As
nonwovens continue their mass entry into new markets, the uses for
natural fibers are still expanding. With benefits including comfort,
moisture absorption and retention and renewability, natural fibers
have proven they are an ideal fit for a variety of nonwovens applications.
Although natural fibers such as jute, hemp, flax and sisal offer environmental
friendliness and strength, cotton is by far the most popular natural
fiber, thanks to its versatility in a wide range of products. Cotton
is ideal for nonwovens requiring absorbency, such as hygiene. The
softness, absorbency and wipe-dry performance of cotton makes it a
great choice for nonwovens, said Chuck Allen, technical accounts
manager of bleached cotton supplier BBA Nonwovens Natural Fibers Group,
Simpsonville, SC. There is a consumer preference for products
containing cotton.
Nonwovens that use cotton fibers include feminine hygiene items, industrial
and medical wipes, needlepunched batting, mattress pads and filtration
media as well as a variety of niche segments within these markets.
Cotton is a good fiber to use in liquid filtration applications
because of its unique ribbon shape and range of fiber diameters that
are well suited for depth filtration applications, explained
George Hargrove, vice president of sales and marketing at bleached
cotton supplier, Barnhardt Manufacturing Company, Charlotte, NC.
Mr. Hargrove added that bleached cotton is ideal for medical and wipes
applications or other end use products where consumers expect a pure
product. Barnhardt operates a Continuous Bleaching Line, which enables
it to offer pure white cotton fibers to these market segments. Fibers
on this line offer the purity of cotton with the uniformity traditionally
found in synthetic fibers. Barnhardts Continuous Bleaching
Line provides our customers with more open and less broken fibers,
which leads to less linting, Mr. Hargrove explained. This
is particularly valuable for spunlace producers, which have traditionally
used synthetic fibers. Wipes are undoubtedly a perfect end use for
cotton because of its biodegradability.
Biodegradability has gained increasing importance as growing environmental
concerns continue to prevail globally. One of the ways manufacturers
are responding to this increased environmental awareness is by reverting
back to natural fibers for nonwovens.
Sustaining Natural Fibers
The expansion of global wipes market has helped boost natural fibers
popularity throughout Asia and Europe, mainly because of increased
ecological awareness in these areas. Asia has experienced a growth
in cotton spunlaced wipes, whereas Europe is experiencing increases
in the use of cotton nonwovens because of the boom in the cosmetic
wipes market.
In the past few years, there has been a push by consumers
to move toward natural fibers that offer the same performance as
synthetics, said Marcel Dartee, global platform leader for
nonwovens at Cargill Dow, Minnetonka, MN. The biggest push
for natural fibers is currently coming from the Asia-Pacific region,
where concerns for the Earth are the highest. This is followed closely
behind by the European market.
Cargill Dow has responded to consumer preference for products containing
natural fibers by spending the past decade, and more than $750 million,
researching and developing its new Ingeo fiber. The companys
business is now equally split between packaging and Ingeo fibers.
Ingeo, which was launched globally in January, can be derived from
any form of annually renewable starch resources or fermentable sugars,
but Cargill Dow is currently only making it from corn. Ingeo is
reportedly replacing polyethylene in spunlaced wipes. Meanwhile,
in the automotive and construction areas, Ingeo is being used as
a binder fiber. Other areas where Ingeo is gaining ground include
the baby, cosmetic and household wipes markets as well as in high
loft waddings.
Sustainability is a growing concern for the nonwovens industry,
as well as for consumers, explained Cargill Dows Mr.
Dartee. The trend toward natural fibers has shown growth during
the past few years, and we believe it will continue to grow. There
are natural fibers available today that offer the same comfort and
performance of synthetics, making it easier for companies to make
the switch.
Ingeo, which can biodegrade in approximately 50 days in industrial
compost or standard waste disposal systems, offers wicking, soft
hand, low melting point characteristics and is naturally flame retardant.
When compared to fibers made from petroleum-based materials, such
as polypropylene, Ingeo reduces greenhouse gas emissions and the
use of fossil fuels.
Ingeos benefits have not gone unnoticed. To date, Cargill
Dow has secured more than 100 global partners who have signed on
to develop and market products under the Ingeo brand. The most recent
partners are Toray Industries, Osaka, Japan, Far Eastern Textiles,
Taipai, Taiwan and The Radici Group, Bergamo, Italy. All of these
companies have agreed to sell Ingeo branded products in markets
such as bedding, carpeting and furniture, to accredited downstream
participants.
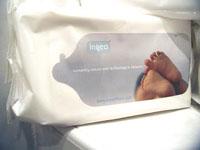 |
Cargill
Dows Ingeo fiber, which is derived from corn, is replacing
polyethylene in spunlaced wipes. |
Ingeos success has served as an example of how important
continued product development and innovation are to the natural
fibers market; however, keeping natural fibers on a fast track in
new nonwovens markets will not be the easiest task for suppliers.
One of the largest hurdles fiber suppliers are facing is raw material
price increases. This has significantly impacted both the natural
and synthetic fiber markets. With higher oil and energy costs and
changing cultivation conditions driving the prices of raw materials
up, many fiber suppliers have had no choice but to increase the
prices of their products.
There has been a sharp spike in fiber prices during the last
quarter of 2002 and the first quarter of 2003, explained BBAs
Mr. Allen. The forecast is for fiber prices to increase slightly
throughout the rest of this year. Having said this, it must be noted
that the early 2002 cotton fiber prices were at their lowest in
30 years.
These higher prices will most likely prevent significant growth
for natural fibers in North America in 2003. Despite this, fiber
suppliers are reportedly developing new products that, once commercialized,
will greatly impact the natural fibers market.
Fiber Innovation Prevails
In an effort to expand natural fibers presence in nonwovens,
fiber suppliers are blending natural and synthetic fibers, which
gives the fiber higher strength and length. When compared with other
materials, fibers such as cotton can then be applied in applications
that require more durable and high strength materials. Among these
are the automotive and construction markets.
Blending cotton with low-melt synthetic fibers, such as polypropylene
or polyethylene can produce thermal bonded fabrics, both high loft
and point bonded, explained BBAs Mr. Allen. This
trend could increase as fabric demands require properties of both
cotton and synthetic fibers also increase. The properties of each
are often complementary. For example, the absorbency of cotton is
combined with the strength of a synthetic fiber.
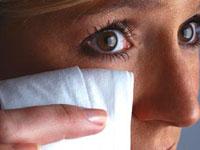 |
Barnhardt Manufacturing produces
bleached cotton fibers for carded, needled, chemical bonded,
spunlaced and thermal bonded nonwovens. |
Fiber combinations, coupled with technological advancements, will
continue to tailor natural fibers for specific applications. For
example, in the case of a thermal bonded product, manufacturers
can add or subtract cotton to adjust the fibers bonding and
melting points.
Cotton is not thermoplastic, so combining it with polypropylene
or polyethylene or any other bicomponent fiber will adjust the temperature
needed for fiber bonding for certain applications, added Mr.
Allen. These applications include furniture and bedding, where uniformity
and bulk are a necessity. Also emphasizing fiber selection research
is Cotton Incorporated, Cary, NC. The company is currently running
wipe trial runs to research the impact that fiber selection has
on the nonwoven and the final product. Cotton Incorporated is researching
the use of cotton in carding and airlaid materials and experimenting
with different cotton grades to improve the fiber opening, processing
performance, efficiency and the aesthetic value of the nonwoven
comprising the fiber.
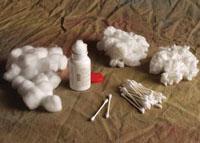 |
BBA
Nonwovens Natural Fibers Group has seen an increase in cotton
in the cosmetic market. |
We are conducting internal research to increase cottons
presence in North America, explained Mac McLean, associate
director of nonwovens research and implementation at Cotton Incorporated.
This includes strength and absorbency tests and the effects
of polyester blends. Wipes have the fastest growing appeal in North
America right now and they still continue to generate large profits.
In addition to stressing the importance of fiber research, manufacturers
are also touting the advantages that fiber finishes can bring to
the fiber. Any manufacturer who is looking to differentiate its
product is aware of how important fiber finishes have become in
gaining marketshare. End use products have become more dependent
on treatments such as flame retardancy, liquid repellency and antimicrobial
finishes. Cotton fibers used in needlepunched products are treated
to be more lubricant so the needles can better penetrate the fabric.
Meanwhile, fibers used in spunlaced products will often be treated
with a slick finish to prevent foaming during water jet entanglement.
With bleached cotton, fiber finishes will improve lubricity
and static resistance, which then improves processing speeds and
minimizes fiber breakage and damage during web forming, BBAs
Mr. Allen explained.
As fiber finishes continue to add value to products, manufacturers
are placing more emphasis on ensuring that the chemicals used are
safe and lack harmful side effects. At Lahore, Pakistan-based Ihsan
Sons, for example, cotton is bleached only with hydrogen peroxideinstead
of more harmful chlorine chemicalsaccording to Sarah Tayyib,
marketing manager of Ihsan Sons.
Finishing treatments are heavily influenced by consumer demands,
so the concentration of certain chemicals varies accordingly,
Ms. Tayyib explained. For example, with the use of bleached
cotton for food industry filters, the amount of an antimicrobial
treatment is much greater than other finishes.
Fiber combinations, finishing treatments and implementing ways to
derive natural fibers from the Earths resources all present
manufacturers with increased opportunities to expand the role of
natural fibers in nonwovens. Research and marketing studies will
also help promote the benefits of natural fibers and help them penetrate
newer markets.
|