Tara Olivo, associate editor04.07.15
Let’s take a look at some numbers: 20 billion, 3.5 million, 8000, 500. The U.S. Environmental Protection Agency estimates 20 billion disposable diapers are sent to landfills each year, accounting for over 3.5 million tons of waste. It’s also projected that, on average, each baby will use 8000 diapers in its life; each diaper is said to last 500 years in the landfill. The amount of waste generated from disposable diapers is astounding.
But let’s face it; disposables aren’t going anywhere. Parents and caregivers value the benefits of the one-time use products. They’re superabsorbent, hygienic and convenient. At the same time, more and more consumers are looking for products with eco-friendly characteristics, while also choosing brands that follow environmentally sustainable practices.
So, while diaper makers are doing their part to create the “greenest” products they can, other companies, like Knowaste, are figuring out ways to recycle absorbent hygiene products (AHPs) such as baby and adult diapers, as well as feminine hygiene products. With parents well aware of the amount of diapers used and being sent to landfills, this is something they can get behind.
And, while baby diapers play a big role within the nonwovens industry, producers of nonwoven materials are also doing their part to reduce, reuse and recycle at the onset of the production chain.
Turning Trash into “Treasure”
Run by CEO Roy Brown and U.K. Business Development Director Paul Richardson, Knowaste has been researching and developing technology for recycling absorbent hygiene products since the mid-1990s. While the company has had research & development plants in Canada, the U.S. and Holland, it has been concentrating on the U.K. in recent years.
After running the plants in North America and Holland, the company’s first U.K. facility was established in 2011, and was based around Knowaste’s newest technology. “Previously all technology had been to do with sanitizing the used product and then recycling just the fiber. But when we came to the U.K., we needed to sterilize the product because in the U.K. and Europe, sanitization is not recognized. Because we wanted to create products from everything, not just from the fiber, but from the plastic as well, we needed to sterilize,” Richardson says.
While the facility closed in 2013, Knowaste is planning to announce a new commercial facility that will be based in the U.K., an important market for the company, according to Richardson.
“The U.K. will be the technological platform for any other plant that we build anywhere in the world. We’re reconfiguring our technology, and we have new patents and new technology that would compose of it,” he says. This facility will be the exemplar for future facilities in the U.K., as well as any other plants launched throughout the world, he explains.
The company hopes to open the new facility in West London early next year, with an additional plant in the U.K. to launch later.
According to Richardson, the U.K. market uses about 1.1 million tons of AHPs annually across two sectors: commercial and household. For the commercial sector, which includes nurseries, daycare centers, hospitals and retail centers, there are about 250,000 tons of used AHPs annually, collected by commercial hygiene companies. Richardson says homes make up about 860,000 tons per year. “We have commitments from several local authorities in the U.K. to operate collection schemes and deliver so that the household will have a container in their house while they have a child or while they have an adult dependent on incontinence. They will deliver [the used items] to our facility in West London and wherever else we build,” he says.
Regarding the process, all parents and caregivers have to do is do what they normally do—dispose the used AHPs in a bag. Then, they put the bag or bags into the designated container provided by the local authority. “We just take them as they are and we deal with everything,” Richardson explains. “We deal with any of the products that would go with it as well, [such as] wipes. Anything that a household would use or a commercial operator would use.”
Knowaste can recycle 100% of the clean product, he says. The company is also working on processes that will utilize the waste product, but Richardson couldn’t elaborate further.
Through the recycling process, the company will get two products—fiber and plastic. Knowaste will leave the superabsorbent polymer in the fiber and deactivate it, though the product should retain about 30% of its absorbent capacity, Richardson explains. He says the first two plants in the U.K. will have the fiber made onsite, where they will convert it into cat litter and possibly other items. “We’ve tested many, many items and we know the market really well. But we found that the one that was most beneficial to us, and is quite a nice market as well, is the cat litter market.”
Richardson says the plastics that are recycled will be completely reformed and pelletized. The plastic pellets are then supplied to the company that makes the containers for the nappy and incontinence waste. “It’s full circle,” he says.
While Knowaste doesn’t have any plants running at the moment, the company is well known across the U.K. and sees public demand for this type of system. “They really get why they should do it, and they like to participate because, I think, as soon as you have a baby, you suddenly realize that you want to leave the world in a better condition than it currently is so I think they get what we do and appreciate it,” Richardson says.
Manufacturers Thinking Green
Nonwovens producers have made a big push toward more sustainable practices. It’s not only good for the Earth; it’s good for the business. Companies are recycling trim material, reject rolls, and even materials sent back to them from customers.
Among the recyclers in the industry is Sandler. Manufacturing 100% polyester nonwovens for applications in the automotive industry, construction and office acoustics, Sandler doesn’t use chemical additives during production, according to Ulrich Hornfeck, member of the management board.
“During the production of our polyester nonwovens, edge trims are sent directly for reprocessing and are reused as a raw material in production,” Hornfeck says. “We also recover processing waste from our customers and send it for external recycling.”
What’s more, Hornfeck indicates that these durable nonwovens can be recycled after many years of use, “providing raw material for new applications.” Among these recyclable products are automotive sound and heat insulation, roof insulation and sound insulation that’s used for interior design in offices such as partitions, wall decoration and more.
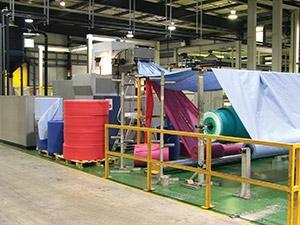
Photo courtesy of Don & Low.
U.K.-based Don & Low Ltd., a division of the Thrace Group, has been recycling excess nonwovens since 2000. The company recycles its polypropylene spunbond and meltblown nonwovens and films, according to Keith Galloway, general manager of nonwovens at Don & Low.
“More than 70% of recycled material is reused in-house; the surplus are sold to convertors for use in injection molding or the like,” Galloway says. Recycled materials turn into black low shrink products or black groundcover, and low tensile critical applications, he adds.
The registered waste merchants that Don & Low sells its surplus to guarantee downstream use and further conversion into other industries, resulting in zero landfill status for the company, he explains.
Also recycling polypropylene fabrics is Argentine manufacturer Softbond Nonwovens. The company began recycling nonwovens over 10 years ago, according to Softbond director Alessio Romanelli.
“We recycle both inline and offline with dedicated equipment,” he says. “We reuse almost all of the recycled material and some excess is sold in the market.”
While he couldn’t comment on specific numbers, Romanelli says the company diverts hundreds of tons of material from landfills each year.
Perhaps one of the earliest recyclers in the industry is Kimberly-Clark. Lisa Morden, the company’s senior director for global sustainability, estimates that the company has been recycling its excess nonwovens since the late 1980s. “Conservatively, K-C has invested at least $10 million in capital over the last 20 years, advancing our ability to reuse our scrap nonwovens back into K-C nonwoven assets,” she comments.
K-C reprocesses most of the homo-polymer scrap generated onsite, which they then return to the nonwoven process for reusing, Morden explains. “Anything that we cannot reclaim back into our nonwoven assets is sold by a central team and directed into valuable recycle markets and is ultimately converted into products such as garbage cans, plastic fans, shelving, storage tubs and automobile parts.”
Recycling is also part of nonwovens maker Suominen’s overall sustainability strategy, according to Alistair Brown, director of marketing and communications for the Finnish company. “The approximately 60% reduction in landfill waste was the result of several targeted activities, including investments in recycling, and success in identifying new external end users for the waste generated in the company’s manufacturing processes,” he says.
As part of its green efforts, Brown says Suominen will launch a separate project to develop the sustainability of its product range later this year.
Reasons for Recycling
So, what exactly is motivating companies to recycle? For Sandler, reasons run the gamut.
“Sustainability and the conservation of resources have always been an integral part of Sandler’s corporate philosophy,” says Hornfeck.
“The sensible use of raw materials, the recycling of edge trims, for example, and the development of products, which support closed material cycles even after use are therefore important and, at the same time, self-evident to us.”
Economically, he says, there are several advantages because of the established value chain for polyester, citing the collecting and recycling of polyester drinking bottles as an example. “They are reprocessed into so-called bottle flakes, which in turn are processed into polyester fibers. Thus, recycled fibers are readily available as a raw material for nonwovens production and, additionally, these possibilities of upcycling support closed material cycles,” he explains.
Additionally, Sandler is hearing high demand from customers for ecofriendly products due to climate change and the increasing shortage of resources.
“Customers are looking for products that offer some ecological benefit in addition to performing their specific function. Nonwovens that are partially made from recycled raw materials and are recyclable themselves after use offer this combination of functionality and sustainability,” he comments.
And, while reusing recycled edge trim brings some cost savings to Sandler, Hornfeck says it’s not on a large scale.
Galloway agrees that there are various reasons driving the need to recycle. For Don & Low, these include cost savings, customer demands for sustainable products and cost reduction of commodity products.
Recycling trim also allows Softbond to save on costs, according to Romanelli, while it contributes to the company’s overall sustainability efforts.
An important factor for K-C is the “value created by the sale of secondary materials,” but the company also strives to keep valuable materials out of landfills, Morden explains. “Reusing or recycling these fibers is a financially and environmentally responsible approach,” she states adding that more than 99% of nonwoven manufacturing waste is diverted from landfill.
Challenges
With recycling comes challenges. Will the recycled products be up to par?
Hornfeck admits upholding the quality of the product and ensuring its uniformity are among the most important challenges for Sandler regarding recycling and using recycled fibers. “Being a renowned supplier of high-quality products, it is a matter of course for Sandler to ensure, that while furthering sustainability we also maintain our quality standards and do not affect product characteristics,” he says.
“When it comes to recycled fibers as a raw material, the traceability of the value chain is crucial—being able to ascertain where the raw material comes from and what additives might be contained in the fibers.”
For Softbond, one of the main challenges of recycling nonwovens is reducing environmental impact while trying to reuse recycled materials in the main production process, Romanelli says.
Morden acknowledges a key issue for K-C with regard to recycling. “One of the most significant challenges occur when material or additive changes—usually designed to enhance product functionality, performance or cost—introduce incompatible materials that cannot be reused or recycled with conventional recycling technologies,” she says.
Machines Making it Happen
One of the companies supplying machines to nonwovens producers is Starlinger, a manufacturer of machinery and complete lines for woven plastic packaging production. The company founded its recycling division in 2000, launched its product range “recoSTAR” in 2002 and its first line was supplied—and is still up and running—to the U.K. in 2003.
The fact that Starlinger’s machines were able to recycle nonwoven fabrics was unintentional. “We did not specifically design a technology for nonwovens recycling but realized when existing customers brought this application to us that our product range recoSTAR can handle this scrap perfectly well,” says Elfriede Hell, MBA, general manager recycling technology.
Starlinger offers two machines for the nonwovens industry, recoSTAR universal and recoSTAR basic, which was relaunched at NPE in March 2015 with new features as recoSTAR dynamic. Its recoSTAR universal line is a shedder/extruder combination mostly for the recycling of polypropylene nonwovens. Starlinger’s recoSTAR dynamic is a SMART feeder/extruder combination mostly for the recycling of polyester materials.
“Principally, the material for the recoSTAR universal only has to be proportioned. The line is equipped with a shredder, thus also start-up lumps as heavy as 30kg can be processed,” Hell explains. “For recoSTAR dynamic, [the] customer provides pre-shredded material or we supply the shredder.”
Within the nonwovens sector, producers of the materials make up most of Starlinger’s customers. Hell says this ensures that the materials aren’t contaminated on the way to recycling. “They usually separate the different types they have allowing them to use high percentage of regranulate in some applications as they know the recipe perfectly well,” she adds. Though, she says one customer recycles post-industrial waste—where nonwovens have gone through another step—diapers.
Something rather unlikely is that the company also has one customer collecting post-consumer waste, but Hell says this is only because they are collecting from specific sources, such as hospitals. “[This ensures] the same quality and rather clean waste,” she explains.
Hell believes an overall shift towards recycling, sustainability and awareness—that scrap is a secondary resource versus a waste—is among the reasons why nonwovens manufacturers are recycling. Moreover, she says, “Producers started to understand that if, instead of selling the waste or even paying to have it disposed of, recycling their waste can contribute to their overall success.”
But let’s face it; disposables aren’t going anywhere. Parents and caregivers value the benefits of the one-time use products. They’re superabsorbent, hygienic and convenient. At the same time, more and more consumers are looking for products with eco-friendly characteristics, while also choosing brands that follow environmentally sustainable practices.
So, while diaper makers are doing their part to create the “greenest” products they can, other companies, like Knowaste, are figuring out ways to recycle absorbent hygiene products (AHPs) such as baby and adult diapers, as well as feminine hygiene products. With parents well aware of the amount of diapers used and being sent to landfills, this is something they can get behind.
And, while baby diapers play a big role within the nonwovens industry, producers of nonwoven materials are also doing their part to reduce, reuse and recycle at the onset of the production chain.
Turning Trash into “Treasure”
Run by CEO Roy Brown and U.K. Business Development Director Paul Richardson, Knowaste has been researching and developing technology for recycling absorbent hygiene products since the mid-1990s. While the company has had research & development plants in Canada, the U.S. and Holland, it has been concentrating on the U.K. in recent years.
After running the plants in North America and Holland, the company’s first U.K. facility was established in 2011, and was based around Knowaste’s newest technology. “Previously all technology had been to do with sanitizing the used product and then recycling just the fiber. But when we came to the U.K., we needed to sterilize the product because in the U.K. and Europe, sanitization is not recognized. Because we wanted to create products from everything, not just from the fiber, but from the plastic as well, we needed to sterilize,” Richardson says.
While the facility closed in 2013, Knowaste is planning to announce a new commercial facility that will be based in the U.K., an important market for the company, according to Richardson.
“The U.K. will be the technological platform for any other plant that we build anywhere in the world. We’re reconfiguring our technology, and we have new patents and new technology that would compose of it,” he says. This facility will be the exemplar for future facilities in the U.K., as well as any other plants launched throughout the world, he explains.
The company hopes to open the new facility in West London early next year, with an additional plant in the U.K. to launch later.
According to Richardson, the U.K. market uses about 1.1 million tons of AHPs annually across two sectors: commercial and household. For the commercial sector, which includes nurseries, daycare centers, hospitals and retail centers, there are about 250,000 tons of used AHPs annually, collected by commercial hygiene companies. Richardson says homes make up about 860,000 tons per year. “We have commitments from several local authorities in the U.K. to operate collection schemes and deliver so that the household will have a container in their house while they have a child or while they have an adult dependent on incontinence. They will deliver [the used items] to our facility in West London and wherever else we build,” he says.
Regarding the process, all parents and caregivers have to do is do what they normally do—dispose the used AHPs in a bag. Then, they put the bag or bags into the designated container provided by the local authority. “We just take them as they are and we deal with everything,” Richardson explains. “We deal with any of the products that would go with it as well, [such as] wipes. Anything that a household would use or a commercial operator would use.”
Knowaste can recycle 100% of the clean product, he says. The company is also working on processes that will utilize the waste product, but Richardson couldn’t elaborate further.
Through the recycling process, the company will get two products—fiber and plastic. Knowaste will leave the superabsorbent polymer in the fiber and deactivate it, though the product should retain about 30% of its absorbent capacity, Richardson explains. He says the first two plants in the U.K. will have the fiber made onsite, where they will convert it into cat litter and possibly other items. “We’ve tested many, many items and we know the market really well. But we found that the one that was most beneficial to us, and is quite a nice market as well, is the cat litter market.”
Richardson says the plastics that are recycled will be completely reformed and pelletized. The plastic pellets are then supplied to the company that makes the containers for the nappy and incontinence waste. “It’s full circle,” he says.
While Knowaste doesn’t have any plants running at the moment, the company is well known across the U.K. and sees public demand for this type of system. “They really get why they should do it, and they like to participate because, I think, as soon as you have a baby, you suddenly realize that you want to leave the world in a better condition than it currently is so I think they get what we do and appreciate it,” Richardson says.
Manufacturers Thinking Green
Nonwovens producers have made a big push toward more sustainable practices. It’s not only good for the Earth; it’s good for the business. Companies are recycling trim material, reject rolls, and even materials sent back to them from customers.
Among the recyclers in the industry is Sandler. Manufacturing 100% polyester nonwovens for applications in the automotive industry, construction and office acoustics, Sandler doesn’t use chemical additives during production, according to Ulrich Hornfeck, member of the management board.
“During the production of our polyester nonwovens, edge trims are sent directly for reprocessing and are reused as a raw material in production,” Hornfeck says. “We also recover processing waste from our customers and send it for external recycling.”
What’s more, Hornfeck indicates that these durable nonwovens can be recycled after many years of use, “providing raw material for new applications.” Among these recyclable products are automotive sound and heat insulation, roof insulation and sound insulation that’s used for interior design in offices such as partitions, wall decoration and more.
Photo courtesy of Don & Low.
“More than 70% of recycled material is reused in-house; the surplus are sold to convertors for use in injection molding or the like,” Galloway says. Recycled materials turn into black low shrink products or black groundcover, and low tensile critical applications, he adds.
The registered waste merchants that Don & Low sells its surplus to guarantee downstream use and further conversion into other industries, resulting in zero landfill status for the company, he explains.
Also recycling polypropylene fabrics is Argentine manufacturer Softbond Nonwovens. The company began recycling nonwovens over 10 years ago, according to Softbond director Alessio Romanelli.
“We recycle both inline and offline with dedicated equipment,” he says. “We reuse almost all of the recycled material and some excess is sold in the market.”
While he couldn’t comment on specific numbers, Romanelli says the company diverts hundreds of tons of material from landfills each year.
Perhaps one of the earliest recyclers in the industry is Kimberly-Clark. Lisa Morden, the company’s senior director for global sustainability, estimates that the company has been recycling its excess nonwovens since the late 1980s. “Conservatively, K-C has invested at least $10 million in capital over the last 20 years, advancing our ability to reuse our scrap nonwovens back into K-C nonwoven assets,” she comments.
K-C reprocesses most of the homo-polymer scrap generated onsite, which they then return to the nonwoven process for reusing, Morden explains. “Anything that we cannot reclaim back into our nonwoven assets is sold by a central team and directed into valuable recycle markets and is ultimately converted into products such as garbage cans, plastic fans, shelving, storage tubs and automobile parts.”
Recycling is also part of nonwovens maker Suominen’s overall sustainability strategy, according to Alistair Brown, director of marketing and communications for the Finnish company. “The approximately 60% reduction in landfill waste was the result of several targeted activities, including investments in recycling, and success in identifying new external end users for the waste generated in the company’s manufacturing processes,” he says.
As part of its green efforts, Brown says Suominen will launch a separate project to develop the sustainability of its product range later this year.
Reasons for Recycling
So, what exactly is motivating companies to recycle? For Sandler, reasons run the gamut.
“Sustainability and the conservation of resources have always been an integral part of Sandler’s corporate philosophy,” says Hornfeck.
“The sensible use of raw materials, the recycling of edge trims, for example, and the development of products, which support closed material cycles even after use are therefore important and, at the same time, self-evident to us.”
Economically, he says, there are several advantages because of the established value chain for polyester, citing the collecting and recycling of polyester drinking bottles as an example. “They are reprocessed into so-called bottle flakes, which in turn are processed into polyester fibers. Thus, recycled fibers are readily available as a raw material for nonwovens production and, additionally, these possibilities of upcycling support closed material cycles,” he explains.
Additionally, Sandler is hearing high demand from customers for ecofriendly products due to climate change and the increasing shortage of resources.
“Customers are looking for products that offer some ecological benefit in addition to performing their specific function. Nonwovens that are partially made from recycled raw materials and are recyclable themselves after use offer this combination of functionality and sustainability,” he comments.
And, while reusing recycled edge trim brings some cost savings to Sandler, Hornfeck says it’s not on a large scale.
Galloway agrees that there are various reasons driving the need to recycle. For Don & Low, these include cost savings, customer demands for sustainable products and cost reduction of commodity products.
Recycling trim also allows Softbond to save on costs, according to Romanelli, while it contributes to the company’s overall sustainability efforts.
An important factor for K-C is the “value created by the sale of secondary materials,” but the company also strives to keep valuable materials out of landfills, Morden explains. “Reusing or recycling these fibers is a financially and environmentally responsible approach,” she states adding that more than 99% of nonwoven manufacturing waste is diverted from landfill.
Challenges
With recycling comes challenges. Will the recycled products be up to par?
Hornfeck admits upholding the quality of the product and ensuring its uniformity are among the most important challenges for Sandler regarding recycling and using recycled fibers. “Being a renowned supplier of high-quality products, it is a matter of course for Sandler to ensure, that while furthering sustainability we also maintain our quality standards and do not affect product characteristics,” he says.
“When it comes to recycled fibers as a raw material, the traceability of the value chain is crucial—being able to ascertain where the raw material comes from and what additives might be contained in the fibers.”
For Softbond, one of the main challenges of recycling nonwovens is reducing environmental impact while trying to reuse recycled materials in the main production process, Romanelli says.
Morden acknowledges a key issue for K-C with regard to recycling. “One of the most significant challenges occur when material or additive changes—usually designed to enhance product functionality, performance or cost—introduce incompatible materials that cannot be reused or recycled with conventional recycling technologies,” she says.
Machines Making it Happen
One of the companies supplying machines to nonwovens producers is Starlinger, a manufacturer of machinery and complete lines for woven plastic packaging production. The company founded its recycling division in 2000, launched its product range “recoSTAR” in 2002 and its first line was supplied—and is still up and running—to the U.K. in 2003.
The fact that Starlinger’s machines were able to recycle nonwoven fabrics was unintentional. “We did not specifically design a technology for nonwovens recycling but realized when existing customers brought this application to us that our product range recoSTAR can handle this scrap perfectly well,” says Elfriede Hell, MBA, general manager recycling technology.
Starlinger offers two machines for the nonwovens industry, recoSTAR universal and recoSTAR basic, which was relaunched at NPE in March 2015 with new features as recoSTAR dynamic. Its recoSTAR universal line is a shedder/extruder combination mostly for the recycling of polypropylene nonwovens. Starlinger’s recoSTAR dynamic is a SMART feeder/extruder combination mostly for the recycling of polyester materials.
“Principally, the material for the recoSTAR universal only has to be proportioned. The line is equipped with a shredder, thus also start-up lumps as heavy as 30kg can be processed,” Hell explains. “For recoSTAR dynamic, [the] customer provides pre-shredded material or we supply the shredder.”
Within the nonwovens sector, producers of the materials make up most of Starlinger’s customers. Hell says this ensures that the materials aren’t contaminated on the way to recycling. “They usually separate the different types they have allowing them to use high percentage of regranulate in some applications as they know the recipe perfectly well,” she adds. Though, she says one customer recycles post-industrial waste—where nonwovens have gone through another step—diapers.
Something rather unlikely is that the company also has one customer collecting post-consumer waste, but Hell says this is only because they are collecting from specific sources, such as hospitals. “[This ensures] the same quality and rather clean waste,” she explains.
Hell believes an overall shift towards recycling, sustainability and awareness—that scrap is a secondary resource versus a waste—is among the reasons why nonwovens manufacturers are recycling. Moreover, she says, “Producers started to understand that if, instead of selling the waste or even paying to have it disposed of, recycling their waste can contribute to their overall success.”