03.06.12
The show will be held April 24-26 at the Georgia World Congress when it will assemble all vertical aspects of the technical textile industry. From research and development through raw materials and production processes and finally ending in conversion, further treatment and recycling, virtually all aspects of technical textile production will be represented.
Beginning this year, ATME-I (American Textile Machinery Exhbition International) will be incorporated into Techtextil North America, providing textile machinery equipment, producers and service suppliers a broader technical textile and nonwoven industry base to showcase their products and services.
Held in conjunction with the three-day exhibition will be a symposium, featuring dozens of sessions focusing on the latest in research and emerging technologies. The symposium is structured for attendees to conduct business and network on the show floor as well.
Keynote Address
Tuesday, April 24, 2012
8-9 a.m.
Miguel Caballero, the Armani of Bullet Proof Clothing
Designer, Miguel Caballero known as the ‘Armani of Bullet Proof Clothing’ founded his label in 1992 in Colombia’s capital, Bogota.
Señor Caballero will talk about where the idea for his company came from, how it grew to become recognized as a “specialized brand name” and a leader in personal protection solutions using high technology innovation, where he sees the industry heading, who his clients are and why they are attracted to his company.
Morning Sessions
Concurrent, 9:30- 11:30 a.m.
TT01: The Basics 1 – From Fiber to Fabrics
Session Chair: Dr. Fred Cook, Professor, Materials Science and Engineering, Georgia Tech, Atlanta, GA
This is the first part of a two-part session intended for those who are new in the industry or those who may want a refresher in textiles oriented to technical applications. Elements of fiber, yarn, fabric types and subsequent processes used to enhance properties and/or provide greater function will be included. A review by academic and industry experts of the attributes of various materials, their advantages and applications, and how they fit into technical textiles will be an integral part of this program. This session is designed to honor many requests for such a program at the beginning of the event to make your visit more valuable.
TT02: New Technology
Session Chair: Jim Kaufmann, Textile Engineering and Manufacturing, TEAM Inc., Woonsocket, RI
As technical and specialty textile applications continue to innovate, evolve and diversify; textile manufacturing technologies must keep pace. This session will focus on several new and innovative textile processing technologies that either already are, or soon will be impacting the industry and subsequently the marketplace.
• TT02.1 Melt Spinning of Yarn John Wilson, R&D Manager, The Quantum Group, Colfax, NC
• TT02.2 Nano fibers and Nano‐nonwovens Laura Frazier, Director, SNS Nano Fiber Technology, LLC, Hudson, OH
• TT02.3 Multi‐Axial Weaving Technology from Dornier Marty Colwell , American Dornier, Charlotte, NC
• TT02.4 Weft Inserted Warp Knitting Lutz Heinig, Technical Manager, Karl Mayer, Greensboro, NC
TT03: High Performance Composites
Session Chair: Dr. Ysuf Ulcay, Vice President, Bursa Technical University, Bursa, Turkey
Composites are everywhere and touch our lives in major ways daily. In technical textiles, composites involve materials that reinforce a resin to produce products (often called reinforced plastic) with high strength‐to‐weight ratios, most often reducing the weight of existing products of metals such as steel and aluminum. It is a growing market. Yet, to most of us, composites appear invisible. This session will review some of the applications, materials, construction and the advantages of using composites.
Afternoon Sessions
Concurrent, 1:30-4 p.m.
TT04: The Basics 2 – From Woven to Nonwovens to Knits
Session Chair: Dr. Fred Cook, Professor, Materials Science and Engineering, Georgia Tech, Atlanta, GA
A continuation of the elements of technical textiles. This session covers nonwovens in technical textiles along with specialized finishing processes and applications.
TT05: Military – Continuing Impact on Technical Textiles
Session Chair: Dr. Eugene Wilusz, Natick Soldier RDE Center, Natick, MA
Technical textiles continue to be an important component of countless items used by the military. Dress clothing, protective clothing, tentage, shelters, parachutes and many other items utilize technical textiles. Some of the current areas of interest include ballistic protection, flame resistance and chemical and biological protection. Presentations will cover the latest developments in science and technology of particular interest to defense applications.
• TT05.1 Thermal Testing Margaret Auerbach, Natick Soldier RDE Center, Natick, MA
• TT05.2 Super-Repellant Coatings Hoon Joo Lee, Professor, North Carolina State University, NC
• TT05.3 Microwave Promoted Deposition of Protective Coatings Dr. Jeffery Owens, Air Force Research Laboratory, Tyndall Airforces Base, FL
• TT05.4 Advanced Multi-Functional Nanofiber-Textile Materials for Chemical and Biological Defense Applications Xiangwu Zhang, PH.D., Assistant Professor, North Carolina State University, Raleigh, NC
This presentation will review work on developing novel textile materials for chemical and biological defense applications that require large volume‐to‐weight ratio, excellent filtration efficiency, high detoxifying activity and good durability. Latest developments in material processing methods in electrospinning and atmospheric plasma treatment were utilized to achieve these goals.
TT06: Automotive – Opportunities for Technical Textiles
Session Chair: Lee Woodard, Global Advanced R&D, Guilford Performance Textiles, Wilmington, NC
The automotive interiors marketplace is highly competitive. Being successful in this market requires fully integrating design expectations with technical performance; all at very aggressive price structures. Advances in technology, coupled with changing OEM design and styling requirements, are having a significant impact on the selection process for automotive interiors. This session will begin by reviewing key drivers for the raw material supply base for automotive textiles. Other presentations will explore emerging design trends in automotive interiors, including sustainability initiatives, and examine key changes to technical requirements for the various automotive textile applications.
• TT06.1 The Lifecycle of Automotive Textiles- From Dreams to Demolition Laurie Busch, Senior Designer, Guilford, Inc., Wilmington, NC
This presentation traces the current lifecycle of automotive soft trim. It begins with a look at what we are working on for vehicles still in the concept phase; model years 2013 and beyond. The presentation then reviews the vehicle trends from the 2012 Detroit Auto Show, including some significant changes in textile usage and placement. The presentation concludes by examining life after sale of a vehicle, from the perspective of soft trim and total vehicle recycling.
• TT06.2 The Synthetic Fibers Roller Coaster Alasdair Carmichael, President - Americas, PCI Fibers, Spartanburg, NC
The global markets for synthetic fibers have had a highly volatile last two years. What has influenced these markets? Fiber demand has been strong for much of this time, and oil prices have increased, so what has been the main driver of price. This paper will discuss these issues and look at where the automotive industry is impacted by synthetic fiber movements.
• TT06.3 Understanding Recycled Fibers for Automotive Applications Meredith Boyd, Product Development Manager, Unifi Manufacturing, Inc., Greensboro, NC
Learn everything you need to know about recycled fibers for automotive applications. Why are recycled fibers important for our future? Understand the differences of recycled products and how to use them in your products. This seminar will teach you everything from the process of making recycled fibers, their performance characteristics, and the companies that make them. Get all the information you need for informed decision making when it comes to recycled textiles for automotive.
Morning Sessions
Concurrent, 8:30-11 a.m.
Protective Textiles
Session Chair: John Cronin, Marketing Manager, HP Laboratories, New Ipswich, NH
The Protective Textiles Session is a forward‐looking program prepared for those engaged in the Personal Protective Equipment supply chain for public safety, military, industrial safety and other markets. This year’s expert speakers will discuss emerging federal standards, on‐going research and emerging technologies.
• TT07.1 Achieving Advanced FR Properties Through New Advances in Raw Materials Brian M Beitz PhD, Research and Development Manager, Offray Specialty Narrow Fabrics, Chester, NJ
Learn about the new advancements in fr properties with new raw material developments like fr-flex. This will allow the industry to explore new avenues for stretch applications in all of their fr products.
• T07.2 Application of 3D Orthogonal Woven High Performance Fabrics James A. Larsen II, Director of Engineering, Diamondback Tactical, LLLP, Spindale, NC
The presentation will include the application of 3D orthogonal woven high performance fabrics in Structural, Vehicle, Maritime, Aerospace and Body Armor. Touching on the comparisons between traditional 2D vs. 3D fabrics. The focus will be on the gained structural performance of the fabrics and processing improvements that benefit faster production times and higher fiber volume fractions.
TT08: Technical Textiles in Sports and Outdoors
Session Chair: Jim Kaufmann, Textile Engineering and Manufacturing, TEAM Inc., Woonsocket, RI
Sports and outdoor applications utilize a great deal of specialized technology to make the wearer or user more comfortable, hidden, and protected, even allowing greater performance and efficiency. As it is so often the case in technical textiles, many of the materials and technology used are “internal” and not visible, often given little thought but are vital to the user. Much research and development is focused on this area. This new session will examine some of those applications. Is there “gold” you might find in this area?
Afternoon Sessions
(Concurrent, 1:30-4 p.m.)
TT09: Technical Nonwovens
Session Chair: Dr. Behnam Pourdeyhimi, Director Nonwovens Institute, NCSU, Raleigh, NC
The session deals with the latest developments in nonwovens process technologies allowing the creation of novel structures from a varied of materials sources. The talks will focus on the latest developments in staple fiber processing.
• TT09.1 Advances in Heavy-Denier, High-Throughput Spunbond Timothy Robson, Hills Inc., Melbourne, FL
This presentation focuses on the machinery and methods associated with higher (>8) dpf spunbond production at rates at or above 300kg/m/hr. Spunbond machinery is broken down into two main systems, closed or open. The associated pros and cons of these systems are compared including suitability for various end-products. Specific attention is paid to the quenching, attenuation and laydown of filaments in these configurations. Dimensional comparisons of the spinning and formation distance have important affects on both the process and final product, particularly the MD:CD tenacity ratio and visual appearance of the fabric.
• TT09.2 Through Air Drying (TAD) and Comparative Bonding Processes American Truetzschler Nonwovens, Speaker To Be Announced
This presentation will focus on through air drying (TAD) and comparative bonding processes. To differentiate through air drying from other thermal bonding processes, the presentation will compare and contrast TAD with other processes, highlighting the pros and cons of each.
• TT09.3 Current Status of Winged Fibers and their Commercial Applications Walter Chapman, Allasso Industries, Morrisville, NC
The paper summarizes the development of the Allasso Winged Fiber, an innovative macro fiber with tunable geometries. Commonly identified by its deep channels and wing-like projections, the winged fiber enables the creation of tailor-made fibers for a wide range of applications.
TT10: Achieving Sustainability – Continuing Impact on Technical Textiles
Session Chair: Meredith Boyd, Product Development Manager, Unifi Manufacturing, Inc., Greensboro, NC
Sustainability is wide ranging and includes such things as conservation of materials and resources, utilizing environmentally friendly raw materials, producing biodegradable products, eliminating/reducing waste, revising work practices, and adapting new environmentally friendly technologies. How does the technical textiles industry work with such guidelines where performance is the primary criteria in material and product selection? Learn what industry leaders are doing.
• TT10.1 Developing a Niche Business in the Face of Intense Import Jack Miller, SustainTex, Greenville, SC
• TT10.2 Performance from a Bottle – the Good, Bad and Ugly of PCR Fiber Bob Usher, Technical Director of the David C. Poole Company, Greenville SC
From textile to nonwoven processing, the use of post-consumer recycle polyester fiber has risen worldwide despite shortcomings with fiber quality and the ability to achieve virgin quality standards. This paper seeks to discuss those issues and actions taken/underway to deal with these issues.
Concurrent, 8:30-11 a.m.
TT11: Medical Technical Textile Advancements
Session Chair: Tom Langdon, Vice President of Sourcing and Purchasing, Encompass Group, Atlanta, GA
While most healthcare professionals focus on reducing costs and improving patient outcomes what sometimes gets lost is the fact that no other single item is in more direct contact with the patient then the medical textiles. In this session we will focus on how advancements in areas such as antimicrobials, Derma Care, DVT prevention, patient and surgical staff safety are improving patient outcomes and reducing costs by applying innovative strategies to enhance comfort and safety for the human element on both sides of the hospital bed.
• TT11.1 The AAMI Standard covering Surgical Protective Apparel Shelly Patrovskis, Marketing Director, Lac-Mac Limited, London, ON
The risks associated with the transmission of bloodborne pathogens has elevated the purpose for Surgical Protective Apparel. Protecting against strike‐through has become crucial today. This presentation outlines the rationale behind AAMI’s defining the Standard for Surgical Protective Apparel and will exhibit the effectiveness of barrier protection through a visual demonstration.
• TT11.2 Derma Therapy Innovative Approach for Improving Skin Sensitive Conditions James Barry, Product Manager, Precision Fabrics Group, Inc., Greensboro, NC
Learn about new fabric technology that reduces friction and wicks away moisture providing an improved surface for skin interaction and less trauma for sensitive skin and how this technology works. Clinical trials data including baseline comparisons, study designs, results and conclusions will also be discussed.
• TT11.3 Medical Applications and Barrier Properties using Forcespun Nanofibers Bryce W. Davis PhD, Materials Engineer, FibeRio Technology Corporation, McAllen, TX
TT12: Fibers
Session Chair: Jeff Dugan, Co-founder and Research Vice President, Fiber Innovation Technology, Johnson City, TN
The important performance properties of a technical textile are often delivered primarily by the properties of the fibers used in the fabric. New technologies are being developed to produce new performance properties in staple fibers, filament yarns, and fibers made directly into nonwovens such as spunbond and meltblown fabrics. This session will examine some of the most intriguing new fiber technologies.
• TT12.1 Durable Stretch Nonwoven Using a New Bicomponent Fiber System Dr. Behnam Pourdeyhimi, Director Nonwovens Institute, NCSU, Raleigh, NC
• TT12.2 Fibers From Soy Robina Hogan, Commercialization Manager – Fibers, Omni Tech International, Midland, MI
• TT12.3 Piezoelectric Fibers From PVDF D. Vatansever and E. Siores, The University of Bolton, Institute for Materials Research and Innovation, UK
Interest in piezoelectricity of polymers arose in the second half of the 20th Century when Kawai claimed that poled thin films of Polyvinylidene Fluoride (PVDF) exhibited a large piezoelectric coefficient. Using polymer based piezoelectric materials provide some advantages over the ceramic piezoelectric materials since polymeric materials are lead free, inexpensive, light in weight, flexible and easy to process. Furthermore, in the energy regeneration area, polymeric piezoelectric materials can generate higher voltage and power than ceramic piezoelectric materials under certain conditions, such as low impact and moderate wind.
In addition to the symposium, the show floor will feature more than 100 exhibitors all doing business within the nonwovens and technical textile market. These exhibitors range from machinery and equipment suppliers to raw material producers to nonwoven and fabric makers to the makers of finished products targeting a number of different industries. Below, find an advanced look at what some exhibitors plant to bring with them to Atlanta.
Aurora Specialty Textiles Group
Aurora Specialty Textiles Group, Inc. (ASTG) will showcase its processing capabilities and finishing technologies, especially in regards to wider-width textile products, at Techtextil North America. As a full-service textile finisher, ASTG specializes in fabric sourcing, preparation, dyeing, coating and technical finishing for the woven and nonwoven fabrics industries. Headquartered in Aurora, IL, with a second manufacturing facility in Travelers Rest, SC, ASTG’s innovative fabric solutions are used throughout the world in print media, pressure sensitive tapes, home furnishing, napery, apparel, medical and industrial applications. In continuous operation for more than 130 years, ASTG is a leader in the textile industry, known for longevity, integrity, quality, value and cutting-edge technology. Its proven formula for creating and manufacturing finished fabrics not only allows for expansion into new markets and industries but also serves as an integral part in its customers’ continued success.
www.auroratextile.com
Dilo Group
Dilo will provide extensive information about recent machine concepts from its group companies including Dilo Temafa, DiloSpinnbau and DiloMachines. A major focus of the new equipment is to improve operational efficiency, web quality and uniformity with positive effects on all bonding processes.
In particular, the group will present its DON dosing opener of DiloTemafa designed as a link between the opening/blending operation and the card feeder. The DON ensures that fiber flow to the feeder is both continuous and consistent.

Photo courtesy of Dilo.
Additionally, the multifeed card feeder from Dilo Spinnbau, which is available in working widths can exceed five meters. This unit is equipped with a twin fiber delivery system in the upper chamber which provides a more regular material flow. The roll opening stage allows fibre into the lower chamber with further compaction by mechanical means and air movement derived from the permeable delivery apron. Such a unit can deliver over 400 kg/m/hr of 1.7 dtex fibre with a cross direction evenness CV of 2-3% immediately prior to the card. Changeover times with this Multifeed system are fast thus reducing downtime and web reprocessing requirements. Machine direction evenness is controlled by a weighbelt scale linked to the card infeed.
Multifeed can be used with all DiloSpinnbau card types in crosslapping applications or with high speed cards in series for web formation prior to hydroentanglement and thermal bonding.
The MultiCard – also designed by DiloSpinnbau - has roller infeed, a breast cylinder with three worker/stripper pairs and a 1500mm main cylinder with a further five roller pairs. This is a double doffer system with the possible activation of condenser rolls for heavier webs. Such a card will handle the full range of fiber fineness and length with a web speed potential up to 200 m/min and offers an economic solution for crosslaid nonwoven production.
The MultiCard enjoys a high production availability due to its easy and fast accessibility for cleaning and maintenance work.
Also on display will be Vertical (HL series) and horizontal (DL series) crosslappers available from DiloMachines which provide infeed speeds up to 200 m/min (HL series) eliminating bottlenecks in the production line. The Dilo DL lappers operate in an infeed speed range of 80-160 m/min depending on application and specific model used. In addition to high infeed speeds new apron arrangements have been designed to give high layering precision based on excellent web control. These machines have been supplied up to 14 m in width for papermachine clothing applications.
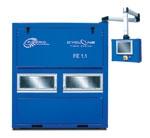
Photo courtesy of FibeRio.
FibeRio Technology Corporation
FibeRio Technology Corporation provides the technology and capital equipment to transform the materials market through the unlimited availability of nanofibers. FibeRio was formed to make Forcespinning™ Technology, the next generation of nanofiber production equipment, commercially available for both R&D and high-volume industrial applications. The company will be located at Booth 1413 and will be featuring the Cyclone L-1000 laboratory equipment and the Cyclone Fiber Engine 1.1 continuous nanofiber production equipment utilizing Forcespinning™ technology. The 1.1 meter wide system is the only nanofiber production equipment in the world that comes in turn-key Melt and/or Solution process configurations providing users with the widest possible range of materials to work with.
www.fiberio.com
Fi-Tech
Fi-Tech will be present at Techtextil North America, representing a number of machinery and equipment producers. Information from the following companies will available at the Fi-Tech booth:
• Brückner - Through Air Systems for Nonwovens.
• Enka Tecnica - Spinnerets, Breaker Plates and Spin Packs for all applications
• filtertechnik.Europe - Pack Filter Screens and Screen Changer Filters
• Hastem - Slat Transport Aprons for nonwovens
• Mahlo America - On-Line Gauging Systems for Nonwovens
• Reifenhauser REICOFIL - Spunbond and Composite Nonwoven Systems
• Schill & Seilacher - Fiber Finishes and Nonwoven Surfactants
• Sikoplast - Fiber and Nonwoven Recycling Systems
• Ungricht - Heated, Cooled and Engraved Rolls for Nonwovens
Lentex
First time exhibitor Lentex will present its nonwoven products at Techtextil North America. The Polish company makes spunlace, thermal bonded, chemical bonded and needlepunched nonwovens for automotives, clothing, upholstery, civil engineering, filtration, industrial and household wipes and medical applications. Additional capabilties include rewinding and slitting, powder and paste coating, impregnation, lamination, calendering and stitching.
www.lentex.com.pl
Tajima America
Tajima America Corp will display a wire laying machine which automates attaching wire to a backing for use in heated products. The process is accurate and reproducible using computer generated patterns. Applications include heated automotive seats, flexible pads, garments, blankets, pipe warmers, chemical process heaters and toilet seats.
Tajima America is the exclusive distributor for this unique machine used to automate manufacture of heating products.
www.tac-us.com
Thrace-Linq
Thrace-LINQ, a supplier of woven and nonwoven geosynthetic technical fabrics, is pleased to announce recent significant market expansions in its needlepunch nonwoven product lines. Capitalizing on its state-of-the art manufacturing capabilities, Thrace-LINQ has extended its line into new markets including industrial, automotive, building materials, absorbency, furniture and bedding.
Strong, durable and suitable for a wide-range of applications, needlepunch fabrics are a popular choice for a range of applications from furniture construction to oil spill absorption and containment. Market interest in these versatile materials continues to grow. Thrace-LINQ’s technology offers the company the flexibility to design and manufacture a wide array of needlepunch fabrics in both small and large volumes efficiently, positioning the company well to meet growing demand and new application needs.
www.thracelinq.com
Beginning this year, ATME-I (American Textile Machinery Exhbition International) will be incorporated into Techtextil North America, providing textile machinery equipment, producers and service suppliers a broader technical textile and nonwoven industry base to showcase their products and services.
Held in conjunction with the three-day exhibition will be a symposium, featuring dozens of sessions focusing on the latest in research and emerging technologies. The symposium is structured for attendees to conduct business and network on the show floor as well.
Keynote Address
Tuesday, April 24, 2012
8-9 a.m.
Miguel Caballero, the Armani of Bullet Proof Clothing
Designer, Miguel Caballero known as the ‘Armani of Bullet Proof Clothing’ founded his label in 1992 in Colombia’s capital, Bogota.
Señor Caballero will talk about where the idea for his company came from, how it grew to become recognized as a “specialized brand name” and a leader in personal protection solutions using high technology innovation, where he sees the industry heading, who his clients are and why they are attracted to his company.
Morning Sessions
Concurrent, 9:30- 11:30 a.m.
TT01: The Basics 1 – From Fiber to Fabrics
Session Chair: Dr. Fred Cook, Professor, Materials Science and Engineering, Georgia Tech, Atlanta, GA
This is the first part of a two-part session intended for those who are new in the industry or those who may want a refresher in textiles oriented to technical applications. Elements of fiber, yarn, fabric types and subsequent processes used to enhance properties and/or provide greater function will be included. A review by academic and industry experts of the attributes of various materials, their advantages and applications, and how they fit into technical textiles will be an integral part of this program. This session is designed to honor many requests for such a program at the beginning of the event to make your visit more valuable.
TT02: New Technology
Session Chair: Jim Kaufmann, Textile Engineering and Manufacturing, TEAM Inc., Woonsocket, RI
As technical and specialty textile applications continue to innovate, evolve and diversify; textile manufacturing technologies must keep pace. This session will focus on several new and innovative textile processing technologies that either already are, or soon will be impacting the industry and subsequently the marketplace.
• TT02.1 Melt Spinning of Yarn John Wilson, R&D Manager, The Quantum Group, Colfax, NC
• TT02.2 Nano fibers and Nano‐nonwovens Laura Frazier, Director, SNS Nano Fiber Technology, LLC, Hudson, OH
• TT02.3 Multi‐Axial Weaving Technology from Dornier Marty Colwell , American Dornier, Charlotte, NC
• TT02.4 Weft Inserted Warp Knitting Lutz Heinig, Technical Manager, Karl Mayer, Greensboro, NC
TT03: High Performance Composites
Session Chair: Dr. Ysuf Ulcay, Vice President, Bursa Technical University, Bursa, Turkey
Composites are everywhere and touch our lives in major ways daily. In technical textiles, composites involve materials that reinforce a resin to produce products (often called reinforced plastic) with high strength‐to‐weight ratios, most often reducing the weight of existing products of metals such as steel and aluminum. It is a growing market. Yet, to most of us, composites appear invisible. This session will review some of the applications, materials, construction and the advantages of using composites.
Afternoon Sessions
Concurrent, 1:30-4 p.m.
TT04: The Basics 2 – From Woven to Nonwovens to Knits
Session Chair: Dr. Fred Cook, Professor, Materials Science and Engineering, Georgia Tech, Atlanta, GA
A continuation of the elements of technical textiles. This session covers nonwovens in technical textiles along with specialized finishing processes and applications.
TT05: Military – Continuing Impact on Technical Textiles
Session Chair: Dr. Eugene Wilusz, Natick Soldier RDE Center, Natick, MA
Technical textiles continue to be an important component of countless items used by the military. Dress clothing, protective clothing, tentage, shelters, parachutes and many other items utilize technical textiles. Some of the current areas of interest include ballistic protection, flame resistance and chemical and biological protection. Presentations will cover the latest developments in science and technology of particular interest to defense applications.
• TT05.1 Thermal Testing Margaret Auerbach, Natick Soldier RDE Center, Natick, MA
• TT05.2 Super-Repellant Coatings Hoon Joo Lee, Professor, North Carolina State University, NC
• TT05.3 Microwave Promoted Deposition of Protective Coatings Dr. Jeffery Owens, Air Force Research Laboratory, Tyndall Airforces Base, FL
• TT05.4 Advanced Multi-Functional Nanofiber-Textile Materials for Chemical and Biological Defense Applications Xiangwu Zhang, PH.D., Assistant Professor, North Carolina State University, Raleigh, NC
This presentation will review work on developing novel textile materials for chemical and biological defense applications that require large volume‐to‐weight ratio, excellent filtration efficiency, high detoxifying activity and good durability. Latest developments in material processing methods in electrospinning and atmospheric plasma treatment were utilized to achieve these goals.
TT06: Automotive – Opportunities for Technical Textiles
Session Chair: Lee Woodard, Global Advanced R&D, Guilford Performance Textiles, Wilmington, NC
The automotive interiors marketplace is highly competitive. Being successful in this market requires fully integrating design expectations with technical performance; all at very aggressive price structures. Advances in technology, coupled with changing OEM design and styling requirements, are having a significant impact on the selection process for automotive interiors. This session will begin by reviewing key drivers for the raw material supply base for automotive textiles. Other presentations will explore emerging design trends in automotive interiors, including sustainability initiatives, and examine key changes to technical requirements for the various automotive textile applications.
• TT06.1 The Lifecycle of Automotive Textiles- From Dreams to Demolition Laurie Busch, Senior Designer, Guilford, Inc., Wilmington, NC
This presentation traces the current lifecycle of automotive soft trim. It begins with a look at what we are working on for vehicles still in the concept phase; model years 2013 and beyond. The presentation then reviews the vehicle trends from the 2012 Detroit Auto Show, including some significant changes in textile usage and placement. The presentation concludes by examining life after sale of a vehicle, from the perspective of soft trim and total vehicle recycling.
• TT06.2 The Synthetic Fibers Roller Coaster Alasdair Carmichael, President - Americas, PCI Fibers, Spartanburg, NC
The global markets for synthetic fibers have had a highly volatile last two years. What has influenced these markets? Fiber demand has been strong for much of this time, and oil prices have increased, so what has been the main driver of price. This paper will discuss these issues and look at where the automotive industry is impacted by synthetic fiber movements.
• TT06.3 Understanding Recycled Fibers for Automotive Applications Meredith Boyd, Product Development Manager, Unifi Manufacturing, Inc., Greensboro, NC
Learn everything you need to know about recycled fibers for automotive applications. Why are recycled fibers important for our future? Understand the differences of recycled products and how to use them in your products. This seminar will teach you everything from the process of making recycled fibers, their performance characteristics, and the companies that make them. Get all the information you need for informed decision making when it comes to recycled textiles for automotive.
Wednesday, April 25, 2012
Morning Sessions
Concurrent, 8:30-11 a.m.
Protective Textiles
Session Chair: John Cronin, Marketing Manager, HP Laboratories, New Ipswich, NH
The Protective Textiles Session is a forward‐looking program prepared for those engaged in the Personal Protective Equipment supply chain for public safety, military, industrial safety and other markets. This year’s expert speakers will discuss emerging federal standards, on‐going research and emerging technologies.
• TT07.1 Achieving Advanced FR Properties Through New Advances in Raw Materials Brian M Beitz PhD, Research and Development Manager, Offray Specialty Narrow Fabrics, Chester, NJ
Learn about the new advancements in fr properties with new raw material developments like fr-flex. This will allow the industry to explore new avenues for stretch applications in all of their fr products.
• T07.2 Application of 3D Orthogonal Woven High Performance Fabrics James A. Larsen II, Director of Engineering, Diamondback Tactical, LLLP, Spindale, NC
The presentation will include the application of 3D orthogonal woven high performance fabrics in Structural, Vehicle, Maritime, Aerospace and Body Armor. Touching on the comparisons between traditional 2D vs. 3D fabrics. The focus will be on the gained structural performance of the fabrics and processing improvements that benefit faster production times and higher fiber volume fractions.
TT08: Technical Textiles in Sports and Outdoors
Session Chair: Jim Kaufmann, Textile Engineering and Manufacturing, TEAM Inc., Woonsocket, RI
Sports and outdoor applications utilize a great deal of specialized technology to make the wearer or user more comfortable, hidden, and protected, even allowing greater performance and efficiency. As it is so often the case in technical textiles, many of the materials and technology used are “internal” and not visible, often given little thought but are vital to the user. Much research and development is focused on this area. This new session will examine some of those applications. Is there “gold” you might find in this area?
Afternoon Sessions
(Concurrent, 1:30-4 p.m.)
TT09: Technical Nonwovens
Session Chair: Dr. Behnam Pourdeyhimi, Director Nonwovens Institute, NCSU, Raleigh, NC
The session deals with the latest developments in nonwovens process technologies allowing the creation of novel structures from a varied of materials sources. The talks will focus on the latest developments in staple fiber processing.
• TT09.1 Advances in Heavy-Denier, High-Throughput Spunbond Timothy Robson, Hills Inc., Melbourne, FL
This presentation focuses on the machinery and methods associated with higher (>8) dpf spunbond production at rates at or above 300kg/m/hr. Spunbond machinery is broken down into two main systems, closed or open. The associated pros and cons of these systems are compared including suitability for various end-products. Specific attention is paid to the quenching, attenuation and laydown of filaments in these configurations. Dimensional comparisons of the spinning and formation distance have important affects on both the process and final product, particularly the MD:CD tenacity ratio and visual appearance of the fabric.
• TT09.2 Through Air Drying (TAD) and Comparative Bonding Processes American Truetzschler Nonwovens, Speaker To Be Announced
This presentation will focus on through air drying (TAD) and comparative bonding processes. To differentiate through air drying from other thermal bonding processes, the presentation will compare and contrast TAD with other processes, highlighting the pros and cons of each.
• TT09.3 Current Status of Winged Fibers and their Commercial Applications Walter Chapman, Allasso Industries, Morrisville, NC
The paper summarizes the development of the Allasso Winged Fiber, an innovative macro fiber with tunable geometries. Commonly identified by its deep channels and wing-like projections, the winged fiber enables the creation of tailor-made fibers for a wide range of applications.
TT10: Achieving Sustainability – Continuing Impact on Technical Textiles
Session Chair: Meredith Boyd, Product Development Manager, Unifi Manufacturing, Inc., Greensboro, NC
Sustainability is wide ranging and includes such things as conservation of materials and resources, utilizing environmentally friendly raw materials, producing biodegradable products, eliminating/reducing waste, revising work practices, and adapting new environmentally friendly technologies. How does the technical textiles industry work with such guidelines where performance is the primary criteria in material and product selection? Learn what industry leaders are doing.
• TT10.1 Developing a Niche Business in the Face of Intense Import Jack Miller, SustainTex, Greenville, SC
• TT10.2 Performance from a Bottle – the Good, Bad and Ugly of PCR Fiber Bob Usher, Technical Director of the David C. Poole Company, Greenville SC
From textile to nonwoven processing, the use of post-consumer recycle polyester fiber has risen worldwide despite shortcomings with fiber quality and the ability to achieve virgin quality standards. This paper seeks to discuss those issues and actions taken/underway to deal with these issues.
Thursday, April 26, 2012
Morning SessionsConcurrent, 8:30-11 a.m.
TT11: Medical Technical Textile Advancements
Session Chair: Tom Langdon, Vice President of Sourcing and Purchasing, Encompass Group, Atlanta, GA
While most healthcare professionals focus on reducing costs and improving patient outcomes what sometimes gets lost is the fact that no other single item is in more direct contact with the patient then the medical textiles. In this session we will focus on how advancements in areas such as antimicrobials, Derma Care, DVT prevention, patient and surgical staff safety are improving patient outcomes and reducing costs by applying innovative strategies to enhance comfort and safety for the human element on both sides of the hospital bed.
• TT11.1 The AAMI Standard covering Surgical Protective Apparel Shelly Patrovskis, Marketing Director, Lac-Mac Limited, London, ON
The risks associated with the transmission of bloodborne pathogens has elevated the purpose for Surgical Protective Apparel. Protecting against strike‐through has become crucial today. This presentation outlines the rationale behind AAMI’s defining the Standard for Surgical Protective Apparel and will exhibit the effectiveness of barrier protection through a visual demonstration.
• TT11.2 Derma Therapy Innovative Approach for Improving Skin Sensitive Conditions James Barry, Product Manager, Precision Fabrics Group, Inc., Greensboro, NC
Learn about new fabric technology that reduces friction and wicks away moisture providing an improved surface for skin interaction and less trauma for sensitive skin and how this technology works. Clinical trials data including baseline comparisons, study designs, results and conclusions will also be discussed.
• TT11.3 Medical Applications and Barrier Properties using Forcespun Nanofibers Bryce W. Davis PhD, Materials Engineer, FibeRio Technology Corporation, McAllen, TX
TT12: Fibers
Session Chair: Jeff Dugan, Co-founder and Research Vice President, Fiber Innovation Technology, Johnson City, TN
The important performance properties of a technical textile are often delivered primarily by the properties of the fibers used in the fabric. New technologies are being developed to produce new performance properties in staple fibers, filament yarns, and fibers made directly into nonwovens such as spunbond and meltblown fabrics. This session will examine some of the most intriguing new fiber technologies.
• TT12.1 Durable Stretch Nonwoven Using a New Bicomponent Fiber System Dr. Behnam Pourdeyhimi, Director Nonwovens Institute, NCSU, Raleigh, NC
• TT12.2 Fibers From Soy Robina Hogan, Commercialization Manager – Fibers, Omni Tech International, Midland, MI
• TT12.3 Piezoelectric Fibers From PVDF D. Vatansever and E. Siores, The University of Bolton, Institute for Materials Research and Innovation, UK
Interest in piezoelectricity of polymers arose in the second half of the 20th Century when Kawai claimed that poled thin films of Polyvinylidene Fluoride (PVDF) exhibited a large piezoelectric coefficient. Using polymer based piezoelectric materials provide some advantages over the ceramic piezoelectric materials since polymeric materials are lead free, inexpensive, light in weight, flexible and easy to process. Furthermore, in the energy regeneration area, polymeric piezoelectric materials can generate higher voltage and power than ceramic piezoelectric materials under certain conditions, such as low impact and moderate wind.
In addition to the symposium, the show floor will feature more than 100 exhibitors all doing business within the nonwovens and technical textile market. These exhibitors range from machinery and equipment suppliers to raw material producers to nonwoven and fabric makers to the makers of finished products targeting a number of different industries. Below, find an advanced look at what some exhibitors plant to bring with them to Atlanta.
Aurora Specialty Textiles Group
Aurora Specialty Textiles Group, Inc. (ASTG) will showcase its processing capabilities and finishing technologies, especially in regards to wider-width textile products, at Techtextil North America. As a full-service textile finisher, ASTG specializes in fabric sourcing, preparation, dyeing, coating and technical finishing for the woven and nonwoven fabrics industries. Headquartered in Aurora, IL, with a second manufacturing facility in Travelers Rest, SC, ASTG’s innovative fabric solutions are used throughout the world in print media, pressure sensitive tapes, home furnishing, napery, apparel, medical and industrial applications. In continuous operation for more than 130 years, ASTG is a leader in the textile industry, known for longevity, integrity, quality, value and cutting-edge technology. Its proven formula for creating and manufacturing finished fabrics not only allows for expansion into new markets and industries but also serves as an integral part in its customers’ continued success.
www.auroratextile.com
Dilo Group
Dilo will provide extensive information about recent machine concepts from its group companies including Dilo Temafa, DiloSpinnbau and DiloMachines. A major focus of the new equipment is to improve operational efficiency, web quality and uniformity with positive effects on all bonding processes.
In particular, the group will present its DON dosing opener of DiloTemafa designed as a link between the opening/blending operation and the card feeder. The DON ensures that fiber flow to the feeder is both continuous and consistent.
Photo courtesy of Dilo.
Additionally, the multifeed card feeder from Dilo Spinnbau, which is available in working widths can exceed five meters. This unit is equipped with a twin fiber delivery system in the upper chamber which provides a more regular material flow. The roll opening stage allows fibre into the lower chamber with further compaction by mechanical means and air movement derived from the permeable delivery apron. Such a unit can deliver over 400 kg/m/hr of 1.7 dtex fibre with a cross direction evenness CV of 2-3% immediately prior to the card. Changeover times with this Multifeed system are fast thus reducing downtime and web reprocessing requirements. Machine direction evenness is controlled by a weighbelt scale linked to the card infeed.
Multifeed can be used with all DiloSpinnbau card types in crosslapping applications or with high speed cards in series for web formation prior to hydroentanglement and thermal bonding.
The MultiCard – also designed by DiloSpinnbau - has roller infeed, a breast cylinder with three worker/stripper pairs and a 1500mm main cylinder with a further five roller pairs. This is a double doffer system with the possible activation of condenser rolls for heavier webs. Such a card will handle the full range of fiber fineness and length with a web speed potential up to 200 m/min and offers an economic solution for crosslaid nonwoven production.
The MultiCard enjoys a high production availability due to its easy and fast accessibility for cleaning and maintenance work.
Also on display will be Vertical (HL series) and horizontal (DL series) crosslappers available from DiloMachines which provide infeed speeds up to 200 m/min (HL series) eliminating bottlenecks in the production line. The Dilo DL lappers operate in an infeed speed range of 80-160 m/min depending on application and specific model used. In addition to high infeed speeds new apron arrangements have been designed to give high layering precision based on excellent web control. These machines have been supplied up to 14 m in width for papermachine clothing applications.
Photo courtesy of FibeRio.
FibeRio Technology Corporation provides the technology and capital equipment to transform the materials market through the unlimited availability of nanofibers. FibeRio was formed to make Forcespinning™ Technology, the next generation of nanofiber production equipment, commercially available for both R&D and high-volume industrial applications. The company will be located at Booth 1413 and will be featuring the Cyclone L-1000 laboratory equipment and the Cyclone Fiber Engine 1.1 continuous nanofiber production equipment utilizing Forcespinning™ technology. The 1.1 meter wide system is the only nanofiber production equipment in the world that comes in turn-key Melt and/or Solution process configurations providing users with the widest possible range of materials to work with.
www.fiberio.com
Fi-Tech
Fi-Tech will be present at Techtextil North America, representing a number of machinery and equipment producers. Information from the following companies will available at the Fi-Tech booth:
• Brückner - Through Air Systems for Nonwovens.
• Enka Tecnica - Spinnerets, Breaker Plates and Spin Packs for all applications
• filtertechnik.Europe - Pack Filter Screens and Screen Changer Filters
• Hastem - Slat Transport Aprons for nonwovens
• Mahlo America - On-Line Gauging Systems for Nonwovens
• Reifenhauser REICOFIL - Spunbond and Composite Nonwoven Systems
• Schill & Seilacher - Fiber Finishes and Nonwoven Surfactants
• Sikoplast - Fiber and Nonwoven Recycling Systems
• Ungricht - Heated, Cooled and Engraved Rolls for Nonwovens
Lentex
First time exhibitor Lentex will present its nonwoven products at Techtextil North America. The Polish company makes spunlace, thermal bonded, chemical bonded and needlepunched nonwovens for automotives, clothing, upholstery, civil engineering, filtration, industrial and household wipes and medical applications. Additional capabilties include rewinding and slitting, powder and paste coating, impregnation, lamination, calendering and stitching.
www.lentex.com.pl
Tajima America
Tajima America Corp will display a wire laying machine which automates attaching wire to a backing for use in heated products. The process is accurate and reproducible using computer generated patterns. Applications include heated automotive seats, flexible pads, garments, blankets, pipe warmers, chemical process heaters and toilet seats.
Tajima America is the exclusive distributor for this unique machine used to automate manufacture of heating products.
www.tac-us.com
Thrace-Linq
Thrace-LINQ, a supplier of woven and nonwoven geosynthetic technical fabrics, is pleased to announce recent significant market expansions in its needlepunch nonwoven product lines. Capitalizing on its state-of-the art manufacturing capabilities, Thrace-LINQ has extended its line into new markets including industrial, automotive, building materials, absorbency, furniture and bedding.
Strong, durable and suitable for a wide-range of applications, needlepunch fabrics are a popular choice for a range of applications from furniture construction to oil spill absorption and containment. Market interest in these versatile materials continues to grow. Thrace-LINQ’s technology offers the company the flexibility to design and manufacture a wide array of needlepunch fabrics in both small and large volumes efficiently, positioning the company well to meet growing demand and new application needs.
www.thracelinq.com