institute of Justice submersion test standards to protect the inner layer of ballistic-resistant materials from water leaks.
The RingMaster award-winning machine ultrasonically attaches filter bags to plastic collars. Strong, reliable bonds are completed in less than 10 seconds, eliminating stitch holes that cause leaks and thread that can get caught in pumps. Fast, easy re-tooling accommodates varying bag sizes and collar diameters. This semi-automatic unit produces up to 250 bags per hour, while the manually operated version, the Filter Collar Bonder machine, will produce up to 80 bags per hour.
SureWeld PlungeBonder machines handle larger, difficult-to-bond and multi-layer materials. Models seal ends of filter bags and produce box-style filters. Custom tooling enables straps made of coated synthetic material to be bonded within the seam of a ballistic vest’s outer shell without compromising the integrity of the ultrasonically-sealed shell so the body armor continues to comply with current NIJ submersion requirements.
SureCut Ultrasonic Cutters/Sealers provide one-step cutting and sealing of ribbons, trims and labels, without frayed edges. They are available in hand-held models for single cuts or for loom-mounted operations.
In addition to the medical and body armor items, these Sonobond machines assemble HEPA-rated filters, industrial and commercial vacuum bags, oil absorbers and oil containment booms, automobile air filters, and various filtration products used by the chemical/pharmaceutical, environmental, food/beverage and manufacturing industries. They also assemble geotextiles for the agricultural industry.
Sonobond provides free sample bonds using a company’s own material and then recommends the appropriate machine for the application. Units can be customized to specific requirements.
www.sonobondultrasonics.com
Spoolex
Since 1955, Spoolex has been engineering and manufacturing quality converting equipment for various industries. After having
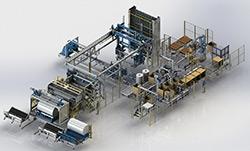
delivered around 8000 machines in more than 100 countries, Spoolex makes an important step by extending its core competences to become a global partner for converting solutions.
Spoolex has, through its worldwide recognized brands Calemard and Decoup+, real expertise in slitting, rewinding/spooling and ultrasonic splicing. Today, to meet the needs of high productivity, operator’s safety and line flexibility, Spoolex’s R&D Department has developed several automated solutions around these brands’ know-how to provide complete cell from mother handling to final product packing.
Spoolex’s latest global solution commissioned is a complete converting cell that was engineered and assembled 100% in house. This cell merges all needs of a cutting workshop but with only one control station. The solution developed combines four modules—splicing, slitting, handling, packaging—designed and automated to reduce operator handling, to increase line speed and capacities and to handle 30 different products and a wide range of pancakes sizes.
To meet the customer needs of automation adaptability and versatility, Spoolex has designed a complete cell working at high speeds (up to 300 m/min), with fine control tension during the whole process and integrating all the latest automated technologies—semi-automated splicing, fully automated slitting positioning, fully automated handling and packaging.
The customer needs were clear: the converting cell must respond to its specific working process while guaranteeing high productivity, operator safety, final product quality and production flexibility.
www.spoolex.com
Teknoweb Converting
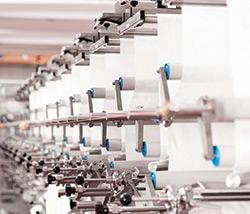
Teknoweb Converting focuses on the development of fully integrated lines for wet wipes converting and packaging. The company says it has always stood for a high degree of innovation and the ability to produce completely integrated systems and individual parts retrofittable on existing machines.
Considering the complexity and range of possible solutions, Teknoweb Converting has pursued a growth strategy implementing expertise and tested solutions to develop integrated systems that positively effect the entire production process.
New generation, fully-integrated lines combine internally-developed and production-proven technology. More complete and versatile machinery provides real benefits to clients thanks to higher operating efficiency; a result of true integration beginning with the project design. Machinery uses economies of scale to reduce the TCO and increase both production speed and the quality of the final product.
Thanks to the recent acquisition by the IMA Group, Teknoweb Converting has strengthened its market leadership in wet wipes and has become the single partner able to provide the best integrated solutions for converting and packaging, along with offering an extensive commercial network that allows clients to quickly bring the latest new products to the market.
Moreover, Teknoweb Converting can offer to clients widely available customer service and a timely and experienced after-sale support organization worldwide.
www.teknowebconverting.com
Teknoweb Materials
Teknoweb Materials, the new player in the world of nonwovens technologies, is a diversified nonwoven system provider of innovative technologies and components for the industry.
Since 2012 it has developed technologies for the production of nonwoven-based substrates, and in July 2015, it became an independent company, Teknoweb Materials S.r.l.
With its eco-friendly Arvell Technology, TKW Materials offers a particularly competitive alternative to existing substrate technologies for the sector of wipes like spunlaced, airlaid, etc.
TKW Materials is very focused on development and innovation and is constantly engaged in the research of new technologies to keep up with the competitive gap without forgetting the sustainable aspect.
High level technologies, products and services are in continuous evolution for the substrates and a diversified range of lines such as Packtek, Airtek, Lamitek, Spintek, Multitek have allowed Teknoweb Materials to become a diversified supplier in the field of nonwovens machinery.
www.teknoweb.it
Tokuden
Tokuden has been an industry leader in providing, energy efficient, environmentally sound, uniform temperature heated rolls. The ultra-high precision thermal processing technology allows control of surface temperatures to 0.5°C.
As far as heating up a roll, a real advantage of induction heating is a very quick heating up of the roll to production temperatures.
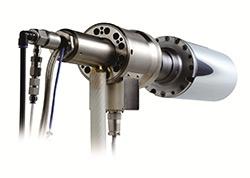
Recently, Tokuden has developed an advance in its roll technology—the Mist Cooled Hybrid Roll, developed for the rapid cooling of the Induction Heated Jacket Roll.
The ‘Hybrid’ Roll uses a special misting system that injects a fine mist of water in the chamber between the coil and the roll shell. The vaporization of the mist transports the thermal energy out of the roll. The primary concept is that a compressed air/mist nozzle is designed on the end of the coil support rod. The mist passes through the coil support rod, passes between the coil and the roll shell, and is discharged.
Main advantages include: means of heating the unit and the means of cooling the unit are independent; mist injection/discharge is without rotary joint; simple design that uses a small quantity of water; appropriate mist conditions can be controlled by the roll surface thermocouple and the rotary transformer.
Tokuden can now provide high and low temperature heated rolls with near perfect temperature uniformity both axially and circumferentially and it can cool the same roll quickly and efficiently.
www.tokuden.com
Trützschler Nonwovens
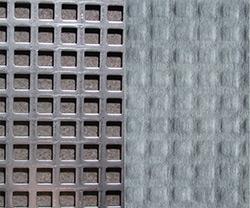
In recent years, Trützschler Nonwovens has heavily invested in further improving its through-air drum technology. Several results include The Streamliner - an innovative drum dryer which passed its acid test in a production line last year. The patented, spiral shaped drying chamber allows for an extremely uniform airflow, high air velocities and a simultaneous reduction in thermal energy consumption. Secondly, the redesigned series of multi-drum dryers now features an intermediate chamber for controlled exhaust air extraction and fresh air supply. Besides reducing heat loss, the chamber homogenizes the airflow inside the dryer for an improved drying quality. The third innovation relates to thermobonding. At ITMA the company will present a structuring shell for the thermobonder drum (patent pending). The results are lofty and fluffy nonwovens with a resilient 3D pattern.
www.truetzschler-nonwovens.de
Valco Melton
Valco Melton is a world-leading manufacturer of adhesive application and electronic monitoring equipment. From sanitary products such as baby diapers, feminine towels and tissues, to medical and surgical products, Valco Melton offers a complete line of nonwoven systems and components for producing a variety of patterns and widths for all hot melt applications associated with most hygiene product manufacturing requirements.
Designed for the high performance and extreme precision required during this delicate manufacturing process, Valco Melton’s range of solutions includes: MITO Multi Pattern Applicator, engineered to allow simultaneous application of different adhesive patterns on the same substrate with only one applicator head; FlexSpray Adhesive Guns with integrated air heater, which achieves a highly accurate adhesive application and reduces investment in additional spare parts inventory; and FlexCoat Slot-Coating Applicators, for continuous or intermittent coatings up to 500m/min and 1200mm lamination widths.
Compact and modular designs for applicators, interchangeable modules and nozzles, provide one of the largest range of hot melt adhesive patterns available to the industry including swirl, meltblown, elastic and slot coat configurations.
Combining more than 60 years of adhesive dispensing experience with industry-specific research and development efforts, Valco Melton continues to provide the nonwovens industry with the latest and most advanced technology to increase production speed, reduce maintenance costs and adhesive usage and maximize flexibility for meeting the changing demands of the market.
www.valcomelton.com
Valmet
Valmet Thru-Air systems for drying, curing and bonding, provide the highest thermal efficiency and lowest temperature and velocity variation available today, according to the company. Valmet Hydro-Dry technology can be found discretely integrated into the most advanced spunlace, spunlaid and other dry/wet laid production lines currently operating.
Now Valmet introduces the next generation dryer/bonder, Advantage Hydro-Dry—newly re-engineered to meet today’s quality, production efficiency and environmental demands.
Honeycomb Roll, with 96% open area, remains at the heart of Valmet’s Advantage. In applications from drying and hydro-entanglement, tensioning and web transfer, Valmet’s shell construction meets the most demanding requirements.
With Advantage Hydro-Dry, users can adjust dwell time, temperature and through air speed to achieve maximum productivity. Unsurpassed temperature uniformity of +/- 1°C (+/- 2°F) assures optimal performance from the web because users achieve accurate bonding temperature at each of the fiber junctions. This allows improved strength-to-basis weight ratio and takes full advantage of the more costly multi-component fibers.
Valmet optimized Thru-Air drying, curing and thermal bonding systems give customers better control over their process, products and profits.
www.valmet.com
VMI Group
VMI is a leader in building automated machines for high efficiency production and packaging of cotton pads. VMI’s ACE 500 sets new standards for productivity and consistent quality, offering manufacturers the natural step-up from ACE 300, the current market leader.
ACE 500 is designed for the high efficiency production of a single product size, while enabling complete size changes to be managed quickly and without disruption. ACE 500 increases productivity by up to 40%, handling 54 bags per minute, even with 100 pads in each bag.
This unit has a 10 square meter footprint, with no special foundation needed. It’s easy to transport, fitting into a single container and can be rapidly installed and commissioned. In operation, it has exceptionally low power and compressed air requirements.
The new machine is already becoming well accepted by industry leaders. Following an early 2014 launch, it’s already up and running at key sites in three different European countries.
ACE 500 is a key example of VMI’s design philosophy, using advanced technology to deliver outstanding levels of automation and ease of use. VMI is an international player in machine automation, a leader in tire building, technical rubber, can-washing and medicine management.
As a global company, VMI provides hands-on support to customers from locations around the world, has real financial stability and is a major innovator, with around 10% of resources devoted to research and development.
www.vmi-group.com
WEKO
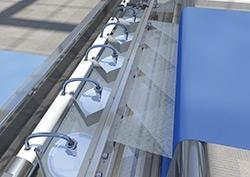
WEKO, Weitmann & Konrad GmbH & Co. KG, from the south of Germany, has been the acknowledged partner for achieving specific functions on a wide variety of materials for over 60 years. At ITMA 2015, WEKO will present in booth E104 in hall 6 the innovative non-contact WEKO-Fluid-Application-System (WFA) and will provide practical information about economic and sustained solutions giving nonwoven and textile materials specific properties.
For nonwovens, a variety of applications exist: PP geotextiles or diaper top sheets that are basically water-repellent and become permeable for water, diapers become absorbent, medical cloth become antimicrobial and automotive filters dirt-repellent. Textiles can be optimally finished with hydrophilic/hydrophobic or oleophilic/oleophobic finishers, softeners and flame retardants as well as antimicrobial agents to provide the desired characteristics.
WEKO offers with its system the solution for everyone who wants to give textiles or nonwovens individual and functional properties through a non-contact fluid application that is gentle to the material and saves resources. Spray disks, rotating at high speeds, the WEKO Rotors apply the liquid via non-contact application to the continuously transported product web. Adjustable sliders form defined spray fans, positioned seamlessly side-by-side, to provide a uniform flow of micro-droplets. The amount required for finishing a wide variety of textiles and nonwovens can be exactly specified.
With the non-contact WEKO-Fluid-Application-System the product web is handled with extreme care since this treatment does not apply any mechanical stress on the fabrics by squeezing between rollers. The high-quality nonwovens and textiles are not strained, and costly post production is made unnecessary.
www.weko.net
Xerium
Xerium recently launched Huycon Air technology for nonwoven airlaid applications. An extension to the globally established Huycon
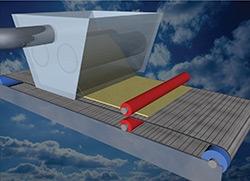
portfolio, Huycon Air incorporates a 2-1/2 layer base fabric with a fine-mesh product side with engineered air-channel-geometry for excellent web formation, retention and release. Huycon Air also incorporates conductive yarns cross-linked by a specially engineered conductive edge sealing providing superb static electricity dissipation. Huycon Air is ideal for the forming and transfer position on all kinds of airlaid machines, delivers non-marking monoplane topography and superior life potential.
www.xerium.com/nonwovens n
A.Celli Nonwovens’ Iridium technology, which made its world premiere in 2013, is developed to offer the highest quality printing onto
This flexo printing technology works web widths that go from 300 mm up to 2800 mm and runs at a speed of up to 1000 m/min, depending on the substrate, and can host from two to 10 color decks.
Among the machine’s main features are automatic pressure adjustment, smart/automatic register, deck washing system, plate and central impression drum cleaning systems and automatic sleeves change.
The company says the success of this new technology is confirmed by another order recently confirmed by an important North American industrial group that has decided to remain anonymous at this time and whose trust in A.Celli Nonwovens technology is the best proof of the Italian group’s winning business strategy.
“Adding this order to our portfolio is not just an important milestone in commercial terms, but also allows us to set the first building block in a recent market for our company—printing,” comments Alessandro Celli, president and CEO of A.Celli Nonwovens. “This order is another strong signal of the wide-ranging versatility and high technological level of A.Celli equipment; a further tangible sign of the answers we are able to supply to our customers’ needs.”
www.acelli.it
Andritz Nonwoven
The original Wetlace process has been developed by Andritz and combines wetlaid and hydroentanglement technologies. It has proven to be ideal for producing flushable wipes from 100% natural and/or renewable raw materials without chemical binders. The material needs excellent dry tensile strength during production. The end-user expects a wet wipe that does not disintegrate before and during use. Once flushed, however, this stability has to disappear completely. These contradictory properties are achieved with innovative wetlace technology that even excels the latest EDANA/INDA flushability standards. Wetlaid production is perfect in terms of achieving excellent web uniformity. Hydroentanglement creates entangling of the fibers without any chemical binders or thermoplastic fibers.
The patterning of flushable wipes is technically very challenging due to the weakness of the flushable substrate, which must have only enough strength for the intended purpose and then be able to disperse completely in water with no residual wet strength. This Andritz patterning solution is also compatible with 100% cellulose-based nonwovens, while other techniques require the use of thermoplastic fibers or chemical binders. It fits perfectly with the sustainable trend in flushable wipes, more and more of which are 100% cellulose-based and contain a majority of wood pulp fibers blended with short artificial cellulose fibers. This powerful and innovative solution for patterning of flushable substrates allows an almost unlimited number of possible patterns.
www.andritz.com/nonwoven
Aurizon Ultrasonics
Aurizon Ultrasonics, a market leader in high-speed rotary ultrasonics, has introduced its patented process of attaching elastic strands to nonwovens, eliminating the costs and issues associated with adhesives. The process supports line speeds up to 2000 feet or 600 meters per minute. Even when line disruptions occur, the ultrasonic system continuously attaches the elastic strands. The end result is elastic strands are secured within the nonwoven substrate, eliminating creep and allowing for maximum product performance. By eliminating glue, the end user experiences a softer feel and greater comfort, the elastic performs better without creep, production lines do not need to shut down due to contamination and the high cost and issues from buying adhesives are eliminated.
Aurizon’s platforms of 20 kHz and 30 kHz rotary ultrasonic systems enable this exciting new capability. Stretch elastic strands and
In addition to elastic strands entrapped in nonwovens, Aurizon can bond many different substrates for many applications for nonwoven products including feature attachment, core bonding, acquisition layers and backsheets. At Aurizon’s facility in Kimberly, WI, trials can be conducted using the customer’s substrates to demonstrate the elastic entrapment and many other ultrasonic bonding capabilities.
www.aurizonultrasonics.com
Diaper Recycling Technology
Diaper Recycling Technology is a technology company solely focused on advanced diaper recycling solutions. Its advanced recycling technology is used within hygiene plants (Adult-Baby-Fem) to reclaim pulp, SAP and plastic from rejected products.
Diaper Recycling’s technology offers hygiene producers superior performance in the following areas: (1) No measurable SAP damage; (2) Best in class purity of PE/PP stream; (3) Best in class purity of SAP stream; (4) Best in class purity of fiber stream; (5) No mixing of raw materials (In-Line system) ensuring zero contamination risk without compromising existing raw material tracking systems; (6) Significantly reduced space requirements within a factory with in-line systems requiring as little as two square meters; (7) Lowest energy in class (8 - 10 KW) due to a revolutionary air-less process; and (8) No impact on installed HVAC/utility loadings.
Diaper Recycling Technology’s combined equipment portfolio including inline and central configurations offers end-users a financially viable business proposition independent of their factory size. The company’s breakthrough technology has been specifically developed to support hygienic producers to achieve environmental targets through the elimination of landfill; burning/incineration; transportation; and all environmental aspects in relation to non-recovered products at product B processing sites.
Diaper Recycling Technology invites hygiene producers to send samples of rejected diapers for initial testing where it can analyze the separation performances allowing detailed project NPV/ RORs to be calculated.
www.diaperrecycling.technology
Diatec
“Evolutionary” is the right expression to describe Diatec’s recent product updates in the converting machinery segment. For over 20 years, Diatec has established itself in the world as a designer and builder of converting machinery for sanitary products, including baby diapers, adult incontinence products, sanitary napkins, panty shields and underpads.
Over the last year Diatec has invested in the development of its technology by developing know-how in disposable products in absorbent food pad production. This new product is used on food packaging to absorb fluids released by meat and fish inside a tray.
Diatec machines can be used as food pad lines with airlaid film or with fluff core through a vacuum forming system, following the customer’s needs.
Diatec technology also developed a new section in laminating lines for the production of high quality laminates up to 3200 mm wide. Three different sealing technologies are offered: ultrasonic, thermal bonding and hot melt. Nonwovens, breathable polyethylene layers, metal coatings, aluminized layers and nettings are usually used in roofing and house construction. The industry studies and technological developments in laminating machines gives customers access to more areas including mobiltech, med-hygienictech and clothtech.
At the same time, Diatec gives its customers the possibility to manage different kinds of raw materials, developing a complete range of spool winding machines and unwinding units for different sizes of materials between 35 and 190 mm at a linear speed up to 650 m/min. Thanks to spool technology, Diatec gives customers convenient packaging for handling, storage and unwinding solutions.
www.diatec.it
Dienes
As a worldwide leading manufacturer for industrial slitting technology, Dienes sets once again a new standard with the innovative DS 6 in the field of knife holders. The DS 6 is the culmination of Dienes’ 100 years experience and know-how from more than 500,000 produced knife holders. Whether it is with manual or semi-automatic operation, the DS 6 impresses with its extremely high stability with very small cutting width from 30 mm and speeds up to 2000 m/min. Adding to this is the worldwide unique cutting pressure positioning, its high longevity, as well as its comprehensive compatibility.
Due to the Dienes honeycomb structure and the long guide bodies, the compact and light design of the DS 6 is extremely sturdy. This means the user can expect the highest accuracy even for small cutting widths, and additional benefits from an increased durability. Furthermore, the DS 6 with its high variability is suited to many sophisticated fields of application, like the processing of paper, foil, nonwoven material and non-ferrous metal foil. Dienes’ unique patented cutting pressure positioning prevents the stick-slip effect with the balanced pressure distribution on the knives.
The fact that its new knife holder is trendsetting on the market is also demonstrated by the other product features of the DS 6. For example, it has an integrated patented adjusting slide, which enables precise and reproducible positioning of the holder towards the bottom knife. The setting of the shear angles is possible in two ways: Conventionally with a plate on the retainer as well as from the front with the Dienes angle supports. The quick-change heads ensure a simplified, timesaving and above all safe removal during maintenance and knife exchange – the knife head and the integrated 360 degree guard can be completely removed and inserted as one unit. Furthermore, this unit can be used in both directions, so that the knife holder is suitable for all feed-ins or can be quickly repositioned. In addition, the knife holder has a forced sequence control for the cutting pressure positioning. Alternatively, however, supply via two separate compressed air circuits for individual adjustment of vertical and horizontal stroke can be selected, so that the cutting pressure can be set even more accurately and reproducibly.
Operation of the DS 6 is intuitive, comfortable and wholly flexible by being usable from all sides. Its design is vibration absorbing and it has comprehensive rust and dust protection for maximum sturdiness. Furthermore, it is compatible with almost all existing slitting systems and is thus ideally suited to easily update existing machines and make them future-proof.
The DS 6 knife holders are available as version M with manual depth adjustment as well as version S with semi-automatic design. The innovative depth adjustment of the DS 6-S provides particular comfort, as it is done step-by-step via a display, which has an integrated teach-in phase. The user thus benefits from even higher accuracy and traceability. At the same time, operating errors are minimized.
www.dienes.de
DiloGroup
DiloGroup offers universal and customized modern nonwovens lines characterized by high capacity, a wide range of applications, ease of operation and excellent maintenance.
Dilo machines are used for production of the complete range of staple fiber nonwovens, including technical applications, automotive and household, medicine and hygiene, decorative felts and floor coverings, but also base material for coatings, composites and high-tech applications.
Dilo installations for the production of geotextiles represent another significant application area. Due to the required strength values and homogeneity in longitudinal, cross and diagonal directions, these installations can include drafting systems before and after preneedling. In Dilo lines the finish needling from both sides is done either in a double needleloom OUG or in two subsequent needlelooms with alternating needling directions. These needlelooms are delivered as universal or high capacity machines with a wide range of stroke frequencies, needle patterns and in working widths exceeding 8.000 mm where required.
For the production of nonwovens used in the car, Dilo offers lines for flat and structured felts. The focus is still on velour, needled on the DI-LOUR machines. For the production of felts used as sound and heat insulation in the car, Dilo machines are often equipped with the DI-DUST system, as these felts are produced with recycled fibers and filling material. DI-DUST is a cleaning system that automatically discharges fiber dust.
A special installation is a line for production of the so-called wheelhouse linings. In this case, two parallel card/crosslapper lines produce the base and the cover felts. The intermediate layer consists of flakes of recycled automotive carpet. This construction results in excellent strength values in the subsequent thermal molding.
Machines and lines for the production of wipes, for needling spunbonds, for medical and hygiene applications represent further challenges that are met by DiloGroup.
DiloGroup also offers nonwoven machines for the needling of metal and inorganic fibers, for fibers used in high performance and high temperature applications as well as machines for tubular felts.
Endless tubes and narrow belts are indispensable technical nonwovens, and not only as paper machine felts. For this application Dilo offers wide needle looms, including the new machine design PMA, which allows single or double sided needling of tubular felts in a range of 2 to 8 meters wide and a circumference up to 9 m. This machine offers new fields of application for example as transport aprons in the textile and food industries, high capacity felts in metallurgy and highly efficient handling techniques provided by endless needlefelt belts.
The demands on the fibers used, in terms of processability, mechanical and textile properties are steadily increasing.
DiloGroup delivers highly efficient production lines from fiber opening to finished roll goods in all working widths. The card capacity which determines the efficiency of the whole line is between 300 and 550 kg per meter of working width depending on fiber type and fineness. Working widths can be more than 5500 mm.
Universal crosslappers of all types have been tuned to the process and work with modern apron technology, highly efficient drives, apron guiding and web guiding technology of the Dilo Webguide system to reach the highest web infeed speeds.
If high web regularity is required, web profile adjustment is realized with a CV1 system installed between card exit and crosslapper entry, controlled by a batt weight measurement system at the end of the line. Longitudinal and cross cutting as well as winding are carried out with subsequent machines. Sometimes an accumulator is used to ensure continuous production without stop during roll change.
DiloGroup engineers special machine systems for all these applications. The components for opening and blending - DON - and for card feeding - MultiFeed – are able to deliver exact webs to the universal card MultiCard even when low weights are processed and the working widths of the card increase.
www.dilo.de
Everwear
Engineered from the knife out, Everwear Knife Rolls, Anvil Rolls, and Cutting Modules have reliability, speed and productivity built into
Machine builders maximize knife life in converting machinery by including an Everwear cutting module intotheir design. Everwear’s design philosophy gives machine builders who are looking for fast, reliable cutting, a low maintenance platform.
Producers with existing lines—whether the need is to replace outdated crush-cut technology or if a new product requires a different module—Everwear will customize a roll or cutting module to help them realize their production goals.
www.everwear.com
Formfiber Denmark
Formfiber Denmark’s patented Spike AirCarding Forming Equipment delivers innovative airlaid nonwovens technology, designed to efficiently form carding length or shorter fibrous raw materials. If a customer’s mat product application requires heavy basis weight mats up to 10,000 gsm, Spike AirCarding is an ideal technology, which can also be used for applications that require a low-basis weight web of 10 gsm or more.
Spike AirCarding formers are being applied to applications with production line speeds of up to 600 mpm for low basis weight webs, to deliver consistently good formation, with short fiber lengths, and superior productivity.
Formfiber Spike AirCarding Technology offers the following commercial advantages: substantially higher forming capacities, per Meter Width of Former; substantially lower forming air consumption; form natural or synthetic fibers with lengths from 1 to 102 mm (4.0”); form and then thermally bond mat products with a finished mat thickness of 400 mm (15.75”) or less; and forming zone widths of 600 to 5000 mm (24” to 197”).
Formfiber Corporate facilities in Denmark provide test plant facilities for its clients’ product development trials.
www.formfiber.dk
Hills, Inc.
Hills, Inc. offers advanced fiber extrusion equipment to produce spunbond and meltblown fabrics, as well as staple fiber and continuous filament materials. Customers use Hills’ extrusion technologies to produce the world’s most complex multi-component fiber cross sections with unprecedented combinations of polymers. Applications include micro fibers with practically any geometry for applications such as filtration, artificial leather, industrial fabrics, and medical uses. The same advanced concepts are being pursued in areas such as carbon fiber precursor, new membrane materials, and high quality textile fabrics using spunbond and staple nonwovens.
Recent Hills programs in nonwovens include the following: Hills spunbond machines use a proprietary high-speed slot aspirator especially suited to high-performance polymer applications such as primary carpet backing, roofing membrane substrate, artificial leather substrate and filtration media. When combined with Hills’ knowledge and unique capabilities in multi-component extrusion technology, the flexibility of Hills’ equipment makes many of these applications possible on the same machine. In addition, Hills has recently introduced patent-pending high loft and high stretch spunbond fabrics with diverse applications including barrier fabrics (such as thermal, acoustic, particle or shock barrier), distribution layers, and MD & CD stretch fabrics without the use of elastic polymers.
Hills meltblown machines employ proprietary die technology to make a variety of high-value products including sub-micron and nano-products as well as multi-component products. Hills’ dies are available with hole counts to 100+hpi, and unlimited capillary L/D which allow custom designs to precisely fit the customer’s polymer and product needs.
In addition to production equipment, Hills laboratory and pilot extrusion machines for the above processes are available and are presently running in many private and public R&D centers around the world.
www.hillsinc.net
ITW Dynatec
ITW Dynatec, a global supplier of hot melt equipment and solutions, is launching the latest Ultra SCS (Strand Coating System).
Coming soon to the market, this revolutionary strand applicator can provide customers with the highest line efficiencies. The new technology features a patent pending design and the most accurate and highest efficiency adhesive coating on strands ever designed to provide customers with the best product performance and less product issues. Its new Ultra SCS also features: next level high-speed technology (up to 1400 pads per minute – 700 MPM); Rapid Change-Over (RCO) design for quick maintenance solutions; Ultra-Stitch and Ultra-Touch nozzle designs to meet multiple requirements; integrated hardened steel elastic strand guides for extended long life; large adhesive orifices for less plugging and higher line efficiency; optimized Ultra-Apex module technology for fastest response and longest cycle life; and lowest usage of adhesive available with total creep strength down to 1% (even as low as 15 grams/linear meter/strand). The Ultra SCS was developed with CFD modeling (Computational Fluid Dynamics).
Recent tests indicated that when new creep data was compared to older data (latest competitors offering), Ultra-SCS performance surpassed expectations. “It blew any other trial creep results out of the water,” says one of ITW Dynatec’s global customers.
www.itwdynatec.com
Jiangsu Yingyang Nonwoven Machinery
Situated in Changsu Province, Jiangsu Yingyang Nonwoven Machinery Co. Ltd. (YY) was founded in 1993 and has grown into one of the largest single site nonwoven machinery makers in the world.
YY covers all variations of nonwovens including opening, lending, carding systems, airlaid systems, needlepunch, thermal bond, spunbond, and vertical lapping and other associated nonwoven systems.
Over 90% of all machinery is made totally in the factory including card cylinders, all machine frames, needle boards and all electrical control systems. Carding machine capacities are up to 1200 kg per hour dependent on fiber types. Needle looms up to 11 meters in width are available as well as multi head looms and Random Velour units. All types of patterning looms are available. For thermal bonding both through air and conventional ovens are made with various airflow systems to suit customers needs. Spunbond units up to 6.2 m width are available.
VLS is the newly patented Vertical Lapping system from YY and this new design gives larger thickness options, higher speeds and lower capital cost than any previous system.
For testing purposes YY has a 3.6 meter needling line available with up to nine looms and a full production size VLS vertical lapping at 2.5 meter width able to run any fiber from customers.
All lines made for the Western markets are totally built and tested with material if required by the customer prior to shipping. In both Europe and North America, YY has both bases holding spare parts as well as locally based trained engineers as and when service is needed.
www.china-nonwovens.com
Kansan
Kansan is continuing to shape the global wet wipes industry’s landscape by developing a new cross fold converting machine, “Flexiwork” with an advanced stacking system and the capacity for up to 600 cuts per minute.
Flexiwork is available with one, two, three or four roll units which work individually yet in complete harmony. With Flexiwork, manufacturers are able to produce two different types of wet wipes in terms of dimension and lotion while at the same time diverting to the two packaging machines.
As a part of the continuous development strategy, the R&D department of Kansan enhanced the Automatic Flow Pack Machine, Acurapack 120, to offer its clients less wastage and more comfort.
Based on client feedback, the equalizer conveyor has been redesigned to minimize packaging and nonwoven material waste while the communication with the converting machine has been improved.
Thanks to the heat distribution in the jaw system homogenization, product with opp mat and pet packaging materials can be produced 10% faster. With enhanced die cut system, knives will last longer and overall, operators are able to operate only with few adjustments.
www.kansanmak.com
Lemtech
Located in Paterson, NJ, for over 20 years, Lemtech has offered polyband web spreader rolls, a wide range of machine parts/assemblies for Lembo equipment and decades of process expertise. The Lemex Expander roll is effective in spreading a wide
www.webspreading.com
Mobi-Air
Mobi-Air, makers of Mobi-Flex, the hygiene industry’s most advanced filtration platform, supports hygiene manufacturers meet their environmental, financial and operational targets through low energy, state-of-the-art flexible equipment solutions. The Mobi-Air equipment platform is still the world’s only true hybrid filter technology offering the best of both bag-house and drum-filter technology and break-through performances to the end-user.
Mobi-Air designed the entire utility and filtration concept from the ground up, putting all of its engineering expertise together into one all new visionary filtration platform. That forward-thinking platform, today, offers the end user: (1) The world’s first flexible hybrid platform with superior drum-filter and dust-collector technologies and no downside; (2) Multi-business unit compatibility with a single equipment platform; (3) Instant mobility with assembly-free vertical start-up; (4) The highest filtration performance in its class; (5) The lowest energy-consumption in its class; (6) The highest safety in its class; and (7) Industry first plug & play modularity.
New hybrid filtration technology offers end-users a “hybrid” filtration solution offering both a compact equipment solution of far smaller size than even latest generation drum filter technology and a wide process window similar to bag-house technology. Mobi-Air’s filtration technology not only provides world class air filtration levels up to 99.999995 @ 0.3 micro; the low energy filtration process provides best in class energy consumption achieved through low pressure-drop hi-surface-area media of up to 1500 square meters; next generation 64BT CFD modeled processes ensuring best in class performance.
Newly developed zero energy plug-in HVAC modules coming later in 2016 create an ideal factory work environment with minimal operating costs.
www.mobiair.technology
Mondon
Downstream in the process area, Mondon installs its TW Series winders, achieving high productivity and first-class results. This turret winder supports two shafts to unload a bobbin while rewinding a new one. The TW Series Winder combines performance with durability and first-rate technology. TW Series technology permits users to wind large bobbins or small rolls thanks to a multi-cut station. TW Series Winder control is performed thanks to a network application with the upstream processing line. Due to its non-stop process, the winder avoids the transition sequences. The accuracy of the TW Series turret winder rotation is a key factor to maintain a very constant tension in the product and to deliver the highest quality reels.
Mondon also manufactures slitter rewinders, short rolls winder and spooling lines, completed with packing and palletizing modules.
www.mondon.com
Nanoval
Nanoval uses a specific effect by which a steadily accelerated gas running in parallel to a liquid stream attenuates it until it splits up by bursting, forming a multitude of continuous filaments in a split-swinging effect. It is also used for disintegrating metal melts to form powders. The atomized powders are increasingly used in three-dimensional printing as in additive manufacturing.
Due to the splitting action, the gas-dynamic Nanoval effect can use large spin nozzles even for fine filaments. Functional particles like
Nanoval has already spun cellulosic webs with up to one-third of wood particles and two-thirds of pulp or waste paper in a Lyocell process improving flushability of wipes. Cellulosic nonwovens can reinforce paper so that both components are biodegradable.
In polymers like polypropylene, fine filaments in the micro-nano range can be produced to nonwovens for filters at high retention and low pressure drop.
The process and equipment are robust and energy consumption compared to conventional systems like meltblown is lower, throughput in kg/m*h is higher.
www.nanoval.de
Nordson Corporation
Nordson continues to help disposable hygiene product manufacturers cost-effectively produce high-quality, high-performance baby diapers, adult incontinence garments and feminine hygiene items. Enabling variable material dispense capability – different add-on weights or patterns from a single applicator in a single pass – is one tool to help improve product quality and reduce material costs. Nordson offers several variable dispense applicators to meet different manufacturing needs.
Using Nordson Allegro and/or SureWrap elastic attachment nozzles further optimizes adhesive use and improves product quality. And, Duet applicators incorporate Nordson’s patented Universal clamping feature for quick, easy nozzle changes.
Trio triple shim applicators produce patterns with different add-on weights in both machine and cross-web directions from a single applicator. Additionally, Trio applicators can apply multiple materials simultaneously and dispense coating-on-coating patterns. This flexibility with variable add-on weights and patterns helps disposable hygiene product manufacturers meet varying functional and sensory performance needs more cost- and production-efficiently.
Production efficiency delivered by Nordson’s variable dispense applicators is further enhanced with quick-exchange components, such as filters and modules, that simplify maintenance and increase production up-time.
www.nordson.com/nonwovens
Optima Packaging Group
The new Optima LS Stacker processes up to 1600 units per minute and forwards them in stacks of up to 100 units to the downstream packaging machines. This is quite an achievement considering the weight of the bundled bed liners, incontinence products or other nonwoven stacks to be transported through the machine –up to 5kg per bundled stack.
Due to the high speeds, considerable g-forces are exerted on the product mover and the guides of the Optima LS Stacker. These forces are compensated by way of the inherent magnetic fields of the linear drives. With the new drives and output, the stacker enters the domain of diaper packaging speeds and can therefore also find application there.
Newly designed cassettes on the Optima LS Stacker take up the products. Instead of base plates, the new cassettes use intermeshing forks. These can be adjusted as needed to suit the pitch of the freely adjustable mover. Format changes can therefore be made “on the fly” at the push of a button.
A further feature of the new Optima LS design is the so-called tightening function. The product stack which is in the cassette is held and calibrated for a specific force.
The new mover cassettes are compatible with existing packaging processes—the typical “standard” transfer is unaffected. The new Optima LS Stacker can be intelligently combined with various packaging machines supplied by Optima nonwovens.
www.optima-packaging-group.de
Osprey Corporation
Osprey Corporation has implemented industrial level remote connectivity into its electrical control systems that allows remote programming and monitoring of ethernet and serial connected devices from its headquarters in Atlanta, GA, or from anywhere in the world. Osprey can assist with basic commissioning of the equipment, troubleshooting equipment in operation or major system changes that may arise during the lifecycle of the equipment. This can reduce the time and travel expenses related to the service and support of its equipment installed globally.
A DIN rail mounted industrial router communicates with ethernet and serial connected automation devices inside the control panel including PLCs, HMIs, motor controls, etc. To make these devices remotely accessible, the router makes a secure outbound connection to a cloud based Virtual Private Network (VPN) server. Osprey can then connect to the cloud-based server, which verifies credentials and completes an encrypted VPN pathway between the Osprey engineer and the connected equipment.
An optional GSM modem and service from a cellular internet provider allows locations without an available hardwired network connected to the internet to also benefit. Other optional features include historical data logging for troubleshooting and custom web interfaces for remote monitoring of equipment by authorized plant personnel.
www.ospreyfilters.com
ProJet
ProJet BV applies decades of experience to deliver process belt cleaning solutions worldwide. Consistent belt cleanliness applies to all companies producing nonwoven roll goods with airlaid, drylaid, meltblown, spunbond, spunlaced or wetlaid nonwoven forming technologies.
ProJet “PowerCleaner” advantages include: high-pressure (up to 5,100 psig) and low water volume (about 0.26 gpm per nozzle) to efficiently clean process belts without chemical additives; no contaminated water mist is expelled into the process area; belt cleaning and drying is accomplished simultaneously; contamination is collected and transferred to a save all pan with a vacuum pick up system without an auxiliary vacuum pump; and automatic nozzle cleaning, head flushing, and system maintenance is accomplished without interrupting continuous production.
ProJet provides complete, turn-key fabric cleaning solutions, which include: mechanical and electrical control engineering services; customized solutions for each unique belt cleaning application; door to door delivery services; on-site installation supervision services are provided by ProJet Engineers; and best in the business customer service after the sale.
www.pro-jet.nl
Rando Machine Corporation
Rando Machine Corporation is an expert in airlaid technology and web formation. Its latest technology helps manufacturers improve
From soft to hard edge trimmings, its new Rando Waste Shredder/Refiberizer is outfitted with state-of-the-art technology to help break down material into small, uniform tufts to be reintroduced to production and contribute to a finished product.
Discarding the material that is trimmed from the finished product takes a heavy expense on organizations as they pay outside services to remove and dispose of the excess material. Purchasing a Rando Waste Shredder/Refiberizer eliminates this need by providing a manufacturer the opportunity to reclaim and repurpose the excess “skeletons” back into the finished product. The Rando Waste Shredder/Refiberizer will not only save money by removing this expense, but also provide an additional, usable source of reclaimed fiber material that can be reintroduced into the production line accordingly reducing overall fiber costs. Therefore, our new machine provides an attractive solution for organizations looking to save money and improve environmental practices.
After exceeding expectations during its pilot program and operating at full capacity for a major manufacturer, Rando is proud to announce that it will be adding this machine into its laboratory line in the near future.
www.randomachine.com
Sandvik Hyperion
Sandvik Hyperion is a global company specialized in hard and super-hard applied materials, belonging to the Sandvik Group. Within the nonwovens market, Sandvik Hyperion is a leading company in rotary cutting solutions for the hygiene business. The high quality of its products, combined with the engineering service, customer assistance and global/local service, make it easy to find the right solution for customers’ needs.
In the continuous effort to stay closer to its customers and serve them locally, Sandvik Hyperion is opening its new maintenance center in China, located in the Sandvik factory of Wuxi. The maintenance center is aimed to serve the Asian market for after sales service needs, like rotary cutter inspection and resharpening, anvil regrinding and frame maintenance. The Sandvik maintenance center in China adds to the established centers in the U.S., Brazil and France.
The hygiene business is evolving to higher converting line speeds, more difficult raw materials to cut, innovative manufacturing processes, new cutting profiles which all require reliable cutting solutions. Sandvik Hyperion is able to assist customers with a full range of services to ensure stable and long lasting performance. Particularly in the vibration control area, Sandvik Hyperion, in partnership with Sandvik Teeness, has developed and patented a tuned mass damper. It consists of a passive dampening system working at a pre-set frequency range which dampens the vibrations of moving parts of a cutting unit, maximizing their lifetime. Field test results show cutter lifetime multiplied by two and anvil lifetime by three.
www.hyperion.sandvik.com
Schober Technologies
Schobertechnologies is launching the redesigned SL106 - Sheetline (Rotary Sheetfed Converting Machine). The SL106 is equipped with a high-speed belt stream feeder combined with a well proven suction head technology, a heavy duty die cutting station as well as a robot-automated stacking, counting and piling system.
Most of the features, which have proven their efficiency in the web-fed die cutting machine such as the pre-set and calibrated cutting pressure adjustment, high-precision bearing assemblies and housings for low temperature running, vibration-free design and micrometric die wear compensation adjustment (GCS), have been integrated in the die cutting station of the SL106.
In addition, the converting station is equipped with a vacuum controlled magnetic cylinder tool and the new and unique gripper sheet guiding system, which ensures high-precision finishing of pre-printed sheets. The products are separated from the matrix immediately after the cutting process and redirected to the robot-automated stacking unit by a conveyor belt.
Magnetic dies guarantee the shortest set-up time as well as the highest productivity even for short runs.
The unique design of the die cutting station and its accessibility allows the possibility to integrate additional finishing tools at a later stage. The robot-automated stacking system is capable of handling different types of products combined within the same printing image. These can be heavily nested and can be a combination of large and small products.
Product specific fast exchangeable pick-up plates collect products at synchronized speed and stack them non-stop into a twin piling cassette system.
The SL106 is designed for a sheet size of 106 x 78 cm and a foil thickness starting at 50mμ. High functionality and availability, flexibility and accuracy are the characteristics of this high performance production machine.
www.schobertechnologies.de
Schott & Meissner
German machinery manufacturer Schott & Meissner, an expert in the field of “heat treatment” for the nonwoven and composites industries since 1986, now has two different kinds of machinery for producing ADL products on the market—the ADL-Air Trough Drum and the ADL-Speedliner single belt oven.
According to Schott & Meissner, both machines have their own advantages and meet the performance demands of each customer. The ADL-Air-Trough DrumDryer is available in various drum sizes up to 3m, with a very high air velocity and the company’s innovative air distribution system. These highly developed systems guarantee its customers excellent temperatures and air speeds over the complete width and treatment length. The arrangement of this Omega-type is space-saving and especially for light webs up to 100 gsm webs designed.
ADL-Speedliner is the new machine in Schott & Meissner’s scope of supply. This oven type is not limited by the treatment length of a drum diameter and can be increased in modular form to reach line speeds up to 400 meters per minute. This type of ADL-machine is also for higher web weights, and has the advantage of a very soft hand, due to the high air volume at a low operating pressure. This is all rounded out by a new guiding and air flow system.
To protect the environment and reduce energy costs, the Schott & Meissner ADL-Speedliner can be equipped with a Heat-Recovery System, which allows the customer to save not only energy but also increase the performance of the oven.
The company says both systems are already producing materials all over the world and satisfy their customers and the demands on the end users.
www.schott-meissner.de
Shemesh Automation
Shemesh Automation Wet Wipes is a world-leading manufacturer of round wipes packaging machinery. With over 25 years experience, it is uniquely positioned to offer dedicated expertise and support to the wet wipes market and provides innovative, high quality solutions not found elsewhere.
Products supported include rigid canister or bucket packs and ready-made/pre-made flexible pack bags, stand up pouches & refills. Equipment modules manufactured include feeders, wipes canister loaders, liquid fillers, sealers, cappers, labelers, form fill & seal case packers and full quality control.
Rigid packages include inline turnkey systems. Starting at 60ppm and running up to 200ppm these systems feature the company’s flagship canister loader—the SAS Series. Officially launched in 2013 and with more than 15 units already installed globally, the SAS Series is the only truly proven vertical nonwovens donuts canister stuffer in the world.
The Xpander and Xpander Plus round wipes packers offer an all-in-one Monoblock design. These innovative systems boast the only technology in the world to date capable of delivering complete, 30-35ppm, round wipes packing all in a strikingly small footprint. The Xpander serves both entry-level operators and high volume wet wipes manufacturers looking to diversify production.
Flexible packages include the Fortress, which is designed to create flexible packs from a master roll of film. It forms the bag, loads the wipes, fills, seals and discharges the finished product. The Fortress provides two levels of efficiency through the economic use of raw materials and savings gained from process automation.
The SAW-MB200, an all-in-one monoblock packer, is designed for ready-made bags. With the SAW-MB200, bags are stacked in a magazine and fed into a rotary index table where they are opened, loaded with wipes, liquid filled, sealed and discharged.
The Fortress and SAW-MB200 are made to service the jumbo rolls, standard wet wipes in flexible packs and refill markets.
www.sawetwipes.com
Sonobond Ultrasonics
Sonobond Ultrasonics’ units seal, sew, and trim—all in one quick pass. Their high-frequency vibratory waves produce safer medical garments and disposable items with bonded edges and secure seams without stitch holes, glue gaps, fraying or unraveling to meet tough OSHA regulatory requirements for barrier seams. No thread, glue, or other consumables are required. Sonobond manufactures a wide variety of machines that handle multiple nonwoven and synthetic material assembly applications.
The SeamMaster Ultrasonic Sewing Machines are a complete line of continuous-bonding models that operate like traditional sewing machines. The line includes general purpose units, table-mounted cutters/sealers, and modules for OEMs. All units utilize a patented rotary operation, where both horn and pattern wheel rotate at the same time, providing ultra-reliable and soft-to-the-touch seams achieved up to four times faster than with conventional sewing machines and 10 times faster than with adhesive methods.
The SeamMaster High Profile Ultrasonic Sewing Machine is now the most popular unit in the line due to its large pattern wheel, high clearance and ability to accommodate bulky materials and hand-guided operations with tight tolerances and curves. In fact, this machine is used by most major body armor manufacturers to seal the outer nylon shell of ballistic vests and produce a bond so reliable that it complies with National Institute of Justice submersion test standards to protect the inner layer of ballistic-resistant materials from water leaks.
The RingMaster award-winning machine ultrasonically attaches filter bags to plastic collars. Strong, reliable bonds are completed in less than 10 seconds, eliminating stitch holes that cause leaks and thread that can get caught in pumps. Fast, easy re-tooling accommodates varying bag sizes and collar diameters. This semi-automatic unit produces up to 250 bags per hour, while the manually operated version, the Filter Collar Bonder machine, will produce up to 80 bags per hour.
SureWeld PlungeBonder machines handle larger, difficult-to-bond and multi-layer materials. Models seal ends of filter bags and produce box-style filters. Custom tooling enables straps made of coated synthetic material to be bonded within the seam of a ballistic vest’s outer shell without compromising the integrity of the ultrasonically-sealed shell so the body armor continues to comply with current NIJ submersion requirements.
SureCut Ultrasonic Cutters/Sealers provide one-step cutting and sealing of ribbons, trims and labels, without frayed edges. They are available in hand-held models for single cuts or for loom-mounted operations.
In addition to the medical and body armor items, these Sonobond machines assemble HEPA-rated filters, industrial and commercial vacuum bags, oil absorbers and oil containment booms, automobile air filters, and various filtration products used by the chemical/pharmaceutical, environmental, food/beverage and manufacturing industries. They also assemble geotextiles for the agricultural industry.
Sonobond provides free sample bonds using a company’s own material and then recommends the appropriate machine for the application. Units can be customized to specific requirements.
www.sonobondultrasonics.com
Spoolex
Since 1955, Spoolex has been engineering and manufacturing quality converting equipment for various industries. After having
Spoolex has, through its worldwide recognized brands Calemard and Decoup+, real expertise in slitting, rewinding/spooling and ultrasonic splicing. Today, to meet the needs of high productivity, operator’s safety and line flexibility, Spoolex’s R&D Department has developed several automated solutions around these brands’ know-how to provide complete cell from mother handling to final product packing.
Spoolex’s latest global solution commissioned is a complete converting cell that was engineered and assembled 100% in house. This cell merges all needs of a cutting workshop but with only one control station. The solution developed combines four modules—splicing, slitting, handling, packaging—designed and automated to reduce operator handling, to increase line speed and capacities and to handle 30 different products and a wide range of pancakes sizes.
To meet the customer needs of automation adaptability and versatility, Spoolex has designed a complete cell working at high speeds (up to 300 m/min), with fine control tension during the whole process and integrating all the latest automated technologies—semi-automated splicing, fully automated slitting positioning, fully automated handling and packaging.
The customer needs were clear: the converting cell must respond to its specific working process while guaranteeing high productivity, operator safety, final product quality and production flexibility.
www.spoolex.com
Teknoweb Converting
Considering the complexity and range of possible solutions, Teknoweb Converting has pursued a growth strategy implementing expertise and tested solutions to develop integrated systems that positively effect the entire production process.
New generation, fully-integrated lines combine internally-developed and production-proven technology. More complete and versatile machinery provides real benefits to clients thanks to higher operating efficiency; a result of true integration beginning with the project design. Machinery uses economies of scale to reduce the TCO and increase both production speed and the quality of the final product.
Thanks to the recent acquisition by the IMA Group, Teknoweb Converting has strengthened its market leadership in wet wipes and has become the single partner able to provide the best integrated solutions for converting and packaging, along with offering an extensive commercial network that allows clients to quickly bring the latest new products to the market.
Moreover, Teknoweb Converting can offer to clients widely available customer service and a timely and experienced after-sale support organization worldwide.
www.teknowebconverting.com
Teknoweb Materials
Teknoweb Materials, the new player in the world of nonwovens technologies, is a diversified nonwoven system provider of innovative technologies and components for the industry.
Since 2012 it has developed technologies for the production of nonwoven-based substrates, and in July 2015, it became an independent company, Teknoweb Materials S.r.l.
With its eco-friendly Arvell Technology, TKW Materials offers a particularly competitive alternative to existing substrate technologies for the sector of wipes like spunlaced, airlaid, etc.
TKW Materials is very focused on development and innovation and is constantly engaged in the research of new technologies to keep up with the competitive gap without forgetting the sustainable aspect.
High level technologies, products and services are in continuous evolution for the substrates and a diversified range of lines such as Packtek, Airtek, Lamitek, Spintek, Multitek have allowed Teknoweb Materials to become a diversified supplier in the field of nonwovens machinery.
www.teknoweb.it
Tokuden
Tokuden has been an industry leader in providing, energy efficient, environmentally sound, uniform temperature heated rolls. The ultra-high precision thermal processing technology allows control of surface temperatures to 0.5°C.
As far as heating up a roll, a real advantage of induction heating is a very quick heating up of the roll to production temperatures.
The ‘Hybrid’ Roll uses a special misting system that injects a fine mist of water in the chamber between the coil and the roll shell. The vaporization of the mist transports the thermal energy out of the roll. The primary concept is that a compressed air/mist nozzle is designed on the end of the coil support rod. The mist passes through the coil support rod, passes between the coil and the roll shell, and is discharged.
Main advantages include: means of heating the unit and the means of cooling the unit are independent; mist injection/discharge is without rotary joint; simple design that uses a small quantity of water; appropriate mist conditions can be controlled by the roll surface thermocouple and the rotary transformer.
Tokuden can now provide high and low temperature heated rolls with near perfect temperature uniformity both axially and circumferentially and it can cool the same roll quickly and efficiently.
www.tokuden.com
Trützschler Nonwovens
www.truetzschler-nonwovens.de
Valco Melton
Valco Melton is a world-leading manufacturer of adhesive application and electronic monitoring equipment. From sanitary products such as baby diapers, feminine towels and tissues, to medical and surgical products, Valco Melton offers a complete line of nonwoven systems and components for producing a variety of patterns and widths for all hot melt applications associated with most hygiene product manufacturing requirements.
Designed for the high performance and extreme precision required during this delicate manufacturing process, Valco Melton’s range of solutions includes: MITO Multi Pattern Applicator, engineered to allow simultaneous application of different adhesive patterns on the same substrate with only one applicator head; FlexSpray Adhesive Guns with integrated air heater, which achieves a highly accurate adhesive application and reduces investment in additional spare parts inventory; and FlexCoat Slot-Coating Applicators, for continuous or intermittent coatings up to 500m/min and 1200mm lamination widths.
Compact and modular designs for applicators, interchangeable modules and nozzles, provide one of the largest range of hot melt adhesive patterns available to the industry including swirl, meltblown, elastic and slot coat configurations.
Combining more than 60 years of adhesive dispensing experience with industry-specific research and development efforts, Valco Melton continues to provide the nonwovens industry with the latest and most advanced technology to increase production speed, reduce maintenance costs and adhesive usage and maximize flexibility for meeting the changing demands of the market.
www.valcomelton.com
Valmet
Valmet Thru-Air systems for drying, curing and bonding, provide the highest thermal efficiency and lowest temperature and velocity variation available today, according to the company. Valmet Hydro-Dry technology can be found discretely integrated into the most advanced spunlace, spunlaid and other dry/wet laid production lines currently operating.
Now Valmet introduces the next generation dryer/bonder, Advantage Hydro-Dry—newly re-engineered to meet today’s quality, production efficiency and environmental demands.
Honeycomb Roll, with 96% open area, remains at the heart of Valmet’s Advantage. In applications from drying and hydro-entanglement, tensioning and web transfer, Valmet’s shell construction meets the most demanding requirements.
With Advantage Hydro-Dry, users can adjust dwell time, temperature and through air speed to achieve maximum productivity. Unsurpassed temperature uniformity of +/- 1°C (+/- 2°F) assures optimal performance from the web because users achieve accurate bonding temperature at each of the fiber junctions. This allows improved strength-to-basis weight ratio and takes full advantage of the more costly multi-component fibers.
Valmet optimized Thru-Air drying, curing and thermal bonding systems give customers better control over their process, products and profits.
www.valmet.com
VMI Group
VMI is a leader in building automated machines for high efficiency production and packaging of cotton pads. VMI’s ACE 500 sets new standards for productivity and consistent quality, offering manufacturers the natural step-up from ACE 300, the current market leader.
ACE 500 is designed for the high efficiency production of a single product size, while enabling complete size changes to be managed quickly and without disruption. ACE 500 increases productivity by up to 40%, handling 54 bags per minute, even with 100 pads in each bag.
This unit has a 10 square meter footprint, with no special foundation needed. It’s easy to transport, fitting into a single container and can be rapidly installed and commissioned. In operation, it has exceptionally low power and compressed air requirements.
The new machine is already becoming well accepted by industry leaders. Following an early 2014 launch, it’s already up and running at key sites in three different European countries.
ACE 500 is a key example of VMI’s design philosophy, using advanced technology to deliver outstanding levels of automation and ease of use. VMI is an international player in machine automation, a leader in tire building, technical rubber, can-washing and medicine management.
As a global company, VMI provides hands-on support to customers from locations around the world, has real financial stability and is a major innovator, with around 10% of resources devoted to research and development.
www.vmi-group.com
WEKO
For nonwovens, a variety of applications exist: PP geotextiles or diaper top sheets that are basically water-repellent and become permeable for water, diapers become absorbent, medical cloth become antimicrobial and automotive filters dirt-repellent. Textiles can be optimally finished with hydrophilic/hydrophobic or oleophilic/oleophobic finishers, softeners and flame retardants as well as antimicrobial agents to provide the desired characteristics.
WEKO offers with its system the solution for everyone who wants to give textiles or nonwovens individual and functional properties through a non-contact fluid application that is gentle to the material and saves resources. Spray disks, rotating at high speeds, the WEKO Rotors apply the liquid via non-contact application to the continuously transported product web. Adjustable sliders form defined spray fans, positioned seamlessly side-by-side, to provide a uniform flow of micro-droplets. The amount required for finishing a wide variety of textiles and nonwovens can be exactly specified.
www.weko.net
Xerium
Xerium recently launched Huycon Air technology for nonwoven airlaid applications. An extension to the globally established Huycon
www.xerium.com/nonwovens n