Tara Olivo, associate editor08.06.15
Used to prevent infection and maintain hygiene, medical nonwovens encompass everything from surgical drapes and gowns to woundcare dressings and adult incontinence items and are positioned for significant growth in the upcoming years.
According to a recent report from Allied Market Research, Portland, OR, the global medical nonwoven disposables market is projected to record a 9.6% CAGR (compound annual growth rate) during the 2015-2020 time period and will reach $10.6 billion globally by 2020.
The report says surgical nonwoven products had a 54.8% marketshare last year and would continue to lead the market through 2020. Incontinence products will have the fastest growth during 2015-2020 due to the rise in the aging population, as well as personal hygiene awareness and increase in per capita healthcare spending.
Among other findings in the report are that the increasing occurrence of hospital-acquired infections (HAI) would contribute to the growth of the nonwoven disposables market. Other growth drivers include stringent regulations for hygiene and the increase in the number of people with incontinence.
North America is the largest market for these products, according to the report, but Asia-Pacific is expected to surpass the Western continent by 2020 due to growing medical tourism and the rise in spending on “sophisticated hospitality services.” In the LAMEA (Latin America, Middle East and Africa) region, the demands for medical nonwoven products is up “due to the high prevalence of infectious diseases, interventions from the government through awareness campaigns and large-scale public initiatives for maintaining hygienic environment.”
Serkan Gogus, CEO of Mogul, a Turkish nonwovens producer, agrees that medical is a growing area for nonwovens, especially in emerging markets, and as income levels increase and health consciousness rises, demand for such products will go up. “In developed countries, new product developments that include the usage of nonwovens, in addition to current use, is key,” he says.
When it comes to HAIs as a growth factor, Medline, a manufacturer and distributor of healthcare items, sees the importance of nonwovens when it comes to prevention. “Nonwovens certainly have a central place in helping act as a barrier against healthcare acquired infections,” says Barbara Connell, MS, MT(ASCP)SH, VP Clinical Sales, Medline. “As more new technologies are being introduced, hospitals now have a cost-effective way to help in the fight against HAIs in the form of disposable nonwovens.”
Among Medline’s products used for infection prevention are personal protective equipment and disposable cleaning and disinfecting wipes.
In addition to these items, Medline also produces surgical drapes and gowns and sterilization wraps using nonwovens. “We’re always on the lookout for new fabrics and technologies, but, right now, nonwovens are the industry standard for many categories, especially in the operating room and in personal protective apparel,” says Medline’s Mark Chua, senior product manager, Proxima. “Customers are always looking for more value and performance, and Medline strives to have the strongest and most protective fabrics in the industry, while keeping user comfort in mind.”
The company has been also experimenting with the colors and looks and feel to its fabrics. Chua says this is because patient satisfaction is becoming “a more visible statistic in hospitals.” In addition to traditional surgical blue nonwovens, they also use fabrics with patterns like camouflage, pink ribbon and its new pink surgical gown line where a portion of proceeds are donated to the National Breast Cancer foundation.
Cardinal Health, a supplier of medical-surgical products such as surgical drapes, surgical gowns, face masks, sterilization wraps and incontinence items, finds that nonwovens are a reliable material for broad usage in the healthcare market and is seeing growth in several categories.
“We are seeing small shifts in surgical drapes and gowns due to shifts in procedure types,” says Debra Schotz, senior vice president and general manager of Medical Consumables at Cardinal Health. “Some areas, like the isolation gown market, continues to grow steadily, while other areas, such as the incontinence market, are seeing growth in part due to the aging population.”
Schotz says nonwovens offer several benefits in the medical field. “Nonwovens technology offers flexibility in softness, color and barrier levels, which allows for application to various medical product categories,” she explains, adding that they’re also cost effective disposable products, they provide consistent protection and performance, and they lower the amount of lint compared to previous products.
Jacob Holm to Expand Products Under Sontara
With the acquisition of DuPont’s Sontara business last year, the Jacob Holm Group has gained exposure to healthcare markets. Sontara offers surgical gowns, drapes, tape bases and other wound care products—specializing in soft and comfortable solutions that are lightweight, lower lint and specially treated.
“Healthcare is a key market segment for our Sontara business,” says Martin Mikkelsen, CEO, Jacob Holm Group. “Sontara has maintained its solid reputation of high quality and high performance, especially in the operating room, and is well-known in the industry for extreme softness, comfort and breathability. With the Jacob Holm innovation bench strength and our newly implemented Sontara Product Development Team, we will further advance our position in healthcare.”
According to Mikkelsen, the new team is currently working on expanding Sontara into select medical applications and has plans to launch several new products within the year. Although spunlace has lost share over the years in the healthcare market to spunmelt, Mikkelsen sees a lot of value in the material.
“Spunlace continues to be used in a variety of healthcare applications. The unique properties of Sontara and the flexibility to use a broad variety of fiber technologies in manufacturing allow for a wide range of high-performing, customized fabrics for many diverse applications.”
Among the advantages of Sontara are comfort, breathability and soft drapeability, which Mikkelsen says are challenging to replicate in a spunbond. Also, since Sontara is made using cellulose, it offers environmentally sustainable qualities, which are becoming increasingly important in the healthcare market.
Halyard Health Officially Debuts
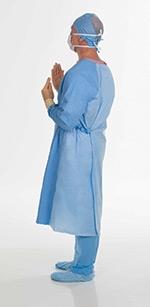
Halyard’s new Aero Blue Performance Surgical Gown is soft and lightweight.
Last year Kimberly-Clark announced that its medical arm, Kimberly-Clark Healthcare, was being spun off to form an independent company, which was renamed Halyard Health. Halyard became an independent public company in November 2014.
According to Mike Tuck, vice president, Global Product Supply, Halyard Health, the $1.7 billion medical technology company is now able to invest to drive its long-term growth, which it couldn’t do when it was part of a much larger company where capital was returned to K-C.
As its own company, Halyard Health offers a broad range of medical products including surgical gowns, surgical drapes, sterile wrap, surgical masks and apparel, which are manufactured using its internally produced nonwovens. “Nonwovens technology provides protection from liquids while remaining breathable,” Tuck explains. “These fabrics are ideal for use in hospitals because they provide a higher level of protection and enhanced sterility over cotton, linen, and paper-based products.”
In 2014, the company launched the Halyard Aero Blue Performance Surgical Gown. Tuck says the new product is soft and lightweight and claims that the gown is four times more protective than comparable surgical gowns. “This product represents a significant innovation in perioperative protection,” he says.
Halyard also launched product improvements to its sterilization solutions. One of these innovations includes Smart-Fold, a sterilization packaging engineered to protect heavy trays and loaner sets from tears and cuts in handling.
Freudenberg Prioritizes Advanced Wound Care
Freudenberg Performance Materials, which produces nonwovens for advanced wound care, traditional wound care, stoma care and transdermal solutions in the medical field, has recently focused on the development of solutions for advanced and active wound care.
“The fastest growth is being seen by hydroactive and superabsorbing nonwovens as well as by antimicrobially-treated nonwovens and foams,” says Marcus Simon, business segment manager medical, Freudenberg Performance Materials.
In fact, on January 1, Freudenberg acquired Polymer Health Technology Ltd. (PHT) of Ebbw Vale, U.K., a leading specialist of polyurethane foams for advanced wound care. Hydrophilic foam solutions play an increasingly important role in modern advanced wound care. Current global market share lies at over 40%.
“With the acquisition of Polymer Health Technology, Freudenberg Performance Materials will be able to offer our globally-active customers additional innovative solutions for modern wound management,” Simon adds.
PHT’s hydrophilic polyurethane foam systems absorb wound exudate, creating an ideal environment for wound healing, according to Simon, and these are special features customers are seeking in wound care products. “They protect the wound from drying out, from cooling and ensure an unhindered exchange of gases and water vapor, thereby accelerating the wound healing process.”
For ostomy solutions, customers are looking for odor absorbing materials and membranes. Simon says Freudenberg’s high performance ostomy carbon filter—used in a pouch—is engineered to remove malodors, which in turn improves quality of life.
Investments in the Middle East
In May, Advanced Fabrics (SAAF) of Saudi Arabia, an innovator in the medical and hygiene markets, added a second treatment line for alcohol repellent and anti-static products. The new line is close to full production, and will give the company a treatment capacity of over 1000MT per month, according to Ian Disley, general manager.
“SAAF added a second treatment line due to demand from customers and a belief that we could better optimize quality and efficiency by having the treatment line next to the new fabric production line in our Rabigh facility,” Disley says. “The new state-of-the-art Reicofil line has enabled us to take our well-known Medalon product further to produce MedalonS, with enhanced softness. As a leading supplier worldwide of treated barrier fabrics we believe the best results are achieved by developing the base fabric and treatment process together.”
Another investment this year came from Turkish nonwovens producer Bayteks, which produces PP spunbond, SMMS, PET spunbond and meltblown fabrics. The company installed a hotmelt lamination machine at the end of April.
“With this one we are targeting the medical sector for the drapes, gowns, and all the surgical, single-use disposables,” says Mehmet Bozkan, director of sales and marketing, adding that the medical market is the company’s main target right now.
“Medical is growing for SMMS fabrics. We are already supplying our material for medical companies, so it’s a complementary product for us, and an added value addition to our product,” he adds.
PLA Meltblown Expert Offers New Technology
Biovation, a technology design and manufacturing company that produces advanced, nonwoven fiber products with integrated antimicrobial properties, is using its expertise in the medical market.
In March, the company launched the BioArmour Blood Pressure Cuff Shield to mitigate the spread of infectious pathogens from blood pressure cuffs. According to the company, this first-in-class medical product offers a multi-use barrier for prevention of hospital acquired infections.
The BioArmour Blood Pressure Cuff Shield is a disposable antimicrobial hygienic barrier that attaches to the blood pressure cuff to prevent direct contact of the cuff with the patient’s skin. The latex-free shield material—a PLA meltblown nonwoven—is composed of a sustainable biopolymer impregnated with antimicrobial and antifungal agents to mitigate the propagation of a wide spectrum of pathogens in controlled release fashion. Contaminant pathogens—including MRSA, VRE, c. difficile and others—are mitigated by the blood pressure cuff shield, allowing for multi-patient use over a 24-hour period. Biovation worked with antimicrobial solutions specialist Sciessent to develop the antimicrobial technology.
“There is nothing like it [in the market],” says Kerem Durdag, CEO of Biovation. “It’s first in its class in terms of approvals, and also as a product. The only equivalent product that’s on the marketplace is a plastic disposable blood pressure cuff meant for one-time use. This would be the first nonwoven, multi-patient, multi-use, multi-pathogen with an FDA 510k Class 2 medical device approval. The plastic disposable cuff is not FDA 510k Class 2 approved.”
While the cuff shield is available in the European Union (registered a CE Class I medical device), Canada and all non-U.S. markets, the product is still awaiting FDA approval. Durdag expects the product to be available in the U.S. in the fall of 2016.
The company has also been hard at work on an advanced wound care dressing, which is also going through the FDA approval process. An all PLA biopolymer nonwoven “back-bone” construction with a proprietary gel-cast coating with wound healing agents and antimicrobials as a non-adherent wound contact surface, Durdag says it will be able to be used on low to medium exudate wounds. The dressing will have comparable benchmark performance to current foam, hydrocolloid and alginate based products and be available in several formats with pricing significantly lower than present incumbent solutions.
The advanced wound care product is expected to be available in the U.S. and EU by mid-2017.
According to a recent report from Allied Market Research, Portland, OR, the global medical nonwoven disposables market is projected to record a 9.6% CAGR (compound annual growth rate) during the 2015-2020 time period and will reach $10.6 billion globally by 2020.
The report says surgical nonwoven products had a 54.8% marketshare last year and would continue to lead the market through 2020. Incontinence products will have the fastest growth during 2015-2020 due to the rise in the aging population, as well as personal hygiene awareness and increase in per capita healthcare spending.
Among other findings in the report are that the increasing occurrence of hospital-acquired infections (HAI) would contribute to the growth of the nonwoven disposables market. Other growth drivers include stringent regulations for hygiene and the increase in the number of people with incontinence.
North America is the largest market for these products, according to the report, but Asia-Pacific is expected to surpass the Western continent by 2020 due to growing medical tourism and the rise in spending on “sophisticated hospitality services.” In the LAMEA (Latin America, Middle East and Africa) region, the demands for medical nonwoven products is up “due to the high prevalence of infectious diseases, interventions from the government through awareness campaigns and large-scale public initiatives for maintaining hygienic environment.”
Serkan Gogus, CEO of Mogul, a Turkish nonwovens producer, agrees that medical is a growing area for nonwovens, especially in emerging markets, and as income levels increase and health consciousness rises, demand for such products will go up. “In developed countries, new product developments that include the usage of nonwovens, in addition to current use, is key,” he says.
When it comes to HAIs as a growth factor, Medline, a manufacturer and distributor of healthcare items, sees the importance of nonwovens when it comes to prevention. “Nonwovens certainly have a central place in helping act as a barrier against healthcare acquired infections,” says Barbara Connell, MS, MT(ASCP)SH, VP Clinical Sales, Medline. “As more new technologies are being introduced, hospitals now have a cost-effective way to help in the fight against HAIs in the form of disposable nonwovens.”
Among Medline’s products used for infection prevention are personal protective equipment and disposable cleaning and disinfecting wipes.
In addition to these items, Medline also produces surgical drapes and gowns and sterilization wraps using nonwovens. “We’re always on the lookout for new fabrics and technologies, but, right now, nonwovens are the industry standard for many categories, especially in the operating room and in personal protective apparel,” says Medline’s Mark Chua, senior product manager, Proxima. “Customers are always looking for more value and performance, and Medline strives to have the strongest and most protective fabrics in the industry, while keeping user comfort in mind.”
The company has been also experimenting with the colors and looks and feel to its fabrics. Chua says this is because patient satisfaction is becoming “a more visible statistic in hospitals.” In addition to traditional surgical blue nonwovens, they also use fabrics with patterns like camouflage, pink ribbon and its new pink surgical gown line where a portion of proceeds are donated to the National Breast Cancer foundation.
Cardinal Health, a supplier of medical-surgical products such as surgical drapes, surgical gowns, face masks, sterilization wraps and incontinence items, finds that nonwovens are a reliable material for broad usage in the healthcare market and is seeing growth in several categories.
“We are seeing small shifts in surgical drapes and gowns due to shifts in procedure types,” says Debra Schotz, senior vice president and general manager of Medical Consumables at Cardinal Health. “Some areas, like the isolation gown market, continues to grow steadily, while other areas, such as the incontinence market, are seeing growth in part due to the aging population.”
Schotz says nonwovens offer several benefits in the medical field. “Nonwovens technology offers flexibility in softness, color and barrier levels, which allows for application to various medical product categories,” she explains, adding that they’re also cost effective disposable products, they provide consistent protection and performance, and they lower the amount of lint compared to previous products.
Jacob Holm to Expand Products Under Sontara
With the acquisition of DuPont’s Sontara business last year, the Jacob Holm Group has gained exposure to healthcare markets. Sontara offers surgical gowns, drapes, tape bases and other wound care products—specializing in soft and comfortable solutions that are lightweight, lower lint and specially treated.
“Healthcare is a key market segment for our Sontara business,” says Martin Mikkelsen, CEO, Jacob Holm Group. “Sontara has maintained its solid reputation of high quality and high performance, especially in the operating room, and is well-known in the industry for extreme softness, comfort and breathability. With the Jacob Holm innovation bench strength and our newly implemented Sontara Product Development Team, we will further advance our position in healthcare.”
According to Mikkelsen, the new team is currently working on expanding Sontara into select medical applications and has plans to launch several new products within the year. Although spunlace has lost share over the years in the healthcare market to spunmelt, Mikkelsen sees a lot of value in the material.
“Spunlace continues to be used in a variety of healthcare applications. The unique properties of Sontara and the flexibility to use a broad variety of fiber technologies in manufacturing allow for a wide range of high-performing, customized fabrics for many diverse applications.”
Among the advantages of Sontara are comfort, breathability and soft drapeability, which Mikkelsen says are challenging to replicate in a spunbond. Also, since Sontara is made using cellulose, it offers environmentally sustainable qualities, which are becoming increasingly important in the healthcare market.
Halyard Health Officially Debuts
Halyard’s new Aero Blue Performance Surgical Gown is soft and lightweight.
According to Mike Tuck, vice president, Global Product Supply, Halyard Health, the $1.7 billion medical technology company is now able to invest to drive its long-term growth, which it couldn’t do when it was part of a much larger company where capital was returned to K-C.
As its own company, Halyard Health offers a broad range of medical products including surgical gowns, surgical drapes, sterile wrap, surgical masks and apparel, which are manufactured using its internally produced nonwovens. “Nonwovens technology provides protection from liquids while remaining breathable,” Tuck explains. “These fabrics are ideal for use in hospitals because they provide a higher level of protection and enhanced sterility over cotton, linen, and paper-based products.”
In 2014, the company launched the Halyard Aero Blue Performance Surgical Gown. Tuck says the new product is soft and lightweight and claims that the gown is four times more protective than comparable surgical gowns. “This product represents a significant innovation in perioperative protection,” he says.
Halyard also launched product improvements to its sterilization solutions. One of these innovations includes Smart-Fold, a sterilization packaging engineered to protect heavy trays and loaner sets from tears and cuts in handling.
Freudenberg Prioritizes Advanced Wound Care
Freudenberg Performance Materials, which produces nonwovens for advanced wound care, traditional wound care, stoma care and transdermal solutions in the medical field, has recently focused on the development of solutions for advanced and active wound care.
“The fastest growth is being seen by hydroactive and superabsorbing nonwovens as well as by antimicrobially-treated nonwovens and foams,” says Marcus Simon, business segment manager medical, Freudenberg Performance Materials.
In fact, on January 1, Freudenberg acquired Polymer Health Technology Ltd. (PHT) of Ebbw Vale, U.K., a leading specialist of polyurethane foams for advanced wound care. Hydrophilic foam solutions play an increasingly important role in modern advanced wound care. Current global market share lies at over 40%.
“With the acquisition of Polymer Health Technology, Freudenberg Performance Materials will be able to offer our globally-active customers additional innovative solutions for modern wound management,” Simon adds.
PHT’s hydrophilic polyurethane foam systems absorb wound exudate, creating an ideal environment for wound healing, according to Simon, and these are special features customers are seeking in wound care products. “They protect the wound from drying out, from cooling and ensure an unhindered exchange of gases and water vapor, thereby accelerating the wound healing process.”
For ostomy solutions, customers are looking for odor absorbing materials and membranes. Simon says Freudenberg’s high performance ostomy carbon filter—used in a pouch—is engineered to remove malodors, which in turn improves quality of life.
Investments in the Middle East
In May, Advanced Fabrics (SAAF) of Saudi Arabia, an innovator in the medical and hygiene markets, added a second treatment line for alcohol repellent and anti-static products. The new line is close to full production, and will give the company a treatment capacity of over 1000MT per month, according to Ian Disley, general manager.
“SAAF added a second treatment line due to demand from customers and a belief that we could better optimize quality and efficiency by having the treatment line next to the new fabric production line in our Rabigh facility,” Disley says. “The new state-of-the-art Reicofil line has enabled us to take our well-known Medalon product further to produce MedalonS, with enhanced softness. As a leading supplier worldwide of treated barrier fabrics we believe the best results are achieved by developing the base fabric and treatment process together.”
Another investment this year came from Turkish nonwovens producer Bayteks, which produces PP spunbond, SMMS, PET spunbond and meltblown fabrics. The company installed a hotmelt lamination machine at the end of April.
“With this one we are targeting the medical sector for the drapes, gowns, and all the surgical, single-use disposables,” says Mehmet Bozkan, director of sales and marketing, adding that the medical market is the company’s main target right now.
“Medical is growing for SMMS fabrics. We are already supplying our material for medical companies, so it’s a complementary product for us, and an added value addition to our product,” he adds.
PLA Meltblown Expert Offers New Technology
Biovation, a technology design and manufacturing company that produces advanced, nonwoven fiber products with integrated antimicrobial properties, is using its expertise in the medical market.
In March, the company launched the BioArmour Blood Pressure Cuff Shield to mitigate the spread of infectious pathogens from blood pressure cuffs. According to the company, this first-in-class medical product offers a multi-use barrier for prevention of hospital acquired infections.
The BioArmour Blood Pressure Cuff Shield is a disposable antimicrobial hygienic barrier that attaches to the blood pressure cuff to prevent direct contact of the cuff with the patient’s skin. The latex-free shield material—a PLA meltblown nonwoven—is composed of a sustainable biopolymer impregnated with antimicrobial and antifungal agents to mitigate the propagation of a wide spectrum of pathogens in controlled release fashion. Contaminant pathogens—including MRSA, VRE, c. difficile and others—are mitigated by the blood pressure cuff shield, allowing for multi-patient use over a 24-hour period. Biovation worked with antimicrobial solutions specialist Sciessent to develop the antimicrobial technology.
“There is nothing like it [in the market],” says Kerem Durdag, CEO of Biovation. “It’s first in its class in terms of approvals, and also as a product. The only equivalent product that’s on the marketplace is a plastic disposable blood pressure cuff meant for one-time use. This would be the first nonwoven, multi-patient, multi-use, multi-pathogen with an FDA 510k Class 2 medical device approval. The plastic disposable cuff is not FDA 510k Class 2 approved.”
While the cuff shield is available in the European Union (registered a CE Class I medical device), Canada and all non-U.S. markets, the product is still awaiting FDA approval. Durdag expects the product to be available in the U.S. in the fall of 2016.
The company has also been hard at work on an advanced wound care dressing, which is also going through the FDA approval process. An all PLA biopolymer nonwoven “back-bone” construction with a proprietary gel-cast coating with wound healing agents and antimicrobials as a non-adherent wound contact surface, Durdag says it will be able to be used on low to medium exudate wounds. The dressing will have comparable benchmark performance to current foam, hydrocolloid and alginate based products and be available in several formats with pricing significantly lower than present incumbent solutions.
The advanced wound care product is expected to be available in the U.S. and EU by mid-2017.