Dell’Orco & Villani has been in the textile machinery construction business for over 60 years. The focus of this Italian company is to produce machines and assist plants with their mechanical recycling of textile waste. It is located in the Prato district of Italy, a few kilometers from the Florence airport in Tuscany.
Dell’Orco & Villani was born from the intuition of two mechanics in 1964, Giovanni Dell’Orco and Silvano Villani who decided to develop a machine that would convert locally produced textile scraps back into fibers. In just a few short years, the company experienced numerous successes and expanded its manufacturing footprint with two plants in Italy and an extensive distribution and service network around the world.
During these decades of growth, Dell’Orco quickly evolved, and recycling machines became more sophisticated to cope with the modern requirements of turning extremely difficult recycling textile waste into fiber. The feature of the new current plants, produced by D&V, is that they can process used garments containing accessories, buttons, zippers, etc. without doing prior textile removal and sorting.
While common recycling plants require the material to be preliminarily treated to remove hard and metal parts, D&V’s machines remove these pollutants automatically during the recycling process without the need to remove buttons and zippers before inserting them into the plant. This makes these machines quite unique from others on the market.
In addition to the automatic metal and button removal technology, our company has developed a TWIN CARDING OPENER that allows textiles to be recycled in a non-aggressive manner, maintaining the length of the fiber despite the recycling process. This type of machinery, successfully presented for the first time at ITMA Barcelona in 2011, has been a great success leading to the sales of more than 200 units since 2011. D&V is leading the way in the search for the best technologies in textile waste recycling despite new players posing as new manufacturers of recycling machines.
One of the key components of this up-and-coming company is the way it combines a family dimension with an industrial organization. This makes it possible to design plants according to the types of materials and customer needs. Customization has always been the company’s hallmark, which together with prompt customer care in after-sales service, has made it the distinguishing feature compared to the big players in the market. In fact, the company has been run by the Dell’Orco family for three generations and, thanks to the technical and sales staff, it establishes a close relationship with customers. This does not end with the delivery of the machinery but continues with assistance in finding products and solutions that support the customers’ business.
It is important to note that all the machinery that makes up the recycling lines are designed, built, and tested in Italy by D&V. There is no other machinery manufactured by other companies or incorporated into our lines except our filtration plants. D&V being able to supply an entire line is a significant advantage for our customers who can count on a single point of contact and prompt dedicated after-sales service. Cutters, blending boxes, hopper feeders, opening/tearing machinery, and bale presses are all critical parts of the portfolio of Dell’Orco & Villani.
Textile waste recycling involves many challenges from the design and implementation of plants to the handling of dusty air generated in the recycling process. For this reason, D&V has been collaborating with Emmebi Impianti for more than 10 years to collect & trap dust to clean and condition the air in textile plants.
For 20 years, Emmebi Impianti has been a solid company present in the global aerotextile panorama specializing in the air treatment for every type of nonwoven production line since 1989. The production site is located in
Milan and has the latest 4.0 machinery for the internal production of its equipment and a long-experienced technical and R&D department which guarantees the great precision and flexibility of its plant solutions.
Thanks to its knowledge of the specific problems of each type of fiber and its own production strength, Emmebi has established itself as a reliable supplier of systems both for end customers and for numerous machinery manufacturers, becoming an industry benchmark.
The company’s ancient textile extraction involves a profound knowledge of the treatment of air linked to processing of natural fibers, traditionally dirtier and dustier, resulting in a strong specialization on filtration units capable of treating significant quantities of dust and waste to be recycled.
This ability has found its natural outlet in applications linked to recycling lines capable of generating rather difficult processing waste which amounts to between 6 and 10% of production.
In the last five years, Emmebi has built more than 50 systems related to the recycling of textile materials and has developed a new version of its filtering units capable of managing quantities significantly higher than market standards. Emmebi filters have, for the same size, the highest filtration surface available on rotary filters and is a greatly enhanced dust extraction capacity keeping electricity consumption to a minimum.
The robust mechanical construction is specifically developed to guarantee working efficiency under strong stress from the load of pollutants to be filtered, even in the ATEX version. The storage of dust occurs through a compaction system that automatically expels the waste compressed to a third of its volume making it easier to dispose of. Each filter is equipped with an automatic pre-filtration system, capable of separating the longest fibers from the dust sending them to a dedicated and patented terminal, the C200© compactor.
This device is ideal for managing longer fibers recovered from the suction of working machines and has a completely pneumatic compression/expulsion operation (unique in the sector) which is different than the standard mechanical auger. Pre-filtration, unlike traditional static systems, guarantees the possibility of recovering good fibers which can be sold separately or which can be automatically sent back online in the production. This allows, together with limited energy consumption, a much faster recovery of the investment.
All Emmebi filtration units are designed to allow the expulsion or recovery of clean hot air. This can be coupled with air conditioning and humidification systems, which are particularly valuable for eliminating static electricity problems and for processing natural fibers more efficiently. The specialization in the sector, the quality of the engineering, and the punctuality of the service were some of the common strengths that have established the long collaboration with D&V, sublimating the very high level of turnkey solutions offered for the textile recycling sector.
D&V and Emmebi have partnered in the North American market with Cross Plains Trading Company located in Chatsworth, GA. Andy Pirkle, owner of Cross Plains Trading Company, is the North American sales agent for the Italian machinery manufacturer and a customer of both agencies with machinery at two of his manufacturing plants.
Cross Plains, established in 2012, produces recycled textile fibers in one facility and recently opened a new facility with a Technoplants airlay line composed of additional D&V blending plant and Emmebi filtration machinery. This plant produces thermal bonded nonwovens from 300-10,000 gsm and uses recycled, natural and virgin fibers.
The Cross Plains recycling plant has multiple D&V recycling lines with several different Emmebi filters. The big advantage of the filter is to separate the dust from reusable fibers, therefore, increasing fiber yield and provide customers a dust free recycled fiber. The lines can process many different types of waste from yarn, fabrics and nonwovens.
Both facilities provide customers access for trials and offer toll manufacturing to assist customers in determining the proper machines required to achieve desired finished product. Cross Plains also provides spare parts and after sales service with technical visits as needed for both D&V and Emmebi.
Cross Plains sales team can be reached at 706-971-4743 or andy@crossplainstrading.com
Dell’Orco & Villani was born from the intuition of two mechanics in 1964, Giovanni Dell’Orco and Silvano Villani who decided to develop a machine that would convert locally produced textile scraps back into fibers. In just a few short years, the company experienced numerous successes and expanded its manufacturing footprint with two plants in Italy and an extensive distribution and service network around the world.
During these decades of growth, Dell’Orco quickly evolved, and recycling machines became more sophisticated to cope with the modern requirements of turning extremely difficult recycling textile waste into fiber. The feature of the new current plants, produced by D&V, is that they can process used garments containing accessories, buttons, zippers, etc. without doing prior textile removal and sorting.
While common recycling plants require the material to be preliminarily treated to remove hard and metal parts, D&V’s machines remove these pollutants automatically during the recycling process without the need to remove buttons and zippers before inserting them into the plant. This makes these machines quite unique from others on the market.

One of the key components of this up-and-coming company is the way it combines a family dimension with an industrial organization. This makes it possible to design plants according to the types of materials and customer needs. Customization has always been the company’s hallmark, which together with prompt customer care in after-sales service, has made it the distinguishing feature compared to the big players in the market. In fact, the company has been run by the Dell’Orco family for three generations and, thanks to the technical and sales staff, it establishes a close relationship with customers. This does not end with the delivery of the machinery but continues with assistance in finding products and solutions that support the customers’ business.
It is important to note that all the machinery that makes up the recycling lines are designed, built, and tested in Italy by D&V. There is no other machinery manufactured by other companies or incorporated into our lines except our filtration plants. D&V being able to supply an entire line is a significant advantage for our customers who can count on a single point of contact and prompt dedicated after-sales service. Cutters, blending boxes, hopper feeders, opening/tearing machinery, and bale presses are all critical parts of the portfolio of Dell’Orco & Villani.
Textile waste recycling involves many challenges from the design and implementation of plants to the handling of dusty air generated in the recycling process. For this reason, D&V has been collaborating with Emmebi Impianti for more than 10 years to collect & trap dust to clean and condition the air in textile plants.
For 20 years, Emmebi Impianti has been a solid company present in the global aerotextile panorama specializing in the air treatment for every type of nonwoven production line since 1989. The production site is located in
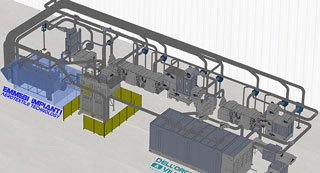
Thanks to its knowledge of the specific problems of each type of fiber and its own production strength, Emmebi has established itself as a reliable supplier of systems both for end customers and for numerous machinery manufacturers, becoming an industry benchmark.
The company’s ancient textile extraction involves a profound knowledge of the treatment of air linked to processing of natural fibers, traditionally dirtier and dustier, resulting in a strong specialization on filtration units capable of treating significant quantities of dust and waste to be recycled.
This ability has found its natural outlet in applications linked to recycling lines capable of generating rather difficult processing waste which amounts to between 6 and 10% of production.
In the last five years, Emmebi has built more than 50 systems related to the recycling of textile materials and has developed a new version of its filtering units capable of managing quantities significantly higher than market standards. Emmebi filters have, for the same size, the highest filtration surface available on rotary filters and is a greatly enhanced dust extraction capacity keeping electricity consumption to a minimum.
The robust mechanical construction is specifically developed to guarantee working efficiency under strong stress from the load of pollutants to be filtered, even in the ATEX version. The storage of dust occurs through a compaction system that automatically expels the waste compressed to a third of its volume making it easier to dispose of. Each filter is equipped with an automatic pre-filtration system, capable of separating the longest fibers from the dust sending them to a dedicated and patented terminal, the C200© compactor.
This device is ideal for managing longer fibers recovered from the suction of working machines and has a completely pneumatic compression/expulsion operation (unique in the sector) which is different than the standard mechanical auger. Pre-filtration, unlike traditional static systems, guarantees the possibility of recovering good fibers which can be sold separately or which can be automatically sent back online in the production. This allows, together with limited energy consumption, a much faster recovery of the investment.
All Emmebi filtration units are designed to allow the expulsion or recovery of clean hot air. This can be coupled with air conditioning and humidification systems, which are particularly valuable for eliminating static electricity problems and for processing natural fibers more efficiently. The specialization in the sector, the quality of the engineering, and the punctuality of the service were some of the common strengths that have established the long collaboration with D&V, sublimating the very high level of turnkey solutions offered for the textile recycling sector.

Cross Plains, established in 2012, produces recycled textile fibers in one facility and recently opened a new facility with a Technoplants airlay line composed of additional D&V blending plant and Emmebi filtration machinery. This plant produces thermal bonded nonwovens from 300-10,000 gsm and uses recycled, natural and virgin fibers.
The Cross Plains recycling plant has multiple D&V recycling lines with several different Emmebi filters. The big advantage of the filter is to separate the dust from reusable fibers, therefore, increasing fiber yield and provide customers a dust free recycled fiber. The lines can process many different types of waste from yarn, fabrics and nonwovens.
Both facilities provide customers access for trials and offer toll manufacturing to assist customers in determining the proper machines required to achieve desired finished product. Cross Plains also provides spare parts and after sales service with technical visits as needed for both D&V and Emmebi.
Cross Plains sales team can be reached at 706-971-4743 or andy@crossplainstrading.com