Karen McIntyre, editor02.05.15
Where the hygiene market attracts the volumes, the attention and the large investment dollars, the industrial market offers nonwovens makers opportunities for quiet growth, innovation, value and an avenue to enter new markets. The major markets for industrial nonwovens include automotives, filtration, geotextiles, aerospace and home furnishings but new opportunities are opening up every day and nonwovens manufacturers are always looking for new solutions to their customers needs. In the past couple of months, many of the major suppliers of nonwovens to these markets have made strategic decisions ranging from investing to acquisition to new product development. Here is a look at some of these events:
AstenJohnson/Eagle Nonwovens
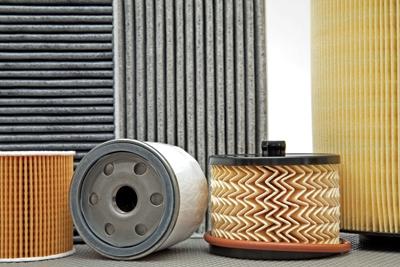
Filtration remains one of the fastest growing and most dynamic industrial market for nonwovens.
In December, AstenJohnson, a premier supplier of paper machine clothing, filaments, specialty and filtration fabrics and equipment for the paper industry, acquired Eagle Nonwovens, a U.S.-based maker of needlepunch nonwovens in a move intended to expand its scope in industrial and technical markets.
Eagle Nonwovens is known for producing consistent, high-quality products and delivering them with fast service. The company has also gained a reputation for creative problem solving by developing innovative needlepunch solutions for the aerospace, automotive, healthcare, filtration and home furnishings industries. It manufactures products at a 170,000 square-foot facility in St. Louis, MO using state-of-the-art Dilo Systems production equipment with in-line calendering, heat setting, singeing and glazing. The company can process more than 30 million pounds of synthetic fiber each year.
The Eagle Nonwovens business unit reports to Steve Polston, senior vice president and CFO of AstenJohnson. Polston said that the acquisition came after his company began looking for growth opportunities in markets adjacent to the pulp and paper industry, AstenJohnson’s primary business. “We are happy with the pulp and paper business, but we are also looking to invest in other areas with solid growth,” he says.
While it was Eagle’s participation in the filtration market that first attracted AstenJohnson’s attention, other markets like automotives and composites are now also on the company’s radar. ”Filtration was identified as a market with good growth, profitable players and good competition, but these other markets are also in line with our strategy. Eagle’s technology allows it to do a lot of things and that is what we liked about this company.”
Fibertex Nonwovens
The next move for Danish nonwovens maker Fibertex Nonwovens is expansion into the U.S. market. In October, the company acquired Non Woven Solutions (NWS), a Chicago, IL-based manufacturer of needlepunch nonwovens with 2013 sales of nearly $17 million. The deal was valued at $25 million. According to Fibertex executives, the acquisition was a logical next step for the strategic development of the company, which as expanded its industrial-centered business through acquisitions in France and the Czech Republic and the creation of a greenfield site in South Africa. The company separated from its sister-company Fibertex Personal Care, a supplier of spunmelt nonwovens, in 2012.
“In recent years, Fibertex Nonwovens has increasingly focused on special-purpose products for the composites, automotive and other industries. NWS is a perfect match for this strategy,” explains Jørgen Bech Madsen, CEO, Fibertex Nonwovens.
Within the automotives market, many of Fibertex’s customers, which comprise major international subcontractors, have been encouraging it to establish a North American presence. NWS meets this demand and also gives Fibertex access to several key market areas. NWS was founded in 2007 and has generated double-digit growth rates in recent years. The company operates two production lines, manufacturing materials for the composites and automotive industries as well as nonwoven products for wound care, filtration, bedding and construction.
Within its existing businesses, which include several operations throughout Europe and Africa, Fibertex Nonwovens has reported growth thanks to increased demand as well as new products and more advanced solutions in its five core markets, automotives, construction, industrial, filtration and wipes. Additionally, the company has been expanding itself into new industrial markets including acoustics and low and high end filtration as well as in what the company refers to as advanced nonwovens.
In addition to acquisition, Fibertex Nonwovens has been working on a company-wide improvement program that modernized and expanded its production platform. This five-year investment plan covers improvements at all of Fibertex Nonwovens’ locations and will include some yet-to-be-announced major enhancements, according to executives.
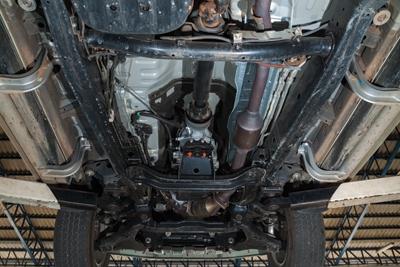
Automotives remains a strong and growing market for nonwovens.
Freudenberg
In an effort to boost its presence in a number of industrial-centered markets, Freudenberg announced upgrades to its spunlaid lines in Kaiserslautern, Germany, and Durham, NC, last year. According to the company, the projects, both line enhancements, improve product quality, allowing them to make nonwovens with high quality and improved performance.
In Durham, three existing spunlaid lines were retrofitted with advanced production technology, improving the quality of nonwovens used for filter materials, OEM automotive carpeting and carpet backings and increasing Freudenberg’s flexibility in supplying global markets.
In Kaiserslautern, an existing pilot line, which provides a good platform for product development at the planning level, was upgraded. This project will lead to improvements in the quality of the product’s physical properties, allowing the business group to proactively serve the needs of its customers. This will bring benefits in not only automotive, carpet and filter segments but also for customers in the shoe and construction segments.
Both investment projects in Kaiserslautern and Durham relate to the further technical development of existing lines and follow Freudenberg’s decades-long tradition of continuous process improvement and will enhance product quality, according to executives. These lines are now able to manufacture nonwovens of a higher quality with improved performance properties.
In other investment news, in May 2013, Freudenberg began work on a new Evolon production line in Colmar, France, the site of the company’s original Evolon investment. Manufactured through a globally patented technology combining the spinning of filaments with splitting through hydroentanglement, Evolon was developed in the late 1990s and has since been successful in a number applications including high tech cleaning cloths, automotives and, most recently, medical areas.
The latest investment in this technology was reported at €5 million and responds to growth in all application segments with Evolon—bedding, cleaning, packaging, and others. Evolon is also making headway in the UV protection market.
Lydall
In early 2014, Lydall expanded its market focus beyond its traditional areas, which include automotives and wetlaid filtration media, when it acquired the industrial filtration business of Andrew Industries. Known now as Lydall Industrial Filtration, the division includes Andrew’s baghouse filtration business with plants in South Carolina, the U.K. and China as well as existing Lydall operations in the U.K. and China. According to company executives, the new division created through the acquisition builds upon the strong technical textile capabilities already held by Lydall. It will continue to be a leader in air pollution control, commercial laundries, office automation, automotive filtration and home appliance markets. In addition to these capabilities, the acquisition adds about $130 million to Lydall’s annual sales.
Products offered through Lydall Industrial Filtration include Fiberlox, a fiber-supported needlefelt, which accounts for over 75% of all pulse jet filter felt consumed in North America, Microfelt, an engineered filter system that provides superior surface filtration performance, and Pleatlox, a complete line of pleatable filter media for today’s pleated bag or cartridge manufacturer. In addition to industrial filtration, Lydall makes wetlaid nonwovens for filtration and insulation applications through its Performance Materials Division as well as polyester-based needlepunch nonwovens for automotives through its Thermal/Acoustical division.
Growth in both new and existing markets is a focus for the company, and while the purchase of Andrew will help the company grow in new markets and new geographies, a growth strategy is also a focus in Lydall’s existing businesses.
In March, Lydall improved its filtration operations with the addition of a small wetlaid line in Rochester, NH. Described as a minimill, this state-of-the-art line, dedicated primarily for smaller runs, offers Lydall’s customers benefits like a faster start up, increased efficiency and better flexibility. This will help Lydall cater to and grow in the life science markets where many applications have smaller batch sizes. The line can provide customers with products in an efficient manner and allows Lydall to hold research and development and testing trials without monopolizing its existing assets.
Polymer Group Inc.
Even though it is the largest maker of spunmelt nonwovens for hygiene applications in the world, PGI Nonwovens has not ignored industrial markets. In fact, the company has invested heavily in this segment, most notably acquiring Fiberweb Nonwovens in 2013. This purchase added about $460 million in sales to PGI’s bottom line, and most of these were within two segments—technical fabrics and geosynthetics. Technologies included in the sale included needlepunch, meltblown, laminates and several other proprietary processes while key markets included roofing, geosynthetics and filtration.
At the time of the acquisition, PGI executives pointed to diversification into technical or industrial markets as the driving force behind the decision.
In November, PGI expanded its role in the filtration segment through the launch of the Everist brand of filtration media for high efficiency applications.
The nanofiber-based technology offers enhanced mechanical efficiency, low pressure drop and excellent dirt holding capacity, making it the ideal solution for companies in heating, ventilation and air conditioning (HVAC) or other industries reliant on high efficiency filtration media.
The launch of Everist media represents a new market entry for PGI, which has already seen success in filtration with Typar and Reemay, technologies inherited through the acquisition of Fiberweb.
According to Jay Forcucci, senior director of product management, PGI, Everist exceeds demands when it comes to enhanced efficiency, low pressure drops, dirt holding capacity, processing, durability and sustainability.
Saying that the launch was three years in the making, Forcucci says that Everist is being made on a new line in PGI’s state-of-the-art Waynesboro, VA, manufacturing facility.
PGI had invested about $8 million in the Waynesboro site, installing new assets and improving an existing quality lab.
Sandler
In recent years, Sandler has made two significant investments to boost its technical nonwovens business. In 2014, Sandler’s latest production line, dubbed VS 32 by the company, came onstream to expand capabilities within the technical nonwovens segment. Featuring proprietary Sandler technology, the €15 million line makes voluminous roll goods and sheet materials through a combination of needlepunching and thermal bonding and is largely targeting lightweight, easy-to-handle insulation materials as well as filter media and nonwovens for home textiles.
The line follows the late 2012 start-up of a new meltblown line targeting highly efficient meltblown media. This new line can process diverse thermoplastic raw materials and is equipped with different nozzle systems, allowing it to create new and unique nonwoven structures for pleatable filter media for air conditioning systems and other applications. The two new lines, as well as the expansion of its technical center in 2013, concluded a series of investments.
“We managed to put a 10-year investment plan into practice in half that time and, in doing so, invested a total of more than €60 million,” said chairman C. H. Sandler at the ceremony inaugurating the VS 32 line. “And once the current investment is completed, we will have created 115 new jobs during the past five years.”
These investments have not only added to Sandler’s capacity and its sales, they have also enabled the company’s success in a number of new markets. One market of note is insulation, where the company’s fibercomfort material prevents heat loss and noise abatement.
This material earned Sandler an INDEX Award at EDANA’s 2014 trade exposition, where the company’s meeting room space was made of the material. “If you notice, this material can really block sounds out,” Hornfeck explains. “It can act as a nice buffer in offices or in apartment buildings.” In addition to the insulating properties, fibercomfort is permanently hydrophobic, able to withstand even harsh weather and is permeable, allowing the building to breathe, preventing an accumulation of moisture. Being tread-proof and flame-resistant, the nonwovens also contribute to safety while the single-polymer recyclable nonwovens also help conserve valuable resources.
Sandler, a company that prides itself on diversification, focuses on both industrial and disposable markets, namely wipes. Industrial markets, Hornfeck says, offer nice, steady growth opportunities with a chance for innovation and new market development, and he has even seen some opportunity for spunlace and other materials in industrial areas.
“There are definitely more opportunities for industrial nonwovens,” he says. “It will never be an explosion but it will be an evolution as we see more projects and more interest from the industry.”
AstenJohnson/Eagle Nonwovens
Filtration remains one of the fastest growing and most dynamic industrial market for nonwovens.
Eagle Nonwovens is known for producing consistent, high-quality products and delivering them with fast service. The company has also gained a reputation for creative problem solving by developing innovative needlepunch solutions for the aerospace, automotive, healthcare, filtration and home furnishings industries. It manufactures products at a 170,000 square-foot facility in St. Louis, MO using state-of-the-art Dilo Systems production equipment with in-line calendering, heat setting, singeing and glazing. The company can process more than 30 million pounds of synthetic fiber each year.
The Eagle Nonwovens business unit reports to Steve Polston, senior vice president and CFO of AstenJohnson. Polston said that the acquisition came after his company began looking for growth opportunities in markets adjacent to the pulp and paper industry, AstenJohnson’s primary business. “We are happy with the pulp and paper business, but we are also looking to invest in other areas with solid growth,” he says.
While it was Eagle’s participation in the filtration market that first attracted AstenJohnson’s attention, other markets like automotives and composites are now also on the company’s radar. ”Filtration was identified as a market with good growth, profitable players and good competition, but these other markets are also in line with our strategy. Eagle’s technology allows it to do a lot of things and that is what we liked about this company.”
Fibertex Nonwovens
The next move for Danish nonwovens maker Fibertex Nonwovens is expansion into the U.S. market. In October, the company acquired Non Woven Solutions (NWS), a Chicago, IL-based manufacturer of needlepunch nonwovens with 2013 sales of nearly $17 million. The deal was valued at $25 million. According to Fibertex executives, the acquisition was a logical next step for the strategic development of the company, which as expanded its industrial-centered business through acquisitions in France and the Czech Republic and the creation of a greenfield site in South Africa. The company separated from its sister-company Fibertex Personal Care, a supplier of spunmelt nonwovens, in 2012.
“In recent years, Fibertex Nonwovens has increasingly focused on special-purpose products for the composites, automotive and other industries. NWS is a perfect match for this strategy,” explains Jørgen Bech Madsen, CEO, Fibertex Nonwovens.
Within the automotives market, many of Fibertex’s customers, which comprise major international subcontractors, have been encouraging it to establish a North American presence. NWS meets this demand and also gives Fibertex access to several key market areas. NWS was founded in 2007 and has generated double-digit growth rates in recent years. The company operates two production lines, manufacturing materials for the composites and automotive industries as well as nonwoven products for wound care, filtration, bedding and construction.
Within its existing businesses, which include several operations throughout Europe and Africa, Fibertex Nonwovens has reported growth thanks to increased demand as well as new products and more advanced solutions in its five core markets, automotives, construction, industrial, filtration and wipes. Additionally, the company has been expanding itself into new industrial markets including acoustics and low and high end filtration as well as in what the company refers to as advanced nonwovens.
In addition to acquisition, Fibertex Nonwovens has been working on a company-wide improvement program that modernized and expanded its production platform. This five-year investment plan covers improvements at all of Fibertex Nonwovens’ locations and will include some yet-to-be-announced major enhancements, according to executives.
Automotives remains a strong and growing market for nonwovens.
Freudenberg
In an effort to boost its presence in a number of industrial-centered markets, Freudenberg announced upgrades to its spunlaid lines in Kaiserslautern, Germany, and Durham, NC, last year. According to the company, the projects, both line enhancements, improve product quality, allowing them to make nonwovens with high quality and improved performance.
In Durham, three existing spunlaid lines were retrofitted with advanced production technology, improving the quality of nonwovens used for filter materials, OEM automotive carpeting and carpet backings and increasing Freudenberg’s flexibility in supplying global markets.
In Kaiserslautern, an existing pilot line, which provides a good platform for product development at the planning level, was upgraded. This project will lead to improvements in the quality of the product’s physical properties, allowing the business group to proactively serve the needs of its customers. This will bring benefits in not only automotive, carpet and filter segments but also for customers in the shoe and construction segments.
Both investment projects in Kaiserslautern and Durham relate to the further technical development of existing lines and follow Freudenberg’s decades-long tradition of continuous process improvement and will enhance product quality, according to executives. These lines are now able to manufacture nonwovens of a higher quality with improved performance properties.
In other investment news, in May 2013, Freudenberg began work on a new Evolon production line in Colmar, France, the site of the company’s original Evolon investment. Manufactured through a globally patented technology combining the spinning of filaments with splitting through hydroentanglement, Evolon was developed in the late 1990s and has since been successful in a number applications including high tech cleaning cloths, automotives and, most recently, medical areas.
The latest investment in this technology was reported at €5 million and responds to growth in all application segments with Evolon—bedding, cleaning, packaging, and others. Evolon is also making headway in the UV protection market.
Lydall
In early 2014, Lydall expanded its market focus beyond its traditional areas, which include automotives and wetlaid filtration media, when it acquired the industrial filtration business of Andrew Industries. Known now as Lydall Industrial Filtration, the division includes Andrew’s baghouse filtration business with plants in South Carolina, the U.K. and China as well as existing Lydall operations in the U.K. and China. According to company executives, the new division created through the acquisition builds upon the strong technical textile capabilities already held by Lydall. It will continue to be a leader in air pollution control, commercial laundries, office automation, automotive filtration and home appliance markets. In addition to these capabilities, the acquisition adds about $130 million to Lydall’s annual sales.
Products offered through Lydall Industrial Filtration include Fiberlox, a fiber-supported needlefelt, which accounts for over 75% of all pulse jet filter felt consumed in North America, Microfelt, an engineered filter system that provides superior surface filtration performance, and Pleatlox, a complete line of pleatable filter media for today’s pleated bag or cartridge manufacturer. In addition to industrial filtration, Lydall makes wetlaid nonwovens for filtration and insulation applications through its Performance Materials Division as well as polyester-based needlepunch nonwovens for automotives through its Thermal/Acoustical division.
Growth in both new and existing markets is a focus for the company, and while the purchase of Andrew will help the company grow in new markets and new geographies, a growth strategy is also a focus in Lydall’s existing businesses.
In March, Lydall improved its filtration operations with the addition of a small wetlaid line in Rochester, NH. Described as a minimill, this state-of-the-art line, dedicated primarily for smaller runs, offers Lydall’s customers benefits like a faster start up, increased efficiency and better flexibility. This will help Lydall cater to and grow in the life science markets where many applications have smaller batch sizes. The line can provide customers with products in an efficient manner and allows Lydall to hold research and development and testing trials without monopolizing its existing assets.
Polymer Group Inc.
Even though it is the largest maker of spunmelt nonwovens for hygiene applications in the world, PGI Nonwovens has not ignored industrial markets. In fact, the company has invested heavily in this segment, most notably acquiring Fiberweb Nonwovens in 2013. This purchase added about $460 million in sales to PGI’s bottom line, and most of these were within two segments—technical fabrics and geosynthetics. Technologies included in the sale included needlepunch, meltblown, laminates and several other proprietary processes while key markets included roofing, geosynthetics and filtration.
At the time of the acquisition, PGI executives pointed to diversification into technical or industrial markets as the driving force behind the decision.
In November, PGI expanded its role in the filtration segment through the launch of the Everist brand of filtration media for high efficiency applications.
The nanofiber-based technology offers enhanced mechanical efficiency, low pressure drop and excellent dirt holding capacity, making it the ideal solution for companies in heating, ventilation and air conditioning (HVAC) or other industries reliant on high efficiency filtration media.
The launch of Everist media represents a new market entry for PGI, which has already seen success in filtration with Typar and Reemay, technologies inherited through the acquisition of Fiberweb.
According to Jay Forcucci, senior director of product management, PGI, Everist exceeds demands when it comes to enhanced efficiency, low pressure drops, dirt holding capacity, processing, durability and sustainability.
Saying that the launch was three years in the making, Forcucci says that Everist is being made on a new line in PGI’s state-of-the-art Waynesboro, VA, manufacturing facility.
PGI had invested about $8 million in the Waynesboro site, installing new assets and improving an existing quality lab.
Sandler
In recent years, Sandler has made two significant investments to boost its technical nonwovens business. In 2014, Sandler’s latest production line, dubbed VS 32 by the company, came onstream to expand capabilities within the technical nonwovens segment. Featuring proprietary Sandler technology, the €15 million line makes voluminous roll goods and sheet materials through a combination of needlepunching and thermal bonding and is largely targeting lightweight, easy-to-handle insulation materials as well as filter media and nonwovens for home textiles.
The line follows the late 2012 start-up of a new meltblown line targeting highly efficient meltblown media. This new line can process diverse thermoplastic raw materials and is equipped with different nozzle systems, allowing it to create new and unique nonwoven structures for pleatable filter media for air conditioning systems and other applications. The two new lines, as well as the expansion of its technical center in 2013, concluded a series of investments.
“We managed to put a 10-year investment plan into practice in half that time and, in doing so, invested a total of more than €60 million,” said chairman C. H. Sandler at the ceremony inaugurating the VS 32 line. “And once the current investment is completed, we will have created 115 new jobs during the past five years.”
These investments have not only added to Sandler’s capacity and its sales, they have also enabled the company’s success in a number of new markets. One market of note is insulation, where the company’s fibercomfort material prevents heat loss and noise abatement.
This material earned Sandler an INDEX Award at EDANA’s 2014 trade exposition, where the company’s meeting room space was made of the material. “If you notice, this material can really block sounds out,” Hornfeck explains. “It can act as a nice buffer in offices or in apartment buildings.” In addition to the insulating properties, fibercomfort is permanently hydrophobic, able to withstand even harsh weather and is permeable, allowing the building to breathe, preventing an accumulation of moisture. Being tread-proof and flame-resistant, the nonwovens also contribute to safety while the single-polymer recyclable nonwovens also help conserve valuable resources.
Sandler, a company that prides itself on diversification, focuses on both industrial and disposable markets, namely wipes. Industrial markets, Hornfeck says, offer nice, steady growth opportunities with a chance for innovation and new market development, and he has even seen some opportunity for spunlace and other materials in industrial areas.
“There are definitely more opportunities for industrial nonwovens,” he says. “It will never be an explosion but it will be an evolution as we see more projects and more interest from the industry.”